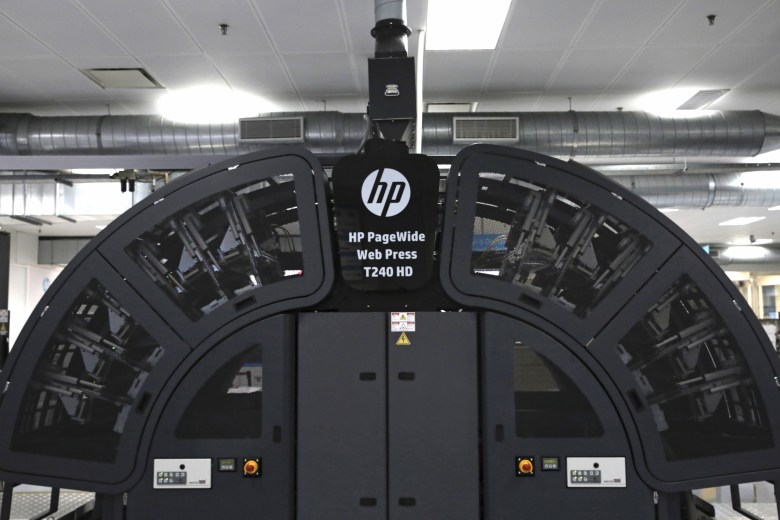
In this industry, even a few years ago, we used to make the quality argument when comparing high-speed production inkjet printing to its lithographic counterpart. Yes, inkjet was fast, but offset still laid claim to the premium end of the spectrum, where quality was the benchmark. But is that still even a little true?
It appears the maturing of high-speed inkjet production printing – increasingly now in B2 and B1 formats – has virtually pushed it to equity with offset printing.
As one vendor expressed it to ProPrint, its inkjet models have “broken the digital/offset barrier”.
As we detail further along in this report, independent testing which integrated inkjet-printed pages into an offset-printed publication came up with a seamless match of stock appearance and colour. Now, of course, some analogue vendors might have different views, but dare we ask: is it time to put down the glasses and declare a draw?
Many suppliers of sheetfed and webfed inkjet machines available today on the Australian market would answer that with a resounding ‘Yes’. And that’s even before you subtract the time-sapping elements of platemaking and press makeready from the offset side of the equation and add in personalisation and VDP on the inkjet side.
Sheetfed inkjet
Colin McKenzie, national manager, digital web press technology, at Océ Australia, describes the Océ VarioPrint i300 (VPi300) as “a unique technology, with a genetic makeup of generations of developments”.
“The VPi300 produces offset quality on offset stocks,” he notes, explaining that this is one of the major hallmarks of its success.
“This press has proven its pedigree in the field with an average uptime of more than 94 per cent, unheard of for a digital press. It is here that the VPi300 separates itself from the digital pack, and closes the gap on offset production,” McKenzie said.
“The Australian installations have been placed into commercial printers and direct mail houses where offset replacement has been the key driver.
“The next installations are planned and will be implemented into commercial printers also to replace sheet fed offset presses.”
Océ’s VPi300 (and its ProStream 1000 – see webfed section) are “the new offset in every way,” reflects McKenzie.
“The Australian commercial print market does not have the advantage of larger markets to focus on one or just a few applications. In the past, an offset press investment was based on the broadest criteria to deliver a diverse mix of jobs. So it is for a digital press. The new digital press must be versatile, reliable, meet all quality expectations, and above all deliver on the ROI”.
“Creating the value chain around fueling the emotions of print from targeted communication pieces to individualised communication will generally create the additional business opportunities and therefore greater ROI for brand owners and producers alike. In a more pragmatic way, the print service provider would benefit from an Océ digital inkjet press that provides reliability, lower production costs, more flexible application opportunities, and removes many of the costly touch points from their traditional and digital print businesses.”
Currie Group sales and marketing director Phillip Rennell sees the HP Indigo HD Imaging System, a new high-definition writing head solution, as a significant advancement in the evolving HP Indigo story. Available on the HP Indigo 12000 Digital Press, the new system doubles print resolution and decreases ink dot size by 30 per cent compared to non-HD presses, for maximum smoothness on photo and high-end commercial applications. It enables the Indigo to surpass offset quality at 1600dpi with high LPI screen sets up to 290lpi, for art gallery quality prints with high detail reproduction.
“Using the default fifth ink station to take advantage of special inks and spot colours is another asset. The Indigo can emulate Pantone colours on-press using CMYK or HP IndiChrome’s six- or seven-colour process. True spot colours can be ordered from the HP IndiChrome Ink Mixing Service,” says Rennell.
“HP Indigo offers a suite of integrated solutions that simplify and automate colour management and enable you to save time and costs with fewer colour adjustments and reprints. It ensures colour consistency over time, across presses, sites, and between offset and HP Indigo technology,” he adds.
Describing it as an easy fit for offset printers, Rennell says the HP Indigo 12000 HD Digital Press offers a solution for the digital printing of any commercial application on virtually any substrate. The full sheet can be used to print any high-impact commercial application, from attention-grabbing posters, to folders, oversized books, photo applications, specialty products using high-value substrates or inks, and much more”.
Konica Minolta’s recent improvement to the AccurioJet KM-1 inkjet press continues the success of the B2+ platform with a recent installation at Imagination Graphics in Sydney in October, reports Tatjana Ferguson, product manager, Industrial Print, at Konica Minolta in Australia. The AccurioJet KM-1 can print up to 3,000 single-sided B2 sheets per hour at up to 1,200dpi, she states. “Major benefits of the system include moving short-run offset to digital inkjet, the ability to carry out hybrid printing with the integration of the AccurioJet KM-1 into existing offset processes, duplex printing, and larger sheet sizes, as well as printing on packaging board, lightweight papers and textured stock.”
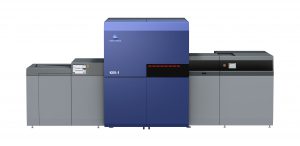
Ferguson notes that Konica Minolta’s high-resolution inkjet heads are the heart of the KM-1 press. “The inkjet heads are now moving into their third iteration, and customers are enjoying even higher quality across flat tones and solids. They are longer-life and quicker to replace – and deliver crisp, fine type. All of this equates to higher focus on uptime and productivity, as well as image quality. In addition, the introduction of ink reduction software algorithms has resulted in a 20 per cent decrease in ink consumption on average.”
And she adds that with a ‘no click-charge’ model, the consumption of ink is a major factor in ensuring the consumption model of the KM-1 remains competitive. These options put the KM-1 at a greater advantage in terms of manufacturing cost over other B2 sheet fed solutions.
Meanwhile, Revolution Print, an AccurioJet KM-1 installation in Ballarat, Victoria, is trialling Konica Minolta’s wearable AIRe Lens smart glasses, which use Holographic Optical Element (HDE) technology to enable Konica Minolta technical engineers to remotely instruct the operator to change parts and ensure quicker repairs, providing Revolution Print greater control over service intervals.
Heidelberg’s Primefire 106 takes the mantle of first digital press in B1 format for the packaging market, combining the gold standard for reliability as an offset platform – the Heidelberg XL106 – with a direct print process that ensures repeatable quality results. All of this can be plugged and played within an existing workflow by using Heidelberg’s Prinect solutions.
Richard Timson, Heidelberg A/NZ managing director, notes that Heidelberg partners with Fujifilm in CMYKOVG, a process that enables upwards of 12 billion drops per sheet in seven process colours, providing around 95 per cent Pantone colour gamut coverage with Heidelberg Multicolor technology. And, Heidelberg’s Saphira water-based consumables conform to Swiss Ordinance, offering the best available conditions for low-migration products.
Primefire 106 has been impressing printers and customers in the folding-carton sector, offering versioned and personalised print, and short runs and higher supply chain efficiency. Cost effective production of high volumes is a must in this market segment and combining Primefire 106 with traditional offset production provides a powerful combination, offering flexibility and quality on proven platforms.
Troy Neighbour, senior product manager, Graphic Systems, at Fujifilm Australia, sees its Jet Press 720S as an optimal B2 inkjet solution. It can print a 74cm sheet in a single pass, at speeds of up to 2,700 sheets per hour, generating output that’s dry to the touch, which makes inkjet even more cost effective as an alternative to litho.
The Jet Press offers printing with standard coated/uncoated stock instead of specialised digital paper – and after imaging, standard stocks can be treated like offset stocks and finished using conventional bindery equipment.
Fujifilm says the half-size solution enables print runs down to one, or into the thousands, where conventional litho and digital printing are not delivering, and offers a better prospect for the fastest-growing segment of the commercial market. As Neighbour explains, the most efficient way to produce short-run print is to send the PDF to the press and print.
“This is how the Jet Press 720S operates; a groundbreaking B2 inkjet press that eliminates all the time-consuming and costly preparation and set-up parameters of an offset press.”
Webfed inkjet
Screen’s digital inkjet press strategy is based on a firm foundation of over 1,500 installations since it released the first Truepress Jet 520 continuous-feed model in 2006. Over 100 of these are the latest 520HD (high definition) model, released only two years ago and featuring the industry’s smallest ink droplet size of two picolitres. The HD model was further advanced last year with the introduction of Screen’s Truepress SC ink, with expanded colour gamut, fast drying and greater stability. Most importantly, they can print on standard offset stocks without the need for any pre-coating or primer.
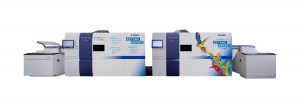
“The Truepress Jet 520HD with SC inks has broken the digital/offset barrier when it comes to high speed inkjet production,” says Peter Scott, managing director of Screen GP Australia. “Earlier this year, an independent test by Technology Watch in the USA matched output from the 520HD+SC inks with offset printed on a Heidelberg XL-105. Thousands of the digitally printed pages were incorporated into the offset-printed publication and it was a perfect match in stock, appearance and colour.”
Scott adds that 520HD+SC ink users all over the world are singing the praises of the quality, enabling customers to offer the quality and paper stocks of offset but with the digital advantages of variable data, personalisation, no makeready and plates, and short runs without a price penalty.
Screen’s business proposition is rare among digital vendors in that they do not charge a ‘click’ or linearage rate, says Scott. “We take the view that, if you build the machine right, have excellent factory-trained technicians and offer service agreements, we do not need to take a portion of the printer’s profit with a click-charge. It means digital can be used in the same way as offset presses.”
The Truepress 520 series covers all potential applications including monochromatic book production, transactional documents, direct mail marketing and now commercial printing on a par with offset.
For transactional form printing, the company recently introduced the Truepress Jet 520NX which is a full-colour press but the CMY printheads can be ‘parked’ when printing mono. This model can also print MICR ink for magnetic recognition, UV security and IR absorbing inks. It is rated at 150 linear m/min but in black enhanced mode can operate at 180 linear m/min.
At the top of the speed stakes is the Truepress Jet 520ZZ, which can run at up to 220 linear m/min. It has proved popular with higher-volume customers such as Bertelsmann Print Group in Germany and Leaderform in Italy, who now have two ZZ models.
“We have a solution to fit all levels of productivity, all quality requirements from transactional up to offset, and all market sectors. Personally, I am excited about the 520HD with SC inks for our market as it offers offset quality on offset stocks, at speeds suited to Australia-New Zealand market demands,” says Scott.
Océ Australia’s Colin McKenzie sees its ProStream 1000 as, “the next generation imaging technology utilising the ever reliable piezo drop-on-demand 1200dpi print heads. With the Océ multi-level dot modulation (variable droplets likened to offset stochastic screening), FOGRA 51 print quality standard is achieved, in combination with Océ’s latest polymer pigment ink set.
“What the commercial printer can look forward to is the consistent print quality related to customer branding on offset coated stocks, reliability and minimal operator intervention. Like all digital webfed presses, the inline finishing options are available in abundance.
“The first installation for Australia of the ProStream 1000 has been completed with further information to follow.”
Paul Haggett, Kodak ANZ’s sales & marketing director, enterprise inkjet systems, is looking ahead to Ulstrastream, Kodak’s fourth-generation continuous inkjet (CIJ) technology for high-speed digital printing, which he says is leveraged from the success of Kodak Stream and Versamark inkjet technologies. “Kodak Ultrastream elevates digital inkjet to another level, offering improved image quality to match offset or other analogue technologies, expanded substrate ranges, and the lowest cost per image at production speed,” Haggett said.
Haggett explains that Ultrastream is a complete writing system that raises the bar for production inkjet. This fourth-generation continuous inkjet technology uses smaller drop sizes and precise placement accuracy to print high-definition quality at high-speed productivity, regardless of ink coverage.
“With a resolution of 600x1800dpi delivered at speeds up to 150m/min, Ultrastream combines offset-like quality and productivity with compelling economics, expanding opportunities for inkjet to new markets. Ultrastream’s writing system includes a modular, scalable printhead that can be configured in varying widths from 10 to 250cm. It’s also available in a scanning head configuration to enable wide-format printing, with multiple heads on a moving carriage. With flexible print width, a static or traversing printhead, offset-like print quality, and the ability to integrate variable data at high speeds on a wide range of substrates, Ultrastream opens up a world of opportunity for production inkjet technology.”
Meanwhile, Kodak’s Prosper range, already kicking goals in the Australian market, prints industrial-strength ink laydown on a diverse array of papers, especially glossy, and at high speed, says Haggett. The line-up comprises four devices – the Prosper 6000S standalone press, for one-sided printing, the 6000S hybrid (one-sided), and the 6000P and 6000C perfecting presses. With Kodak Stream inkjet technology, the drop generation technology inside Prosper 6000 presses creates drops in excess of 400KHz, which means each Prosper printhead produces 480,000 drops per second, significantly ahead of drop-on-demand inkjet.
HP PageWide Web Press customers have now printed over 320 billion pages worldwide, and currently print over six billion pages per month on the range of PageWide Web Presses that have seen continuous innovation since 2011, notes Michael Gillis, country manager, HP Indigo and PageWide Industrial, HP South Pacific.
Gillis explains that High Definition Nozzle Architecture (HDNA) is HP’s latest inkjet printhead technology. “By delivering 2,400 nozzles per inch and providing support for dual drop weight per colour, these new printheads represent a breakthrough in the print quality and performance of HP PageWide web presses.”
This high quality opens up new publishing, direct mail and general commercial printing application opportunities, such as colour trade publications, posters and banners up to 2.74m long, as well as high-end retail brochures and catalogues, he says. “As the market shows trends toward shorter run lengths, faster job changeover and tighter deadlines, and the demand for data-driven personalisation increases, print service providers require presses that offer mass- customisation at a competitive cost, and on a variety of media options.”
HP PageWide Web Presses are already producing a broad range of applications globally – books, newspapers, catalogues, direct mail, transactional, posters and much more – at offset-class quality and speed, but with digital versatility and variable data. And it all comes with a full suite of software solutions and finishing partners to automate workflow and optimise production capability.
As run lengths shrink, EFI has responded to the new reality with a cost-effective solution to customer requirements, constantly diminishing response times, versioning/VDP, just-in-time and on-demand printing – all of it designed to cut inventory costs and waste. Its Nozomi C18000 offers high-quality, high-speed digital LED printing at up to 75 linear m/min (with one- and two-lane printing) on stocks up to 1.8m wide.
Designed with continuous operational, environmental, and competitive improvements in mind for innovative print providers, the Nozomi delivers resolutions up to 360x720dpi, and single-pass, LED, digital drop-on-demand piezo inkjet technology with four-level greyscale imaging. Combined with this is a variety of configurations, including CMYK, CMYK+W, CMYKOV and CMYKOV+W, and an inline primer that allows dot gain and ink absorption control over a range of corrugated top sheets. EFI offers a totally integrated platform with top- and bottom-feed options for digital corrugated packaging.
The trend towards ship/shelf-ready packaging favoured by popular Big Box retailers is where multiple products remain inside the outer corrugated carton from warehouse to shelf, notes EFI. That provides an opportunity to upscale the printing of higher quality, full colour graphics rather than just standard single-colour blocks with heavy text and barcodes on the outer box. EFI also identifies strong growth in online shopping and in corrugated packaging used by internet retailers such as Amazon to protect goods en-route from automated warehouses to residential addresses.
Xeikon, now part of the Flint Group, has had its Panther PX3000 label press in the Australian market for just over two years. The press is based on Xeikon’s Panther UV inkjet technology complementing the Xeikon 3000 series and Xeikon CX3 label presses, based on dry toner technology. Its features a web width of 330mm and a maximum speed of 50m/min. Colour configuration is CMYK plus white, with a print quality of 600x600dpi. Substrates include paper, PVC, PP, PET and PE.
Comment below to have your say on this story.
If you have a news story or tip-off, get in touch at editorial@sprinter.com.au.
Sign up to the Sprinter newsletter