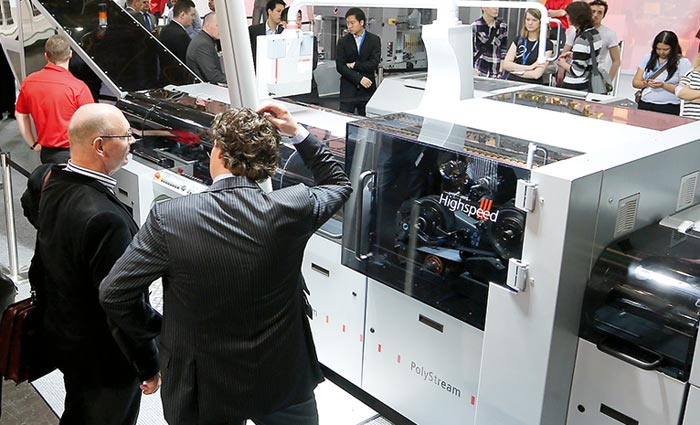

One reason digital is attractive for short-run production is its integration of finishing. Post-press manufacturers have embraced automation and high-speed digital. As run lengths fall, makers of digital printing and finishing products have found a marriage made in heaven.
At Drupa, 20 Hunkeler lines consisting of more than 85 modules were set up on 14 different digital print, finishing and mail inserting partner booths. Systems are tailored to meet the application requirements of the commercial print, book publishing, data centre, transpromo, financial and DM markets.
Hunkeler introduced its Starwheel Stacker with glue dots, which was part of a complete bookbinding workflow that begins with pre-printed digital rolls up to 30 inches wide. The standard Hunkeler double plow-fold module applies one or two folds in the web direction as needed before the CS6 cutter converts the multiple-up imposition into book blocks, which are then glued and stacked as 4-, 6-, or 8-page signatures. From there, the glued book blocks are transferred to a near-line perfect binder for book finishing. The signature book block solution is capable of running at speeds up to 653 feet per minute, and 450 output cycles per hour (multiple books per cycle), for offline or inline production.
Muller Martini displayed 10 machines including variable size web-offset presses, saddlestitchers, perfect binders, hardcover systems, newspaper mailroom systems as well as systems for modern digital book production.
Canon and Océ continue to work closely. A high-capacity stacker has been co-developed and works alongside an open, standard finishing device interface that offers unlimited stacking capacity via an ‘unload-while-printing’ functionality that facilitates continuous production. It has a high stacking capability to configure stack height and ensure exact output to input if post-processing is done at another location. There is also the option of re-using the original box in which the paper was delivered.
CP Bourg demonstrated a desktop duplication technology that allows an operator with a wireless computer to monitor, control and diagnose sheet feeders, bookletmakers and perfect binders from anywhere within the reach of a secure wifi network. This is the first implementation of print finishing products operated remotely through a mobile computing device. The demonstration showed how an operator or supervisor using an Apple iPad can start, stop, change or query operating parameters, enable diagnostics, and track the performance
of any CP Bourg finisher.
With the steady penetration of digital into the offset printing space, print shops, mailing services and transactional printers do not want an offset workflow with separate bindery components with the work being moved from one to the other. They are looking for finishing systems that mirror the way their digital solutions work with a smooth in-line or near-line production process and lots of automation.
There were also a host of JDF-compliant systems on the latest bindery equipment for all types of applications. Interactive, icon-based touchscreen interfaces are almost ubiquitous. The ability to archive jobs for future use is becoming more common, and many systems also incorporate training videos and presentations.
GBC had the fastest lamination speed. Its 8500HS Cyclone laminated 102.2m2 of paper in 40.53 seconds. Heidelberg, Manroland, Komori and Ryobi showcased enhancements in cold foiling. New coating capabilities offered users more ways to add value and differentiate their printed pieces.
Some finishing manufacturers are integrating digital finishing on their finishing platforms. New inkjet and toner continuous post-press systems from Lasermax Roll Systems, Hunkeler, Kern, EMT, Magnum Digital, Muller Martini and Kolbus were debuted.
No discussion of Drupa would be complete without noting Highcon. Its Euclid machine combines patent-pending Digital Adhesive Rule Technol-ogy (DART) to create the digital crease lines with a unique high-speed and high-quality laser cutting solution. Highcon has totally re-engineered the die-cutting and creasing process. Rather than using a single die for cutting and creasing, the firm has separated the two processes out. Creasing rules are embossed into the board using a rotary die matrix produced using Highcon’s DART process. Consumables for DART are foil, or base sheet on which the creasing matrix is made up, and the UV-cured polymer used to make the rules
The creasing rules are produced by applying a special UV-cured polymer to the base foil. The result is a robust and yet rapidly produced die. Highcon talks about Euclid being suitable for runs up to 10,000 sheets.
Lasers are used to cut the boards, providing a quick and accurate counterpart to the creasing. Pricing for Euclid has yet to be finalised, but the company expects the production of an average die to use $300 of materials. Simpler dies with less folding crease lines will cost less, while more complex dies will cost more.
Frank Romano is professor emeritus at the Rochester Institute of Technology
Comment below to have your say on this story.
If you have a news story or tip-off, get in touch at editorial@sprinter.com.au.
Sign up to the Sprinter newsletter