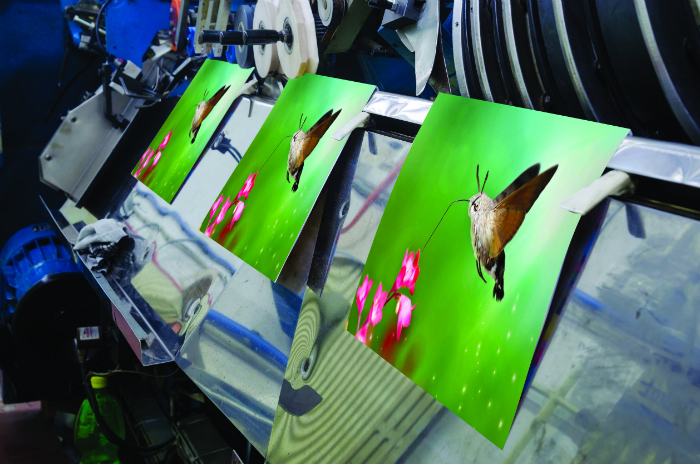
What are the best options for finishing at print businesses which have digital printing? Do you invest in the onboard extras that can be integrated inline into digital printing systems from the major press vendors? Or do you need to sink some of your hard-earned into a standalone offline finishing kit? And is your existing litho offset bindery machinery up to the job of finishing your digital printing?
And beyond that, what opportunities exist for digital printers to add value in finishing? Hard pressed printers are looking for every opportunity to create margin – primarily by adding value and cutting costs. What do today’s digital print finishing solutions offer printers to help them to achieve these twin aims?
At multimedia Frontline
At Frontline Printing, a 32-year-old Sydney-based pioneer of digital printing, the finishing is a blend of inline scoring and saddle-stitching on its Ricoh 7110, sourced from Ricoh Australia, and a Morgana DigiFold and Morgana Major (the latter for higher volumes), sourced from Ferrostaal Australia.
Located at Artarmon with 13 staff Frontline offers flyers, cards, two-pass folded work, pre-folded booklets, celloglazed score-and-folding, and eight-page folded flyers. But nowhere does that synthesis of inline and offline bindery come together more than for Frontline’s latest project, a multimedia marketing campaign for – what else – but Ricoh presses — for client Ricoh Australia.
Frontline’s managing director Wayne Godsell describes the smart printed piece: it is printed on a 10mm-gauge A5 sheet, bifolded, with sensors that activate a miniature video screen that springs to life with a choice of full-colour video clips, with audio track, advertising Ricoh’s presses. What better example of the medium being the message?
The pieces are pre-scored on the Morgana DigiFold to become a fold-out document. Godsell is a great believer in pre-scoring on toner work, to minimise toner cracking. The 700mm-long sheets are printed VDP on the 7110 – personalised to the recipient — and spot-varnished inline on the press. Diecuts are done on a Heidelberg Platen, and the screens are glued in place, with trimming on a Polar 66 guillotine, explains Godsell.
Frontline imports the dedicated multimedia 110 x 60 mm LED screens from China. The wafer-thin screens derive their content from a microchip glued into the printed matter, and pre-loaded with Ricoh’s video clips, and their power comes from a tiny battery that averages a year’s life with moderate usage.
Also on Frontline’s order books has been a VDP job involving a mailout of 4,000 pieces using VDP on a six-page folder comprising 700mm sheets and printed addresses directly onto the envelopes.
“The sheets ran perfectly with VDP,” recalls Godsell. “And the 4,000 individually addressed envelopes which were metallic silver passed through the Ricoh with no jams. Two years ago, we couldn’t do a job like this, at that volume,” he says.
The business switched to the Ricoh press in July last year, as Godsell and his team were impressed by all the boxes it ticked – spot varnish, white toner, ability to print long (700mm) sheets and an envelope feeder.
Frontline is a digital-only provider and has never printed litho. But five years ago, it diversified into wide format, with a series of signage and vehicle wrapping jobs that now keep its two Rolands, two Canons and a Mimaki press occupied.
What the vendors say
Currie Group managing director Bernie Robinson is a firm believer in both inline and offline finishing solutions. For example, you can connect a Horizon SPF-200L booklet maker inline to an HP Indigo 5600 or 7800 and you can add a Horizon HOF- 400 high-speed offline feeder. You can take a pre-printed cover and merge it with the book-block. “My preferred option is offline, because digital presses are made to print, they’re not made to finish. But it’s horses for courses, and we can provide the best of both worlds,” he says. Another factor is that while a sheetfed job is being finished, it slows the upstream printing on the same line, so there are no real productivity gains from being all inline.
“For example, with perfect binding, you need to hand-feed the book-block from the digital press into a perfect binder. The Horizon SPF-200L can do 4,500 sets per hour. Digital press speeds can’t match that, so you’re better off finishing offline via a robotic feeder,” he says.
In addition, barcode set-up enables unique configurations within a single print run, lessening the need for separate set-ups in a variable job lot.
Robinson says Horizon’s SmartSlitter, a perforator-creaser-cutter specially designed for finishing A3 digital print, uses the same dies as Horizon’s CRF-362, but can do a lot more. It can do a ticket on a tee, with stop-start perforating in the direction of the sheet. It also performs scoring and provides for manual perforating, for four-to-six perfs on an A3 sheet. It will do a tear-off. It can also do business cards and greeting cards, cutting and creasing from an A3 sheet – all with barcoding, including barcoded stop-starts, in code-39 and QR options. “Every second sheet can be different,” says Robinson of the barcoded slitting.
The SmartSlitter was on show at the Visual Impact show in Brisbane in April this year, where it drew a lot of traffic to the Currie Group Mobile Showroom. “We demonstrated it with five different pre-printed items and it sets up five times within a matter of two-to-three minutes. That means five jobs finished within minutes,” he explains.
Meanwhile, the CRF-362 creaser-folder will take pre-printed digital work, crease the spine, with two creases and two perfs on an A3 sheet, top to bottom, and also has two buckle plates. “Again, all the Horizon gear has memories for 200 programmes, with provision to download configurations to a USB stick, and clear the onboard drive for a further 200 programmes.”
And a Horizon SmartStacker is a B2 stacker that integrates with a HP Indigo Digital Press for scoring, perforating and slitting – computerised and able to finish a job on the run, says Robinson. Smart stitching of digital rollform is taken care of with a StitchLiner 6000, connected to a Hunkeler system for sheeting and creation of book blocks.
Heidelberg ANZ post-press product manager Brian Evans says some of the onboard finishing available today is adequate for digital print work. “Three-side trimming, stitching and punching are three processes that work well with online digital print engines. However many other processes often need to be included and for these functions, offline finishing machinery is required.”
Evans believes a range of offset equipment can be used in conjunction with digital printing. “Card cutters, die-cutters, scoring and slitting devices are just a few examples.”
Creasing is a major issue with stock printed digitally, and Heidelberg offers a range of products that can help eliminate this problem. Heidelberg’s Ti52 inline scorer performs what Evans sees as a basic of digital folding. The Ti52 is designed for high speed, accurate folding, he says. Most suppliers can provide scoring inline, but accuracy at speed is a more challenging task and one which Heidelberg has been able to solve, he explains.
Heidelberg also offers its CH56KT folder, which has made a major impression in Europe. Meanwhile, for cutting, there are the Polar 56ECO and NET models, Polar 66ECO and NET, Polar 80ECO and NET, Polar 78ECO and Plus, and Pro models, as well as the Polar Guillo-crease.
Evans says that with digital print’s popularity and most offset printers now also having a designated digital print room, ‘cutters and folding machines can be used for both digital and offset and with the appropriate accessories, most digital work can be processed’.
“Most digital print shops will have their own finishing machinery that stands alongside the digital print engine and is suited for the short run work,” he states. In fact, he points out that printing often starts with post-press, that is, cutting of sheets prior to printing.
According to Nathan Broughton, national product manager at Ferrostaal Australia’s digital and offset finishing division, vendors today offer a range of finishing solutions inline with the print engine, some of which come in at low investment costs, and can add value to the end product without the need for additional processes.
He says one such machine is Morgana Digifold Pro, which can crease to remove any paper or toner cracking and fold in one process. This multi-step process achieves the same level of quality as traditional offset procedures.
“This is an attractive concept, however when the printer investigates further, they find that the total solution is not always as flexible as they need. Many of the inline finishing units can slow the printing process considerably and there is usually a need to trim the products before finishing as a folded brochure or making a booklet. Additional click charges can also apply if the product requires multiple processes and then is required to be re-fed through the print engine to finish the products,” he says.
Broughton believes that in some cases traditional offset finishing equipment can be useful to finish the end product but, in most cases, printers would do well to consider the difference of using finishing equipment that has been specifically designed to produce digitally printed products.
“One point in particular to note is the amount of sheets required to make ready when using offset finishing equipment, which can require up to 50 sheets to set up, whereas a machine doing the same job from the digital finishing specialist such as Morgana generally only require one or two sheets to set. Time to set up the machines is also something to consider, as most digital finishing equipment is set up in a matter of seconds, which obviously improve the all-important turnaround time to deliver the job,” he says.
“Today’s digital print finishing equipment is designed to take away the need for highly skilled operators and make the process of print finishing very simple and user friendly. This can immediately improve the bottom line by cross-skilling staff without the need for specialist operators to output high quality products. The equipment is usually very versatile,” notes Broughton, “and often one machine can handle a range of processes that can add value to the end-product.”
Chris Pettitt, marketing manager of finishing specialist Neopost, says nowadays digital finishing has become part of general postpress. For instance, Neopost’s Ucos UD-300 rotary cylinder die cutter, while noted for its specialisation with digital print, is also adept at short-run creasing and perforation of offset print.
Neopost’s DS-200 folder and inserter performs standard mailer insertion and booklet inserts. And Duplo’s upgraded range of DocuCutters, including the DC-646, an upgrade of popular DC-645, are making inroads. Duplo has added to its range of booklet makers with the DBM-600 for landscape booklets, augmenting the DBM-500.
Graph-Pak’s Thermotype range from the US has attracted interest, says managing director Tom Ralph, particularly its NSF foil presses, which provide die cutting, hot foil stamping, foil fusing, creasing, dimensional embossing, single-level embossing, numbering, hologram placements, perforating and crash printing – all in a single device.
To show ROI and keep margins low, a bindery needs to offer rapid makeready, low wastage, and flexible kit, argues Ralph. Robustness and operability at low skill levels are also advantages in the digital bindery, he finds.
The maturing of cloud technology has taken a huge bite out of content provision by university in-plants for students’ reading materials, with syllabus content ready to download at students’ fingertips.
But specialised roles for tertiary-institution print centres remain, and there are ways for in-plants to cut margin and maintain themselves as profit centres, explains Rowan Brown, senior team leader, campus services, at Deakin University’s logistics department, based at Burwood, in eastern Melbourne.
Brown, who has printed with Deakin for 22 years of its almost 40 years of operation, has seen a lot of changes. He reports that web-to-print cloud access via computers in Deakin’s libraries – or even on students’ smartphones — has cut his print centre’s output from 150 million black-and-white impressions a year seven years ago down to a present figure of around six million.
A decade ago, a lot of the output was for students, printed offset, mainly in black-and-white, with some spot colours – at three in-plants. The centre’s two-colour press and perfectors were the workhorses that churned out the volume. Since then, in-plants at Geelong and Warrnambool have been closed. Today, print is specialised, mainly servicing staff requirements, a lot more of it in four-colour, generated in micro-runs (typically 100 A4 by six sheets) and fully digital.
And while teaching and administrative staff have access to green-button printing on a range of multifunction devices, when it comes to documents that need to be printed on better stock, or from fussy files in need of a prepress cleanup, or impositioning, or the addition of logos and other branding, the in-plant is still the place to ask. And then there is the display material – banners, wobblers and similar – printed professionally in wide-format.
By increasing efficiencies in finishing, Brown and his team at Deakin Print Services are able to provide cost effective printed collateral for the teaching faculty at Deakin’s Victorian campuses at Melbourne-Burwood, Geelong-Waterfront, Geelong-Waurn Ponds and Warrnambool. These include prac notes for a wide range of classes and exam papers for all campuses, as well as course handouts and some student notes. The Burwood print facility, which has two staff, offers overnight delivery to the other campuses.
A major focus nowadays is printing Deakin’s marketing materials, which include brochures, flyers and pull-up banners and conference banners. These are generated on Deakin’s Canon-Océ presses, which include a 250ppm Océ VarioPrint 6250 and a 100ppm VarioPrint 2110 for mono, and two Canon ImagePress C7000VP presses and a wide-format Canon imagePrograf IPF8400 for colour work.
Brown explains that Deakin’s trimester calendar, in contrast to the more widely used semesters at other universities, enables students to finish courses more quickly, which attracts overseas students to the university. It also means shorter, more frequent runs of teaching materials and exam papers, that need to be produced three times a year at 14-week intervals.
“Inline stapling on the 6250 and 2110 and inline saddlestitching, booklet making and one-page A3/A4 and A4/A5 folding on the CV700s is useful up to a point, but greater efficiencies are only found offline,” he says. “With the inline features, we didn’t have the opportunity to do gatefolds or trifolds.”
A Shoei Star folder filled that requirement, says Brown, but the Shoei was a hangover from the offset era and struggled to handle toner printed documents, which were liable to show cracking.
The hunt was on for a dedicated digital folder, with Brown, who is also southern branch manager of NIPPA (Network of Inhouse Print Professionals of Australia), conducting extensive research, including a visit to PacPrint 2013.
The upshot was the selection of a Morgana DigiFold Pro from Ferrostaal Australia in January this year, which was added to a bindery already sporting a Wohlenberg guillotine, Horizon saddle stitcher, Stahl drill and a hot-laminator from Hilton Laminating.
The DigiFold’s set-up times are minimal, and there are very few paper jams. The only downside is it does not handle stock under 90gsm very smoothly, and Brown generally will not go below 100gsm for jobs to be folded on the DigiFold.
However, the new machine has helped Deakin Print Services to meet and exceed its new requirements.
Brown says: “The DigiFold Pro also enables perforating and its smaller footprint makes life easier.”
Comment below to have your say on this story.
If you have a news story or tip-off, get in touch at editorial@sprinter.com.au.
Sign up to the Sprinter newsletter