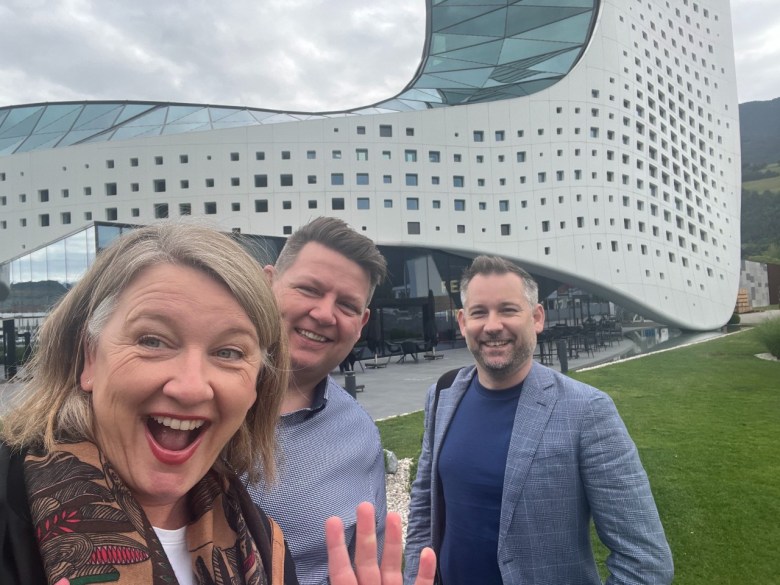
This story was originally published in print in the August issue of ProPrint magazine. To read the full story click here.
Anyone who makes the trip to Durst’s corporate headquarters and factory in Brixen in northern Italy is in for a treat.
Not only will you see from start to finish the meticulous process that is undertaken in building a Durst digital printing system from the ground up, but you will also receive a solid dose of Italian hospitality and the opportunity to wander through a historic village – all set against the dramatic backdrop of the snow-capped South Tyrol.
Durst Group is a third-generation family business which is majority owned by the Oberrauch family with CEO Christoph Gamper also holding a stake.
The company started in 1929 and now boasts 880 employees worldwide and a solid reputation for the quality and reliability its advanced digital printing technologies provide in the global graphics, ceramic tiles, labels and packaging and commercial corrugated packaging markets.
Durst also offers software including back office ERPs, digital workflows and B2B/B2C online store front solutions.
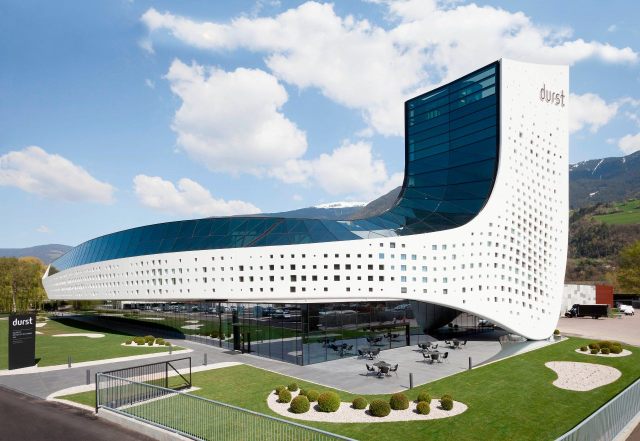
Additionally, it also owns a number of other companies, including Alupress – a producer of high-grade aluminium, TBA – a start-up incubator for budding entrepreneurs and ADAM – a specialist in 3D metal printing.
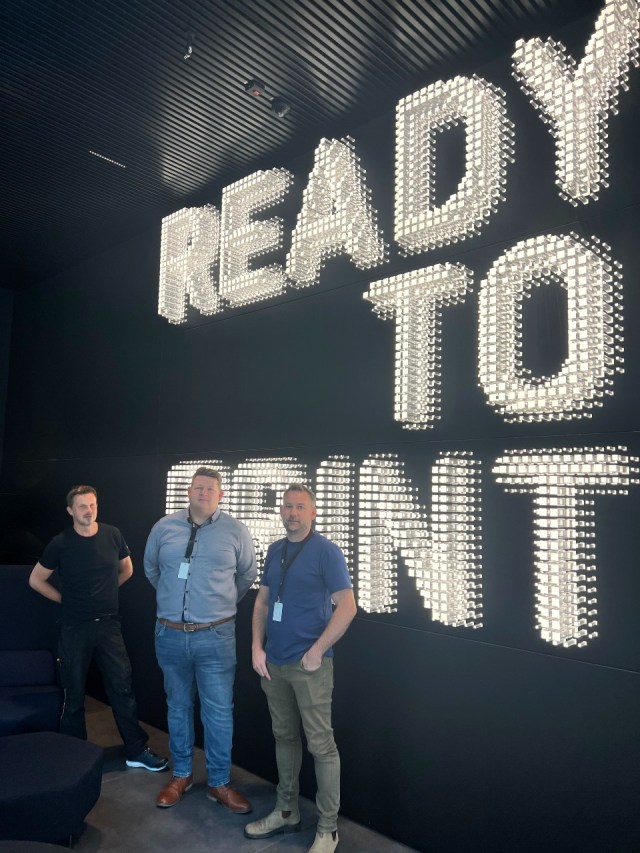
Durst’s reputation is further illustrated by its striking Brixen headquarters, with another remarkable building also at its sister site in nearby Lienz, Austria.
The Brixen site showcases incredible high-end design, a variety of different outdoor spaces which were being attended to by two robotic lawn mowers during my visit, a seriously lovely café and an educational theatre space named after the creator of the first ever computer, Ada Lovelace, which the local community can also utilise.
Durst Oceania’s Ashley Playford-Browne and Dan Mantel doubled as tour guides for my recent visit to Brixen with the added assistance of Durst’s Brixen-based Roman Dorigetti who led the tour through the Customer Experience Centre and the factory that operates behind it, producing some 300 machines a year.
Early beginnings
Durst’s history is rooted in photographic reproduction technologies.
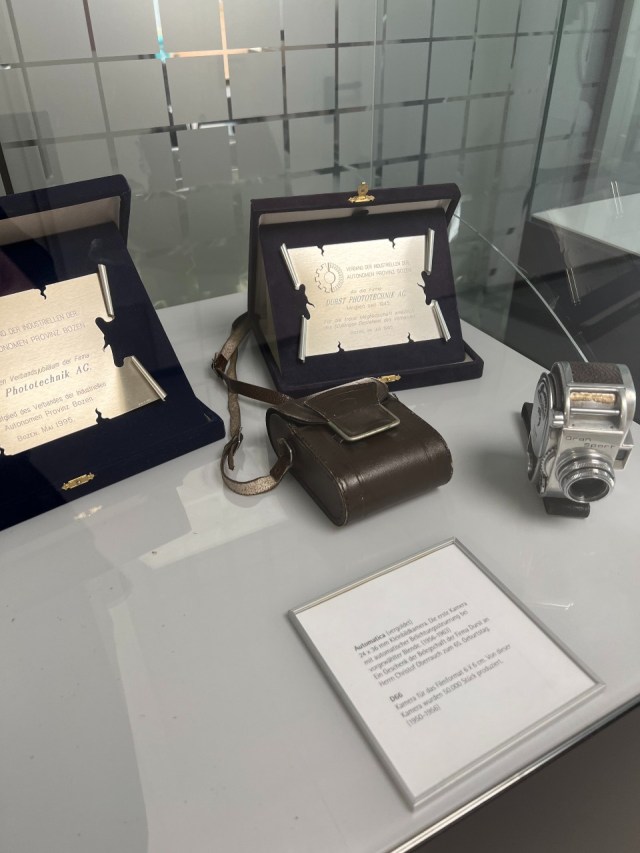
In 1956 Durst broke new ground by inventing the ‘Automatica’ – the first ever film camera with an automatic exposure system which is often referred to as ‘point and shoot’.
Then in the 1990s it launched the ‘Lambda’, a photographic-based digital enlarger which enjoyed strong take-up for producing high quality advertising photographic banners, particularly in the beauty industry.
“Still to this day the Lambda is the best quality backlit print you can get,” Playford-Browne said.
“The Lambda got us on the digital path and in the early 2000s we entered into wide format and this was soon followed by ceramic tile printing, label printing, textile printing and corrugated.”
The lessons learned on the journey from then to now continue to impact Durst’s research and development. The majority of the R&D is conducted at Brixen, with additional scientists and laboratories located at Lienz.
Successfully manufacturing highly industrial digital ceramic tile printing systems, which cannot be turned off due to the kilns that also operate in the production line, is one area which has provided a solid base for building machinery which is strong and reliable.
“Ceramic printing has to be run 24/7. Uptime is critical as the line can only be stopped twice a year for maintenance, so it demands that the technology be very reliable. It is single pass technology and Durst applies that same technology to other areas of the business,” Playford-Browne said.
There are high numbers of these ceramic tile printers around the world, with one location alone operating 60 units constantly.
Similar lessons have been learned with ink formulation. Pigment inks are used across Durst’s platforms but there are five different kinds, each developed specifically for certain substrates whether that be flexible, rigid or textile. Once the inks are formulated in Lienz they are then manufactured in bulk with every single batch returned to Lienz for testing to ensure the ink is working and is consistent with the tolerances of the Durst machines.
“The issue with inkjet is if the ink is not consistent it can block your heads and kill your printheads which can cost a lot of money to fix so what we do is we check the ink ourselves to be sure the batch conforms to our tolerances,” Playford-Browne said, adding each batch carries a QR code which once scanned informs the system that the ink is in date and suitable to proceed.
Designer factory
The word factory doesn’t properly explain the experience of visiting Durst. Yes, it is a factory, but the words ‘Designer Factory’ did spring to mind during my tour.
Precision was another word that leapt out. Each digital machine built at Durst is done so by a specific team of engineers and technicians who shepherd the platform through each stage of production.
Durst machines are literally built from the ground up at Brixen, even down to the internal componentry which is made onsite using premium aluminium supplied by Durst’s company, Alupress, which also supplies the aerospace industry.
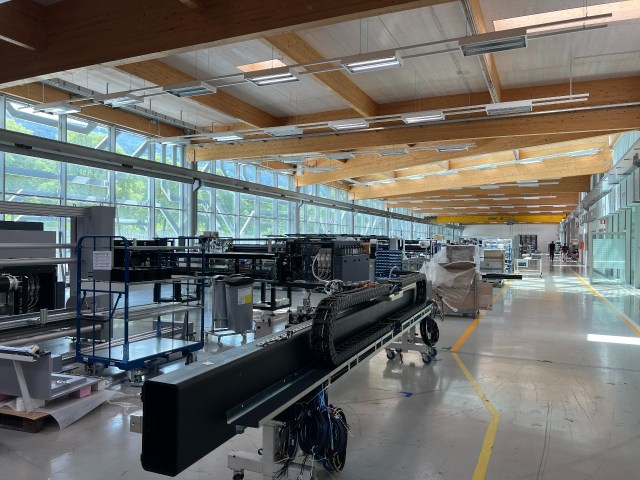
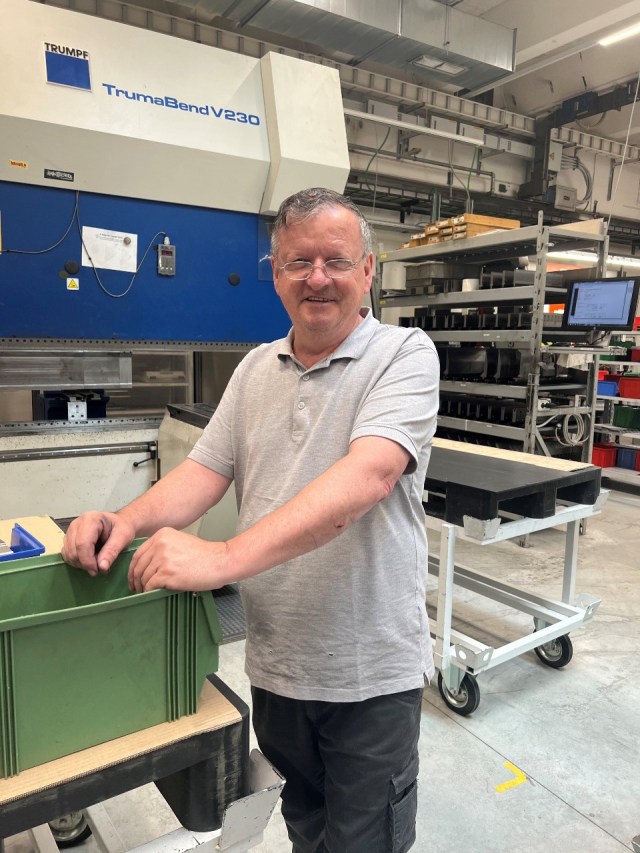
at Durst for 43 years making the aluminium parts which are built inside the machines.
Massive industrial CNC machines on site at Durst ensure Durst engineers can control every part of fabrication and manufacture.
Playford-Browne explains the benefits of having ownership of the aluminium part of the supply chain.
“It is all about the quality and in times like this aluminium is going up, but we have control over our supply chain which means as a manufacturer we can remain quite competitive as well. Everything in the machines is made here and the tolerances they work to are very high.”
The modular nature of the Durst platform makes it a popular choice for printers who can pick and choose what they want to add to the core unit – automatic loaders and stackers, a flatbed for rigid stock or extra rollers.
The other part of the system which is standard across all product types is the massive 500-kilogram steel beam which holds up the print sledge and allows the ink to be dropped with incredible speed and accuracy.
Watching a steel beam being hoisted into the purpose-built temperature-controlled room specifically for this part of the build was mesmerizing. To maintain the desired 24 degrees Celsius and keep any dust out of the space, an automatic sliding glass window automatically shoots up and down as a crane hoists the mighty beam in.
Once it has been carefully placed, the window zips up again.
Two technicians then set to work maneuvering the beam into place. If the beam is out by even 0.1mm there can be issues down the line with ink drop and speed, so it is imperative that this is done – perfectly.
Production for the popular P5 large format and TAU RSCi UV inkjet label platforms – both of which have had strong take up in Australia – was running hot during my tour with machines lined up across the factory floor in various stages of construction.
This next part of the factory has sky-high ceilings lined with natural timber beams which exudes a sense of calm as the teams of technicians put the final touches on the machines. Floor to ceiling windows allow the ever-present mountains to stare in and show their beauty.
From the rear of the factory floor the loading dock awaits, ready to ship the completed machines out to customers near and far.
New P5 500
The day after my visit to Brixen, the new P5 500 five-metre platform was launched at the FESPA Global Print Expo in Berlin. It brings a five-metre option to the P5 family and as such offers commonalities which allow for greater operability and ease of servicing.
The P5 500 features integrated roll support for ease of change and has multi-roll functionality as well as an in-built retractable mesh kit which saves operator time and increases productivity.
Other features include an option for double-sided registration and an integrated horizontal cutting system which means the press does not need to stop while cutting.

For more information, please contact Durst Oceania.
Comment below to have your say on this story.
If you have a news story or tip-off, get in touch at editorial@sprinter.com.au.
Sign up to the Sprinter newsletter