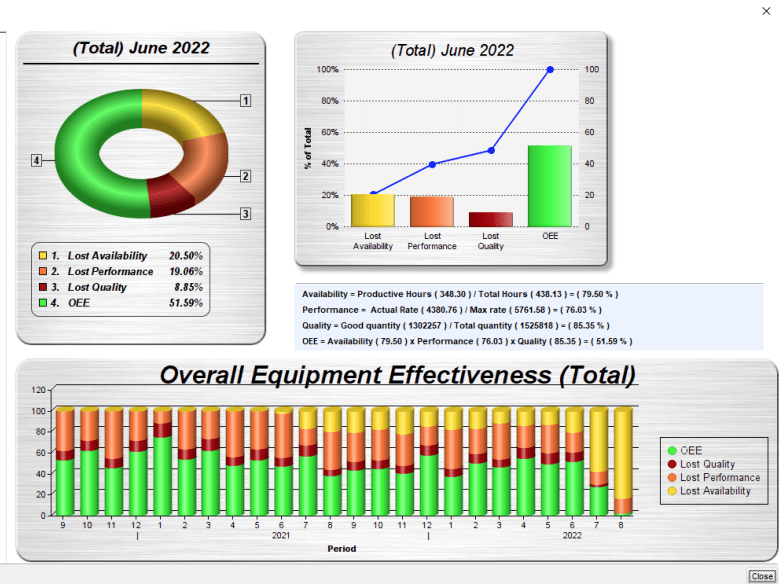
This article first appeared in the September issue of Australian Printer, authored by Optimus Group commercial director Steve Richardson and Australian business manager Con James
In today’s world, a print service provider needs to have digital foundations in place to be far better equipped to rapidly respond to the pressures and immediacy of most customers’ modern-day demands. Having an integrated workflow/MIS for some printers can transform their business capability – by enabling them to instantly provide a level of transparency that most of their customers assume they already have.
Just look around the society we live in. Most everyday consumers get all the information they ever want from mobile devices on the palms of their hands. So, it’s only logical that this expectation exists when dealing with print service providers.
However, a good Management Information System (MIS) is one that’s properly configured and provides accurate and incisive data on sales, production, and financial and delivery information in an easy and accessible way. The savings achieved from automation and efficiencies can often help the investment to be fully paid off within months.
At Optimus, we sell MIS software. Our primary offering to the wider market is our award-winning Optimus dash MIS.
We believe the uniqueness of an Optimus dash MIS lies in its ability to offer great flexibility in adapting business rules and different manufacturing methodologies. So, whatever a print service provider produces or needs managed, an Optimus dash MIS can handle it.
This is a highly configurable solution, not a customised one. This means that long after the initial implementation of the system, when a print service provider is faced with the task of managing inevitable change with regards to either adding a new product or process, their Optimus dash MIS software suite can adapt and grow with the business.
Critically, Optimus can run a highly configurable process-led approach, meaning that steps can be mapped into the workflow and the level of complexity or simplicity that is deployed is up to the end user. We take our inspiration from a lean manufacturing-led approach, which seeks to ensure maximum information for the minimum number of clicks.
From a workflow perspective, we are an MIS company. That’s our core activity; so, we look to combine with best-of-breed workflow software solutions. Optimus has first-class integration capabilities that allow us to combine bi-directional processes with a variety of global products and services.
The most recent integration delivered was in combination with Enfocus Switch, but we can work with any workflow solution that has an API. When providing MIS and workflow, we also provide extensive professional services and consultancy to ensure a desired outcome.
An Australian packaging printer recently invested in our Optimus dash MIS. The install has revolutionised their ability to analyse real-time data efficiently and easily. By fully automating with Optimus, which included combining estimating with a fully integrated imposition suite to gang jobs, they have transformed their operations.
Prior to this, numerous spreadsheets with manual intervention and potential for error handling was the way these processes were managed. Challenges were orientated around managing a wholesale change in process and ensuring staff were well-supported to get the results they needed. But now, this new automation has provided the business with the foundations for delivering instant, trusted data.
It can now plan and output jobs in a far more efficient and transparent way. This new functionality has also been designed to work in conjunction with a new warehouse management system for pallet tracking. The bottom line is, their profitability and performance are now up!
When it comes to migration from one software system to another, this requires a great deal of common-sense planning and clear dialogue about the possibilities of the solution. As a business, we are always seeking to be as accommodating and creative as possible, but in equal measure, the team at Optimus Australia will advise straight away if something can’t be easily done. We say this, because not all software systems have equivalent fields and structure, and there is no point in pretending otherwise.
We can typically always import customer, supplier, and stock item information into a new Optimus MIS from an older system; we have well-established routines for migrating this data. We would always suggest running your old legacy software system with one or two users for a period of 12 months before the transition to the new MIS/workflow investment.
As is the nature of all software, it never stands still. At Optimus, we are always looking for ways of improvement and advancement that can evolve our software over time to suit the needs of printers going into the future.
At the heart of this, from our perspective, is the provision of a first-class architectural foundation to ensure that flexibility and connectivity are baked into any of the solutions we provide to our global customer base. We believe we already have the right architectural structures in place now to ensure customers can indeed adapt and connect their Optimus MIS in an ever changing, fast-paced world.
Comment below to have your say on this story.
If you have a news story or tip-off, get in touch at editorial@sprinter.com.au.
Sign up to the Sprinter newsletter