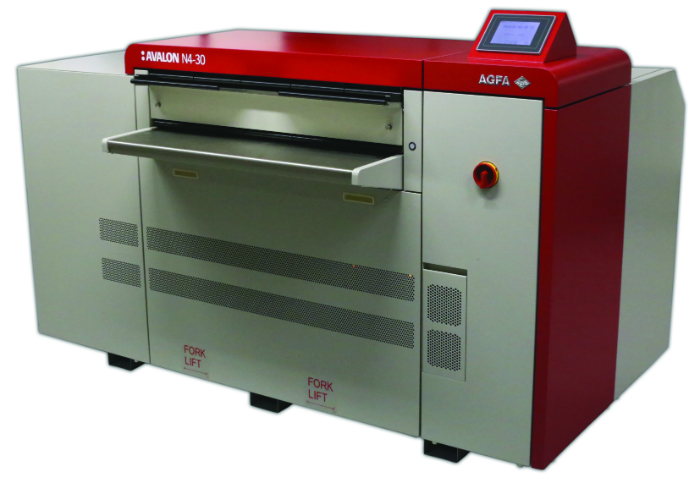
Platesetters
Agfa Avalon N4
The Agfa Avalon N4 thermal CtP system offers the automation and imaging capabilities of larger devices in a compact format. It handles plates up to 830 x 660mm, with a maximum throughput level up to 33 plates per hour.
The Avalon N4 brings today’s commercial and packaging printers the high-quality digital plates they need to stay competitive. The range consists of the productive Avalon N4-30 XT, the Avalon N4-30 S, and the entry-level Avalon N4-30 E. Printers can upgrade any time from the E model to the S model.
Each model comes with an optional inline punching system and standard Ethernet connection, providing direct interfacing with the Apogee workflow. The N4-30 AL-S and N4-30 AL-M plate loaders offer convenience and automation.
Agfa Graphics offers a broad array of services, from product installations and systems integrations to expert training and continuous improvement programs. Its commitment is to assist customers, ensuring they can maintain peak performance and cater to demands of their customers’ needs. Service is a critical component of Agfa’s total solutions commitment.
Specs at a glance:
Laser technology: 830nm thermal
Imaging system: 16, 32, 64 channel fibre coupled
Max image area: 830 636mm
Recording system: External drum
Resolution: 1,200 – 2,400dpi
Throughput: 11 – 33 plates/hr
Loading: manual and automatic with Autoloader
Online processor: Yes
CRON 3-in-1 CTP
Supplied by Currie Group and previewed at Graph Expo the new CRON automated 3-in-1 CTP combines plate cassette input with precision imaging, punching and transport. The company says this provides a low-cost easy-to-use and compact unit which is easy to maintain.
The exposure unit is based on CRON’s magnetic linear drive platform, which the company says provides fault free imaging across a wide range of resolutions, with registration accuracy up to 0.01mm and a tonal range of 1-99 per cent, in either conventional or stochastic screening.
The 3-in-1 (H Series) solution in the 660mm format is already available, with larger formats up to 1168mm scheduled for release this year. CRON has several different types of CTP products, including silver plate CTP, violet CTP and thermal CTP.
The CRON Thermal Series comes in several formats, including 26”, 36”, 46” and 72”. They image at up to 3600dpi resolution and come with a V shaped guide rail, an exclusive three point loading system with non-contact sensor, a vibration free dual balanced drum, and a patented auto clamp closing and drum vacuum technology. Plate output ranges from 77 an hour for the 26” version to 20 an hour for the 72” model.
CRON produces an Autoloader to work with its CTP units, which comes in two versions and can handle up to 200 plates an hour in single size version and 150 plates an hour in the three cassette multiple size version. The company also supplies an automated Chemistry Regulation Device to ensure the stability of processing fluid automatically calculates and replenishes. CRON also has an optional Online Punch Bridge which gives a punch accuracy of 0.01mm.
Currie Group has been the CRON reseller since 2012, and has fully trained factory engineers in Australia to support its national distribution.
Specs at a glance:
Laser wavelength: 830nm
Laser type: IR laser
Plate: Thermal chem-free
Max plate size: 925 x 675mm
Min plate size: 340 x 240mm
Resolutions: 1,200; 1,500; 1,800; 2,400; 2,540; 2,800; 3,000; 3,600dpi
Production capacities: 23 – 77 plates/hr
Plate thickness: 0.15–0.03mm
Esko CDI Crystal 5080
The CDI (Cyrel Digital Imager) offers results that before were only achievable in offset or gravure. There is a CDI for every need from narrow web label printing to flexible packaging and wide-format corrugated printing, one-colour printed corrugated boxes to sophisticated multi-colour packaging and even security printing.
New to the Esko portfolio is the CDI Crystal 5080 XPS flexo platemaking system, designed to address the overriding market pressures driven by shorter run lengths and a growing number of SKUs. It requires fast plate turnaround to address this increasing demand for product versioning, and the CDI Crystal 5080 XPS delivers that. It also brings higher quality to flexo, delivering better consistency, and is simple to use for operators at all skill levels.
The CDI Crystal 5080 flexo platemaking system exposes both sides of a flexo plate using UV LED heads. It also combines imaging and exposing into the same compact footprint. This results in 50 per cent fewer manual steps, 30 per cent faster access to plates and 73 per cent less required operator time.
Along with Full HD Flexo will be Esko’s Digital Flexo Suite (DFS), offering significant cost savings through the automation of flexo plate production. Label ‘one-ups’ are nested economically on the plate to reduce plate and substrate waste. The optimised plate and the corresponding cutting layout are simultaneously sent to a CDI and Kongsberg table. The plate is staggered cut to enable flexo cylinders to print continuous labels on the press. The Kongsberg X20 offers the flexibility of upgrading to add more cutting, creasing and milling tools as business needs develop.
Esko has a local team in the Australian region, providing full training and service locally for all products and solutions.
Fujifilm PTR 8900
Fujifilm supplies and supports the Screen high productivity B1+ thermal PTR8900, which is available in a number of versions, capable of producing up to 70 press-ready B1 plates (PlateRite 8900Z) per hour in manual, semi automatic or fully automatic configurations.
With a maximum plate size of 1165 mm x 950 mm x 0.3 mm the PlateRite 8900 is compatible with most B1 and B2 presses. In addition, as standard the smallest size of 304 mm x 305 mm x 0.15mm further extends the systems flexibility (other plate size and gauge options are also available). Integrated punching enables the production of press-ready plates for most commercial sheet-fed presses. Custom punches are available, as is a range of offline transfer punches to meet all formats.
Three configurations exist with the PlateRite 8900. In its most basic form, the platesetter will stand alone requiring both manual load and unload. A low cost upgrade can provide automatic unloading to either an online processor or plate stacker, with a reduction in manual intervention. If full automation is required, the 100 plate single cassette autoloader (one plate size at any time) will significantly improve workflow efficiencies enabling unattended operation for an entire shift. Should your business dictate that several plate sizes are to be available at any one time, then the multi-cassette autoloader will meet your needs. With up to five cassettes online, the system can automatically select from up to five plate sizes.
No safelight requirements mean the machine is easy to use, service and maintain.
Used in conjunction with Fujifilm’s thermal CTP plates, the company says printers can confidently work in daylight for extended periods. In the event of a laser diode failure, the GLV head enables continued production. Unlike other GLV head designs, with the PlateRite 8900 component replacement is possible in the field without having to swap the complete head assembly.
The company says PlateRite 8900 achieves optimal productivity with Fujifilm thermal CTP plates. The high sensitivity of the plates allows the platesetter to image at its fastest speed.
Specs at a glance:
Imaging: Thermal
Max plate size: 1165 x 950mm
Recording system: External drum
Resolution: 1200lpi-4000lpi
Throughput: Up to 70 plates an hour
Loading: Manual, semi or fully auto
Heidelberg Suprasetter A75
Multiple factors make Heidelberg’s Suprasetter range a market leader, including its plug and play functionality, ease of operation and its pre-installation.
The laser head is designed by Heidelberg engineers and offers a long life with a warranty of up to seven years. The machines also feature inbuilt temperature control to ensure a stable environment, which has made the Suprasetter popular in rural locations and tropical climates.
The Suprasetter units have a very small footprint, making them accessible technology for all sized businesses, and their low energy consumption meets environmental concerns and reduces operational costs. Every Suprasetter is delivered with a CO2 neutral certificate confirming that Heidelberg has offset the carbon used in manufacture of the unit.
Suprasetters are upgradable in the field so those who start with a basic model can upgrade from manual to automated processes and also increase speed. The Suprasetter allows unattended operation and repeat jobs to be programmed, further streamlining workflow.
Suprasetter CtP devices require minimum maintenance as the units self-check each day when they are turned on. For the rare occasions when there is a problem, Heidelberg’s engineers can remotely access the machine to make a diagnosis, ensuring minimum downtime.
The most popular model in the range is the Suprasetter A75, which is ideally suited to the A2/B2 market and comes in various configurations including Automatic Top Loader and Dual Top Loader for high volumes. The Suprasetter A75 produces plates at 2,540dpi up to 5,080dpi for special applications such as stamps and security printing. The A75 runs on low power consumption using only five watts on standby and 550 watts on average when imaging.
The Suprasetter family is competitively priced and Heidelberg provides options for financing. With its high productivity and proven reliability the Suprasetter is a secure investment engineered to Heidelberg Germany’s exacting standards.
Specs at a glance:
Operating technology: thermal
Min plate format: 240 × 240mm
Max plate format: 676 × 760mm
Max imaging area: 1,413 × 1,460mm
Max throughput: 22 plates/hr
Resolution: 2,400dpi, 2,540dpi, optional 5,080dpi
Kodak Trendsetter
Q 400/800 W
At drupa, Kodak launched an ultra-high speed imaging technology – the new W speed – to the Trendsetter Q400 and Q800 Platesetters. The new imaging technology significantly increases throughput to 68 plates per hour on an 8-up plate and 75 plates per hour on a 4-up plate imaging Kodak Sonora XP plates, creating what Kodak says is the world’s fastest process-free CTP. This configuration will deliver a more efficient, compact and faster plate-making process – all without chemistry or processor use.
Kodak has also responded to a growing demand for higher resolution imaging, mostly triggered by security, lenticular and high resolution art printing applications, by introducing a new 4,800 / 5,080 dpi resolution option to its Trendsetter platesetter ranges. This option can be used to image small features with great details like background patterns or wavy lines of variable width, and for micro printing indiscernible to the naked eye.
A host of new automation options to complement the Kodak Trendsetter and Kodak Achieve CTP families were launched at drupa. These include the new Multi-Cassette Unit (MCU) that features online access to four cassettes of 120 plates each, a total of 480 plates can be imaged without manual intervention.
The Trendsetter Q400/Q800 Platesetters feature a fully integrated, in-line punch system option with accurate three-point registration, helping eliminate costly errors by automating the punch process. The punch system option allows for up to 10 customised punch heads once the system is added.
Specs at a glance
Resolution: 2400dpi, 4,800dpi, 5080dpi
Plate size: 1,030 x 800 mm
Cassettes: 480 plates max
Speed: 68 plates an hour 8-up, 75 plates an hour 4-up
Screen platerite HD8900N
Screen GP (Graphic Precision) is the acknowledged leader in worldwide CtP hardware sales and also manufactures thermal platesetters for three of the four major plate manufacturers. The Kyoto, Japan, headquartered company has a fine tradition in engineering precision imaging technologies for both the graphic arts and the semiconductor industries.
The latest addition to Screen GP’s range is the new high-resolution B1 platesetter, the PlateRite HD8900N, available in three speed configurations.
The 8900N – Z achieves a maximum productivity of 70 plates per hour (1,030 x 800mm @ 2,400dpi) using two laser diodes (60W) and a 1,024-channel optically improved GLV (Grating Light Valve). The other two speed variations (‘S’ and ‘E’) produce 48 or 36pph.
The HD8900 S and E models can be factory optioned for ultra-high resolution of 4,000dpi or 4,800dpi (for 3D lenticular printing). At 4,000dpi, the HD8900N can resolve up to 700lpi. For FM/stochastic screening the dot resolution can be tuned to RandotX 10 (10 microns). A new STEP mode corrects the issue of pixel shift caused by spiral exposure mode.
Peter Scott, Screen GP Australia managing director, said, “The HD8900N is easily the highest quality CtP device we have ever offered. With the high-resolution options and the right plate and processing environment, offset print quality can reach new levels. If sheer productivity is called for, the Z model at 70 B1 plates per hour – or 80 B2pph – is offered.”
The PlateRite HD8900N features energy saving benefits both in production and while idling. A factory-only option to deliver plates to the front of the machine instead of the rear is available where space restrictions are a consideration. The familiar options for automated plate loading remain unchanged, with the single cassette autoloader or the multi-cassette option that can take up to 500 plates of differing sizes and load them without manual operator intervention. Screen CTP systems are also supplied by Fujifim and WRH Global.
Specs at a glance:
Recording system: External drum
Light source: 512 or 1,024 channel laser diode
Max plate size: 1,165 x 950mm
Min plate size: 304 x 305mm
Plate: Thermal aluminium
Resolution: 1,200, 2,400, 2,438, 2,540, 4,000dpi (4,000dpi only available when high res option is selected)
Productivity: 36-70 plates/hr (model dependent)
Options: Plate transport system to connect with plate processor, various printing press punches, support for 0.4mm thickness, high resolution (4,000dpi support), lenticular printing plate output, air filter unit (AF-180N), upgrade to Z or S specifications
Plates
Agfa Energy Elite Eco
Agfa’s Energy Elite Eco is a robust no-bake thermal printing plate for high-end, high-performance commercial, packaging and UV printing. It offers a run length of up to 600,000 prints (up to 150,000 copies when using UV ink), ensuring maximum productivity for a variety of different applications and press conditions.
Specially designed to be compatible with the latest screening technologies of 340lpi Sublima and FM10, Energy Elite Eco creates durable images at 1-99% dot resolution, without dot loss.
The Energy Elite Eco technology enables a wide press latitude in sheetfed, heatset and UV packaging printing, ensuring excellent lithographic performance, fast restarts, low dampening levels, fast roll-up and a stable ink-water balance Energy Elite Eco fits into the Agfa Graphics ECO³ framework, designed with a dedication to ecology, economy, and extra convenience. Combined with standard processors, the printing plate effects a 20 per cent decrease in waste production and chemicals used. It also allows for a longer bath life, less frequent and easier processor maintenance. Processors can be cleaned using standard tap water.
By combining the Energy Elite Eco plate with the Arkana smart processing technology, the full benefits of its ECO³ features can be achieved. By deploying Agfa Graphics’ patented gum cascade system, Arkana no longer requires water for plate rinsing. Instead, the cascaded gum has a dual function, cleaning the plate and protecting the plate with a finishing layer.
Specs at a glance:
Plate type: Positive, digital thermal offset
Substrate: grained and anodised aluminium
Spectral sensitivity: 830nm
Plate sizes: 450 x 480mm to 2,080 x 1,590mm
Resolution: ABS: 1-99% at 200 lpi at 2400 dpi; Sublima: 1-99% at 340lpi at 2,400dpi;
FM: 10μm
Max run length: 600,000 (UV: 150,000).
Fujifilm Superia ZP
The processless Superia ZP plate (formerly PRO-T3), represents the fastest route from platesetter to press as the plate is simply imaged and mounted directly on-press, and has the same sensitivity as any other high performance plate.
The latest version of the processless Superia ZP plate represents Fujifilm’s most advanced printing plate to date. It features a number of technologies designed to optimise performance, including a special new Multi Grain (MGV) technology. This is a micro-graining process applied to the surface of the aluminium and guarantees the widest possible latitude in ink/water balance on-press. Another advance is a multi-layer coating, unique to Fujifilm, which provides different functionalities within ultra-thin layers.
Fine Particle Dispersion (FPD) technology helps improve the softening of the non-image area and an undercoat layer incorporating Rapid Stable Start-up (RSS) technology speeds up the removal of the plate coating by the ink/fount and onto the paper substrate.
Fujifilm gives a percentage of the sales of Superia ZP plates in Europe, the Middle East and Africa to the WaterAid charity.
Specs at a glance:
Laser: Thermal 830nm
Resolution: 200lpi (1-99%); 20 micron FM screening
Run length: 100,000.
Safelight environment: White 400 lux for 2 hours for latent image visibility
Heidelberg Fujifilm ZAC
To reduce the use of chemistry and water when processing plates and minimise maintenance requirements, Heidelberg’s offering of Fujifilm low-chemistry LH-PJE and LH-PLE plates and the award winning Fujifilm intelligent ZAC processing system allows printers to meet their environmental concerns and reduce maintenance at the same time.
The Fujifilm ZAC system provides optimised processing quality by using intelligent developer replenishment. This results in a significant reduction in the volume of chemistry and water used, which helps to reduce printers’ environmental footprint.
The Fujifilm ZAC processor can achieve up to 80 per cent reductions in chemistry by identifying only the areas on the plate that actually need processing, and by constantly measuring the bath conductivity. The intelligence of the ZAC system means there is hardly any need for operator intervention. Plates are produced consistently, without effort and quality is maintained. The ZAC/Fujifilm plate combination is the closest to processless chemistry reduction with the benefit of a processed plate.
Maintenance requirements are also slashed due to the intelligent replenishment system that monitors developing conditions and accurately calculates the required volume of replenisher. With the Fujifilm ZAC system, bath life can be extended up to four months or 15,000m2, maintaining dot structure and stability. This means maintenance is reduced to less than half the time of many other processors, and may only need to be carried out four times a year. This is a massive saving in labour and wasted time for businesses trying to achieve more with fewer staff.
Heidelberg has the portfolio of plates to suit printers’ needs in thermal or violet, processless or processed. In addition to the ZAC system, Heidelberg also offers the complete range of Fujifilm’s new Superia thermal and violet CtP plate technologies, which includes the LP-NV2 processed plate technology, the Pro-V low-chemistry option which uses only a finishing solution instead of the traditional developer or replenisher for violet systems, and the Fujifilm processless thermal Superia ZP.
ibf direct
Distributed by WRH Global Australia, the soon to be released IBF DirectT offers the best of both DOP (Develop on Press) and conventional thermal CtP plate technology.
After exposure, the IBF Direct T can be immediately put on the press and commence printing.
The emulsion is softened by contact with the rollers from the dampening system, and the blanket removes this emulsion from the plate surface, processing it. This residue is then carried by the first sheets of paper, mixed with ink.
With a 6.2 Delta E latent image, it is possible to read text and see the image while adjusting the inking system accordingly. It has a resolution of 1-99% at 200lpi with a run length of up to 100,000 sheets, depending on substrates.
Specs at a glance:
Imagaing: Thermal
Resolution: 200lpi (1-99%)
Run length: 100,000
Kodak Sonora XP
The Sonora XP Process Free Plate from Kodak is a thermal plate that requires no processing equipment or chemistry. It uses Kodak’s press ready technology to enable a printer to go directly from platesetter to press with no intermediary processing or clean out step. The plate offers fast imaging speeds with laser energy required of 150 mJ/cm2 on Kodak Squarespot Imaging Devices, so printers can take advantage of the maximum throughput capability of their platesetter in most cases.
The plate is capable of run lengths up to 200,000 impressions on heatset and commercial coldset web presses, 100,000 impressions on sheetfed presses, 50,000 impressions for non-UV offset packaging applications and 10,000 impressions for UV-ink applications. The plates also offer high-quality 20-micron FM screening capability on Kodak Squarespot Imaging Devices and AM screening of 1-99 per cent at 200 lpi.
Kodak’s press ready technology uses the basic principles, mechanics and components of lithographic printing to clean out the plate. During the startup of the press, the fountain solution prepares the un-imaged coating to be physically removed from the plate by the tack and shear of the ink. The coating is transferred from the plate to the blanket and then onto the makeready sheets within the first few sheets.
With Sonora XP Plates, in almost all cases, a printer’s current press setups, sequences, inks, fountain solutions, and blankets can be used successfully. Press ready technology also works with integrated and non-integrated conventional and continuous dampening systems and for printers with automatic startup sequences.
Specs at a glance:
Laser: Thermal negative 800 – 850 nm
Resolution: 200lpi (1-99%)
Run length: 200,000 web 100,000 sheetfed, 50,000 offset packaging, 10,000 UV
Safelight environment: Up to one hour under white light
Xingraphics Primus Plus
The new Primus Plus positive thermal CtP plate from Xingraphics is a hybrid plate, and is distributed in Australia by WRH Global Australia. It provides both environmental and economic benefits with a reduction in water requirements and a corresponding reduction in ink.
According to the company, installations have achieved water reduction by 20-30 per cent and
reduced ink coverage by 5-20 per cent in offset printing. Printing with less water ensures faster drying times, fewer water-on-paper related problems on sheetfed presses, and can also lead to a reduction in paper breaks on web presses.
Xingraphics says all these factors further assist the bottom line through a reduction in energy consumption.
Specs at a glance:
Type: Thermal positive
Substrate: Grained and anodised alumium
Max width: 1,480mm
Spectral sensitivity: 830nm
Resolution: 450lpi 1-99%)
Run lengths: 250,000 unbaked; 1,000,000 post-baked
UV ink compatible: When post-baked
Comment below to have your say on this story.
If you have a news story or tip-off, get in touch at editorial@sprinter.com.au.
Sign up to the Sprinter newsletter