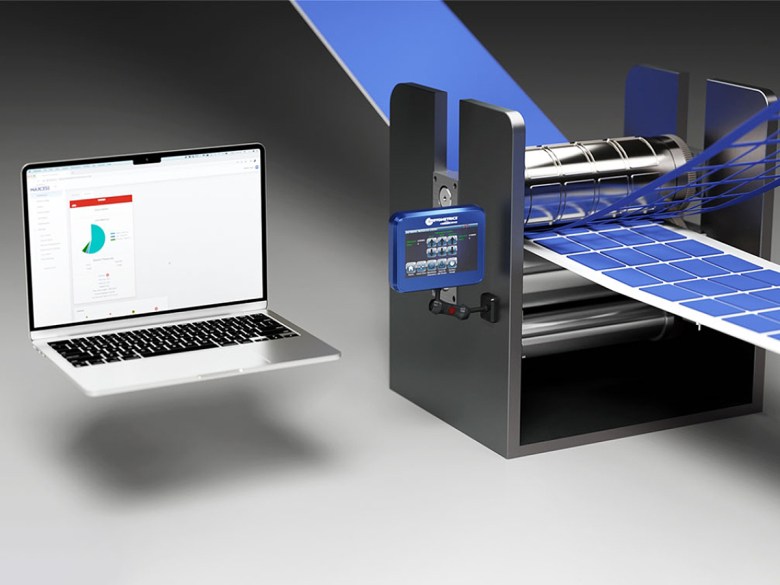
Maxcess, a web handling specialist, has launched RotoMetrics RotoAdjust, an intelligent die station featuring an easy-to-use touchscreen, critical industry 4.0 alerts and analytics and the ability to re-order worn components online.
The new product features an intuitive colour touchscreen interface with software able to store and recall typical jobs from its history.
Moreover, it provides analytics from the entire die station, claimed to be the first feature of this kind in the industry. It gives operators access to critical data such as die station revolutions, material usage, pressure information, setup and run times, and more, allowing them to run and plan work more efficiently.
When critical components are projected to wear out beyond recommended operation, operators receive alerts and can automatically re-order parts through an online portal with a single click.
“We designed the new RotoAdjust from the ground-up with our global R&D team, which has spent decades designing and shipping automated web handling solutions from our storied brands of Fife and Tidland,” said Nadine Powell, global product manager at RotoMetrics, a Maxcess Brand.
“This solution gives customers an intuitive and powerful tool to control liner variation that they are seeing daily. The RotoAdjust lets you work smarter, with its industry-leading Industry 4.0 analytics that alerts operators to failure points and highlights worn die station components while directly interfacing with our MyRoto.com e-commerce platform for single-click re-ordering,’ concluded Powell.
Comment below to have your say on this story.
If you have a news story or tip-off, get in touch at editorial@sprinter.com.au.
Sign up to the Sprinter newsletter