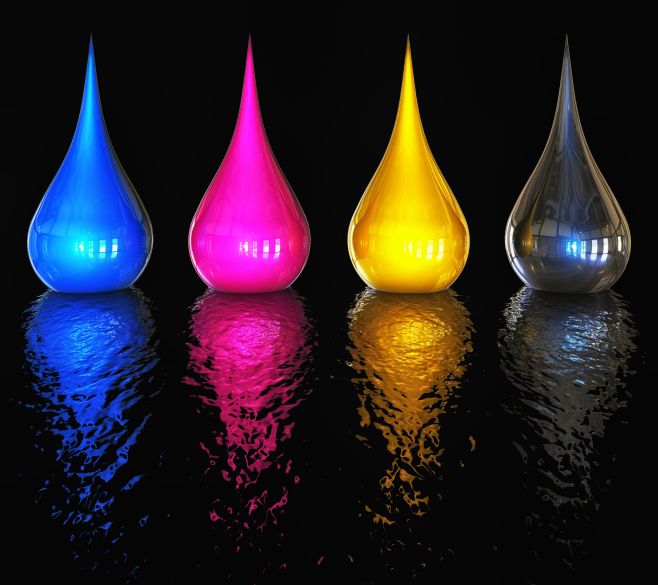
Digital printing as commercial printers have known it is changing rapidly. The old assumptions which placed HP Indigo at the top of the tree for quality competing with the Xerox iGen, Xeikon, and Kodak Nexpress for speed and formats, and pretty much everything else a league behind, no longer exist. While these four continue to fly the flag for quality, the gap between this and what is possible on Ricoh, Canon and Konica Minolta machines has closed, however the cost gap remains.
Printers are deciding for instance that a Ricoh ProC91100 and the like are perhaps a sound investment for straightforward good quality colour print, given their more affordable investment level.
The Japanese manufacturers have tackled the limitations of their machines in terms of substrates, fit and colour consistency and are now offering extra functionality such as the ability to print long sheets, together with being able to print on additional materials, and with extra colours.
Toner particles are much more even and much smaller than in the past, hence the print layer is thinner, delivering a more even surface to the print, and better lift of colour.
These sorts of improvements are not limited to just the top end of the product family, but partly because nobody wants to produce machine specific toners or imaging drums, are available across a product range.
These digital machines share the same technology and are more often distinguished by differing monthly production ceilings, and not necessarily by functionality or quality.
As well as the scope to print banners and on textured papers, additional colours are the new name of the game.
Ricoh, and by extension Heidelberg, can print with a clear toner, with white and most recently with neon yellow and pink on its Pro C7100.
Xerox has also introduced white to the blue and green additional colours on its iGen 5, extending the colour gamut, and in white delivering an ability to print on coloured papers or metallics which need white for the other colours to sit on.
Xerox claims opacity is good enough for the double hit achieved in a single pass to suffice. For those wanting greater impact, the sheet will need to be printed multiple times.
Fuji Xerox has offered gold and silver additional colours through the Color 1000 print engine produced in Japan, but this is the first extension beyond four colours for the flagship iGen machines.
Additional colours will be available over time, including no doubt orange and neon colours.
Intriguing both white and neon toners are available on the low-cost Oki desktop machines, and many a printer uses these low-cost printers for producing invitations or social stationery, ultra-short run packaging, covers and the like, without the cost of an extra colour for a workhorse digital press.
The additional colours have also been available on the Kodak Nexpress, offering a gold, clear varnish and security inks among others. The security inks are invisible under normal light but show up under infrared black light.
It is being used on marketing material by startup tech companies in particular.
However, the upgraded and faster Nexpress announced at drupa last year, has not yet materialised. Some rethinking may be underway.
There is a growing market for higher value digital print as customers struggle with accurate personal profiling, and as marketers are looking to invest in quality rather than quantity. A well-produced engaging piece may cost more, but will be far more effective than a bland mass personalised low-cost mailed message.
In short value-added digital print like this taps into the emotional engagement that print can have though touch, interaction, as well as the visual quality of the piece.
HP can also deliver the neon colours as part of the Indigo press, as it has long been able to print special colours that a customer can mix for itself, or through the added value benefits of seven colour print. It is also possible, though not especially practical, to create raised print effects through repeated application of clear toners, these though will be heavy on the click charge.
Likewise the white for the Indigo will need repeated applications to achieve strong opacity because of the liquid toner used. It delivers a high quality thin print layer with high transparency, not so good for white.
But HP has taken a further step towards keeping its crown. It has expanded the format into B2, something that we saw at drupa 2012 becoming reality. At a stroke HP Indigo took an unchallenged market position, one that for the limitations of the imaging heads, other electrophotographic machines cannot match.
Xeikon can produce B2 format sheets, but this is by virtue of the image length it can print, not its width.
The larger Indigo print engines have been a success, more than 600 B2 sized systems are installed worldwide. And to keep the position as the leader in quality, Indigo is bringing a high definition imaging head to market before the end of this year.
This can image at more than 1600dpi, twice the resolution of the current series 4 engines.
The quality improvement is achieved through addressing more points on the sheet. The toner remains the same, but thanks to the extra finesse in imaging, the result is much smoother vignettes, flesh tones and greater detail in the image. It is the same approach as the high definition print head for HP’s inkjet machines.
For HP the enhanced imaging will open up, or rather cement its position in photo printing and short run art books. The twin engined Indigo 5000 web press will now attract the attention of those in this portion of the books market.
However, while Indigo may have clear blue sea between itself and its traditional rivals with the step up in format size, its potential customers are looking at an altogether different set of technologies. Here comes inkjet printing.
Inkjet printing has been slow to make an impact on sheetfed printing, mostly because of the engineering issues around keeping complete control of a sheet so that it can pass safely under the array of printhead just1mm above the paper. Conventional litho press systems do not work because the tail edge of the sheet is not under control and would flick up. In web printing it is relatively easy to keep the paper under tension so the expensive heads are not at risk.
It has not prevented manufacturers creating sheetfed systems based on a vacuum belt or cylinder, a different gripper arrangement or some combination of both. Heidelberg’s imaging cylinder for the Primefire 106 is designed like a Swiss watch, it can take many, many hours to assemble. Fuji’s approach is more straightforward, though is first design for the Jetpress 720 has been revised for the Jetpress 720S. This is to date the most successful of the B2 inkjet sheetfed presses with well over 100 sold and installed.
The Jetpress 720S printheads are the proven Samba piezo heads firing 3pl droplets of aqueous ink at 1200dpi. The results are high quality colour at 3,000 B2 sheets an hour. The press is capable of higher impact colour, but most users tune the machine to match the offset colour space so that work can be switched between technologies. When printing a look book, pitch document or photobook this is not necessary.
Feedback from early users gives the inkjet press another key advantage over electrophotographic printing: the up time. If sheet transport is more complex in a sheetfed inkjet press, the actual imaging is relatively simple, at least at these speeds.
Users have come to expect frequent service visits from the more mature digital printing technology, with inkjet up time can be more than 90 per cent.
A drawback of the Fuji design is that it is single sided only, making fully personalised printing more complex, using barcodes to identify sheets and call down the file to print. But, most applications are of the value added kind using the ability to print on a wide range of papers as the key to open the door.
Screen is also in the B2 inkjet sheetfed market, although like Fujifilm has yet to convince offset printers to make the move over.
Because of Screen’s inkjet technology, the Truepress Jet SX is able to print on standard offset papers, including high-gloss materials – even those that have previously been printed by offset.
The flexibility of the Truepress Jet SX is further enhanced through the use of a paper handling system that is based on traditional press technology, this means the machine’s output can be processed on existing post-press equipment.
This innovative B2-format duplex printing system boasts quick startups and production flexibility to handle diverse applications that require offset quality.
The Truepress Jet SX prints 1,620 simplex sheets or 810 duplex sheets per hour. It accommodates coated and uncoated cut sheets up to 530mm x 740mm. The greyscale printhead emits a minimum droplet size of 2 picoliters, producing a maximum resolution of 1,440 x 1,440 dpi.
Thanks to the reversing mechanism that enables duplex printing inside the main unit, the Truepress Jet SX delivers full-color printing on both sides of the sheet in one pass. The beauty of the Truepress Jet SX is its ability to print on standard offset paper without precoating. The Truepress ink dries almost instantly, allowing sheets to go directly to postpress.
A rival to the Jetpress 720S and Screen is the new B2 inkjet sheetfed printer developed jointly by Konica Minolta and Komori. It can print on even more substrates, thanks to its use of UV cured ink and because Komori has designed an extra cylinder, it can print on both sides of the sheet under the same print heads. Again throughput is around 3,000 B2 sheets an hour, half that in perfecting mode. If sheet handling issues have been solved (Komori has adopted a central cylinder design), speed is a big issue at least compared to offset litho especially as these presses are the same sort of price.
Speed can be gained by reducing the resolution, in one direction at least, but pushing inkjet too fast may lead to problems of controlling droplet placement from a piezo head to avoid droplets being affected by air turbulence. Higher firing speeds will help as Kodak has shown with its high speed Stream continuous inkjet technology, but this is not yet on a sheetfed press.
Canon acquired a great depth of inkjet experience to add to its own thermal inkjet technology which has resulted in the Voyager project, while developers in Venlo have created the i300, a two page inkjet machine much faster than toner printing. Xerox has taken the same approach with the Brenva cut sheet inkjet press, careful not to undercut the appeal of the iGen products in terms of quality with which it shares the paper transport design.
A different approach is an offset inkjet design, introducing another layer of complexity to overcome limitations. First shown at drupa 2012, the gap between a premature launch and installation of the first beta machine indicates its complexity. Landa Digital Printing has its first high speed press in the field, what founder Benny Landa– never given to understatement- is calling the ultimate printing technology. This is a B1 format press, a stride away from Indigo and every other digital printing device apart from Heidelberg’s Primefire and the planned KBA/Xerox Varijet.
At $3m each and a hefty service charge on top, this is a world away from the Canon CLC1, the first digital colour press, the early Indigo and various guises of the Xeikon DCP1.
Landa will no more eliminate Ricoh, Canon, Xerox and others any more than HP Indigo has been able to do. There is more room in the continually expanding universe for digital printing for machines with deliver, speed, quality, value added print colours and effects.
Comment below to have your say on this story.
If you have a news story or tip-off, get in touch at editorial@sprinter.com.au.
Sign up to the Sprinter newsletter