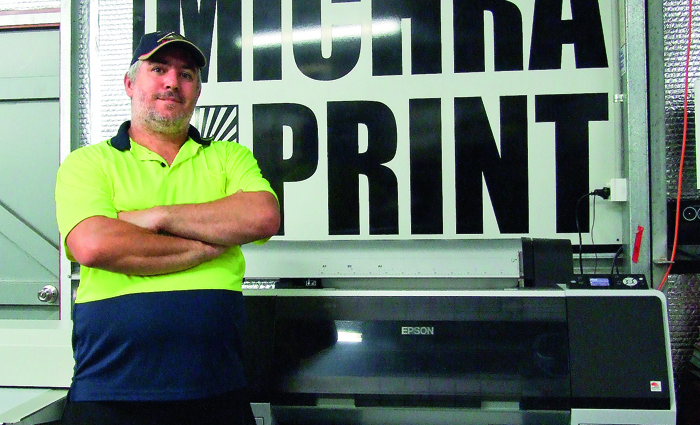
Describe your business
I run a one-man operation, based in Narangba in Brisbane. The company specialises in NCR docket book printing and spot colour printing, as well as small-run diecutting and embossing. We have a pair of Heidelberg GTO 46 presses and specialise in jobbing work for printers.
What have you bought?
An Epson 7900CTP engine and baking unit from G2 Solutions.
What does it do?
It is a platesetter based on a modified Epson wide-format printer that can image aluminium plates. I see the potential for this to be as revolutionary as when small offset presses came out in the 1980s.
Did you consider any other products?
I also considered a Kimosetter, but it was a much more expensive option.
Why did you choose the Epson?
The capability of producing smooth screens and quality halftone images was a must. As soon as I became aware of the Epson’s price and capability, it was like a shoe that just fits. I quickly decided it was the best replacement for the imagesetter. The bonus of being able to print high-quality colour was a plus.
When was the system installed?
Late September 2012.
Did it replace anything?
An ageing Dainippon Screen imagesetter, which offered excellent quality but was getting old and unreliable.
What benefits has it brought?
We are saving considerably on chemicals and film to produce plates. Every day I am learning more about adapting to the different way of producing a plate.
Are you pleased with the investment?
I am confident that we now have a more reliable plating system in place. To replace a Dainippon Screen imagesetter on a tight budget was a big ask because the results from that system were very good. But with the age of that older device, a replacement was necessary.
I believe the Epson 7900CTP is the best value system for any small offset printer looking to change to chemical-free or to upgrade from silvermaster.
What is the quality like?
When you print for other printers, you have to be a perfectionist. The plates are very close to the quality I enjoyed with film plus pre-sensitised plates but without all the processing, apart from the baking. My plates are GTO 46 plates and my other main concern was the ability to produce consistently straight plates, but I have been pleased with this aspects of the new device. I have found the plates not only to be consistently straight but have found the images to be extremely square.
How reliable are the plates after processing?
I have noticed that the baked image is not strong enough to withstand solvents on press. A lot of care is needed when cleaning these plates, especially as we are used to the durability of pre-sensitised plates. I find the plates run cleaner more quickly when I have pre-wet the plate before makeready. I am running bareback dampers with Varn alcohol-free fountain solution at 2.25% with my own rainwater.
Even without pre-wetting, they will soon clean up after 30-60 revolutions of the press. Running up the plates faster would be easier if you were to run a sponge over plate with fountain, like you would for a silver master before running. The plates are more stable during a run once you achieve your water balance, and the water balance window is much wider.
The other thing I have noticed is the ability for the screens to stay more open. As any GTO operator knows, this is a challenge for a small press at 150 lines per inch. It seems the non-image of the plate is highly hydrophilic and this seems to really help to keep the screens open.
What else do you like?
I’ve noticed the ink on the image is less prone to drastically washing out. All in all, the plates aren’t hard to work with and I think the only challenge with the plates is preserving the image over long run lengths. The longest run I have done so far is 16,000 plus overs; it survived that run even against the NCR chemical, which is destructive to most silver images.
Who is this machine right for?
I would recommend this to any small offset printer running a one- or two-colour GTO, Itek or similar presses. Although I have not run process work with these plates, I imagine they would do a reasonable job, maybe even perfect. I’d recommend to anyone using silver-master plates to seriously consider the change to the Epson CTP. I would also recommend this to anyone who out-sources film as a way of getting to plate in-house at a comparative low cost to implement.
Supplier’s response
The Epson CTP system driven by Xitron RIP was the obvious solution to Michra Print’s plate production requirements. After G2 discussed at length the pros and cons of the solution with Chris Watson, it was decided the system ticked all the relevant boxes. Chris was on board from the start and has worked closely with G2 providing hands-on experience to get the system working to its full potential. Chris has been involved in every way, from what was best from a printing press perspective, right down to what was best from the Epson 7900 and Xitron software.
Comment below to have your say on this story.
If you have a news story or tip-off, get in touch at editorial@sprinter.com.au.
Sign up to the Sprinter newsletter