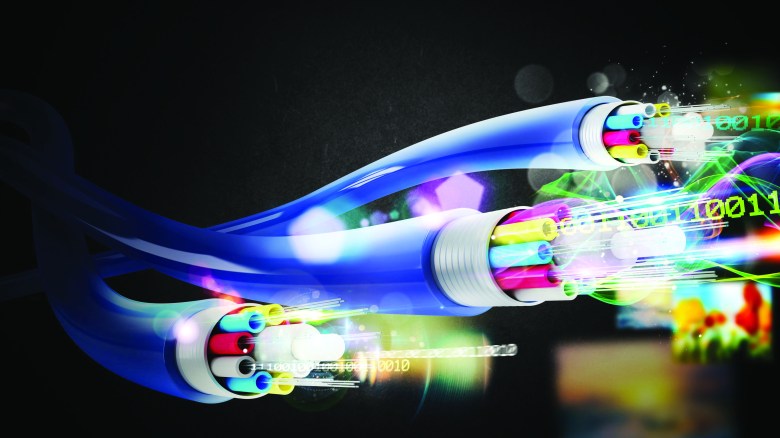
Logjams in workflows are the bane of efficient printing. They can occur as a result of operator errors, or simply when outputs get out of lockstep, such as when a press is generating output faster than a folder or creaser can process the load.
It is a truism to say workflow automation is essential in the modern day printing operation, but how easy is it to implement workflow automation? At what point does it become viable, does it work out with just one cutsheet digital printer, or do you need a fleet of presses to make it pay?
And in today’s commercial print enterprises, where hybrid operations of offset and digital printing operate parallel to each other, what are the smartest ways of not reinventing the wheel, on both sides of that divide – in fact, should it even be seen as a divide?
In other words, do you need different setups for offset and digital or does one workflow cover them all?
And then there is the question of how to integrate MIS and W2P. Is it even worth investing in workflow automation if you don’t have these two elements? And closely linked to that is the question about whether workflow should be based in the cloud.
Integrating MIS, W2P and the cloud
For Peter Janusik, national sales manager, Unified Workflow Solutions, at Kodak A/NZ, the most important part of implementing automation is to first understand the workflow and plan what you want to automate. Once that is done, implementing automation is less complex, he argues. “There are many components to Kodak’s Prinergy workflow wherein the user can crawl, walk and run. Automation is one such component.”
“Prinergy’s Rules Based Automation (RBA) works by using triggers to start events or actions. With the installation of RBA, a printer can begin to immediately see RoI by simply implementing an archive strategy. The user’s natural progression of job status becomes the trigger for a timed archive. In my example, job status has been changed to Complete, a timer starts for seven days; which would commence with the files duplicated to archive on the seventh day. This is what I would term crawl,” he explains.
“If there are recurring jobs, touch points are identified where user inputs could create errors, simply because there is human intervention. Identifying these opportunities, can be strung together through a visual user interface to create workflows – this is the walk phase.
“Ultimate automation is achieved through the use of input (XML or JDF). These control files can be interpreted and then used to route, control and present to output – this is the ‘run’ phase,” he concludes.
Is it worth implementing a vendor-based workflow for just a single press, or do you need to have a fleet of presses to make it viable? Janusik responds that while any software/hardware purchase must run a gamut to determine the RoI, Prinergy’s RBA is one that pays for itself with the first couple of uses. “RBA ultimately is a software development kit, but visual, so the user doesn’t have to do any coding (but if they want to, scripting is available). With access to almost everything that Prinergy itself has to offer, and the ability to incorporate third-party solutions as triggers throughout.”
Janusik explains that Prinergy comes with some canned, or standard, rules. “Using the canned rules pays for the cost of the licence, then everything else is cream on top.
“Implementing a cut-sheet strategy is another example that can run the gamut from crawl, walk to run. We have printers that are using fully automated workflows to their digital devices wherein the operator submits the job and receives the output at the printer. Inclusive of all the production-class decisions that need to be made, from colour matching to imposition,” he says.
Is a hybrid enterprise a divided operation? To what extent can offset and digital processes be integrated? Janusik sees Prinergy as the page production hub, regardless of the output type. “By leveraging RBA, all the printer needs to define would be a quantity – a rule based on that alone could make the determination for output … ‘if less than X go to digital, then greater than X go to CtP’; and Prinergy addresses all the set-up processes for each path. The page is simply part of the process.”
How can you integrate your management information system (MIS) and web-to-print (W2P) capabilities into your production workflow? Prinergy integrates with MIS solutions that are based around JDF, by using Business Link, states Janusik. “This solution in itself is a form of automation, but it does not end there. Once again, triggers within the production workflow can notify, create and send pages to a variety of sources to meet the needs of the internal – your sales/customer service, and the external – your customer.”
“Web-to-print is even easier; here you have finely tuned and constrained pieces of information that relate to specific products or types. Prinergy can read an XML schema, and use that to transform the W2P inputs into customised workflows, not touched by human hands,” he notes.
“Now the second question, is it worth investing in workflow automation if you do not have these two elements? Absolutely. Repetition and human errors are the number one reason for re-runs and higher production costs; taking out as many steps as possible that require human input takes those costs out so your skilled operators can perform tasks that generate income rather than define a cost centre.”
With widespread growth of cloud-based software in the printing industry nowadays, it seems inevitable that production workflows can reside in the cloud rather than on bulky, difficult to access servers. Says Janusik: Parts of a workflow can indeed be located in the cloud. “But all of it – today – no. If we are talking digital, the amount of information that must be processed to keep the DFE running would be on hold while waiting for the download of a page from any cloud solution. Mix that with CtP output and an average 1-bit TIF file at a 40MB per A4, and you are looking at a lot of throughput.”
But Janusik is confident that will change, due to technologies such as what Kodak will be offering in the near future. “The ability to take the information that is processing through your system, analyse the data for things like ink usage, performance, archive, layout and more — all of these services can take advantage of the processing power inherent in a cloud offering to ebb, flow and grow.
“They do not require access to the page file but rather to small data-rich text files. These encrypted, raw files can then be transformed and manipulated in costing templates, calculation algorithms for press optimisation and more.
“The computing horsepower for these services, while feasible, would be extremely expensive – new technology, IT infrastructure and personnel to maintain it when you can use as the demand is needed,” he says.
Dierk Wissmann, Heidelberg A/NZ’s product manager, prepress and digital, says the challenge in automating workflows comes at the operational and business end. “You have to ensure clear objectives are set and the correct partners are aligned. Achieving lights-out production or OTM (One Touch Manufacturing) which covers full automation from receipt of enquiry to shipped goods is absolutely feasible now.
“However, it takes the right platform and dedication — from both the business adapting this process and the vendor — to ensure the organisational and commercial benefits are aligned from concept through to delivery.”
Wissmann believes automation can begin on production floors even with only one cutsheet press. “It’s absolutely viable; every business that uses output devices wants to ensure minimum touch points from an administration and workflow perspective.”
As to hybrid workplaces, “if you adapt upstream automation tools that take care of the initial interaction with the client, then developing dual or hybrid workflows, followed by a single point of entry into manufacturing [printing] is there and available now.”
Wissmann says integrating your MIS and W2P portals is also no problem. “Every business should adapt a few key principles; lowest operating cost per sheet for the highest sales return and ensuring that every business that wants to achieve growth develops a platform that can be scalable and adapt new aspects as they grow or realign.”
And he is upbeat about the ability to operate workflows from the cloud, but advises: “Understanding the client’s requirements for this aspect is pivotal. With more partnerships now starting to take shape across many geographical locations and businesses evolving into multi-site facilities, these aspects are there and can allow our customers to achieve hub-and-spoke production tools or to maximise partnership capacity in the different sectors they operate.”
Mark Fletcher, EFI’s associate marketing specialist, APAC, points to InfoTrends research showing print providers believe reducing production cost and improving efficiency is their number-one business focus over the next five years. Printers also list expanding workflow features to offer new services and reducing manual labour with software investments as their top workflow initiatives. “These providers recognise the need for automation to keep up with aggressive deadlines and shorter runs,” he says.
The research shows that today only 9.1 per cent of jobs are produced without intervention. But print service providers expect that 76 per cent of job production will be fully automated in the near future. “If you think automation is intimidating, too complex, confusing, and expensive, it doesn’t have to be. Seventy per cent of successful digital printers already use EFI Fiery digital front ends every day.”
“Whether you start small by saving the print settings of a job in a Fiery pre-set, configuring job properties in Fiery Hot Folders or Virtual Printers, or jump straight into workflow automation with Fiery JobFlow, one thing is clear, automation can help you improve efficiency, stay competitive, and grow profits. Fiery print servers are feature-rich digital front ends that drive a full range of colour and black-and-white digital print engines. Fiery DFEs provide industry-leading performance, colour accuracy, usability and integration that improve the quality and efficiency of digital printing and allow you to profitably provide a wider range of print services.
Fletcher says the latest range of Fiery Workflow Suite products, released at drupa this year, expand the power of Fiery servers, providing solutions for every stage in the print production process. These modular products broaden the server functionality for more advanced colour management, automation and job preparation. “You can choose what you need now, and add more as you need to adapt to changing market demands or to grow your business. Using Fiery Workflow Suite products can reduce labour costs, improve output quality, cut job turnaround time and reduce waste.”
The latest workflows from drupa 2016
Agfa
Agfa Graphics has new versions of Apogee, Asanti and Arkitex workflows, including StoreFront web-to-print and many state-of-the-art cloud implementations. Apogee Cloud incorporates all Apogee 10 workflow modules, yet relies on the cloud infrastructure, know-how and security offered by Agfa Graphics.
Apogee users today run their workflow off-site, in the same private and secure cloud Agfa also uses for its Arkitex workflow software for newspapers. Agfa Graphics also announced PrintSphere, offering print service providers a cloud-based solution for online data exchange. PrintSphere provides a standardised way to send and receive files, including secure back-ups of production databases, all seamlessly integrated with the Apogee, Arkitex and Asanti workflow software.
EFI
Post-drupa, EFI’s workflow line-up includes its new Fiery XB digital front end (DFE) platform, a scalable, high-volume blade server technology for the new generation of ultra-high-speed inkjet presses.
Fiery Navigator is a cloud-based digital print management platform for Fiery Driven digital production presses. EFI is also offering its Corrugated Packaging Suite and Publication Suite, the two newest, comprehensive productivity suites offered out-of-the-box as certified workflow systems for end-to-end production automation.
EFI CEO Guy Gecht says: “The focus EFI has placed in R&D to improve every part of the digital production chain results in an innovative offering that we are excited to present. The breakthrough new platforms could be game changers for customers as the world moves from long runs to customised, on-demand manufacturing."
Fujifilm
The Japanese press and prepress powerhouse now offers the latest version of its XMF workflow, featuring cross media capability for fully integrated production, optimised turnaround time for sheetfed, web and digital print work, a Pure PDF workflow for optimum efficiency, JDF architecture for maximum flexibility, a simple, intuitive user interface, and image processing, imposition and intelligent automation technologies built-in.
Fujifilm’s XMF portfolio now also includes XMF Remote, which enables customers to submit jobs online via a fully customisable web portal. Preflighting commences as soon as the files are received, with updates to the job status window reflecting this. Online and emailed status reports and alerts ensure that both printer and customers know the progress of any job at any point, speeding up the entire review and sign-off process.
XMF PrintCentre is a fully hosted, cloud-based W2P service. XMF PrintCentre is a fully customisable, comprehensive W2P system, exclusive to Fujifilm. XMF ColorPath is a cloud-based system hosted by Fujifilm that allows calibration, ICC profiling and alignment to ISO 12647 for a wide range of print devices, from offset and screen presses to digital wide format and B2 inkjet printers, such as Fujifilm’s Jet Press 720. And Metrix is an automatic layout calculator for commercial printers. It is used by estimators, customer service representatives, production planners, and prepress operators to instantly calculate optimum layouts, even for complex ganging.
Heidelberg
The German print and graphics giant now offers a number of advances to its workflow suite, demonstrated at drupa. These include a new optional digital front end for its Prinect workflow, which enables integration of Linoprint digital printing systems with Speedmaster presses in a print shop’s overall workflow.
Prinect’s Smart Automation module enables virtually fully automated production of standard print products, from prepress to postpress, with Prinect now automatically defining the production concepts based on job data and product information.
New versatility with Prinect Business Manager optimises mixed-form workflows, new Speed Estimator, in the Prinect Business Manager MIS solution, has fully automatic costing of the entire production concept, layout, and outlay for standard products. The new Prinect Portal facilitates communication between customers and service providers. Print shops give their customers personalised online access and the relevant authorisations can be customised. Prinect Web Shop, a software-as-a-service solution, incorporates media-service-provider customers into the workflow.
Kodak
At drupa, Kodak introduced its Portfolio 8 product line. Prinergy 8, Preps 8, Pandora 8, Insite 8, all in Beta now. And in the very near future, it plans to introduce the first of many cloud based services; archive and system analytics.
As to Prinergy itself, Kodak describes it as modular and customisable, with an open infrastructure that integrates conventional and digital print production. It supports virtually all third-party press equipment in addition to Kodak products. Prinergy is fully integrated, from job submission to output. Configured industry solutions specialise it for commercial (offset and digital) and packaging printing.
Ricoh
Ricoh offers its TotalFlows workflow suite, incorporating data capture to initiate the output process, including W2P job submission; preparation of input data and associated resources for streamlined production and delivery; management of jobs across multiple printing systems; output via Ricoh’s range of digital colour and mono production print devices, and end-to-end control of processes, jobs and devices.
Screen
Since drupa, Screen’s Equios workflow now has the latest Adobe PDF Print Engine 2 core, which enables high-speed processing of large amounts of data, a key requirement of variable data printing (VDP). PDF files can be RIPed to Screen's Truepress JetSX inkjet sheetfed press, as well as to the Truepress Jet520 VDP web press and PlateRite CTP recorders, along with inkjet and toner-based POD presses and proofers from other manufacturers.
Eqiuos supports print-on-demand and CtP production, and makes high-speed VDP possible. The workflow controls production from the time a job is captured or created, through all stages of production to postpress and delivery of the finished project. Wherever JDF is deployed, Eqiuos integrates seamlessly all the way to the bindery, with the EqiuosNet Partnership Programme involving third-party hardware and software vendors. Eqiuos automates job management, including accurate imposition and consistent colour management, across different output devices. It uses a single interface to drive multi-device production at various levels, such as VDP.
Comment below to have your say on this story.
If you have a news story or tip-off, get in touch at editorial@sprinter.com.au.
Sign up to the Sprinter newsletter