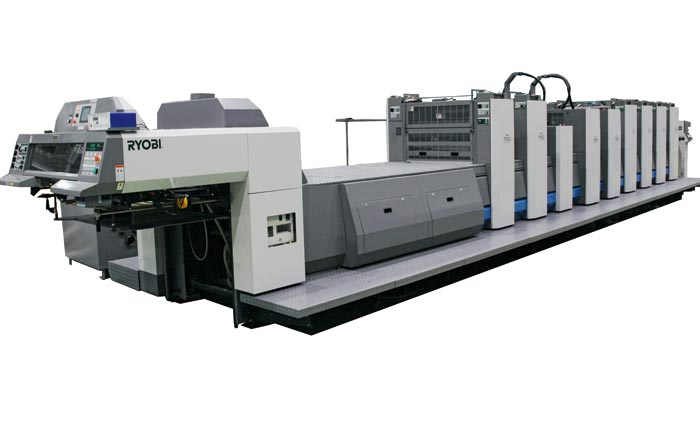
A decade ago, Japanese-based printer Komatsu General Print Co faced a situation that is all too familiar to commercial printers around the globe. Strong local competition meant margins were dwindling. It left the company facing a stark choice: keep filling the presses regardless of margin or diversify into new, high-margin areas of work.
It was a tough call but the management knew that to secure the business’s long-term survival, they needed to branch out into emerging growth areas. So Komatsu invested in a six-colour sheetfed press in 2002 and started printing folded postcards for direct mail applications. The tactic paid off in spades. Komatsu quickly established itself as a major player in the direct mail market. Over time, Komatsu’s offer evolved, with the company adding greater levels of variable data to mailers, such as barcodes and numbering. But company president and chief executive Toshihiko Komatsu knew that there were greater opportunities out there in high-volume variable-data work of run lengths from 1 million to 100 million.
To achieve this, he needed a high-speed variable-data printer. But this was 2010 and at the time there was nothing on the market capable of doing this type of work. So Komatsu approached Kodak and Japanese press manufacturer Ryobi to come up with a device that could meet his requirements. It took just under a year for the partnership to deliver a nine-unit machine, which the manufacturers claim was the world’s first fully integrated hybrid sheetfed press.
Although the product was developed for a specific client with a specific need in mind, the finished machine was so impressive that at Drupa 2012, Kodak and Ryobi announced their plan to offer the configuration to customers worldwide.
Unique spec
In this configuration, the first four units are process colour units, the fifth and sixth unit include three inkjet Kodak Prosper S5 Imprinting Systems, the seventh unit is an NIR dryer, the eighth offers spot colour and the ninth unit is for UV varnishing. Thanks to the machine’s unique configuration, Komatsu can now print high-volume direct mail pieces containing variable information in a single pass without resorting to the costly and time-consuming use of laser printers.
The end product is printed four or five colour, features addressing and QR coding thanks to the Kodak inkjet heads, plus it is UV pressure seal coated, explains Bernard Cheong, managing director of Cyber, the exclusive distributor for Ryobi machines in this region.
“With the UV pressure seal coating, the mailer is easily folded, pressure sealed and slit to make for a high-quality, highly productive, highly efficient production system,” says Cheong.
Building block
Cheong is the man faced with the task of selling the machine into the Australian market. He explains that the basic building block of the hybrid press system is the Ryobi 750 series, which is capable of printing at a top speed of 10,000 sheets per hour (sph). The B2 machine boasts
a number of different features that are commonplace in today’s marketplace. These include a semi-automatic plate changer (fully automatic is an option), automatic blanket cleaning as standard and optional extras such as a smart make-ready function, which the manufacturer claims can shave as much as two minutes off makeready times, and an ink roller temperature control system to ensure consistent quality even on long runs.
Nothing out of the ordinary there, you might think. But where the hybrid system becomes extraordinary is when you start to investigate the vast gamut of different configurations that are available. In addition to offset printing and inkjet printing, you can plump for the inline varnish station. Then there are the option around inkjet heads. Customers can choose from two heads with one drier, four heads with driers or four heads with driers and the inline varnish station.
The configuration varies from customer to customer with 200 different flavours to choose from, explains Cheong. “Ryobi has a large research and development team and a flexible manufacturing system and they are able to address many different customised requirements. Most of these presses are manufactured according to the customer’s wish list and [the Komatsu machine] is an illustration of one of the many possible configurations.”
For Cheong, the key benefits of the hybrid system are “versatility, productivity and efficiency – these are the tools to reduce production cost and improve profitability”.
When you consider how the new system stacks up with the traditional existing method of producing variable data sheetfed work, it’s easy to see why the partners are making such loud claims about this being a game-changing device. At present, if you want to produce a personalised mailer you have to print the direct mail shells on an offset press, let them dry and then imprint them on a laser printer. This can add two days to the production process. However, with the hybrid press you can achieve the same result in a single pass, which saves both time and money.
Inkjet magic
While the Ryobi 750 series may provide the foundation for the hybrid system, it is the introduction of the Kodak Prosper S-Series imprinting heads that make the magic happen. “These heads have been around for only the past two to three years,” explains Darren Yeates, business manager of digital print solutions at Kodak Australia. “However, we have had the previous models of D Series heads for more than 10 years now.”
Kodak Prosper S-Series Imprinting Systems include the S5, S5 with CMYK, S10, S10 CMYK, S20 and S30, with each solution providing “laser-like quality for imprinting at a range of speeds and resolutions, bringing high-quality personalisation to offset print jobs”.
For Yeates, the technology “has advantages over other manufacturers by using continuous inkjet instead of drop-on-demand”.
The S5 heads that Komatsu opted for feature pigment-based ink, which Kodak claims delivers “excellent permanence on a variety of commercial substrates providing scratch, fade and water resistance”. The imprinting system runs at a speed of up to 500 feet per minute at a resolution of 600x600dpi – Kodak recommends that the heads are used in conjunction with a NIR inkjet drying system or similar equivalent product.
Given the number of different options available in terms of print heads alone, it’s almost impossible to put a guide price on what the hybrid system will cost customers, according to Cheong. “All custom presses are application dependent and the prices vary according to the complexity of the requirements. Unfortunately there isn’t a one-size fits all formula – each solution is individually tailored and we will address each customer’s request individually.””
Volume user
To date, Cheong has received interest in the new hybrid system from mailing houses, but there have been no installations or orders placed by Australian customers, largely because “as this is a custom press at the moment we have yet to identify a user with the necessary volume to feed this highly productive system”.
When that first order does come in, Cyber is well placed to deliver top-class service levels, stresses Cheong. Despite its head office being based in Singapore, the company has personnel in all of Australia’s major states with local offices in Sydney and Melbourne and 35 trained service contractors across the country.
“We are a solution provider that continuously challenges ourselves to provide solutions that make our users more profitable and we have sold about 100 Ryobi printing presses – almost 500 printing units – in Australia since 2004. Thanks to our comprehensive after sales support network, we have many repeat customers,” says Cheong.
He’s confident that the company will eventually snare a customer for the new hybrid system thanks to its capability to “print and ship” at speeds never before seen in the sheetfed sector.
You only need to look at the example of Komatsu to see what the system is capable of delivering. Since the machine was installed in late 2010, the printer has handled a much higher throughput of jobs than any time in its history. The fast turnaround time, lower cost and higher productivity levels that Komatsu has been enjoying suggest that it won’t be long before other printers follow in its wake.
ALTERNATIVES
In theory, inkjet print heads can be added to any offset press although it’s much more commonplace to see them attached to web presses. “Sheetfed is a little more difficult due to the paper transport method and requires more development by the press vendor,” explains Darren Yeates, business manager of digital print solutions at Kodak Australia. As a result only a few of the leading press manufacturers currently offer this option.
Heidelberg has a custom bar that sits on top of the reel of the Cutstar sheeter that allows Kodak Prosper S5 Imprinting Systems to be fitted to its presses. And at Drupa 2012, Manroland showed an inline hybrid digital print module developed in conjunction with Atlantic Zeiser to add variable print capability for the printing of bar/matrix codes, names and text to its offset presses. Manroland says the hybrid printing module will not be commercially available until the end of this year at the earliest.
Komori and Konica Minolta also showed a concept machine at Drupa called Impremia. The Impremia IS29 is a four-colour 29-inch sheetfed inkjet printing system that offers 1,200×1,200dpi and a 3,300sph maximum printing speed. As yet there has been no word as to when the machine will be commercially available.
Comment below to have your say on this story.
If you have a news story or tip-off, get in touch at editorial@sprinter.com.au.
Sign up to the Sprinter newsletter