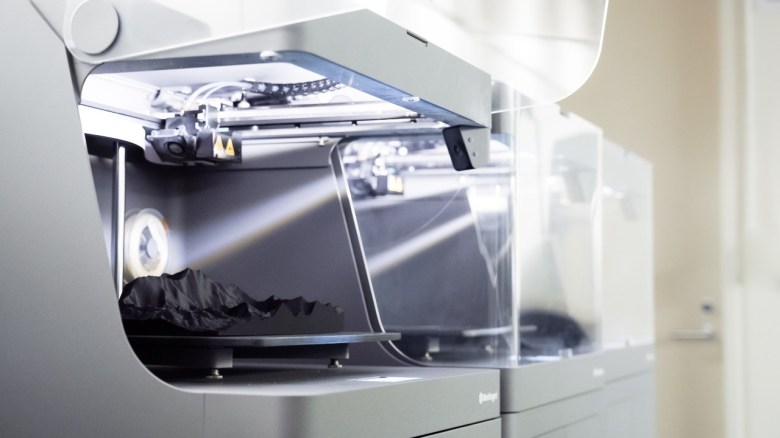
This article was part of a broader 3D Print Technology Focus published in the June 2020 issue of ProPrint. To read the full story, click here.
3D printing is no longer new or experimental.
It has permeated all corners of the community, including our classrooms. But what does it mean for Australia’s commercial print houses? For starters, nailing a corner of the modelling or prototyping market is a coup on competitors struggling with diminishing opportunities. 3D winners will be companies already established in the visual display space, perhaps with strong connections on the exhibition circuit.
Matt Hunter, Konica Minolta Australia’s innovation product manager, says his company has access to a cross-section of all technologies, from small to large.
“As we are partnered with both 3D Systems and Markforged, we cover the entire scope of the market with materials and technologies. Our portfolio includes UV light-cured resin, laser sintered plastic and metal powders, as well as extruded nylons and continuous fibre printing options,” Hunter said.
“We also offer some great industrial software solutions for the 3D scanning and medical markets. There is almost nothing that cannot be made using any of our available technologies.”
He sees strong potential for Australian 3D printing in low-volume and custom parts for automotive production and automation component replacement for equipment where obtaining spares may be tough or prolonged.
There is also growing demand for custom components that need to fit specific geometry – especially in medicine – such as spinal and cranial implants. Parts manufacture in remote locations, like defence and naval, are another opportunity.
3D printing opportunities can also be found “essentially in any engineering need – where what a user needs is not too big and does not need to be mass-manufactured in huge quantities,” Hunter said.
“Geometrically challenging components with complex internal features are also ideal, as they are usually impossible to make with traditional subtractive manufacturing methods,” he said.
“3D printing is very much a materials game, so we’ll be seeing a lot more stronger and cheaper materials competing in both the cheaper and more industrial machine space. Tougher nylons and fibre-backed technologies will start competing in the hobbyist space, for example. We will also see expansion of larger part technologies in the manufacturing of larger scale objects, including machines using secondary machining processes like CNC for finishing.
“And, of course, the medical space will see a rise in bioprinting of organs and bones, although these components will be a slow burner due to regulatory processes.”
Comment below to have your say on this story.
If you have a news story or tip-off, get in touch at editorial@sprinter.com.au.
Sign up to the Sprinter newsletter