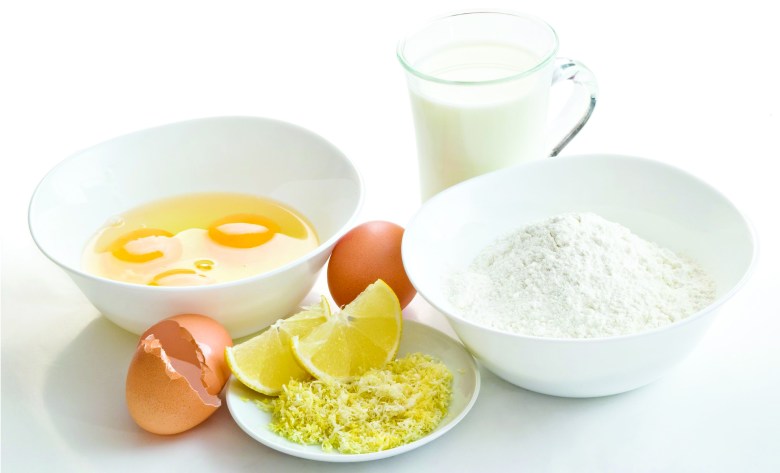
The choice of consumables a business makes can have a big impact on that business. Once this was the preserve of the operations team, and inks and blankets on a litho press were apt to chance following a visit from a persuasive sales rep. Today, with modern, highly tuned presses there is no time for the arguments which inevitably followed when job went wrong: the ink supplier blames the paper, paper supplier blames blanket, and blanket supplier blames the ink in some negative version of rock, paper, scissors. Today printers must be more careful about the choice of consumables to suit a press which will run at 15,000 sheets an hour or more.
The choice of consumables is also becoming important to press suppliers, each of whom can provide preferred products with their presses. Heidelberg has its extensive Saphira products to suit the needs across its customer range, all the other press manufacturers will also supply approved consumables products. There are major benefits in buying your consumables from your press suppliers, the primary one in having just one point of contact when things go awry.
There are two key drivers behind this: performance in terms of predictable productivity and performance also in terms of environmental impact. Those printers seeking the optimum performance from their presses will push suppliers hardest. In the UK, ESP has a reputation for the squeezing the most production from a Heidelberg sheetfed press, regularly setting new production records as minutes then seconds are shaved off make ready time. One of the secrets to this are in the inks and fount solutions used. ESP worked with ink supplier Huber to come up with an ink which would run at 18,000sph without causing misting in the press room, and which would remain stable during the seconds that the press accelerated from a couple of thousand sheets an hour to obtain the pass sheet to 18,000sph production speed, and back to zero only a few minutes later. The company needed to test founts and blankets in the same way, eventually settling on a blanket that is specified for carton printing rather than commercial print.
Not every printer wants to push production to these sorts of limits, but everyone wants to operate a press that performs in a predictable manner with different papers, jobs and operators. This is the proposition behind press manufacturers’ consumables portfolio. The products have been tested by the manufacturers to work in combination on its presses. It makes solving problems when they do arise much simpler. Instead of a collection of suppliers to accuse, the only number to call belongs to press supplier. For the customer the advantage is that there is a single source of supply and he can concentrate on running the business with a major variable under control.
As new generation UV printing grows in importance matching press and consumables is essential. Komori sells H-UV with a package of consumables including ink, fount, blankets and washes with which it can guarantee performance on press. The ink came from Toyo which had worked on development of the technology with Komori from lab to commercial roll out. Most customers have remained with this combination despite the cost of the ink. Komori has also approved other inks to run on the machines which broadens the scope for negotiation, but will point to its guarantee if a company uses a non-endorsed product and subsequently has production problems.
In LED UV printing, Flint has led the way with its Xcura inks, with Heidelberg now offering a Saphira branded ink as it rolls out LED UV drying on its sheetfed presses. The strategy for the company is to reach 50 per cent of revenues from service and consumables and, as it has supplied 50 per cent of the addressable market with presses, there is a strong belief that this will be achievable. Currently service and consumables account for 40 per cent of Heidelberg’s sales. Consumables revenue will help the business iron out the cyclical nature of equipment sales and keep customers in contact with the Heidelberg brand.
The portfolio of Saphira products includes those that are designed to improve environmental performance, founts without VOCs, plates that reduce demand for chemistry and so on. It is a major issue in Germany and aligns with its ability to supply presses where carbon generated in construction has been offset.
The drive for a more sustainable way of printing has pushed each of the world’s three major plate suppliers into products that require little chemistry in processing or which can be developed on press. Agfa’s Azura has been in the market for a decade, expanding from a niche product for smaller printers wanting a more environmental plate or one that eliminated the need for processing chemistry, its management and disposal, into a plate that covers almost all sectors of the market. The Azura TU is suited to all applications save web offset, very long run sheetfed, UV and carton printing. It remains a plate which is washed and then gummed before mounting on press, so is not a develop on press plate.
For many years these have been promised as the ultimate product for those wishing the simplest plate to handle, and with a lack of chemistry, the most consistent. Various approaches have been tried over the years, but develop on press had remained inside just outside the mainstream. The introduction of Kodak’s Sonora plate has changed that. It has greater on press latitude, a higher contrast latent image, much improved run length and does not slow the platesetter to a crawl when imaging. It uses less water, less electricity because there is no processor and is flying off the shelves. Kodak opened a new production line for Sonora in the US this year and notes a 63 per cent growth in volume this year CEO Jeff Clarke told a recent analysts meeting. Agfa has developed a develop on press version of Azura, the Azura TE, to offer when there is a head to head clash between the two companies.
Some suppliers are now providing integrated solutions. The concept is that by working with the balanced set of consumables that have been created to work together, a printer can reduce set up waste, can avoid time wasted through errors in colour management and in remaking plates, using processes plates to cut energy use, water use and improve environmental performance. Workflow and colour management tools can be part of this package. It can also include litho inks and digital inkjet inks. Inkjet printers using inks that don’t come from the head manufacturer may be inviting trouble.
The match between ink, printhead and substrate is crucial in inkjet printing. Heads and inks are engineered alongside each other and often third party inks simply will not work in another print head or worse can cause irreparable damage, or at the least will invalidate warranties, although that particular outcome has not yet been tested in the courts.
This is less the case in older solvent based inkjet technologies where third party supplies are able to create inks for specific purposes where the printer manufacturer will not. These are not always just cheap substitutes. Kodak has reached agreement with Collins which had ended up in court over its wish to supply inks to Kodak’s Versamark presses. This may even help Kodak as it will keep the Versamark machines in use while it can focus on building its Prosper user base.
As inkjet develops, inks develop along with it. The distinctions for continuous feed presses have been dye or pigment based inks. The former are less expensive, the latter produce better quality images because the pigment particles will sit on the surface of the paper rather than be carried into it. Both work better with papers that are coated by the mills for inkjet printing, or else have a priming coat applied at the point of printing.
Currently paper mills are working to create inkjet optimised papers as one option for their machines as volumes of standard woodfree coated papers decline. There will also be inkjet optimised corrugated materials because all the inkjet head and ink suppliers are keen on a share of a market where there is vast acreage of material waiting to be decorated with inkjet ink.
HP has a developed a version of its PageWide T 400 series machines for corrugated printing and has built a machine with KBA that is more than 100 inches wide for the same sector. It will use gallons of ink, hundreds of print heads and many tonnes a year of paper when global packaging groups adopt it. In the meantime inkjet ink are optimised for corrugated printing, lacking some of the components unnecessary under these conditions in order to keep the price down.
In the cutsheet toner market there can be little negotiation about the consumable. It is matched to the press and is part of the negotiated click charge. However, innovation exists with white toners appearing on OKI engines and now Ricoh’s Pro C7100 machines, clear toners from a number of suppliers, spot colours for the Fuji-Xerox iGen5, metallics from Fuji-Xerox and Kodak. Toners for security applications are also available, but the nature of the beast makes interchangeable toners impossible.
The ultimate interchangeable consumable is paper, though inkjet is perhaps changing that. Demand for standard woodfree coated papers is down across the market, hit as much by much better make ready on presses as overall falling demand for printed products. Mills are removing marginally profitable capacity or else converting machines to produce grades suited to packaging.
However, there is a growing requirement for uncoated papers which feel more natural and are less expensive than fully recycled papers. These are no longer the high absorbent, dull and flecked papers they once were, but can have the look, feel and behaviour of virgin fibre papers though not the price. Uncoated somehow give designers a natural feel that can achieve a standout effect in the reader’s hands. Fashion brands have led the way in adopting uncoated papers, and they have become a shorthand for brands that have a strong design or ethical ethos. They work well too in the burgeoning artisanal movement, for restaurants, mail order, business stationery, reports and so on.
Uncoated papers can be problematic for the litho printer. They can absorb ink, demanding changes to tonal curves to compensate. Most of all, however, they can take forever to dry, either filling a press hall with pallets of work in progress or making it difficult to promise a delivery time to the client.
The answer to the conundrum lies with the choice of consumables a printer makes. Many of the new generation UV presses have been installed to solve this problem because the UV cured sheet is instantly dry and can be worked immediately.
While this is the ideal solution, it is an expensive route. The combination of prepress, preset up, inks and other consumables can also improve the problem. In short, the consumables that a business chooses to use can have an impact beyond their price ticket. It is something more printers are thinking about.
Comment below to have your say on this story.
If you have a news story or tip-off, get in touch at editorial@sprinter.com.au.
Sign up to the Sprinter newsletter