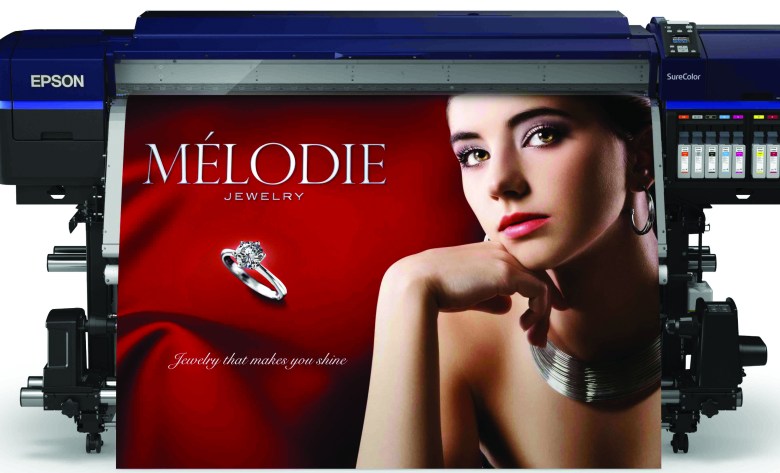
Wide format print was once a job by job operation, each order being independent of the next and customers accepted what was received. If they did not like it, the print provider could go back and try again to match the brand colour that was crucial to his client. This has evolved into an eye-ball matching process where the client is asked to select from a series of patches the colour that he or she believes provides the closest match to the target. Once agreed the setting for this colour on this material can be locked into the job.
If the former way of working was wasteful in terms of sometimes expensive materials and time, the latter is certainly wasteful in terms of time. Increasingly time is a precious commodity, partly due to the increased throughput that today’s generation of wide format printers deliver. If the printer is running close to 1,000sqm an hour, that is a lot of jobs to process. If that sort of throughput is confined to the likes of the Inca Onset X3 and high end Durst or HP Scitex machines, even moderate speed machines are looking at 200sqm an hour throughput. It makes no sense to have to set up different jobs step by step and to reach the ideal colour output through trial and error.
Consequently the wave of workflow automation that has swept across commercial printing is lapping at the ankles of wide format display printing. Where large campaigns are involved, where brand identity is a key element to the job, where multiple products are needed from one sheet of material, workflow is essential. And increasingly digital workflows are becoming available and being adopted where only a few years ago inkjet printers felt that they could cope without change.
In complex sets ups, multiple rips can control output through different output engines, much as high speed plate throughput in newspaper plants is achieved by directing plates to machines that are standing idle. The wide format world with different types of print technology, myriad substrates and print engines, is somewhat more complex than this, but the objective holds. In an ideal environment a job can be passed between different devices, adapting along the way in order to achieve the optimum output. The Onyx 12 rip includes the Onys Thrive workflow that includes JDF connectivity and what it calls Quick Sets to automate processes. These are hot folder workflows that can link different pre-determined production steps. There are four versions of Thrive supporting two to eight rips and up to six printers. The Production Manager function provides remote access to the workflow through a tablet computer. The colour management element of the workflow includes support for GCR ink savings, spot colours and compensation for substrates with optical brightening agents.
One of the most sophisticated of the workflow applications for wide format to date has its feet in the commercial print world. Agfa’s Asanti workflow shares a technology platform with Agfa’s well proven Apogee workflow, in use in hundreds of sites worldwide.
Asanti is the version specific to inkjet, and can manage a workflow from job submission through a web storefront to cutting out on the Acorta flatbed cutting table. En route it will pick up the colour output data for the job, for the material and for the print engine from the Asanti Mediahub. This stores the Calibrated Print Modules which enhance a standard ICC profile with wide format output specific data. Hence it will cope with white printing, with primer and varnish if used. It will optimise ink usage, both in terms of shifting between light cyan or light magenta inks to the denser versions if relevant and in terms of employing Grey Component Replacement to reduce the amount of expensive that is laid down.
In terms of file management, the software will optimise positioning on the sheet, nesting different components to achieve best use of the material. This data is passed to the Acorta cutting table, saving time and errors in setting up a cutting sequence and selecting the correct tool.
A set of colour profiles is supplied by Agfa, with users having the capability to create their own through measuring colour patches and referring these to the values in a look up table. The colour separation files is adjusted as a result and the values become the profile for that machine and that substrate. Asanti can take an output profile and make the adjustments according to the profile of a different print engine. Likewise it can be used to check that a printer remains calibrated.
Fujifilm’s XMF Colorpath carries out these calculations in the Cloud. The readings from a job are fed to the application and a suitable profile is supplied to ensure that whatever the device, the colour is as intended. This applies across litho, inkjet or toner digital printing. This can be by the logged on printer but can also be used to ensure that a number of different printers are working to the same colour output conditions.
Mimaki’s Color picker feature for its Rasterlink software works in a similar way, but is intended to equalise different Mimaki engines in the same print shop. The workflow also includes the sorts of features that are necessary in wide format printing: overlap areas, eyelet placement, knock outs for vehicle wraps for example.
Colour server specialist GMG developed a similar range of tools for its Production Manager workflow as an extension of its powerful Color Server tool. GMG prefers to use DeviceLink profiles rather than ICC profiles as these provide greater flexibility when moving between different colour spaces and manage the black channel in a more flexible way. It says that output and transitions are smoother with the DeviceLink profiles than by using ICC profiles.
Epson has developed its own colour look up tables which are used to ensure consistency across devices, regardless of location. This is designed for remote proofing applications, but also for distribute and print. The colour engine will also calculate the optimum combination of inks in SureColour printers to deliver the desired colour.
Whatever the approach, the colour managed workflow requires some input from the printer. The print engine needs to be well maintained and needs to be calibrated at least once a week, regardless of whether it seems to need it. Profiles can be built using a suitable spectrophotometer (and those used for sheetfed litho may not be appropriate), and a colour chart. The more patches there are to be measured, the greater the degree of accuracy. This can be automated to some extent and the number of patches varied to make profile building faster. Once logged, the process needs to be ongoing, checking and measuring to ensure consistency over time. The subject was featured in a presentation at the Fespa Digital show in Amsterdam introducing Process Standard Digital.
Workflows are about more than just colour management. Rips are being developed for flexibility and automation. Roland DG has recently announced a deal with Global Graphics to include its Harlequin software as part of a new Rip. Global Graphics has long provided the Jaws interpreter as part of a number of rips in wide format printing. The Harlequin rip is a more powerful tool and includes a much more sophisticated colour engine and can link more easily into wider workflows that include offset and cut sheet digital printing. Colour consistency needs to be demonstrated across all forms of output.
Chief technology officer Martin Bailey explains that brand owners are driving demand for consistency, from wide format to packaging so that in store materials have the same appearance. He points out that many will specify a Pantone colour, but can be using an out of date swatch book to do so. This may no longer be accurate. The majority of PMS colours are built into the Harlequin rip, updated as necessary. Profiling materials is a necessary step, and some merchants are starting to do this to support the substrates they sell in order to lower barriers to use. Use of GCR can often help consistency says Bailey, likewise profiles should be held as CMYK, converting into six colours if necessary.
A productive workflow is about more than managing colour. As machines become faster and turnaround times tighter, set up times need to follow suit. Add in the reducing skills base, and the need for simple set up systems increases. User interfaces need to become icon driven, using touch screens and using images of a job to reduce the risks of errors. Many old style interfaces have the look of systems designed by engineers rather than by anyone familiar with touch screen interfaces and the games consoles that press operators are more used to.
Inca for example redesigned the interface for its high speed Onset X printers. The operator can see an image of how the printed sheet will look on the bed, can be setting the next job while one is running, can call up pre loaded settings and so on. As well as enabling operators to keep up with the pace of production, it also reduces the risk of making mistakes under pressure. And that is as expensive and as wasteful as having to repeat a job because the colour is wrong.
For the moment, many in wide format believe they have no need to think about automating workflows. However, the advantage will fall to those that are not only implementing colour managed workflows, but who are also implementing them.
Comment below to have your say on this story.
If you have a news story or tip-off, get in touch at editorial@sprinter.com.au.
Sign up to the Sprinter newsletter