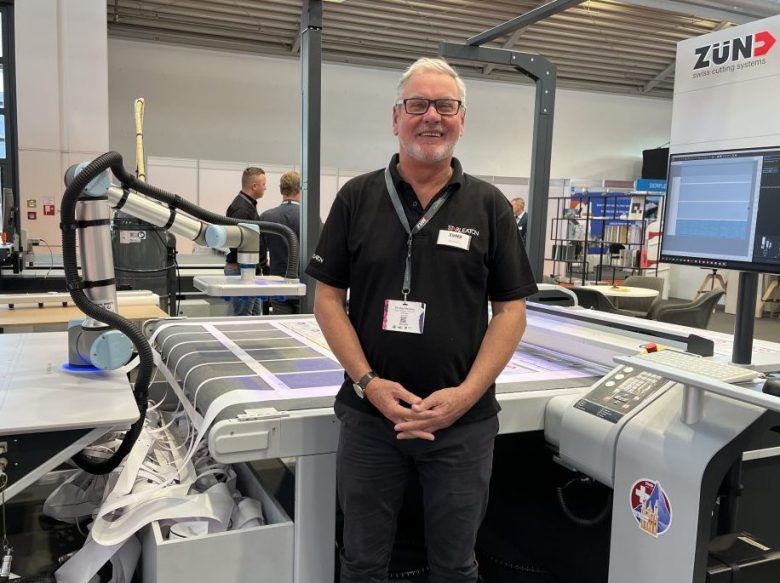
Above: Starleaton senior manager, industrial, Dale Hawkins on the Zünd stand at FESPA
Visitors to the Zünd stand at FESPA Munich last month learnt about the company’s new Q-line integrated system solution for autonomous, pallet-to-pallet production, and saw demonstrations of the company’s various systems, software and solutions.
In the spotlight (although not on display) was the launch of the new Q-Line with BHS180 board handling system. This is a fully integrated system solution for autonomous, pallet-to-pallet production, specifically intended for the demands of highly automated, industrial finishing of printed boards for displays and packaging.
The individual components – board feeder with the Undercam, the new Q-Line cutter generation, and the off-load unit – are optimally coordinated and offer impressive cutting accuracy and reliability.
Zünd products are available in Australia from Starleaton.
“Zünd has created innovative features around the new system, which contains beams made of carbon fibre-reinforced plastic. The result is that the system can generate an impressive speed of up to 2.8 m/s,” Starleaton senior manager of industrial Dale Hawkins said, pointing out that new substructure for Q-Line cutters is made from extremely stable concrete.
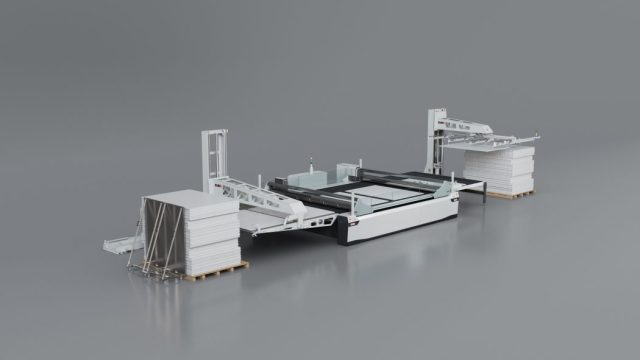
Other notable features include:
- Its ability to remove bottlenecks in digital cutting by eliminating the need for manual material handling.
- The Undercam integrated in the board feeder captures the precise location of the image printed on the board. It reliably identifies any distortions in the print, compensates for them, and perfectly matches the cut to the print every time. With every scan, the software adjusts the cut paths to the printed image, on the fly and in real time, significantly reducing the cycle time for each job.
- During the feeding process, sensors capture the edges of the material, and the board is correctly aligned. If the board is not within tolerance, the board feeder grabs the board once more and realigns it so that it can be fed onto the cutter without interruption.
“A company can actually have true ‘lights out’ production with the new Q-Line systems – once the jobs are set up, an operator can go home for the night, and will find them completed in the morning,” he explained.
Although not currently available in Australia, five lucky Australians were given a live preview of the system at Zünd’s factory in Altstetten, prior to FESPA.
Videos and further details on the new system can be provided on request, by Hawkins.
Highlights on the Zünd stand were:
(1) Demonstrations of Zünd’s digital cutting systems, combined with intelligent software tools and various solutions for automated material handling showed how autonomous, unsupervised, and highly efficient production could be achieved regardless of company size.
(2) Zünd software and analytics, such as Zünd Connect, monitoring and analysing software which identifies optimisation potential in the production workflow, and determines the KPIs of the Zünd cutters connected to it, and uses these to calculate their efficiency.
“Zünd has a focus on workflow and helping customers understand how well their cutters are performing. For example, when experiencing bottlenecks in cutting, some may be inclined to consider investing in new equipment or second shifts. By utilising our software and analytics, they can instead determine the performance of the cutter first and then address what needs to be improved,” Hawkins said.
(3) Zünd’s Robot PortaTable 130 from Universal Robots, which consists of a mobile off-load table equipped with a robotic arm, that can be quickly and easily set up and moved from one Zünd cutter to another, were performing functions on the stand usually carried out by human workers, such as automatically picking and sorting finished parts, ensuring consistent, uninterrupted production.
“One robot on our stand has been picking up decals and stickers and putting them into boxes to getting ready for shipping, while another was picking up and placing posters into a file and the other was picking up material and putting it into the cutter,” Hawkins explained, adding that the robots, which don’t require human intervention, are also human friendly.
Comment below to have your say on this story.
If you have a news story or tip-off, get in touch at editorial@sprinter.com.au.
Sign up to the Sprinter newsletter