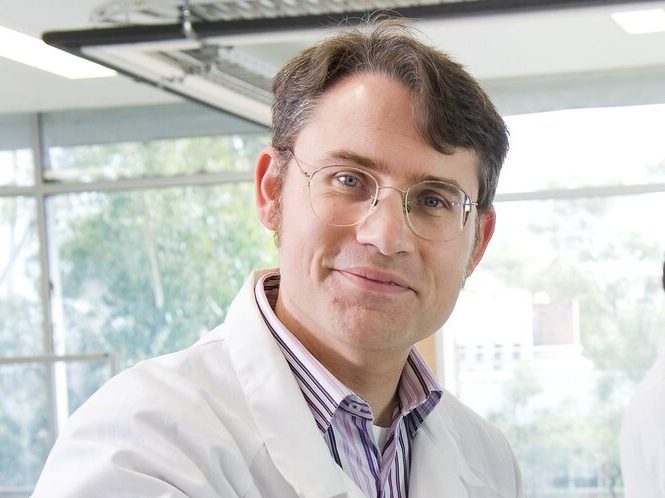
This article was republished from the May issue of Australian Printer, authored by the NSW Smart Sensing Network’s Prof Paul Dastoor
Traditional printing typically involves patterning surfaces, such as paper, card and plastic, with pictures and words. However, the discovery and development of semiconducting inks means that electronic devices, such as solar panels and biosensors, can now be created using commercial-scale printing.
The Centre for Organic Electronics (COE) at the University of Newcastle, Australia, has been working for many years to develop a range of printed organic devices, ranging from large scale printed solar panels to biosensors to tackle urgent global healthcare issues such as eliminating painful finger-prick glucose testing for diabetes sufferers.
The low cost of roll-to-roll (R2R) manufacture means that printed organic electronic devices can be manufactured at extremely low-cost. For example, printed solar panels can be fabricated and installed at a cost of around $10/m2.
Moreover, no other renewal energy technology can be manufactured as quickly and because printed solar panels only weigh 300g per square metre (compared to standard solar panels that can weigh as much as 20kg per square metre), no other competing technology can deliver as much electrical power per gram of manufactured solar panel.
The low cost and weight of this technology combined with speed at which it can be deployed is exciting; enabling solar applications for areas where conventional panels simply are not suitable, such as rapid deployment of solar energy for disaster relief. Indeed, there are over 100 million square metres of lightweight industrial roofing that simply cannot withstand the weight of conventional solar panels.
Manufacturing of printed electronic devices involves multiple layers fabricated using a range of printing techniques – from gravure to slot-die coating – that are commonly used by the printing industry. The printing machines at the core of the industrial development of the technology are conventional converting line instruments.
However, the challenge lies in developing the science and technology to allow the printing of functional inks to produce controlled electronic layers that are extremely thin and uniform over large areas.
Additionally, extensive facilities for upscaling the production of the required organic electronic materials have been established by adapting existing chemical synthesis to enable production at large scale, thus dramatically lowering costs. For example, by tuning reaction conditions to reduce synthetic complexity and avoiding expensive purification, reaction yields are maximised while solvent use and waste are minimised.
Moreover, with over 99 per cent of the printed electronic technology consisting of PET, the material can be simply recycled – a distinct advantage over traditional silicon-based electronics. Recycling for the technology is relatively straightforward procedure, involving separation of the outer PET layers, a series of sequential R2R washing steps enabling reuse with minimal processing. Indeed, with clever handling it is now possible to separate the electronic inks back into their constituent components.
The potential market opportunities for printed electronic technologies are enormous. For example, consider the global market size for blood glucose sensors, which was $15 billion in 2021 and is expected to grow to over $30 billion by 2030.
Alternatively, reflect that with the current global focus on the need to transition the world’s energy profile to renewable sources, the global renewable energy market that was worth $900 billion in 2021 and is projected to reach $2 trillion by 2026. Indeed, most OECD countries are committed to expansive renewable energy growth and a rapid transition of energy production away from fossil fuels. In this environment, the prospect that the printing industry could simply print at low cost enormous numbers of glucose sensors or vast areas of solar panels is extremely attractive.
Establishment of the first manufacturing facilities for printing these new technologies is well underway. With support from the federal government’s Modern Manufacturing Initiative, the COE is working closely with their commercial partners on a purpose-built manufacturing facility.
Construction will begin on the facility this year, with the first devices due to roll off the production line by early 2024. In addition, establishing a printed electronic device industry from the ground up also requires creating a workforce with the required skills and knowledge.
Flexible teaching programs have been designed to allow students to study full or part-time for a series of qualifications, ranging from a six-month Graduate Certificate all the way to a two-year Masters Degree. These new education and training programmes will attract new printers to the industry as well as equip existing printers with the skills and knowledge needed to join new companies, transition existing companies or establish new start-ups.
Comment below to have your say on this story.
If you have a news story or tip-off, get in touch at editorial@sprinter.com.au.
Sign up to the Sprinter newsletter