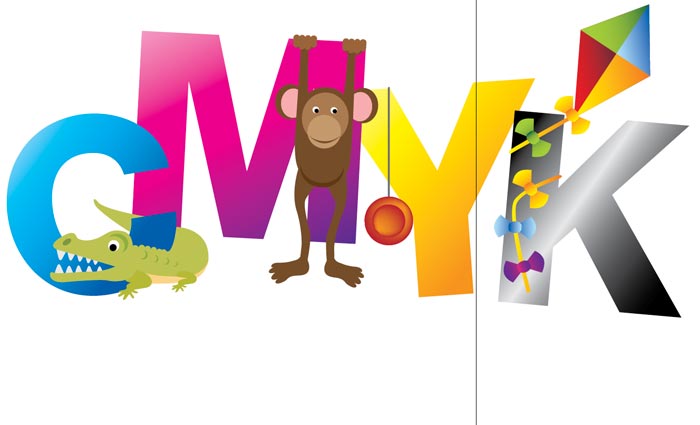
Managing colour is one of the most complex and challenging aspects of producing a quality sheetfed press run, whether traditional litho or digital. Or at least, it used to be. But software, hardware, systems and standards are making it easier than ever to ensure colour is consistent and accurate wherever it goes.
Colour boffins have spent years doing the heavy lifting on colour standards. This is where it gets technical. The Australian AS/ISO 12647-2, which has the support of the Printing Industries Association of Australia (PIAA) and the Lithographic Institute of Australia (LIA), draws directly on the international ISO 12647-2 for halftone colour separations, proof and production prints. Work is now underway on a separate digital colour standard, ISO 15311-2. There’s also Fogra’s Process Standard Offset (PSO) template and certification processes such as the Fogra-based Australian Print Processing Standard (PPS), and alternatives such as the Ugra process.
The beauty of all this is that for the typical print business owner or manager, the complex issue can be more or less fully automated. The pressroom itself is becoming a hive of colour management activity. Onboard technology can integrate the process with the printing and take the headache out of colour management. Since Drupa 2012, some of the new crop of colour management-enabled presses has begun filtering into Australia.
‘Off-board’ colour control
Inline colour management built into the press may be the Holy Grail, but it comes at a significant price. In the current cautious climate, there’s a strong body of opinion that pre-press-driven colour management more than fits the bill. At Print Bound, a 50-staff offset and digital printer with a staff of some 50 in Melbourne’s Oakleigh South, managing director Mauro Mattarucco is confident of the company’s nearline spectrophotometry. A Heidelberg Prinect Image Control system scans the sheets and feeds the colour profiles to the ink keys on Print Bound’s 12-colour Speedmaster perfector and six-colour Speedmaster straight press. Colour data comes through the profiles via the repro phase. The job number is called up and the colour profiles will already be included. “We then do a makeready, adjust the colour, and hold the profiles from the makeready stage throughout the run,” Mattarucco says.
Prinect’s Image Control can be used for up to four presses at once. The next step for Print Bound would be on-press colour management, but Mattarucco believes this decision is best left until the time comes for a general upgrade of the presses.
Colour management might bring to mind offset litho, but digital has come on leaps and bounds. Port Melbourne digital business On Demand claimed a world first a few years back as the first digital printer to get certified to the ISO 12647 standard for its fleet of digital presses, which include HP Indigos, as well as equipment from Fuji Xerox and Canon-Océ. Managing director Bruce Peddlesden is sceptical of integrated colour management, at least for digital.
He sees no need to have individual presses fitted with separate RIPs and colour management. In his view, having already invested in pre-press colour management, it makes no sense to double up and spec individual devices for colour calibration. Moreover, he says driving colour from the device means the cost factor multiplies every time a new press is added. “Our colour accuracy is magnificent, so I haven’t been worrying about alternative approaches.”
All onboard for colour
Steve Dunwell, managing director of Manroland Australia, says integrated colour management is available on the latest Roland 700 and 900 series presses in configurations of four-, six- and eight-colour. Installed over the impression cylinder of the last printing unit, it auto-matically pulls in the colour for the job to set densities programmed by the operator before the start of production. This process is evenly spread between both sizes, not just large-format presses.
“The operation is relatively simple following initial training by the instructor when the press is being commissioned, so long as you have printers with a good knowledge of colour control by densities and densitometry. It is considered by some customers to be green, given the time and material savings,” says Dunwell.
“It’s still something new for sheetfed customers; our webfed customers have had this technology for some time now. It’s perfect for web but still has some restriction when it comes to some sheetfed customers when spectro and metallic colours are high on their agenda.”
On-press measurement
Shane Hanlon, head of product management at Heidelberg Australia & New Zealand, says the vendor offers a full range of colour management systems across its complete press range from the A3-format Speedmaster SX 52 to the very large-format XL 145 and 162 presses.
He cites Prinect Inpress Control, a measuring device located in the last printing unit of the press, and before the perfecting unit in long perfectors. At its core, Inpress Control is a spectrophoto-metric device that corrects colour on the fly, measuring process and spot colours, as well as register in the quality control strip.
It measures a colour strip located at the front edge or centre of the sheet, and automatically measures and adjusts the colour and register on-the-fly without the need to stop the press during makeready to check colour and register. He says there is no great training curve and ROI is typically well under 12 months. “This system has very quickly become the colour control system of choice across all the models it is available on.”
Melbourne’s Southern Colour Victoria runs a 10-colour Heidelberg Speedmaster XL 105 with Prinect Inpress Control built in. When the company’s new six-colour XL 106 with coater and a 10-colour XL 106 are added later this year, they will also be fitted with it.
Allan Gardiner, a director of Southern Colour and in charge of pre-press, tells ProPrint the advantage of onboard colour management is the ability to scan sheets on the fly at full speed.
“With a nearline device, the operator, if he is working very quickly, will at best get a scan every 700-1,000 sheets, whereas with an Inpress system, my understanding is that it’s completing a measurement cycle every 16 sheets, and that’s at 15,000 sheets an hour. You’re getting more constant feedback and tighter control.”
Additionally, Inpress integrates with the Prinect Press Centre, which automatically selects colour reference values from a database, based on substrate type and ink series, rather than leaving it to the operator, who simply has to check the specs against the job ticket, says Gardiner. “The press operator has all that visual, graphical feedback in real time, as well as the numerical feedback instantly through his console.”
Reporting occurs every 200 sheets, providing information such as dot gain and solid primary colour values. Accurate pre-setting information is vital to ensure Inpress Control works at top efficiency.
“When the operator sees a section he’s printing is coated paper type 1 with a particular ink series, he can then look at the plate calibration ID mark and have confidence that what’s on the plate is in harmony with what’s being presented to him as far as those attributes go,” Gardiner adds.
KBA offers its Qualitronic ColorControl camera-based inline colour control system as an option on its Rapida 105, Rapida 106 and all its large-format presses. KBA Australasia’s sheetfed manager, Dave Lewis, says many of its medium-format customers are now buying presses with this option.
“On a straight press, we have one camera and on a perfecting press we have two cameras. These are high-speed cameras that can measure densities up to 20,000 sheets per hour and read every sheet and adjust every few sheets.”
Lewis says Qualitronic is easy for an operator, who simply does an initial colour scan on the press console and then tells the system to keep the densities to the sign-off sheet. And prices for onboard colour management have come down in recent times. “At least 75% of the quotes we do include this option.”
It helps that the technology is becoming more realistic for smaller printers. Lewis says that the price of the Qualitronic ColourControl system has come down by about 35% in the past three to four years.
“This, as well as customers looking for greater productivity and efficiency, has led to much more interest and uptake of this feature. I am sure in the future that this will become standard technology for most press purchasers.”
The Cyber Group has made significant inroads into New Zealand with its Ryobi agency, much of it spurred on by the inline densitometry featured in the presses. David Taylor, general manager of Cyber NZ, says all Ryobis sold in New Zealand over the past four to five years have been fitted with the integrated colour circuitry.
New Zealand print companies benefitting from Ryobi’s closed-loop colour include Crucial Colour, Wickliffe Solutions and PDQ Print in Auckland, Otago Daily Times Print in Alexandra, and Rainbow Print and Federal Print in Christchurch.
Digital does it too
Just as prices have fallen for inline colour management in offset presses, technology is now even becoming available on lower-end digital equipment. One of the selling points of the new Fuji Xerox Color J75 Press is that it offers automated colour calibration, reducing set-up time. Considering the on-demand, fast-turnaround and last-minute nature of many digital jobs, this can only be a good thing.
The J75 now offers press adjustments that previously required an engineer. Onboard the Color J75 is a package that Fuji Xerox calls Automated Colour Quality Suite. This automates the process of colour calibration, not only cutting set-up time but ensuring that prints are the same from job-to-job, first page to last.
Fuji Xerox says Automated Colour Quality Suite reduces mistakes due to human error or mis-measurement by hand – or even when calibration is not done at all. The software can be scheduled to run automatically at the next job boundary after a specified number of hours or printed pages. It colour matches to the designer’s brief using advanced destination profiling.
The colour-savvy J75 is a bellwether of sorts. It shows that nowadays, colour management loaded onto the press is not confined to litho sheet and webfed – a widening range of commercial digital presses from a handful of vendors have got into the game.
Kodak Australia’s print solutions manager, Darren Yeates, confirms that onboard colour control is available on both the NexPress and high-volume inkjet Prosper press. In both lines, the front end has the ability to store unique ICC profiles for each grade of paper. Likewise, the front end has the ability to honour embedded profiles or override them. Customised ICC profiles can be created, and rapid adjustment of the press to match a particular standard or device is easily accomplished, he says.
Kathy Wilson, Ricoh Australia’s general manager, business solutions & production, says that colour management comes standard across its colour range, including the Pro C901 and C751.
Ricoh helps printers with customised colour matching, often across devices from a mix of sources and across the offset-digital divide. Further profiling can be done ‘off-board’ using EFI Colour Profiler and Ricoh’s production consultants are available to match each device.
Case study: Crucial Colour
Gary Furness, director of New Zealand’s Crucial Colour, runs a seven-year old offset and digital business in Auckland’s Penrose, with 52 staff, handling printing, finishing and project management for a mix of advertising agencies and direct customers.
Furness tells ProPrint that all the Ryobi presses in the company’s fleet have onboard colour control and the additional features came standard with the press orders. Driving colour from the press has boosted colour accuracy, which in turn has resulted in speedier makereadies.
Training up Crucial’s press operators went smoothly, he said. “Cyber has its own print demonstrator who provided us with all the training required.”
In fact, he went so far as to agree with the observation that handling inline colour management is fast becoming a ‘green-button’ push.
Case study: SOS Print & Media
At Sydney-based SOS Print & Media, a line of Ricoh C901 presses were spec’d with EFI’s onboard Fiery RIP, says director Michael Schulz. “The cost margin to have onboard spectrophotometry wasn’t massive and we always wanted it, so we didn’t quote without it. These days, you can’t say ‘It’s only digital, so the colour doesn’t have to be accurate.’”
SOS also has an older Xeikon 5000 kitted out with a spectrophotometer “but it’s of limited functionality. It’s not going to make the running of the machine that much easier because it’s not a full closed circuit and you still have to make adjustments.”
Schulz says that when the company moves into high-speed, high-volume colour inkjet, it will definitely spec it with inline colour management.
“It’s absolutely certain that if you do have a closed-loop system, there are no variations of colour in the run. In those volumes, you need onboard colour control, as you can’t always be stopping and starting to sample.”
There was a considerable learning curve for operators on integrated colour management aboard the Ricohs, says Schulz.
But that’s partly because SOS “pushed the envelope” to beat competitors to the forefront of the colour management field. There was no training blueprint and SOS took it a step at a time. “We learned together with our suppliers, Ricoh and EFI.”
The commercial printer also has onboard colour control on its offset line-up – a spectro-photo-meter on its Akiyama Jprint 42 that was spec’d with the purchase and another on its 10-colour Heidelberg Speedmaster 102, which was retrofitted.
The retro-fit was, in Schulz’s words, “a fair investment… but worth it”. All offset and digital output at SOS conforms to the AS/ISO 12647-2 standard.
Comment below to have your say on this story.
If you have a news story or tip-off, get in touch at editorial@sprinter.com.au.
Sign up to the Sprinter newsletter