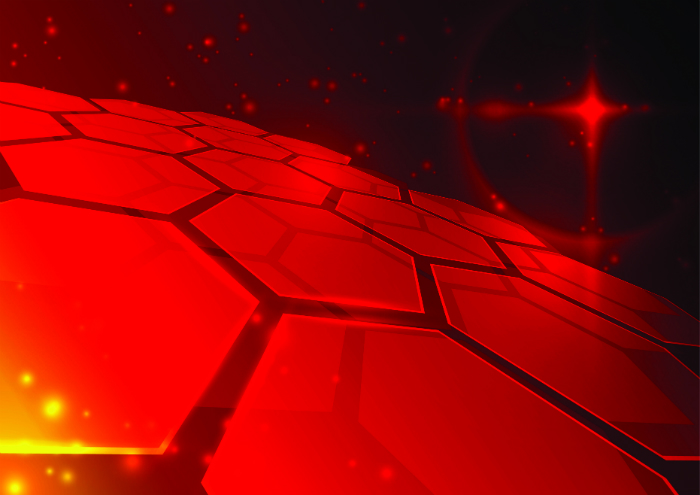
There are many questions for small-to-medium-scale print providers to consider before adopting significant levels of automation — Where will the savings come from? What is needed in hardware and software? What skill sets are necessary?
At what point does it become viable, does it work out with just one cutsheet digital printer and a guillotine, or do you need a fleet of presses to make it pay?
Do you need different setups for offset and digital or does one workflow cover them all? Should you integrate your management information system (MIS) and web-to-print (W2P), is it even worth investing in workflow automation if you do not have these two elements? And can workflow be based in the cloud?
WHAT THE VENDORS SAY
Agfa
Mark Brindley, managing director of Agfa Graphics Oceania, says: “Ideally automation is achieved if disciplined production is managed and applied to deadlines and begins with the estimating process. IT is one component of system integration, IT is key in planning and building the integration, but once generated, a well-managed production will allow automation. IT on staff or on contract is part of the setup process and hence companies can be cost effective with outsourced IT and implement automation.”
He finds the Apogee suite is designed to promote automation, “Apogee Integrate is the top level of the Apogee product suite and, in conjunction with hardware servers or VM-ware support, is the level that printers would need to automate their production needs.”
Brindley says repetition is a key ingredient to automation, “Custom work is when automation can break down. For those reasons, any flavour of printer – large, small, digital or traditional – can implement automation.
“The key to a successful implementation of workflow automation is to standardise work practices, whether that be a small shop with one press or a large plant with multiple presses. Standardisation allows for the implementation of entry-level automation, without complex MIS and IT systems. Apogee Manage, combined with Apogee Impose, allows the user to produce jobs based on pre-defined job ticket templates. The operator simply fills in the variables (number of pages, size of page, binding style, sheet size and press) from options in the drop-down menus and selects auto impose. In the past, mistakes were commonly made by operators when doing the mundane repetitive tasks. Apogee allows these tasks to be automated, freeing up the skilled operator to work on the complex tasks,” he explains.
Does Brindley recommend different setups for digital and offset, or does one workflow cover them all? “Yes and no. However, as Apogee is intuitive, once the job is estimated, the costing process and criteria determine whether Apogee will automatically process the job either in a digital or traditional flow. Again planned processes are the key. Apogee Prepress provides one workflow that can cater for conventional offset (web and sheetfed), third-party digital presses, and wide-format inkjet devices for sign and display work.”
And what is the degree of difficulty in integrating a W2P and MIS into the production workflow? “Ideally JDF is the link to allow MIS and our Apogee workflow their two-way communication. As MIS vendors vary with product capability, XMLJDF is a viable solution to allow automation. W2P is a flavour within the Apogee suite and an integrated solution with automation in workflow, our W2P Storefront compliments our Apogee Integrate or Manage flavours. Apogee Prepress does enable entry-level automation without the investment in MIS systems. Apogee Prepress integrates with Apogee Storefront, Print Sphere and Web approval,” he says.
Storefront and Print Sphere are provided as Software-as-a-Service (SaaS) , hosted by Agfa Graphics and requiring no hardware or IT support by the customer. Web Approval is a licensed option available on Apogee Prepress. Brindley says these three components provide both a level of automation and collaboration between the customer and the printer, through the uploading and pre-flighting of content directly to the workflow and online approval and automatic notifications for jobs in progress.
“Apogee is already available as a cloud solution,” notes Brindley. “When considering a cloud-based workflow, you also need to consider both the speed and reliability of the printer’s local ISP. In countries where the backbone and links to the server farms is both reliable and fast, the cloud is ideal for a wheel-and-spoke workflow implementation.
“In the Oceania region, Apogee is also on offer via a subscription solution. Our subscription model eliminates the ISP demand, allowing the production resources to be local to the printer, and with all the benefit of the cloud solution, as the licensing and system contract exists in the cloud for the system to reference.”
EFI
Mark Fletcher, EFI’s associate marketing specialist APAC, reflects: “As our industry continues transitioning from less long-run static offset to more variable, short-run personalised digital, the singular complex manual workflow just cannot cope – when you are under pressure to process a multitude of different jobs in a matter of hours rather than days.
“It just does not make sense for every job to travel along the same route, regardless of value, turnaround time or run length.
“If you are relying on one workflow for every type of job, then you will end up wasting labour, undermining profits and you will be unable to meet many customers’ expectations of turnaround times.”
He notes that in its 2017 InfoTrends reported that 31 per cent of printers see investment in automation software as the answer to their productivity and workflow challenges. However only eight per cent have fully automated workflow solutions. “So why are more not printers investing in workflow automation? Some of the reasons and challenges we know of are related to the costs and entanglement of legacy systems and mixed vendor environments, as well as the complexity of highly varied workflows, which encompass a myriad multiple entry points.”
Fletcher sees EFI’s PrintSmith Vision as designed and built to directly address these challenges. Being a completely browser-based, scalable and customisable print management solution, PrintSmith is able to streamline operations, reduce costs and provide visibility.
With 10,000 systems sold worldwide, PrintSmith offers estimating, point-of-sale, account management, production management, receivables and sales analysis tools within what Feltcher says is a single, easy-to-use application.
It includes full business reporting capabilities, providing real-time analytics that allow identification of productivity and job costing, as well as real-time status updates – for full visibility across the production floor.
He outlines some of the features of PrintSmith Vision as: easy-to-use; easy-to-leverage; remote secure access from mobile, tablet and desktop; flexibility and scalability; easy and quick implementation, and rapid ROI, as it allows print businesses to take advantage of its benefits within weeks.
EFI says its Productivity Suites address pressing automation and efficiency needs by moving the workflow emphasis away from individual software packages to a complete offering that uses best-in-class segment-based MIS/ERP systems.
Fujifilm
Steve Peck, project & marketing manager, graphic systems, at Fujifilm Australia, says the vendor’s XMF workflow, “Is relatively easy to implement as it is an all-PDF, JDF-based scalable system. Printers just tick the boxes for what they want to automate – it is important that these be identified so they can be set up by our specialists. It works best as an end-to-end solution from PDF creation to imposition and output. Because XMF uses Adobe’s APPE print engine, it is pure PDF throughout. A single production screen puts all information in front of the operator, even for larger multi-output installations. Of course, as with all software, training is needed, but XMF is intuitive and easy to navigate, with drag-and-drop features everybody is familiar with. Having said that, you can push XMF as hard as you like in large, complex environments because along with the scalability comes amazing flexibility.”
As Fujifilm XMF uses Mercury rip architecture, it can rip several jobs at the same time, even to different output devices such as a CTP and digital press, advises Peck. This parallel ripping means the user can specify a medium-to-high spec PC that will use all CPU cores to meet the needs of the most simple or demanding throughput. XMF will use both Mac and PC workstations and, if using XMF’s ColorPath cloud-based colour management, an extra workstation is not needed to achieve this functionality. As all files are uploaded to the cloud, colour is adjusted to ISO 12647-2 across all platforms and corrected files are sent back ready for output.
Regardless of the size of the enterprise, XMF works at various levels, due to its scalability, he explains. “It is up to the customer. XMF is powerful and is naturally more attractive to multi-press, cross-platform environments where offset, digital and perhaps wide format are all present. XMF can handle a one-press environ-ment but it would be rather like buying a Ferrari and driving it only at 30 kmh.”
And XMF dovetails into most existing work environments, especially MIS and order intake, says Peck. “JDF and JTF were designed for just that. Automation is always worth investing in, as it reduces costs and waste. W2P is a choice for printers but MIS of some kind, even just estimating and job tracking, is a must.”
Can workflow be in the cloud? “With XMF, partly,” he says. “ColorPath takes ISO colour management offsite and up to Fujifilm-hosted servers that are always up-to-date, fast and accurate – this feature alone saves a lot of time and reprints.”
Fuji Xerox
Perhaps one of the most basic questions is how easy is it to implement workflow automation, in terms of pre-existing typical printer skillsets? Quentin Sandery, national manager, Production Solutions Business Group, Fuji Xerox Australia (FXA), says FreeFlow Core, the FXA workflow automation solution, has a low learning curve.
FreeFlow made headlines earlier this year when print electronics giant EFI bought the software from FXA’s parent Xerox and is integrating its EFI line-up with the FreeFlow DFE.
“Beyond the initial installation of FreeFlow Core, which is performed by an FXA solution analyst, there is minimal ongoing support required from an IT specialist or IT contractor,” says Sandery. “FreeFlow Core runs a background service on the installed server. A typical printer with basic digital pre-press knowledge can be taught to proficiently use the software within a four-hour training session. Most digital pre-press operators are creating complex workflows within a week of installation.”
Sandery says FreeFlow Core can be supplied as a complete software and hardware package, which includes support for five years across the software and hardware. A customer can choose to provide their own server or virtual server if desired. “Server requirements vary, based on the amount of files planned to go through the workflow. In FreeFlow Core, files are processed simultaneously through workflows, based on the number of CPU cores. For example, a small print shop may choose to provide a server with eight CPU cores and 8GB of RAM. Under this setup, they could process eight jobs simultaneously. A large print shop may provide, for example, a server with 16 cores for greater throughput of jobs.”
Scalability is a major advantage of FreeFlow Core, he points out. “The beauty with FreeFlow Core is that it grows with your business. You can purchase the Base module to just do basic pre-press tasks like impositioning and direct submission to RIPs. In the future, you could scale up FreeFlow Core to load-balance print submission to an entire fleet of printers. Even in small print shops, an ROI can be achieved in as little as three months.
Many print business owners agonise over whether they need different workflow setups for offset and digital, and are hunting for a workflow that covers multiple printing technologies. Sandery explains that FreeFlow Core is PDF-based, and therefore covers both digital and offset printing. “Workflows can incorporate ‘decision routing’ for maximum efficiency.
For example, jobs greater than 1,000 copies can be routed to an offset platemaker, while jobs under 1,000 copies can be routed to a digital cutsheet device. We have installations of FreeFlow core that are feeding a mixture of devices such as digital cutsheet, web offset and digital continuous-feed.”
And then there is the question of integrating MIS and W2P. In fact, is it even worth investing in workflow automation if you do not have these two elements? “Absolutely in the case of FreeFlow Core,” responds Sandery. “There are significant time savings to be had in automating repetitive pre-press tasks. In the future, if you choose to implement an MIS or W2P system, JDF connectivity ensures the ability to communicate across multiple systems.”
And can FreeFlow be accessed as SaaS? Yes, says Sandery,“FreeFlow Core can be installed in the cloud and be used to feed work to multiple remote locations.”
Heidelberg
Dierk Wissmann, Heidelberg’s national sales manager, ANZ, consumables, Prinect and digital, believes there is no doubt that running a highly specified integration system requires certain skill sets. “Skill sets now in business are evolving from craft-based to IT and analytical, however, there has to be a correct blend of the existing and future skills. Heidelberg’s Prinect Production workflow offers Smart Automation capabilities, which can initially be set up in co-operation with Heidelberg, but then be maintained by the customer themselves. We want to ensure we protect those aspects for our customers through any transition towards semi- or full automation. Any system developed should represent the organisations’ requirements from both a business and customer perspective.”
Wissmann says the basic requirements for a printer introducing automated workflows is a server-client configuration, “Depending on the amount of work these can be very different. Heidelberg finds suitable solutions in co-operation with the customer.”
“The Prinect Workflow offers modules covering the complete value chain, from MIS via pre-press, offset, and digital print to finishing,” he states. “Prinect offers a development path to a company that starts to realise it needs to adapt its current position in the market, no matter if the print shop is active in commercial print only, or also in packaging or label. Our recently announced additional Production Manager offering, which gives every print shop – even the smaller ones – the choice between licensing and renting the software it needs, will allow these clients to grow with their customers, and give them a clear roadmap on how to ensure the correct alignment towards not only today’s marketplace but more importantly how their future market dynamics can be incorporated.”
Do you need different setups for offset and digital? “The Prinect Workflow covers both offset and digital printing,” says Wissmann. “Since the introduction of Prinect DFE (Digital Front End) driving the digital ‘fire’ devices (Versafire, Labelfire, Primefire), we offer a single operating system for our customers who need a hybrid print (analogue and digital) business, ensuring continuity from both a workflow and colour management perspective – all available as standalone solutions – or integrated into a smart print shop’s complete workflow environment.
Heidelberg interacts with all the main MIS providers in the market and can deliver or receive the relevant XML, JDF and JMF files. Wissmann notes three defined levels of JDF integration: transferring basic job information like job name, number, run length (level one); transferring the process net (all production processes with assigned machines, duration and amounts) and layout data (stripping parameters) (level two); and transferring shopfloor data back from production to MIS via JMF (level three).
“The quality of such connectivity highly depends on the ability of the MIS supplier to write and read proper JDF data and requires testing efforts, especially after software upgrades,” he says. “With the Heidelberg MIS solution, the Prinect Business Manager, we go some steps further by directly sharing data with the Prinect production workflow in many areas. Job tracking in MIS is based on a direct view into production.
“The printer at the press will directly see if or when the paper for the next job will be available, just to give a further example.
“This scenario can be extended by connecting a Web Shop via an xml-based online connection (Prinect W2P Connector) to the Heidelberg MIS and production workflow. Orders from the web shop can be automatically processed in production by using a functionality called Smart Automation that selects the best-fit templates and production processes according to the product definition in the Web Shop.”
Wissmann explains that parts of the Prinect workflow are already cloud-capable today, namely the Smart Business Intelligence (Integrated reporting solution) and, for example, the remote approval or ordering functionalities. “Heidelberg is on the path of extending cloud service offerings step-by-step.”
Kodak
Peter Janusik, Kodak’s national sales manager, Unified Workflow Solutions, Australia & New Zealand, proposes that the most important part of implementing automation is to first understand the workflow and plan considered for automation. “For that, it is essential that the traditional skill sets are available. The best automation capabilities are of little use if not implemented with the practical requirements of production. Prinergy’s rules based automation (RBA) works by using triggers to start events or actions. With the installation of RBA, a printer can begin to immediately see ROI by simply implementing an archive strategy — the user’s natural progression of job status becomes the trigger for a timed archive. This sort of automation does not require IT skills and is easily implemented using the drag-and-drop visual interface.”
Prinergy’s RBA is used not only for automating production, but also for streamlining the running of a printshop, he says. “Over the past year, I have visited and seen how many customers are working with our RBA and notice that the more automation is implemented, the more time becomes available to invest in further automation. What is very important once the decision to develop automation is made, is that the business sticks to their plan and allows time for the first wave of automation to happen. They will then reap the benefits of being able to continue to invest in automation as more time is freed up.”
On digital-offset integration, Janusik says Prinergy should be the page production hub, regardless of the output type. “By leveraging RBA, all the printer needs to define would be a quantity – a rule based on that alone could make the determination for output. If less than X goes to digital, then greater than X goes to CTP, and Prinergy addresses all the set-up processes for each path.”
New to Prinergy in the latest version 8.1 is the ability to drive more varieties of digital press from within the main Prinergy UI, called Workshop. The new JDF/JMF connector enables a high level of flexibility in sending jobs to a digital press. In the past, most pre-press workflows relied on a pre-set JDF or a virtual printer, reducing flexibility. With Prinergy 8.1, sending a job to a specific digital press will bring up a dialogue showing the capabilities of that press, including media.
Janusik explains that Prinergy easily integrates with most MIS solutions that are based around JDF, by using Business Link. “This solution in itself is a form of automation, but it does not end there. Once again, triggers within the production workflow can notify, create and send pages to a variety of sources to meet internal needs – your sales/customer service – and external needs – your customer.
“W2P is even easier; as here you have finely tuned and constrained pieces of information that relate to specific products or types. Prinergy can read an XML schema, and use that to transform the W2P inputs into customised workflows, untouched by human hands.”
Kodak has taken a view that parts of the workflow can be cloud-based, and are already available, reports Janusik. “For example, with cloud storage now commonplace, the first stage of our Prinergy Cloud was to introduce cloud-based Archive. Even though Prinergy has an advanced archive option available for on-premise use, with internet speeds continuing to improve and the availability of a high level of redundancy, it was an obvious choice.
“Another cloud service is Decision Analytics, which mines the ‘dark data’ residing in the Prinergy database to help administrators understand how their system is performing. To back that up, Kodak now offers time-limited JTP licences allowing customer to ‘rent’ a process module for their busy periods.
“At the moment, we don’t see that there is a need to have core processes like rendering in the cloud. However, there will be more Prinergy Cloud services becoming available that will further enhance the ability to automate.”
Konica Minolta
Grant Thomas, product marketing manager, production print, at Konica Minolta, suggests that implementing a basic print workflow automation is relatively easy for any modern print professional, and once the automation rules are enabled and implemented, the automation benefit is ready to be used with little fuss.
“Workflow automation can be as simple as creating hot folders that complete the required actions for a ready-to-print file, to a highly complex workflow that has web submission and a multitude of rules-based automation that then sends the corrected file to the most appropriate print system available.
“The skills of many print operators are at a level that they understand the process that is being automated, and can easily be trained to implement advanced workflow automation. The majority of the software component can either be easily set up onsite by the operator after training, or training and assistance can be given online to skilled support staff,” he says.
AccurioPro Flux Premium is Konica Minolta’s software solution for professional print workflow automation and provides an essential tool to minimise costs and maximise ROI while providing efficiencies for operators and users, says Thomas.
“The overall viability of any workflow automation is the ability to reduce manual touch points; the reduction in manual touch points then allows operators to focus on other tasks, enabling greater efficiencies in the business. In most cases, print businesses will achieve the most benefit from workflow automation when they have two or more presses.
“These could be of many different makeups. One example would comprise one colour and one black-and-white digital press, where you would see the start of tangible benefits. With this combination of printers, the business can construct basic print workflows that can separate full colour from black-and-white prints, and take advantage of the cost benefit, as colour prints are much more expensive compared to black-and-white prints that are produced on a black-and-white press. Larger benefits can be seen when a digital press and a traditional offset press are combined in a hybrid automated workflow, where volumes and sheet size can determine where best to send the print jobs to create efficiencies and cost benefits.”
Thomas sees traditional offset and digital printing today being combined in workflow solutions, with positive outcomes, but he explains that there is a point where the process needs to be split in the workflow to process the print work. “This is normally designed in the workflow as a rule. The investment in workflow should be the starting point of the automation process for print providers, as this is the key component for internal efficiencies for a print business, as is the case in almost all businesses, he says.
The addition of other key elements of W2P and MIS solutions and how these integrate as one solution is key to the overall benefit that can be leveraged through the business.
Screen
Asked how easy it is to implement workflow automation, in terms of pre-existing typical printer skillsets, Peter Scott, managing director of Screen Australia, responds: “The short answer is: far easier today than it was ten years ago. Since CTP and rips, printers have had some IT skills of one kind or another, and with today’s workflows, such as our Equios (formerly TrueFlow), it is not hard to learn, as it uses hot folders and intuitive instructions. The GUI is logical and translates existing skill sets into understandable traditional skills – imposition, trapping, job ganging, colour management and so on.
“And it is always a good idea to have a workflow champion in any print business but in smaller family print shops, that can be the owner-operator him or herself. A knowledge of JDF and PDF files is a good thing.”
Scott describes Screen’s Equios as a highly scalable workflow that can be used by a single operator/terminal or multiple seats. It is also universal, so it can drive CTP-offset, print-on-demand digital, wide format and other technologies. “Because Screen is the largest manufacturer of variable-data continuous-feed inkjet printers, Equios is also ideally adaptable to VDP. This means the hardware requirement will vary, depending on software applications. In its basic form, we recommend a 64-bit Windows PC with Xeon Quadcore processor or higher, at least 8GB memory and 100GB available disk space. Equios works on both Macs and PCs, OS 10.10 or higher, and Windows 7, 8.1 or 10. For Equios Online, iPad iOS 9.3 or higher is recommended.”
What size does a business have to be to justify workflow automation? “You definitely do not need a fleet of presses to justify Equios,” says Scott. “We start with a basic one-terminal workstation that will drive CTP and a proofer. It is scalable so you can build from there.”
MIS and W2P integration is straightforward. “Any JDF-compliant MIS can be integrated with Equios using Job Ticket Format. Our EquiosNet partnership programme has agreements will major vendors of MIS. For W2P, the same thing; we offer an open interface and also Equios Online for remote client proofing and job approvals. Workflow is worth investing in at any level – partial, comprehensive or full automation. The key is to choose a workflow that is future-proof, such as Screen Equios.”
Cloud-based workflows are with us already, but, says Scott, “we find most printers prefer to host their own jobs onsite for security reasons, although the cloud will no doubt figure more prominently in the future.”
Comment below to have your say on this story.
If you have a news story or tip-off, get in touch at editorial@sprinter.com.au.
Sign up to the Sprinter newsletter