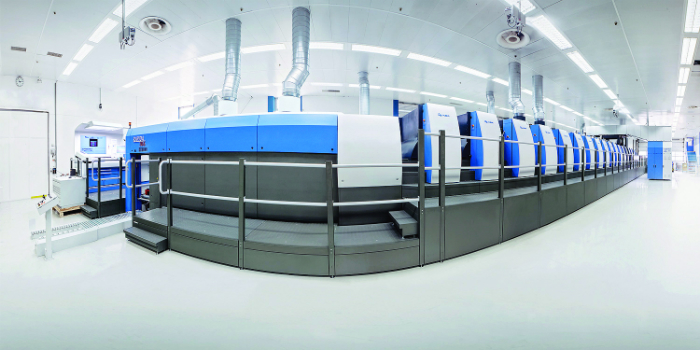
Commercial printing is under pressure. Print providers face shortening run lengths, customers wanting jobs yesterday, cutthroat competition, and the lure of electronic alternatives online, are some of the forces impacting on print businesses.
The past few years have seen the local commercial printing industry destabilised – especially at its SME core – with sweeping amalgamations that rolled in and rolled out, the rise of the internet as a cheap communication alternative, and a crippling global financial crisis.
It has been survival of the fittest – or as the saying goes, what does not kill you makes you stronger. So what are the success secrets in effective, productive commercial pressrooms in Australia today?
Print prices remain depressed, and the drive is on for printers to increase margin by increasing their productivity. That means more sheets out the door in less time, with less wastage and shorter downtimes.
Transforming in the West
At Scott Print, a well-known 37-year-old hybrid offset/digital enterprise in Perth, co-general managers John and Tim Scott have introduced a number of efficiencies in the pressroom, and in the enterprise at large, to keep down costs and improve productivity, while the business continues to gain market share and grow revenue to the point where Scott Print is now regarded as a highly successful combined offset/digital printer in Western Australia.
John Scott, who is on the board of Printing Industries, sees the trend nationwide to print providers becoming more efficient, and focusing on the total requirements of their customers, as well as branching into new fields to make up for work that has been lost to electronic alternatives.
And Scott Print, a family business located in Northbridge, with a diverse, dynamic staff of around 50, has been quick to adopt these types of measures in its own business, Scott tells ProPrint. For example, digital printing represents more than 17 per cent of its overall turnover – and graphic design is a strong component of the business as well.
“In our own business, we are finding less of the work is scheduled, or at least planned well in advance,” he finds. “Our commercial offset side is becoming more like instant digital printing, in that sense.”
Two years ago, the company upgraded its press fleet from three A1-straight presses and a five-colour plus coater to two Komori Lithrones, an eight-colour perfector for four-over-four work, and an A2 six colour with coater for PMS jobs.
Both Lithrones have Komori’s H-UV technology on board, and for Scott Print, H-UV means more accurate, dynamic colours, the almost complete elimination of dot gain, and new frontiers in versatility when it comes to stocks.
“With H-UV, the ink is immediately dry. Our offset printing area has become virtually like our digital area, in that we can advance to the next step immediately,” Scott explains.
On the digital side, Scott Print operates two Xerox 1000i presses which use matte inks and each has a fifth station for silver, gold or clear gloss. “Matte printing on the 1000s closely matches that on the Lithrones, so that the overall output is consistent,” notes Scott. As well, there is an HP Indigo 5000, which also closely matches the H-UV presses.
Initially the company ran an integrated digital-offset workflow but, says Scott, “Higher volumes and the generally faster pace on the digital machines meant integrating key processes between the digital and litho sides of the business tended to slow the overall throughput.”
Four years ago, Scott Print bucked the trend and introduced separate offset and digital workflows, customised to the specific requirements of the two parallel but separate technologies. Says Scott: “At the end of the day, it is easy enough to switch a job from digital to offset, based on workload and capacity on each press.”
What the vendors say
Heidelberg A/NZ managing director Richard Timson says that for several years now, technologies have been integrated into midsized offset presses to enable more efficient, productive pressrooms.
“Technology like full autoplate, synchronised plate insertion, pre-inking, automated makereadies, CIP4 transfer of files – all of these enable customers to run down to 50 copies and be profitable. Alternatively with the Anicolor technology, you can run as low as 20 sheets which for expensive specialty stock results in huge savings,” he explains.
But investment in these efficiencies is a basic prerequisite, he believes. Lower-specified alternatives might save a bit of capital up front, but have a cost-drag downside. Without these integrations, forget about six-minute makereadies, and be content with 15 minute makereadies.
He sees integrated offset-digital workflows as common today, “however not all printers choose the right output device to print on, as the easy but less profitable option is just to send it to digital”.
At last year’s drupa, the German press giant introduced its Speedmaster XL106, which embodies Heidelberg’s ‘push-to-stop’ philosophy, providing digitised and integrated print production. Makeready times on the XL106 are dramatically reduced with the new Hycolor Multidrive inking unit and further automated, parallel processes. Meanwhile, intelligent assistance systems take the strain off the operator and enable maximum productivity.
The outging manroland Australia managing director Steve Dunwell says its sheetfed division provides both quality and innovation. “On one hand, our presses are known for their durability and perfect register, even after more than 500 million printed sheets, and on the other hand, our permanent development of new features for the benefit of our customers, such as simultaneous plate loading for medium and for large size, inline colour measurement and inline register, extra-large paper sizes like 3B+ or 7B+, indexed InlineFoiler, LED UV curing, and so forth, will continue driving our future technologies.”
Reflecting on changes in sheetfed technology, Dunwell says: “Since the small size suffered during the last decade due to several structural changes – namely digital and productivity – and the large size seems not to become a mainstream – lower volume, shorter runs – the 3B size fits well into the current market demands for packaging, commercial and even editorial print. The Roland 700 Evolution offers 3B format (740mm x 1040mm), as well as optional 740mm x 1050mm and 780mm x 1050mm.”
Dunwell says that in addition, automation, makeready time, and enhancements tend to be the keys to success for most printers. “The Evolution fulfils all these criteria offering a good price/performance ratio.”
He notes onboard features that enhance productivity include automation technologies adapting to further shorten makeready time (Simultaneous Plate Loading System, InlineColorPilot and InlineRegister), reduction of cost per copy (dynamic ink controlling, InlineInspector), and adding value through inline enhancement measures (InlineFoiler, double coating, UV, LED UV).
“Our upgrade products and solutions can also make more out of existing presses, such as FutureProof technology the ‘printservices’ portfolio and ProServ,” he says.
According to KBA Australasia’s general manager Dave Lewis, ultra-quick makeready is an SME pressroom’s greatest resource. The Rapida 106 exemplifies the quest for speedy makeready and a host of productivity enhancing features, he adds. “Our Rapida 106 has a sidelayless infeed and Simultaneous Plate Change via direct drive technology so all plates are changed in 50 seconds while the blankets are washing.”
KBA’s PlateIdent system pre-registers the job before pulling the sheet and the QualiTronic ColorControl camera system starts measuring and adjusting colour, including special colours from the first sheet. “Our Data Matrix Select feature scans a QR code on the plates as the plates are being loaded and finds the job automatically in our LogoTronic server and then sets the press up without the operator having to locate the job on their console,” says Lewis.
Meanwhile, KBA offers its Rapida 105, which is built on the same platform as the 106 but with a lower level of specification and price.
OffsetOnDemand is Komori’s system to facilitate short runs and quick turnarounds by shortening makeready time, cutting paper waste and reducing the printing process to the absolute minimum, says Print & Pack’s sales manager, southern region, David Corbo, while maintaining the high print quality and productivity of offset printing.
“The core of Komori’s new Offset-OnDemand printing system is the fusion of the KHS-AI integrated control system, the award-winning H-UV Innovative Curing System and the new leading-edge colour management system. The result, OffsetOnDemand, is the ultimate short-run and quick- turnaround solution for today’s highly competitive printing marketplace,” he says.
Corbo has found significant transformations in offset press technology to help SMEs achieve greater productivity. On the Lithrone GX series, specifically the newly released GX44-RP, these have combined to create what he describes as ‘the ultimate one-pass, double-sided printing press’.
Features include labour-saving automated systems such as the KHS-AI (Advanced Interface) and benderless Full-APC (auto plate changing). The configuration of the one-pass, double-sided press, which does not involve sheet reversal, contributes to the efficient use of paper because of the tail-edge margin required for a perfector is unnecessary.
Equipped with the newly developed A-APC (Asynchronous Automatic Plate Changing System) for significantly shorter makeready times, the Lithrone GX44-RP also sports the H-UV system, which enables fast print drying and short turnarounds. “For linkage with prepress and postpress equipment, Komori assures JDF connectivity and conducts frequent inter-operability testing with systems from other manufacturers and vendors. This way Komori implements open architecture thinking, with the priority on users’ operating environments,” says Corbo.
Running down all inefficiencies in a pressroom is a rewarding discipline in terms of the bottom line, reflects Greg Knight, general manager, Victoria and Tasmania, at Cyber Group.
Supplying RMGT (Ryobi Mitsubishi Graphic Technology), Cyber Group has been supporting its customers in their search for more efficient, automated pressrooms, he says, with most of these efficiencies being onboard or inline integrations.
For example, LED-UV on board a Ryobi press will cut power consumption by up to 90 per cent in energy-hungry activities such as UV printing, notes Knight, and also provides instant drying for speedier turnarounds.
Ryobi’s flexibility with a broad array of stocks means the press range is ready for print shops that want to venture out of their conventional operations and take on packaging work, he says.
The RMGT 9 series is 8-up DIN A4 production, and the LED-UV option enables the delivery of sheets that are completely dry, suitable for feeding back to print the reverse side, or to deliver straight to the finishing department. This means no stacks of part printed work on the shop floor. One critical element of LED-UV that speeds up payback of the investment is the low power consumption compared with IR or other UV products.
With a smart fully automtic plate change the basic 920ST-4 changes plates in 75 seconds, while the long perfector 920PF-8 does it in 100 seconds. Printing speed for the 920ST-4 is 16,200, while the 920PF operates at 13,000sph. Offset litho printing presses have come a long way in a short space of time, as they meet the challenge of a market that wants on demand print of the highest quality.
Comment below to have your say on this story.
If you have a news story or tip-off, get in touch at editorial@sprinter.com.au.
Sign up to the Sprinter newsletter