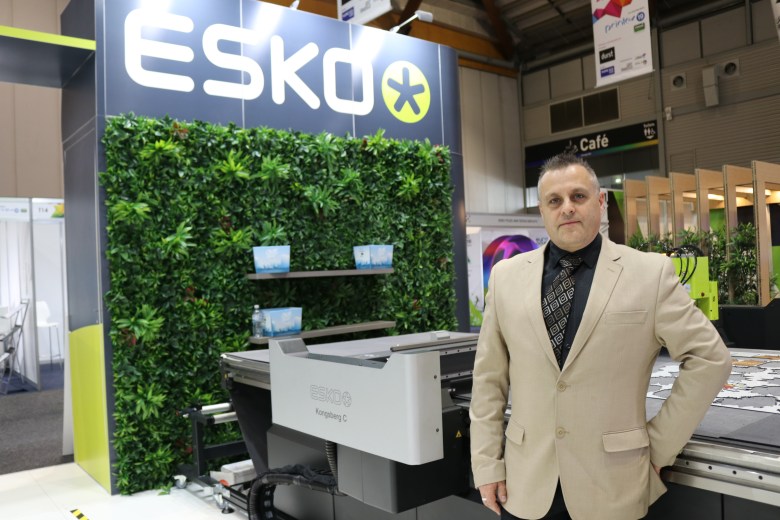
This article first appeared in the September issue of Australian Printer, authored by Esko Oceania regional marketing and channels manager Scott Thompson
With today’s brands and retailers seeking more versatility from their suppliers, there is only one way for print and packaging converters to thrive – through improving operational efficiencies. This means to digitise, automate and connect. Processes need to become more integrated to create a smooth workflow from incoming artwork to product shipment. Avoiding manual intervention in the process, optimising production efficiency, and ensuring right first-time manufacturing to minimise waste and costs, are all key. This is the promise of today’s prepress software.
Esko software covers the entire journey of packaging print, from inspiration to artwork to press-ready separations. It scales along with a business’ requirements and enables converters to tackle the most urgent problems first and scale up their software capabilities as the business grows.
The latest version of the Esko workflow server software Automation Engine includes the option to host the workflow automation server in the cloud. Under this Software-as-a-Service model, companies can avoid IT overhead costs and complexity by standardising workflows, even across multiple geographically distant production sites, further driving up efficiency and performance.
Esko solutions integrate with all MIS systems on the market today to bring the specific capability required for the prepress part of the overall converter’s operations. By implementing a solution such as Esko WebCenter – a labels and packaging management and collaboration platform – all stakeholders can work on the same version of an artwork and its constituting components, avoiding unnecessary duplications and versioning errors. Artwork approval is a key feature of the collaboration workflow, bringing brand owners and their suppliers closer together around a single version of the truth.
Fundamentally, a connected workflow simplifies, streamlines and standardises each step of the prepress process, making it easier to manage, identify issues and resolve problems before they occur. It delivers proactive, positive control and ultimately optimises headcount to minimise operational costs and waste.
The most important consideration for any business should be – through a process of value stream mapping and comprehensive research – to ensure that the deployment, installation and configuration of any given solution meets their specific business and operational requirements. This is particularly the case with integrating MIS/ERP with prepress automation. Esko engages with its customers in ‘Discovery Workshops’ to help them deploy the best workflow implementation.
Software solutions must also be tailored to the specific business operations, skills and competencies, as well as the individual’s requirements. As an example, Esko’s recent User Experience (UX) improvements in WebCenter were geared at optimising the experience of non-expert users.
Management software solutions have become integral to most modern businesses too, so gathering data – from customers during the job onboarding process and from multiple online systems in the company during production – then analysing this information and producing reports to aid management decision-making, has led to contemporary MIS solutions being viewed as the backbone of any organisation.
Feedback from the industry has shown that in terms of speed, quality and consistency, workflow automation at the very start of a project – especially with the integration of automated data exchange between Management Information Systems (MIS), Enterprise Resource Planning (ERP) systems and the prepress workflow – are the areas with the biggest potential for delivering efficiency gains.
Further digitisation, automation and improved connectivity across a business are key to enabling converters to achieve more with less. Integrated systems and software can now manage everything from accepting an order and assigning the design task all the way through to obtaining approval and organising shipping of finished products to the customer.
Esko works with customers worldwide and a recent example of a company that has integrated Esko WebCenter into its prepress is an Austrian packaging services provider, QuarterPack.
The QuarterPack team has worked with Esko technology for many years, typically operating PDF based workflows. In 2018, the company began a project using software to deliver a customer-oriented project management solution, with the aim of streamlining and smoothing the complexity of operations in the company.
By using WebCenter, it was able to not only make sure that its message to the customer was clear and comprehensible, but it also brought the company closer to the customer’s needs and wants. QuarterPack’s entire release process is now managed by WebCenter. That makes the business flexible when it comes to serving its customers, and has allowed it to prepare print data for customers, with benefits including traceability and speed.
With the latest software release, Esko addresses today’s market needs and ensures its innovations significantly improve customer outcomes. It is also focused on helping customers make the best use of it to deliver immediate results and meet the challenges they face in the long-term.
Comment below to have your say on this story.
If you have a news story or tip-off, get in touch at editorial@sprinter.com.au.
Sign up to the Sprinter newsletter