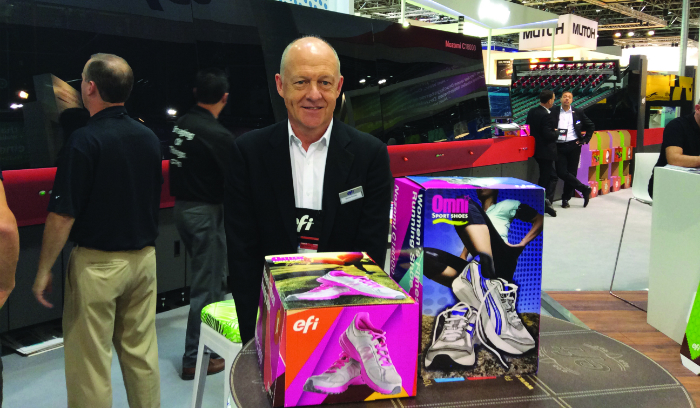
It is a natural progression up in capacity from the big flatbed industrial inkjets that are already fairly common sights in the sector to digital corrugated printing systems.
While installations are only just getting off the ground, the number of high-speed, high-cost digital corrugated presses announced at drupa earlier this year showed how seriously the suppliers are taking the prospect. Prices are all in the millions except for a hand-fed Xanté at about A$200,000.
Corrugated is a huge worldwide industry where market and technology changes are driving demand for high-quality printing. Conventional print processes here are flexography for direct printing onto brown or white kraft board, or web offset lithography onto white liner paper that is then laminated onto the rolls of brown fluted media. Digital equivalents are so far all inkjets of some sort.
Two years ago a Smithers Pira report, The Future of Digital Print for Packaging to 2019, said that conversion of corrugated board was 90 million tonnes in 2013 and would increase by over 22 million tonnes by 2019. The majority of print will remain analogue flexo and litho, but it forecast the highest growth in digital, expected to increase on average by 7.4 per cent year-on-year up to 2019. This followed growth of 13.5 per cent annually from 2009 to 2012, probably as flatbed inkjets were initially adopted.
Boxes are by far the largest use for corrugated, though there is a smaller display sector that uses it for things like large promotional items in stores and cinemas or POS end bins for supermarkets.
Corrugated boxes can contain and protect heavy items with less need for environmentally dubious expanded polystyrene: for retail use these boxes tend to be white with attractive colour printed designs to maximise shelf appeal.
Early adopters are just getting started, the world’s first Sun Automation CorrStream66 inkjet board press is in UK a production site. This 1,325mm wide, 71m/min machine went in as a beta in April and is now producing regular commercial work.
The company is HSG, its managing director Ben Ginesi says: “We do conventional flexo and quite a lot of litho laminating work. Five or six years ago I was talking to HP about digital. We decided to wait for single-pass technology. We wanted a progressive technology, rather than something that was more in the mature phase of its lifecycle.”
With six months experience under his belt, Ginesi says that throughput and running costs are not far off those of flexo. “Because a lot of the setting-up work is done off-line and we have refined the workflow to do that, we have very short set times, job to job,” he says. “We find that the machine’s square meterage output level is similar to flexo overall. It may be run slower than a flexo press, but it saves literally 40 minutes per set.
“When we were looking at the feasibility of the technology it became apparent that it was not all about machine speed, actually the key to making the technology successful was to become much more efficient in pre-press than conventionally a plant in our industry might be.”
Ink costs were also a big factor in his decision to choose the CorrStream, he says. It uses a water-based ink that’s food-safe. “There is a marked difference between what you pay for ink per litre and ink cost on the sheet,” says Ginesi. “For a lot of other systems I looked at, that was not a design concern. Let’s say your piece of board is 40c per square metre. The ink cost over a spread of 10 jobs on a UV liner printer I looked at will probably average 20c per sqm. So you are adding 50 per cent of the material cost into the job. The reality with the Sun system is it is adding five cents.”
The potential for digital presses in corrugated is much the same as in other print sectors: they allow very quick response to orders and they are economical for on-demand short runs, so customers don’t have to warehouse thousands of boxes that may become obsolete if there’s a change in the product appearance or printed information.
Ginesi is reluctant to name names, but says there have already been live projects that make use of the ability to change the printed image within a longer run. “Versioning and personalisation are becoming powerful parts of the technology,” he says. “Customers can come to us and say ‘I do not want a 3,000 minimum run, I would like a price for a 10,000 bulk quantity, but I would like to order it with a mix of images – 2,900 of one, 5,500 of another and so on.’ “It is effectively allowing them a choice in terms of how they split their print run. It is a different cost model to flexo.”
If you want a CorrStream of your own you are looking at list prices between A$3.5m and A$5m depending on width. Rivals’ prices we have heard of are much the same or higher depending on speed and width and the wild card of exchange rate.
New players
Back in 2014 only Sun Automation and Barberan had actually built fast single-pass inkjets for corrugated boards, while Bobst was working with Kodak on one. Today Sun has its HSG installation, Barberan reportedly has five or six, and Bobst has two test presses in commercial sites, with another built and due to go in.
Since 2014 there have also have been launches or announcements by Durst, EFI, HP (several), Screen/Inca Digital/BHS and an update from Xanté to it’s a $200,000 manual-load Excelagraphix. Some use water-based inks, other UV-curing.
The real challenge has been the materials handling – how to shift big, heavy sheets of corrugated board into and through a press, when they are also floppy and prone to warping and dust.
Many of the developers of high-speed digital corrugated presses already have some experience in related processes: Bobst is an established corrugated flexo press and boxmaking machinery maker, Sun Automation makes lead-edge feeders and ink systems for corrugated presses (and worked with Inca Digital and Sun Chemical on the FastJet corrugated project ten years ago), Barberan developed inkjets for heavy flooring and laminates before adapting them for corrugated, while Screen and its Inca subsidiary have teamed up with the big corrugating machinery maker BHS to make a hybrid printer.
HP has had an association with corrugated since the early 2000s, when the Israeli start-up Aprion was developing an early inkjet corrugated press called CorJet when it was acquired by Scitex Vision, which is now HP Scitex. Apart from its dedicated corrugated flatbeds, HP offers a simplex PageWide T400S and worked with KBA on the 2.8m-wide T1100S, both for corrugated liner printing. At drupa it announced PageWide C500, a forthcoming board printer.
Warping apart, the materials handling challenge for corrugated board is similar to that in the ceramic tile industry, which has seen a remarkably fast take-up of single-pass inkjets in the past seven years. It is no coincidence that EFI Cretaprint, a Spain-based builder of inkjets for tiles, is the factory behind EFI’s drupa launch of the Nozomi UV-LED inkjet for fast corrugated print. Durst also makes single-pass ceramic tile printers.
Digital corrugated summit
Late last year Fespa, an association which serves industrial printers as well as sign and display, held a Digital Corrugated Summit. This was sponsored by HP and included speakers from packaging software and cutting table supplier Esko, brand agency Studio Minerva, corrugated converter Swanline Print Group (which uses HP FB1000 UV flatbeds for digital work) and materials supplier Smurfit Kappa.
The summit was organised by Peter Kiddell, a consultant and director of Fespa. He says digital lets corrugated producers addresses changing markets, commenting, “Retailing is a rapidly changing sector. Customers are making decisions on the net and then coming to them and saying ‘this is nice.’ It is a change of the way people look at packaging, and we are reflecting that in the event.
“Also, say you order a widget over the web. If the box it arrives in looks particularly attractive, it is not just for protection, it is actually bringing some excitement to the product.
“Runs are getting shorter and the needs of producing specific information is increasing. And the way to deal with it is with digital print technology and the ancillary processes.”
Comment below to have your say on this story.
If you have a news story or tip-off, get in touch at editorial@sprinter.com.au.
Sign up to the Sprinter newsletter