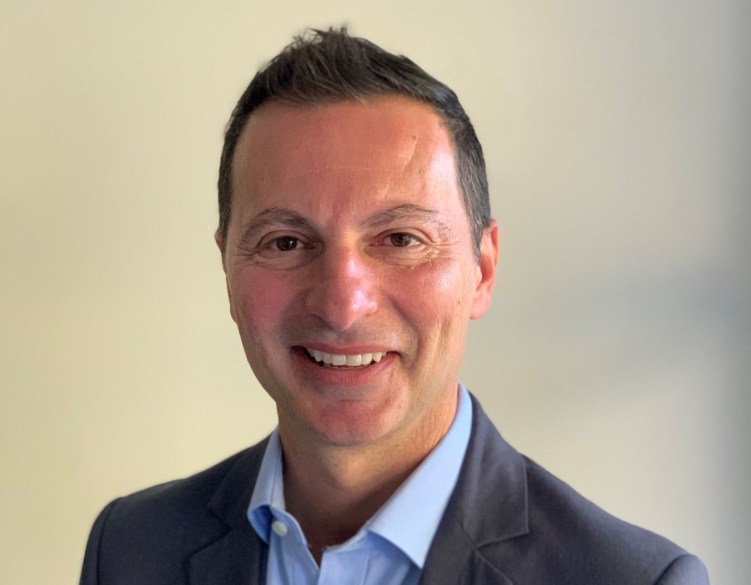
This article was first published in the March 2021 issue of Australian Printer, by Heidelberg A/NZ managing director Savas Mystakidis
Printing is like triathlon. A three-in-one race, all against time. Plates and correct parameters from pre-press, accurate fine print from press in order to finish perfectly in post-press, right before delivery. Every process in print production is equally important as they are inter-dependent in achieving the best quality on time.
Post-press may involve different processes on different equipment. For example, producing a greeting card with hot foil stamping, embossed and die-cut before folding can be exceptionally challenging. As the last process in print production, compensating delays or flaws from pre-press and press if any, yet producing and ensuring the print products is at its finest quality with the least waste and delivered on time all happen in post-press. It can be a real disaster if post-press production is not properly planned in the beginning.
In the commercial space, Stahl folder’s pallet feeder allows the printed stack to be fed directly while the PFX feeds the substrate into the folding machine in shingled mode. Furthermore, camera systems that scan the barcode on the sheets has made Push-to-Stop a reality in folding.
The peak performance Stahl folder, TH82-P, capable to achieve 15,000 signatures/hours, is well accepted by the market and is proving to be a real benchmark in the industry.
Not only does the TH82-P match the performance of XL 106 sheetfed for mid to long run jobs, Push-to-Stop has broadened the job scope to short run also. The professional packaging houses love the stability as well as the user-friendly operation.
In the packaging segment, Masterset is an optical registration system that aligns the sheets perfectly before hot foil stamping or embossing and die-cutting; while the inline inspection on the selected Diana series folder gluer allows the blanks to be inspected before being folded and glued into carton or envelopes for greeting cards in this case.
Masterset saves tremendous time and waste sheets, as it ensures every sheet is aligned perfectly, even if the sheets have to go through the Promatrix multiple times for different processes.
For professional packaging houses, both Promatrix series and Diana Easy are among the preferred models in the region. The Promatrix 106 FC comes with hot foil stamping and die-cutting while the Promatrix 106 CSB processes the sheets directly into blanks.
While Diana Easy is famous for wide range of applications, not only in traditional box designs up to four and six corners and double wall, but also for commercial jobs such as CD sleeves and envelopes, the Digiset improves the setup times by 10-15 minutes.
Not to forget, all Heidelberg/MK equipment are GS certified.
Some areas of play within post-press that are lucrative for printers include embellishments such as deep embossing on wine or whiskey case, hot foil stamping on cosmetic packing and hologram on pharmaceutical and product cases that set to fight counterfeiting are lucrative as they are high value-adding to the prints, thus leaving a good impression to the consumer market; they’re excellent for branding.
But there are some challenges that printers should be aware of in the post-press space.
The most common is printshop digital workflows that stops at press. Collecting accurate production data from different types and brands of post-press machines can be extremely challenging, especially the analogue way. However, this is what we are seeing today in most of the print houses.
Subsequently, avoiding data manipulation as well as typos during data input is again difficult. The cost of the whole exercise becomes significantly high, especially with the risk of making poor business decisions out of the inaccurate data.
Printers can alleviate these challenges by using fully integrated printshop digital workflows. Heidelberg has Prinect Postpress Manager and Postpress Data Ready to simplify the production planning through digital data acquisition from post-press.
The former is complete digital workflow from Heidelberg, that is ready for autonomous production on Stahl automated folders while the latter focuses on production data reporting. The non-proprietary Data Ready allows the data collection from MK Packaging equipment in XML for analysis. Data Ready is set to be open for more post-press in the market, regardless of brands.
In the coming years, post-press in the post-pandemic economy is set to be equipped with more automation that is not only labour saving, but also more hygienic as it involves less human touch points.
Besides, combining different processes into a single platform it will ensure greater efficiency in post-press production that meets both quality and quicker delivery expectations.
Integration will occur via Prinect Postpress Manager and Postpress Data Ready that will allow complete transparency in post-press production. This will expand widely in the future thus connecting post-press equipment brands that are willing to work together, to major MIS systems available in the market.
Comment below to have your say on this story.
If you have a news story or tip-off, get in touch at editorial@sprinter.com.au.
Sign up to the Sprinter newsletter