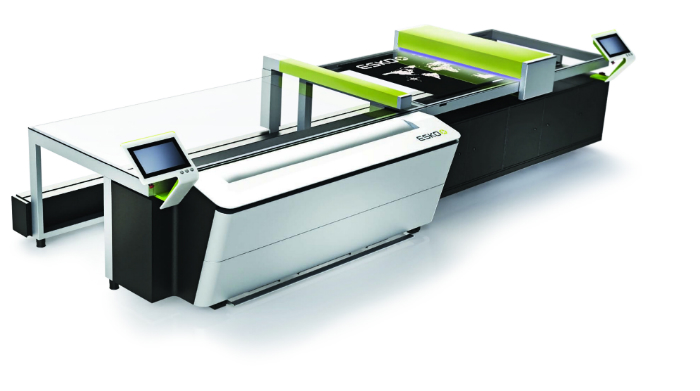
A lot of the profits in commercial printing are made or lost before the job goes to press. Prepress technology has advanced in leaps and bounds, particularly in plates. At last year’s drupa, the major CTP developers all launched new models. But how are these developments helping printers?
What is the latest in the laser technology? How is the plate handling enhancing productivity, particularly in the time-critical area of loading on to the press? Are printers embracing parallel digital workflows with their CTP production lines?
And what about processless plates? We have heard a lot about them for some years, but are the CTP developers enabling or hindering this technology?
Heidelberg and Fujifilm
Heidelberg A/NZ managing director Richard Timson sees a lot of activity in core commercial printing, where the search is always on for the latest, more efficient output device. Low labour intensity across a number of serial processes is the aim, he finds, citing ‘fully automatic lines that feed the plates off the pallet, image the plate, then automatically punch and bend and deliver to the stacker, ready for the press operators to collect – all without a single person involved in the process’.
“As packaging printers make very few plates and they have so much repeat work, they re-use plates, so most packaging printers require very low technology,” he reflects.
Under Heidelberg’s landmark 2014 partnership with Fujifilm, in which Heidelberg offers Fujifilm plates and (switching from Kodak, which is now going direct to the market), Timson says the vendor’s plates range is split between thermal plates and chemistry-free plates, with thermal maintaining an edge on violet these days, particularly for faster, higher-definition work and for advances in automated plate loading.
Automation is the key today, notes Timson. “Depending on the needs of the customer, Heidelberg offers several plate loading and unloading options for the Heidelberg presses.”
Autoplate is a semi-automatic plate loading system, and Autoplate Plus is a fully automated plate unloading and loading system, he states. “At drupa 2016, Heidelberg displayed the latest fully automated push-to-stop technology. This is a combination of software intelligence and Autoplate Plus, and gives an automation to the point that only the plates need to be made available at the press and when it comes to a job change, everything happens automatically.”
Timson says Heidelberg’s laser head offers reliable, proprietary Heidelberg thermal delivery; a screen frequency up to 160l/cm (400lpi) as standard, not optional; FM screening capability as standard; minimal maintenance cost due to miniaturisation; easy setup of plates due to the very high depth of focus, and Heidelberg’s Intelligent Diode System (IDS) for uninterrupted production in case of failures.
With imaging of 830nm sensitive thermal aluminium plates, there are the advantages of full daylight loading and handling; the high availability of aluminium plates from many plate manufacturers, and no limit to one plate type or manufacturer, he says.
Many print providers are now integrating their CTP workflows with production to and from their digital output devices, and this is where Prinect, Heidelberg’s proprietary workflow, can make a significant difference, explains Timson. “With Prinect, Heidelberg offers a fully integrated hybrid workflow, addressing all output devices such as CTP, proofing systems and digital printing machines.”
The debate about the merits or otherwise of processless plates has been going for years – and while many printers have told ProPrint they have been more than happy to discard their chemical plate development lines, the value of fully processless plates remains a matter of conjecture.
Says Timson: “Processless, or process-free plates are part of the standard offering from Heidelberg in combination with a CTP system. In most cases, these plates are actually sold with a new CTP nowadays. Unless the customer has special requirements in terms of high run-length (more than 100,000 impressions) or very high resolution — over 200lpi or FM screening — there is absolutely no reason not to consider a process-free plate technology.”
Heidelberg offers a comprehensive plates portfolio – in thermal or violet, processless or processed, he says. A keystone feature of Heidelberg’s plate offerings are the Fujifilm low-chemistry LH-PJE and LH-PLE plates and Fujifilm’s intelligent ZAC processing system, which is low-maintenance and environmentally friendly.
“This system provides optimised processing quality by using intelligent developer replenishment, resulting in a significant reduction in the volume of chemistry and water used, which helps you to reduce your environmental footprint. The Fujifilm ZAC processor can achieve up to an 80 per cent reduction in chemistry by identifying only the areas on the plate that actually need processing and by constantly measuring the bath conductivity. The intelligence of the ZAC system means there is hardly any need for operator intervention,” explains Timson.
In addition to the ZAC system, Heidelberg also offers the complete range of Fujifilm’s new Superia thermal and violet CTP plate technologies that includes the LP-NV2 processed plate technology; the Pro-V low-chemistry option, which uses only a finishing solution instead of the traditional developer or replenisher for violet systems; and the Fujifilm processless thermal PRO-T3.
Among Heidelberg’s platesetter range, the most popular model is the Suprasetter A75, which is ideally suited to the A2/B2 market and comes in various configurations including Automatic Top Loader and Dual Top Loader for high volumes. This setter produces plates at 2540dpi up to 5080dpi for special applications such as stamps and security printing. The A75 runs on low power consumption, using only five watts on standby and 550 watts on average, when imaging.
And at last year’s drupa, Heidelberg showed a Suprasetter 106 with an output of 42 plates per hour. This system was configured with an auto pallet-loader and a dual cassette loader for three plate formats, and a total plate capacity of 1,400 plates at the same time. In addition to the loaders, it also had an inline plate bending system.
Agfa Graphics
As of last year’s drupa Agfa now has the Avalon N8-90 CTP in its family of thermal computer-to-plate systems, and the new Energy Elite Eco printing plate. With a best-in-class run length for no-bake positive thermal plates, the Energy Elite plate is both mechanically and chemically compatible with today’s needs in sheetfed and heatset applications, says Mark Brindley, managing director of Agfa Oceania.
The N8 setters are compatible with all thermal plates from Agfa Graphics, for what the European prepress giant describes as “an unparallelled throughput speed of 70 plates per hour”.
Meanwhile, the Arkana smart plate processor, built on Agfa’s ECO2 framework, has proved a hit, notes Brindley. Using Agfa’s gum cascade system in which the gum both cleans the plate and protects it with a finishing layer, Arkana removes water for plate rinsing from the process, producing up to 50 per cent less collectable waste compared to other systems. Minimal chemistry usage and maintenance allows Arkana users to further reduce their CO2 footprint.
On the violet side, Agfa announced major advances in chemistry-free innovations for newspaper printing at drupa 2016, with its Attiro VHS clean-out unit on its N95-VCF violet chemistry-free plates.
Agfa also unveiled the new Azura TE processless plate, which is based on Agfa’s ThermoFuse technology and takes printing plate developments yet one step further with imaging off-press, and cleaning on-press.
“CTP compatibility to digital is driven by Agfa’s Apogee Workflow, which has modules to drive CTP, proofing, wide format and digital devices,” says Brindley.
Kodak
Kodak is focused on adding more automation to its Achieve and Trendsetter CTP lines, says David Paterson, Kodak’s regional business manager, Output Devices, Asia Pacific.
“We have always had first-class automation with our Magnus series of CTPs, and we are now expanding this to make it an option on our biggest selling CTP units. At drupa, we showed a Trendsetter with multi-cassette unit capability which we will release in 2017 and we also showed an Achieve CTP with single cassette unit capability running our Sonora process-free plate. Our single cassette unit option has been available and sold since drupa. Both configurations were also showing our inline punch option. So we have a completely automated CTP/Plate solution offering automatic slip-sheet removal, no processing required and the plate is punched and ready to go straight onto the press.”
As commercial printers try to broaden their activities, Paterson sees an uptick in demand for hybrid solutions. “By hybrid we mean offset and packaging, offset and newspaper, and so on. Fortunately our Kodak CTP units have a lot of these capabilities built in. So one CTP device can give you many hybrid and market differentiation options.”
Kodak has developed two laser head technologies, he notes. Its Trendsetter and Magnus CTPs have square-spot imaging, while its Achieve CTP has TH5 technology geared to the entry-level market. “It also provides some unique environmental benefits, with our complete Achieve CTP unit, including automation and punching, only using up to 400 watts of power, making it the most environmental and cost effective thermal CTP in the market.”
CTP automation is a major focus for Kodak. Says Paterson: “We have many CTP configuration options to meet any customer’s requirements. We can start off with an entry-level customer who has the requirements of a semi-automatic Achieve CTP device, right up to a Magnus VLF CTP with auto pallet loading capabilities, and everything in between. This includes newspaper and flexo packaging solutions, all also offering various plates-per-hour requirements to meet these differing market needs. The addition of our inline punch option to our Achieve and Trendsetter CTP further enables a complete automated solution.”
“Our Kodak Prinergy workflow allows you to streamline and manage all of these differing environments from one workflow solution. Offering digital press management, packaging tools, and so on, and integration upstream, such as MIS integration, with web portal solutions to extend your geographical reach,” he adds.
Meanwhile, Robert Mollee, Kodak’s business manager, Print Systems Division, A/NZ, flags a new development in 2017. The Kodak Sonora UV process-free plate will bring process-free platemaking — completely eliminating the plate processing step, including all related water and chemistry — to UV printing. “Printers already use Sonora XP plates for short-run UV applications, but Sonora UV plates will expand the possibilities for process-free platemaking with UV.”
Esko
Esko has moved forward into the Australian market with significant new platemaking technologies introduced at drupa last year, which together are called CDI Crystal XPS, explains Scott Thompson, Esko’s head of inside sales, Oceania. The new CDI Crystal XPS is a flexo plate imaging system comprised of two parts. One is an updated version of the traditional CDI ablation imaging system, with updates. The other an innovative plate exposure unit.
The CDI Crystal imaging system’s improved ergonomics and user interface include an arm that can automatically take a plate and move it from the top of the imager’s glass surface into the imager. When the plate is imaged, it is returned to the glass surface. Meanwhile, XPS Crystal, fitting right next to the imager, is a digitally controlled LED UV exposure unit, providing both main and back exposure, supporting all ablative flexo plates. Plates are placed onto the glass surface, where very accurate back and main exposures — by patented LED UV light technology that, unlike light bulbs, allows very precise control — are conducted simultaneously. Nothing else is required from the operator.
“Together, the integrated automated system automatically loads a plate, images a plate, transfers the plate to the exposure unit and provides the correct front and back exposures, while the imager concurrently images the next flexo plate. The parallel imaging and exposures are critical to improved productivity in time-pressured environments. It cuts the number of manual handling steps in half. Making flexo plates finally becomes a coordinated, linear process,” says Thompson.
The Esko HD optics technology uses high resolution, 4000dpi imaging to produce high line flexo screens with smooth gradients to zero, solids, and exceptional flesh tones. “Of course, it also provides fine line work and text, important for packaging. In addition, the unique Crystal XPS exposure unit uses UV LED to deliver extremely consistent exposure after imaging. This is not possible with fluorescent light sources that are inconsistent throughout a plate, and also degrade over time.”
Thompson says offset and gravure printing quality has always been somewhat of a Holy Grail for flexo. “With HD Flexo and Full HD Flexo, the gap closed. And, with the introduction of the CDI XPS Crystal system, flexo can deliver extraordinary consistency, vibrant colours and increased print quality. Digital LED UV plate exposure ensures greater consistency in plate production and in printing. Flexo printing can now compete with offset for quality labels and with gravure printing for flexible packaging. In fact, with more efficient makereadies, it can challenge the upper limits of digital print for labels and folded cartons.”
Currie Group
Currie Group offers its comprehensive range of Agfa plates, including the ECO2 series, and the Azura TE processless plate, which can be bundled with its Cron H-series CTP setters.
Bernie Robinson, Currie Group managing director, explains that Cron’s H-series thermal plate setter range, demonstrated at last year’s drupa, is a fully automated three-in-one integrated imaging system which features compact design, ease of use, low cost of ownership, easy maintenance, and outstanding dot quality, with a 1-99 per cent tonal range.
The H-series comes with auto plate loading and paper removal. The loader can be retro-upgraded to a 500-sheet capacity or a multi-cassette loader. The 4-up CTP can image plate sizes down to 240x320mm. Built-in punching enables precision registration and avoids any damage to the high-speed drum. Available as a 26-inch unit, it will soon be scalable to VLF.
Robinson saw the latest H-series setters up close at drupa and also with the dealer. Versatility of speeds, governed by the number of laser diodes, is a key feature. “It’s an exciting, efficient and smart product, and you can have various speeds, from 32 up to 128 diodes installed in the machine. With 32 diodes, you’re talking production speeds of 28 plates per hour, up to 66 plates per hour for a 128. The range goes from a Series 26, which is 670x560mm plate size, to a Series 72, which is 1850x1425mm plate size.”
Manual loading is a thing of the past, explains Robinson, and with auto loading, capacities range from 100-500, he says. The most popular option is a loader with three different plate sizes, with the software controlling which rack to draw plates from, depending on the required plate size. “You don’t have an operator in that room anymore. The machine’s driven by the front-end software. You make sure it’s loaded first thing in the morning, then just take the plates out as needed during the day.”
The setters feature online washout units, with an option to go direct to the press from the CTP unit. He says: “Most of our customers prefer to retain the washout unit, rather than introduce chemicals into the fountain solution on the press. It’s a more environmentally friendly approach.”
Currie Group still offers its ECRM violet setters, but as Robinson attests, “thermal is taking the lead in the commercial sphere – plate prices in thermal have come down and can represent even greater value than violet plates.
“Plate per sqm price is under $10, that is standard these days. You have faster, more compact CTP units,” he observes.
Currie Group has coupled the Cron series – as well as its ECRM setters — with its ElecRoc workflow, aimed at commercial printers, which is sourced from South Korean developer Founder Electronics. ElecRoc is a scalable workflow solution that integrates the latest core technologies from Founder. It provides the functionality required for features such as job management, integrated JDF/PDF creation, preflight, trapping, imposition, PDF colour management, CIP4 ink control, and remote proofing.
Screen
Post-drupa 2016, Screen Australia is offering its thermal CTP solutions in the form of its new PlateRite 4600E, S and Z models for optimal versatility in plate production targeting 4-page and 2-page presses. Screen is marketing the PlateRite 4300S as a high-speed model that can comfortably and consistently output up to 33 plates per hour and the 4600S at 21 plates per hour when working with 724x615mm plates at 2400dpi.
The 4600E is an affordable entry-level solution that offers the same high-quality features as the PlateRite 4600Z, and provides output at up to 11 plates per hour. Both models have a proven external-drum design and come with the option of inline punching blocks to help ensure perfect on-press register and faster makeready times.
For the flexo market, Screen offers its range of flexo and letterpress platesetters, which can also image the black mask layer of resin plates directly, eliminating the need for film and other intermediate processing. This results in more efficient operations, as well as more consistent output quality. Additionally, the PlateRite FX series units claim a superior halftone dot reproduction, ensuring consistently high quality printing in highlight and shadow areas.
The FX1524 and 1200 are designed for a wide range of uses, including the production of labels, flexible packaging, cartons, and corrugated packaging. Plates up to 1,067×1,524 mm for the FX1524 and up to 1,067×1,200mm for the FX1200, can be loaded onto their drum with ease, ensuring high precision, high quality output of resin plates.
Screen says the PlateRite FX870 is “the ideal flexo/letterpress CtP recorder for printing companies that already possess letterpress printing presses but want higher quality output, as well as for companies looking to improve the quality of the labels output from their intermittent letterpress printing presses, offset label printing presses, or flexo combination printing presses”. In their standard configuration, the PlateRite FX1524, FX1200 and FX870II support an output resolution of 4,800dpi.
And Screen’s Equios workflow, the core prepress workflow from Screen, lies at the heart of production in more than 4,000 print companies worldwide.
Comment below to have your say on this story.
If you have a news story or tip-off, get in touch at editorial@sprinter.com.au.
Sign up to the Sprinter newsletter