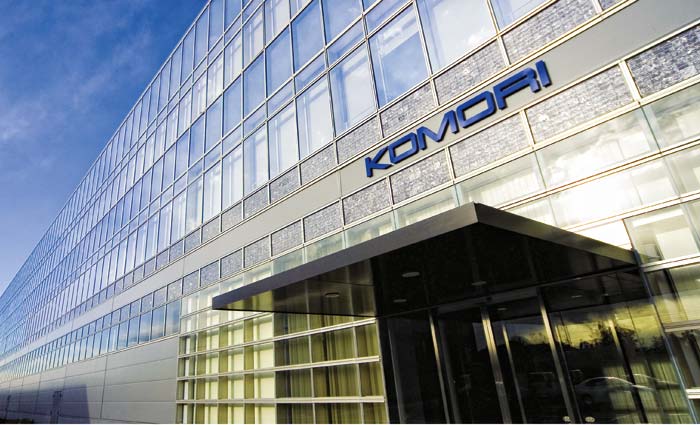
Komori wants customers to know its kit its cutting-edge. This message resonated with the seven Australian and New Zealand printers who the press maker flew to its headquarters in Japan last year. All had joined the trip with serious plans to install presses within the following 24 months. Local distributor Ferrostaal, which also joined the December tour, was keen to highlight the benefits that Komori’s H-UV technology could bring to their businesses.
The party featured a trio of Victorians: Newlitho chief executive Seth Watts, Whirlwind Print chief executive Andrew Cester and Ego Print sales and marketing manager Graeme Lidgerwood. Also present were Van Dyke Press general manager Will Tompson from Sydney, Platypus Graphics owner Tom Lusch from Brisbane, Scott Print manager Tim Scott from Perth and Image Centre Group managing director David Atkins from Auckland. ProPrint went along as a guest of Ferrostaal and Komori.
It was difficult not to be seduced by Komori’s high-tech message during the half-day tour of its factory in Tsukuba, just outside Tokyo.
Machines are produced on a 160 metre-long assembly line, which moves at seven centimetres per minute, and which is said to be the only one in the world to handle both sheetfed and web offset. The line can produce 13 presses per day, 76% of which are exported. As of October, it had handled 220 H-UV orders: 155 for Japan, 30 for Europe, 20 for the US and 15 for the rest of the world. The manufacturing floor is strikingly clean, but you’ll have to take our word for that. Photographs of the ultra-modern site are forbidden.
The 63,000sqm site was completed in 2009 and employs 700 staff. It includes a printing college, technical training centre, demonstration hall and R&D section.
The tour also included a visit to Kodama Printing. Its place on the itinerary was either a remarkable coincidence or an astute piece of marketing from Komori and Ferrostaal. The firm had been using Heidelberg for 20 years, but made the switch to Komori in 2012 with the purchase of three H-UV presses.
As anyone who has ridden Tokyo’s packed subway knows, the city is a crowded place. High population density equals high land values, which poses challenges for print shops. That message hit home during our visit to Kodama. The factory employed 60 people over five storeys. Space was at such a premium that work had to be stacked outside.
Van Dyke’s Tompson was an especially interested visitor. As a food packaging specialist, Van Dyke has to meet strict regulations concerning the cleanliness and appearance of its factory. Tompson said he paid close attention to how Kodama handled and stored materials in such
a confined space.
Watts from Newlitho was another keen observer. “We wanted to look at best practice internationally. We were extremely interested in what the Japanese printers were doing in terms of printing and material handling. Due to their space constraints, we were fascinated to find out how they were laying out, running and automating their factories.”
Watts had only positive things to say after taking his first close look at H-UV. “The Komori technology was something we hadn’t had a huge amount of exposure to and we wanted to understand what it was all about. It was fantastic. For us, presses are about reliability and quality, and I was extremely impressed by the quality systems, attention to detail and excellence in manufacturing.”
Lusch said the technology had given Platypus something to think about ahead of its next investment. “It sounds good.
I’ve been looking at it for a while in various forms, as in LED and H-UV. I know KBA have their own version. It’s an energy-saving technology,” he said.
Scott said Komori was very much on the 60-staff Perth company’s radar as it weighed up its next major purchase.
“It’s interesting. It’s a different style of printing in terms of set-up. It’s good there’s an alternative out there.”
Atkins from Image Centre Group also gave the thumbs-up to the speed and quality of the H-UV presses. Ego Print’s Lidgerwood went further. He said it had “opened my eyes to the future of UV printing”. He even expressed concern that traditional UV printers like Ego could be threatened by H-UV, because it seemed to offer potential rivals an easier entry point than traditional UV.
Tompson said Van Dyke had been using UV for 20 years, and so he wasn’t blown away by the concept of H-UV. However, he liked the fact it used less power than traditional UV. He was also impressed by the inline scanning, the quick makeready and the potential it offered to turn around jobs more quickly.
Cester from Whirlwind was the only tourist to visit more than one manufacturer, having arrived in Japan a few days ahead of the party to also call on Ryobi.
“The trip was about comparing Japanese UV technologies and determining what were the easiest to use and the most economical to use,” he said.
Cester spoke warmly about Komori’s H-UV offering. “I think it looked very easy to use and environmentally friendly. It makes printing easier than conventional printing, in particular in perfecting, and reduces makeready waste by about 50-70%.”
It was probably no coincidence that Cester called on two manufacturers: he said any purchase from Whirlwind would likely come as early as the first quarter of 2013. Image Centre said a decision was about six months away. Newlitho, Van Dyke, Platypus, Ego and Scott Print said they were still 12-24 months away from making up their minds. Judging from their reactions, Komori has made a positive impression on all the printers who visited Japan.
The unanimous chorus of approval would have pleased the three Ferrostaal hosts: chief executive Markus Haefeli, general manager of print and finishing Rayne Simpson and sales manager Iain Sim. However, they would know only too well how much effort it takes to lock in a sale. Shifting multimillion-dollar presses is difficult even in a buoyant market.
Scott from Scott Print could have spoken for the entire group when he said: “You have to go to market and see who has the best available product to suit the work your business does.”
ProPrint was a guest of Komori and Ferrostaal.
Comment below to have your say on this story.
If you have a news story or tip-off, get in touch at editorial@sprinter.com.au.
Sign up to the Sprinter newsletter