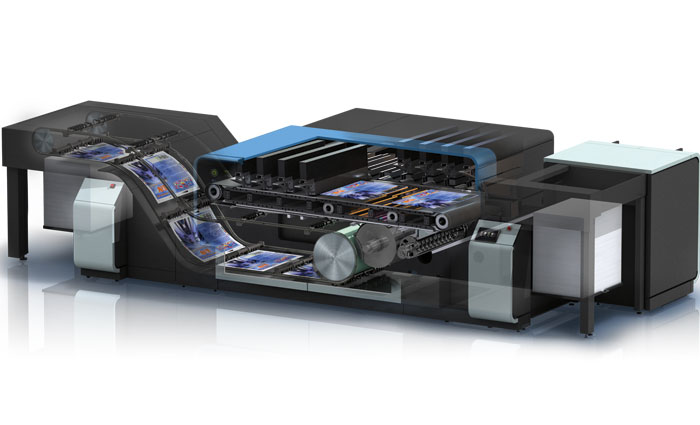
Dubbed as the printing industry’s Steve Jobs, or a modern-day Gutenberg, Benny Landa certainly knows how to create a buzz. His radical new digital printing method based on tiny particles became a huge talking point at Drupa, where he took the wraps off one of the industry’s best-kept secrets: a whole new kind of printing.
Anyone who visited the Landa stand in Hall 9 was able to look under the hood (at least to some extent) of the Nanography presses that were running on the booth. Astonishingly, Landa not only brought a new way of printing to Drupa, but the company also brought six brand-new presses along, too.
The caveat is that not all of the presses on display were running live at the exhibition, although two of them were. The B2 S7 press (up to 12,000sph, or 6,000sph perfecting) and the B1-format S10 (up to 13,000sph, 6,500sph perfecting) were seen printing five times per day after the sold-out Landa theatre presentations.
What is Nanography?
It all starts with Landa’s NanoInk, which is made using nano-scale pigment particles that are “just a few tens of nanometres” in size. Chairman and founder Benny Landa explains that, at this size, the pigments develop special properties, producing a very pure colour, so less pigment is needed.
This aqueous ink is shipped as a concentrate in 15kg containers, and then diluted to the correct working concentration inside the press using ordinary tap water; internal systems within the press handle any necessary water treatment.
“We are not shipping water all around the globe,” says Landa, emphasising the environmentally friendly approach being championed by the company.
As the ink is used up, the containers are constantly weighed, so the press operator knows how much is left of any given colour. The containers collapse down when empty and Landa says they can be disposed of along with everyday plastic beverage bottles.
All of the Landa presses print in eight colours, which could be CMYK plus four special colours, or CCMMYYKK for faster printing or higher resolution. The presses’ resolution is 600dpi or 1,200x600dpi.
Heated blanket belt
At present, Landa is using a modified version of the Kyocera piezo inkjet printheads for its ‘ink ejectors’, with the integration carried out by specialist company Graph-Tech of Switzerland. But Landa’s tech isn’t tied to one manufacturer or type of printhead though.
“Billions of dollars are being invested in inkjet technology development by many companies. We simply leverage that investment – all vendors are potential partners for us,” says Landa, who was also spotted during Drupa investigating the Konica Minolta heads being shown by the manufacturer’s external sales wing, Industrial Inkjet.
In the Nanography process, the ink ejectors create a complete CMYK print image by ejecting drops of NanoInk onto a heated blanket belt.
The image is dried on the belt, which is understood to be heated to around 120˚C, forming an ultra-thin polymeric film. This film, which could be likened to a decal, then meets the printing substrate at an impression cylinder, and is transferred to it via pressure.
Just before the image is transferred, an infrared booster lamp kicks in, providing the necessary temperature for the transfer to work properly. “It requires very little energy – the ink film has to be a certain temperature to transfer. We just bump it up to that before transfer,” Landa explains. “This is only a fraction of the heat that is used for drying conventional print; it is not like fusing.”
The blanket belt is an operator-replaceable component that is estimated to have a life of around 500,000 impressions, although it is expected to be greater than this by the time presses actually ship.
The sheets coming off the press feel barely warm, because it’s not the substrate itself that is heated, it’s the blanket. Printed output can immediately be used in finishing processes, claims Landa, due to NanoInk’s high level of scratch- and abrasion-resistance. The Landa press operators at Drupa were seen demonstrating this by rubbing a coin across freshly printed sheets.
One major selling point of Nanography is its ability to print onto standard printing papers, whether coated or uncoated, and also onto non-absorbent synthetics such as plastic films. The NanoInk layer’s thinness means it conforms to gloss levels of the stock.
The sheetfed Landa presses are based on sheet transfer and gripper technology from Komori, which was also the first traditional press manufacturer to sign up as a partner to license Nanography. Manroland Sheetfed and Heidelberg have followed suit with pledges to develop presses using the technology. More partners are expected to be announced in various segments and markets.
The imaging heads and blanket belt are positioned above the cylinder assembly.
The web press models differ in that they use high-speed web handling mechanisms developed in-house by Landa. The web presses – the single-sided W5 and W10 for flexible packaging, and duplex W50 for commercial printing – have some special features, because of the way Nanography makes use of the intermediate heated blanket belt.
The blanket belt has a seam that needs to be avoided when laying down the image. Dancer rollers are used on the web transport to compensate for this, and a section of the paper web is reversed in order to marry up the substrate with the next image position on the blanket. It’s similar to the way some label converting lines operate, albeit on the Landa devices this is happening at extremely high speed because the web presses run at 200m/min.
Landa describes it as “very good engineering” that uses servo devices to register the end of the previous image to the beginning of the next one.
Another aspect of the W50 also demonstrates Landa’s outside-the-box thinking compared with conventional press structures. The W50 uses the same one-metre-wide printing module as the B1 sheetfed press, but in this case half is used to print side one of the web, which is then turned and the other half of the print module is used to print the second side, hence its ability to print 200m/min duplex.
‘Wow’ factor
A major ‘wow’ factor is the radically different and futuristic look of each Landa press, which can be operated via a giant three-metre touchscreen running along the front of the machine. Landa’s stated aim is to make printing press operation as intuitive as operating an iPhone. “If they can use a cell phone they can run this machine,” he says.
The right-hand side of the display has all the job management features. Jobs are automatically organised into the optimum workflow, but the operator can override this in the case of an urgent job.
The left-hand side of the screen shows the machine functions, such as ink and paper handling. The operator can also choose to display a live camera feed on the touchscreen showing what’s going on inside the machine itself.
When a press is running unattended, it switches into ‘vital signs mode’ and the touchscreen displays giant numbers showing how many minutes and seconds will elapse before the press needs operator intervention, for example more paper or an ink change. This information is also shown on a portable tablet device that can be carried around the workplace. Landa believes a single operator could run as many as three, and possibly even four, presses.
Faith in the vision
Another ‘wow’ factor has been the number of printing companies willing to put hard cash down for the promise of a future product. Hundreds of companies bought into the Landa vision for Nanography and handed over €10,000 ($12,000) along with their letters of intent (LOIs) to buy machines of one variety or another. The B1 S10 press has proved by far the most popular choice, with one in every three orders placed for this model.
But what exactly are people paying for, apart from a promise? Landa says those who have placed deposits have been given a general timeframe, and a preliminary specification and price range for their chosen device. “Because the specification isn’t final, the price can’t be, either,” he says.
The price at the high end will be “in comparable terms to the equivalent offset presses”, yet Landa is expecting to deliver the lowest cost-per-page and cost of ownership when presses begin being used in earnest. The vision is to bring digital printing into the mainstream by making it affordable and viable for run lengths running into thousands.
One local company that was convinced by Landa – at least initially – was IBS Design Resources, based on the Gold Coast. The trade printer’s managing director, Scott Siganto, says he signed a letter of intent to purchase a B2 or B1 press, which would have cost in the region of $1.5 million to $2 million, but changed his mind before the deadline for the down payment.
“That money is better off in our cash flow for the next three years,” explains Siganto.
It’s noteworthy that future machines could be Landa’s own brand or co-branded with partners such as Komori, Manroland or Heidelberg. “We can deliver it ourselves or we can pass the LOI on to a partner,” says Landa, which opens up a more than nano-sized debate about whether Landa will ever ship its own product.
Some believe Landa will license its know-how and make money from the ink and consumables, leaving its partners to produce the actual printing machinery. And some pundits believe that, come Ipex 2014, the ‘Landa effect’ will be apparent in the number of machines sprouting touchscreen interfaces, even if they’re not of the three-metre-wide variety.
Challenges to come
While Landa clearly wowed audiences and convinced many with the promise of Nanography, products are not set to be commercially available until the end of next year, and there are still plenty of hurdles to overcome before anyone has a saleable Nanographic product.
With so much focus on Nanography’s eco-credentials, what about the recyclability of printed materials produced using the process, especially with concern in the paper recycling industry over the deinkability of inkjet and HP Indigo print?
We know that Nanography output cannot be deinked using the same flotation processes used for offset printed papers. Landa is currently working with a number of deinking consortia including the Digital Printing Deinking Alliance (DPDA) to evaluate the different deinking solutions available. “Unlike inkjet, our ink sits on the surface of the paper, which makes it a lot easier,” he explains. “I certainly expect our output to be deinkable – it’s just that the parameters are not exact yet.”
Obvious flaws
At Drupa, Landa and his team were upfront about the fact that Nanographic prints currently show very obvious flaws. The samples shown were all striking and colourful full-page images of animals, such as tigers and peacocks. The image subject matter was quite ‘noisy’ in itself and there were no print samples showing flat tints or text.
The print samples featured very obvious banding lines and white spots in the image area where ink was entirely missing (see the images to the above left, which show close-up detail of the samples). Some visitors expressed surprise at just how poor the print quality was – despite the attempts to manage expectations, although others praised the image intensity and brightness of the colours despite the flaws.
Landa says the current faults are to do with the ejecting process, and are not fundamental issues involving the transfer of the print image from the blanket. “The process is not fully optimised yet. We have flaws and we are very open about it. This all takes testing and it’s not perfect yet.”
Solving these quality issues, and ensuring the machinery itself will be suitably robust in operation, will be occupying the Landa team over the coming months. But they are confident that they will achieve commercialisation in the timescale envisaged, and that the so-called ‘second digital revolution’ will begin in earnest next year.
REACTION FROM SUPPLIERS
“We have a long history with Benny and I always like to see people innovating and driving the industry forward. I wish Benny well. Clearly, if you’re an offset company you’re looking for options and looking to find alternatives, and the early announcements in that space endorse that. We’re always looking on our next thing as well. We just don’t share as far out.”
Chris Morgan, senior vice-president, HP
“Benny has solved two of the fundamental problems of digital print, but he has created two more. Let’s see. It will take at least two years to solve.”
Conventional press manufacturer
“I sense he may never intend to sell a Landa product, but rather license the technology for use by others.”
Dieter Schilling, chief executive, Delphax
“Given customers’ interest in high-volume print, prior to making a decision for or against Nanographic technology, we feel it is necessary to take time analysing and assessing the pros and cons. It is good that Benny Landa has applied his creative skills and invested money in driving advances for the benefit of print. This illustrates the appeal of print products and their future potential for those with the intelligence to see it.”
Klaus Schmidt, marketing director, KBA
“The current print quality status is so poor – I think it will take more than 18 months to fix. However, you can’t underestimate the future potential. The Landa Nanography process looks superior from a technical point of view, yet many items remain to be proven.”
Digital press manufacturer
“Seeing Landa at Drupa and the promise of his commercialised products in coming years is encouraging. We think it’s too early to comment on Nanography until we’ve had a closer look, but the story presented by Landa reinforces Memjet’s proven model and belief in focusing on what you do better than anyone else, and then partnering with great OEMs for adoption and integration.”
Jeff Bean, VP of brand & communications, Memjet
“Anyone who comes with innovations to this industry should be welcome. And if it’s Benny – well, welcome, Benny.”
Antonio Perez Chairman and chief executive, Kodak
“It looks very interesting, which is why Manroland Sheetfed has entered into a strategic partnership with Landa. What it means in terms of products and time to market, I think it’s too early to say. Given Landa’s track record, one would be a fool to ignore what he’s doing.”
Steve Dunwell, managing director, Manroland Australasia
“Can Benny ‘do another Indigo’? Can he achieve inkjet speeds currently beyond everyone else? And can he do it all with commercial quality and a price point closer to conventional offset than the current digital technologies? If the technology can tick those boxes, we are looking at a true game changer.”
Garry Muratore, general manager, GMG Australia
REACTION FROM PRINTERS
“It’s obvious that inkjet is the future for many areas of print. If Landa can achieve the quality on standard stocks it will be a game changer, particularly with the support of traditional press manufacturers.”
Barry Davis, managing director, Hyde Park Press
“After being in the photographic industry for over 35 years and only getting involved in the printing industry four years ago, going directly to digital, I have seen many changes. What I saw at Drupa with Landa’s Nanography I believe will change the way we print until print totally disappears in the future.”
Michael Warshall, executive director, Picpress
“It was definitely the entertainment highlight of the show. I hope the substance will be as good as the sizzle. Great to see a real lateral thinker working outside the bounds of current knowledge. I feel it will not be the ‘end of traditional printing’ – whatever that is – but rather will add a new component to the printing matrix.”
Gordon Lang, managing director, Documaster
“The sad thing is the way the industry is imploding: the Landa technology won’t arrive for at least 12 months and who will want to go and buy this very, very expensive technology that hasn’t been proven in a depressed market where there is excess capacity?”
Melbourne digital printer
Comment below to have your say on this story.
If you have a news story or tip-off, get in touch at editorial@sprinter.com.au.
Sign up to the Sprinter newsletter