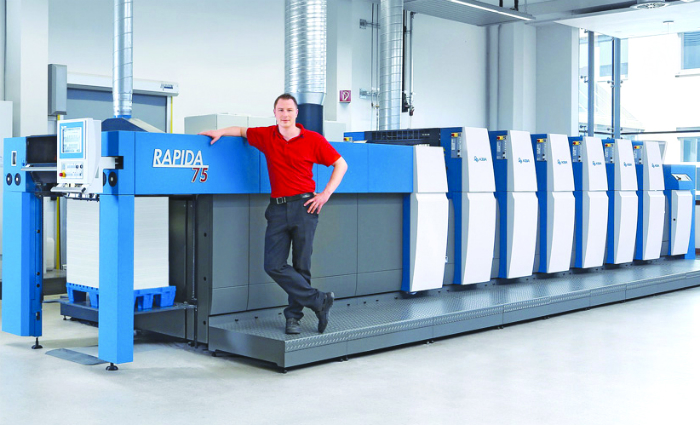
HEIDELBERG SPEEDMASTER XL 106
Heidelberg claims that the Speedmaster XL 106 offers users the highest productivity potential and configuration flexibility of any offset press available worldwide. Numerous production examples of installed machines in various markets show users achieving an output in printed sheets of up to 80 million impressions per annum.
Standard features such as the Preset Plus feeder and Preset Plus delivery are designed to boost productivity with a production speed of 18,000 sheets per hour in both straight printing and perfecting models. This allows for efficient output of longer runs, and automation features such as Autoplate Pro and Prinect Inpress control help users to reduce makeready times on the press.
The Speedmaster XL 106 has a wide range of model offerings designed to suit the individual requirements of commercial and packaging printers, as well as specialty and label printers.
Standard configurations include presses with and without water-based coating units. Packaging printers can choose from almost limitless configuration possibilities with Logistics for automatic pile transportation, Double (LYYL) , offline coating (LY) and UV models.
Commercial printers often opt for two configurations. The first is highly automated straight printing, and the second is long perfecting eight to 12 colour presses which can be optionally equipped with a coating unit for further embellishment effects.
Over the past several years numerous machines have been installed with the Heidelberg Drystar LE-UV technology (Low Energy UV). The Drystar LE UV system allows printers to use the recently developed high reactive ink series which uses low power for curing inks. This gives printers fast throughput of jobs, minimal use of spray powder and further effects such as drip-off coating and UV gloss effect of inks and coating on uncoated substrates.
Heidelberg Australia offers financing solutions for the Australian market, along with an aftersales service support structure that allows customers peace of mind in the investment. It includes all necessary training for the machines through its local service organisation.
Offerings include remote internet based monitoring and diagnostics, service contracts, training, consultancy and business analysis services.
SPECS AT A GLANCE:
Max sheet size: 750 x 1,060mm
Min sheet size: 340 x 480mm in straight, 410 x 480mm in perfecting
Max print output: 18,000sph (standard straight printing), 15,000sph (standard perfecting), 18,000sph (option perfecting)
Options: Prinect Inpress control, Colour Assistant Pro, programmable inking unit sequences for start-up waste reduction, digitally controlled ink zone system
KBA RAPIDA 106
KBA’s Rapida 106 is designed for very quick makereadies and high running speeds, says general manager, sheetfed presses, at KBA Australasia, Dave Lewis.
“It starts with the DriveTronic feeder, which is driven by independent motors instead of a mechanical drive from the press. This gives much smoother, vibration free running and a constant jerk-free feed pile lift. Then we have our SIS Sensoric Infeed System, which is a sidelayless infeed. This gives quicker makereadies and very accurate registration, and allows very high running speeds. KBA is the only press manufacturer that offers this technology,” he said.
The Rapida 106 has a top speed of 20,000 for a straight press, the fastest in the industry, and 18,000 for a perfecting press. KBA also offers its DriveTronic SPC Simultaneous Plate Change system with a full-time motor drive on the plate cylinder so there is no plate cylinder gear. This means that all plates are changed at the same time in 50 seconds while the blankets are washing, so in effect there is no plate changing time.
KBA also offers its PlateIdent system, which scans register marks on the plates and then brings the job into register before taking a pull, saving time and substrate. KBA also offers a Data Matrix Select option which reads QR codes on the plates when they are loaded and finds the job automatically on the KBA server, then downloads the job with no intervention from the operator, and then sets the press up automatically.
KBA’s Qualitronic ColorControl camera system reads densities and then makes density adjustments without having to scan a sheet. It can also detect defects through the same camera. Qualitronic PDF scans the printed image and then compares this to the original job PDF.
One of KBA’s latest additions is SRW Simultaneous Roller Washing, which allows the washing up and inking of units not being used while the press is in production. This is particularly useful for customers running lots of special colours. KBA also offers SFC Simultaneous Form Change on the coating units, which changes the coating plate while the press is in production.
KBA says it is the only press manufacturer with its own drying system, called VariDry. This includes IR/Hot air dryers as well as UV, including traditional UV as well as LED and HR UV. This means the dryer system is fully integrated into the press.
“With all these features, this makes the Rapida 106 the fastest and most productive press in its class,” said Dave Lewis.
SPECS AT A GLANCE:
Max sheet size: 740 x 1,060mm
Special format (straight): 750 x 1,060mm
Min sheet size: 340 x 480mm straight, 400 x 480mm perfecting
Print speed: 18,000sph (up to 10 units) 20,000sph (high speed package)
KOMORI LITHRONE G40 SERIES
Komori’s PR says that the company’s “green” rationale emphasises the coexistence of the environment, people and nature. A mutually beneficial balance among these three elements is the thinking behind Komori’s green concept which was behind the Lithrone G40’s development – a high-performance machine created with consideration for the environment and ecology. The “G” of the Lithrone G40 stands for green.
The development goals of the new Lithrone G40 presses were high-speed stability, improved print quality, suitability for short-run work, equipment reliability, environmental fitness and improved production efficiency. Equipped with the KHS-AI integrated control system, the Lithrone G40 meets the need for short job cycle time, competence with short runs, the capability to produce many different printed products, and cost reductions.
The H-UV Innovative Curing System is a powderless drying system jointly developed by Komori, ink makers and lamp manufacturers. It uses high-sensitivity ink and an ozone-less UV lamp. The quick drying ability of the system is the key to Komori’s OffsetOnDemand system.
The Lithrone G40 can be specified with the OffsetOnDemand system, which the company says will solve many of the issues currently facing printers.
OffsetOnDemand is the fusion of the KHS-AI integrated control system and the H-UV drying system. By shortening makeready time, cutting paper waste and reducing printing time while maintaining print quality and productivity, short-run competence and short job cycle times are achieved. The OffsetOnDemand solution is ideal for the Lithrone G40.
Included on the Lithrone G40 are technologies and systems that support OffsetOnDemand:
- Automation: Benderless fully automatic plate changing (Full- APC) reduces the number of processes and shortens makeready time.
- Standardisation: KHS-AI, the PDC-SX Spectral Print Density Control-SX and the PQA-S Print Quality Assessment system improve print quality and productivity.
- Innovation: Innovation H-UV Curing System and 20Matching (reaching density within 20 sheets of start-up printing) significantly shorten production time.
SPECS AT A GLANCE:
Number of colours: 2, 4, 5, 6, 7, 8
Max printing speed: 16,500 15,000 (7-8 colours)
Max sheet size: 720 × 1,030mm
Min sheet size: 360 × 520mm
Max printing area: 710 × 1,020mm
MANROLAND 700
The Roland 700 Evolution supersedes both the Roland 700 HS and the Roland 700 Direct Drive, on an all-new platform. Designed from the ground up and incorporating a sleek, futuristic look, the latest generation Roland 700 incorporates many new technological developments, aimed to give printers unprecedented levels of efficiency, productivity, operation and quality.
Among these new developments are a newly designed central console with touch-screen control, a new feeder pile transport that cuts down on waste, manroland’s new suction belt sheet handling technology for a more even pile contour, all-new dampening units in the press, bearings that significantly reduce vibration and, when used with the sophisticated software for practice-oriented roller washing cycles, further reduces downtime. The result is enhanced productivity and print quality alongside a further lowering of production costs.
The new manroland 700 Evolution has ergonomic operating user interface with touch-screens, Direct Drive technology, runs at 18,000sph, has optional 750 x 1,050mm sheet size for maximum multiple-up images. The feeder, delivery and dampening units are specially designed for high-speed production. Features include TripleFlow inking unit, intelligent speed compensation for inking and dampening units, and effective anti-ghosting solutions.
The company has solidly fixed the suction head to reduce vibration and wear while ensuring safer sheet separation and higher average printer speeds. The press also has completely redesigned cylinder-roller bearings, with separate bearings for radial and axial rotation for longer life and better print quality. New dampening units bring greater solidity and lessen vibrations during passing of the plate cylinder channel, meaning fewer stripes as well.
Software for practice-oriented roller washing cycles reduces downtime and makes for a more precise dosage of the dampening solution across the entire width, reducing the possibility of skewing the dampening dosage roller.
A three-phase AC motor makes for lower energy consumption with higher power output. Manroland says the machine has no need for wearing parts, carbon brushes or additional costs for part, helping it to further cut down on unproductive time, strengthen the market position of printers and raise its green credentials.
The Evolution also features a new chambered doctor blade system, which the company says will exceed expectations in the gloss effects it can produce. The system, with additional profile, aims to provide higher solidity over the width of the doctor blade, and a more even varnish application.
Manroland says that not only does it feature better absorption of vibrations from the Anilox roller and doctor blade caused by passing the coating form cylinder, it also results in fewer stripes, especially in combination with pigmented varnish.
New suction belt sheet brake technology offers higher printing speeds, with improved sheet alignment and tail edge stabilisation. This gives a more even pile contour and reduces the risk of misaligned sheets in the delivery pile.
SPECS AT A GLANCE:
Number of colours: 2, 4, 5, 6, 7, 8, 10, 12
Max printing speed: 18,000
Max sheet size: 750 × 1050mm
Max sheet size 3B: 780 x 1050mm
Paper size: 0.4mm-1mm
RYOBI V3000/920
Ryobi MHI recognised the changing market demand several years ago and has developed a range of press solutions that can ensure high quality print is delivered to customers as quickly as possible.
The full size B1 V3000 105cm press can be configured as a straight press, a convertible perfecting press or tandem perfecting press which utilises a translink unit enabling sheets to be printed on both sides using the same grip edge and without the need to turn the sheet.
Ryobi’s best selling, and economical, A1 92cm size press offers 16-page A4 sections
Ryobi MHI can offer several options which result in both time and money savings. By incorporating the Ryobi MHI Smart Makeready function the number of sheets used and the time taken for makereadies is significantly reduced. Blanket cleaning, plate changing, preset inking and test printing can be performed within this feature.
The new Smart RPC plate changing system changes plates automatically and simultaneously reduces the time taken to change any number of plates from two to 12 in approximately 75 seconds. Colour management systems continuously monitor and check imperfections, to improve the overall quality of the printed sheets.
No reduction in press speed, whether printing in straight or perfecting mode, is available.
LED UV enables instant drying, low power usage, the elimination of spray powder, no ozone, the ability to print on plastic, an instant on/off, and no generated heat are just some of the benefits available by the use of this feature. Value added inline features such as foiling, holographic casting or chemical embossing can also be incorporated.
All of Ryobi MHI’s presses can be configured to the customer’s requirements.
Options such as perfecting, coating (aqueous or UV), full automation or semi automation, the ability to handle a wide variety of stock from thin paper to thick board or rigid plastics are available.
Cyber offers full training on all its installations. The company has three factory trained demonstrators and 20 factory trained engineers across Australia, as well as representatives in all states.
SPECS AT A GLANCE:
Ryobi V3000
Max printing speed: 16,200sph
Max sheet size: 740 x 1,020mm or 750 x 1,050mm
Min sheet size: 360 x 540mm
Max image area: 730 x 1,020mm or 740 x 1,050mm
Ryobi 920
Max printing speed: 16,200sph
Max sheet size: 920 x 640mm
Min sheet size: 410 x 290mm
Max image area: 900 x 615mm
Comment below to have your say on this story.
If you have a news story or tip-off, get in touch at editorial@sprinter.com.au.
Sign up to the Sprinter newsletter