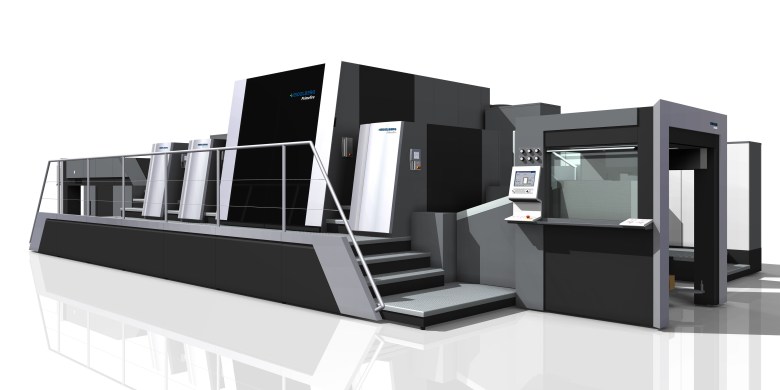
Canon i300
The new Canon Océ VarioPrint i300 is a sheetfed B3 format inkjet press. This inkjet was originally announced in 2015, but has since undergone significant enhancements which were revealed at drupa. Sheetfed inkjet is considerably faster than sheetfed toner, and of higher quality than webfed inkjet.
The print engine is adapted from Océ ColorStream inkjet webs, with Kyocera piezo printheads giving 600dpi resolution and DigiDot 2-bit variable drops for a ‘perceived 1,200dpi’ quality. It can print up to 300 A4 impressions per minute. Canon says it can reliably output 8,700 duplex A4s per hour on average, including cleaning and other stoppages. In offset terms, this is about 4,350sph B3.
At the show Canon unveiled the new ColorGrip technology in the i300. ColorGrip prints drops of priming liquid underneath each drop of colour ink. This has a number of implications. This printing practice means that the range of papers the i300 works with will be greatly extended, and it will also allow it to handle work of a much higher quality than was originally anticipated. The i300 boasts a CMYK system with six ink channels, with two ‘spares’, and the ColorGrip uses one channel to print its priming liquid beneath the coloured ink drops.
As well as this, Canon has displayed an enhanced CMYK ink set at drupa, which will have a wider gamut on a greater range of media, and enhances image quality on commodity grade untreated media,. Plus, two new finishing options were introduced; the BLM600 bookletmaking system and the Tecnau TC1530 dynamic cut-sheet perforator. The former allows the production of square-back booklets up to 224 pages thick, whereas the perforator allows the creation of horizontal and vertical micro-perfs.
According to Canon customer ramp up, once installed is high, with each press printing an average of more than 2.5 million pages per month. Early indications are that the i300 has an uptime rate of 95-98 per cent.
Durst RHO 130 SPC
Shown for the first time at drupa 2016, Durst says the new Rho 130 SPC, with a print speed of up to 9,350m2/hour, offers the industrial productivity needed to transform the packaging sector towards digital technology.
Alongside the more cost-efficient production of shelving and sales packaging in small and medium-sized job runs, the Rho 130 SPC also supports sampling, customisations and versioning, directly and without setup costs.
With the development of a non-hazardous ink system based on Durst water technology, Durst says it is addressing future directives for sustainable packaging products in the food retail sector. The Rho 130 SPC is based on the latest generation of single-pass printing systems which Durst is already using in the label printing segment — for instance, with the Tau 330.
Durst demonstrated its print performance live at drupa, and ensured that the aisles around Durst’s booth were crowded on subsequent days. With a media transport belt running continuously at two metres per second the Rho 130SPC was printing 120 high corrugated sheets a minute in high quality.
The European Digital Press Association (EDP), an association of leading European trade journals focusing on digital production, honoured Durst with two prestigious EDP Awards.
EFI Nozomi C18000
In a media release at its launch EFI called the Nozomi C18000 its biggest inkjet product development to date.
The EFI Nozomi uses single-pass LED technology to print at speeds up to 75 linear metres per minute, or 6,600 boards per hour, on substrates up to 1.8 metres wide and 3.0 metres long. It suits corrugated, packaging and merchandise display printing.
EFI combined some of the best features from many of its leading development operations in the C18000, including single-pass inkjet imaging systems from US-based EFI Jetrion, the company's Cretaprint ceramic decoration printer operations in Spain, LED inkjet innovations from EFI's global ink development centres, superwide-format press technology from the company's US-based VUTEk operations, scalable Fiery digital front end (DFE) processing and management technology from EFI's Silicon Valley development centre and cloud-based remote diagnostics and support advances from the company's Bengaluru, India, technical hub.
Users will be able to print in nearly any board application from 14-point card stock to a full range of corrugated flutes — A, B, C, D, E, F, G, N, O, AB, AC, BC, EB, EF, and triple wall — without slowing down the press. The corrugated board press prints in up to seven colours, including white, with resolutions up to 360 x 720dpi with four-level greyscale imaging.
An inline primer provides control over dot gain and ink absorption on different types of corrugated top sheets. A 100% inline image quality inspection system on the press is tied to print optimisation technologies including inkjet nozzle, alignment and uniformity correction for the highest possible imaging quality.
The Nozomi press's permanent head architecture eliminates the downtime associated with replacing consumable print heads.
The new Fiery DFE for the Nozomi C18000 press also will integrate with MES and ERP technologies in EFI's Packaging and Corrugated Packaging Suites, as well as with Esko workflows, for management, dynamic scheduling, shopfloor data collection and more.
EFI is the first to offer fully integrated top- and bottom-feed options for a digital corrugated packaging press, using a patented system that also handles media separation, lift, transport and alignment at full press speeds with programmable features for faster, automatic feeding configurations on repeat jobs.
EFI is planning to start installations of Nozomi C18000 presses within the next 12 months.
Fujifilm JetPress 720S
Launched as a technology concept at drupa 2008 as the Jet Press 720, the press has benefited from a wide range of enhancements since its commercialisation at drupa 2012. In particular, the improvement in press up-time, the addition of a new bar code system for variable data production and new modular Samba printheads, together with the ability to handle heavier-duty carton board stock introduced in late 2015, ensure the current Jet Press 720S model is a proven, reliable and incredibly versatile production press.
Over the last decade, the application scope and capability of Fujifilm's inkjet technologies have expanded substantially, making it possible to meet the exacting needs of commercial and package printing customers. The integration and evolution of printheads, inks and image optimisation technologies is critical to delivering a reliable, high quality inkjet production system. Fujifilm is able to optimise each of these three cutting-edge core technologies to optimise system performance to the maximum extent. Fujifilm showcased these technologies at drupa 2016 under the brand name Fujifilm Inkjet Technology.
The latest generation of Samba printheads form the heart of the single-pass system used for high-performance and stable jetting. The wide-gamut Vividia water-based pigment ink is applied with Rapic anti-coagulation technologies to achieve ultra-sharp printed results on a wide range of printing papers. Other features include extended FM screening optimised for inkjet and an automatic on-the-fly image compensation function that controls ink deposition inconsistencies. Endorsement of the performance and reliability of these technologies comes from the growing number of Fujifilm customers, and a number of suppliers, not least Heidelberg who have chosen these technologies to form the heart of their recently launched B1 industrial inkjet press.
Press up-time has been improved by a further 20% thanks to software upgrades which have improved the efficiency and job handling capability of the press. In addition to being able to print on heavier duty carton stock, the ability of the Jet Press 720S to print on canvas media has now been approved, widening the application capability of the press even further. Fujifilm's XMF Workflow has been improved to more effectively communicate with Online Order and Management Information Systems and more efficiently manage the Jet Press 720S alongside existing offset presses. This allows press utilisation, whether offset or digital, to be more effectively controlled.
Fuji Xerox iGen 5
The iGen5, recently released in Australia, was shown at drupa 2016, and is available in a two-feeder, single-engine, one-stacker configuration, but can be extended with a range of different feeding and stacking options according to printers’ needs and run lengths.
The iGen5 is a cut sheet, dry ink (toner) based, third-generation xerographic print engine, supplementing traditional CMYK colours with an additional fifth colour station offering orange, green or blue. The supplementary colours promote a larger colour gamut to suit the needs of customers for ensuring colours are reproduced correctly. It will match over 90% of the Pantone Plus coated library within 3dE Paper Format Standard Sheet Size.
Image quality resolution is rated at 2,400 x 2,400dpi for line screens from 160lpi to 250lpi. The maximum image area is 2mm less than sheet size (a 1mm border on all sides) on paper weights for coated, uncoated, textured, specialty stocksfrom 60gsm to 350gsm.
Its paper stock flexibility enables it to print on recycled, perforated, tabs, transparencies, a wide variety of labels, synthetics, sheets with removable cards, polyesters, magnets and thick stock up to 24pt. Mixed-stock jobs of up to 12 stocks are supported at the rated speed.
It uses a colour maintenance tool and closed-loop controls with an inline spectrophotometer for colour control.
A load-while-run paper capability and unload input capacity from up to six feeder modules, or 12 trays, gives the iGen5 up to 30,000-sheet capacity.
It offers a wide variety of bindery options including the CP Bourg BSF-X sheet feeder, the Epic Cti-635 inline coater, the GBC Fusion Punch I, the Watkiss Powersquare 224 or CP Bourg CDF-e/BDFN-x document finisher and BM-e booklet maker/BookMaster Pro 30. For slitting, scoring and perforating, the Rollem Jetslit is available.
A range of training servicing levels is offered, depending on the SLAs a business has with their customer. In most cases Fuji Xerox Australia can guarantee a technician on site within four hours of an issue being reported.
Heidelberg Primefire 106
At drupa 2016 Heidelberg showed a world premiere for industrial production of digital printing applications in 70 x 100cm format with the Primefire 106. The system is based on inkjet technology from Heidelberg’s development partner, Fujifilm, and the Heidelberg Peak Performance platform from the company’s offset technology.
The Primefire 106 enables packaging printers in particular to take the first step in developing new areas of business — for example, with the production of variable or personalised packaging.
The digital printing system offers a maximum quality of 1,200 x 1,200dpi at a printing speed of up to 2,500 sheets per hour, and capable of achieving production volumes of up to 1.5 million sheets per month in future productivity modes.
The seven-colour inkjet system with Heidelberg Multicolor technology also covers up to 95% of the Pantone colour space. All liquids are Swiss Ordinance approved and enable printers to aim for food compliant production.
The system can handle formats up to 75 x 106cm – like a Speedmaster XL 106 – enabling printers to use existing postpress equipment without any additional investment. Due to open interfaces, digital post-processing will be possible.
Heidelberg has outfitted the Primefire 106 with the new Prinect Digital Center Inline with Perfect Stack technology. In combination with the Prinect digital front end (DFE) from Heidelberg, the new control station offers seamless integration into a print shop’s existing overall workflow. In combination with the Perfect Stack technology and controlled by the Prinect Digital Center Inline, the Speedmaster XL-based feeder only allows good sheets into the delivery pile. The operator can also output test sheets directly to the control panel at the push of a button in order to visually check their quality.
“Folding carton producers in particular develop new digitally driven business models and thus improve their competitiveness,” said Jason Oliver, head of Heidelberg Digital.
Shown at drupa as a world premiere system, the first Primefire 106 will be shipped to a beta test site in December this year. Further customer placements will follow and are already scheduled.
HP Indigo 12000
HP premiered the HP Indigo 12000 digital press at drupa 2016. The company says the 12000 offers major innovations in print quality, application range and productivity, as well as breakthrough priming technology and colour matching capabilities.
It boasts a maximum printing speed of up to 4,600 B2 colour sheets per hour, so it is capable of producing over two million colour sheets per month. It can print monochrome in duplex at 4,600 sheets per hour.
The Indigo 12000 can print virtually unlimited applications including synthetics, canvas, and metallised with on-press HP Indigo ElectroInk Primer and One-Shot Colour technology. It will print on stocks from 70gsm to 400gsm and 75 to 450 microns in thickness, including coated, uncoated, coloured and dark papers, and paperboard for folding cartons. Using the digital inline primer it gives printers the ability to print on a wider gamut of stocks that don’t have to be pre-primed or sapphire coated.
Like all HP Indigo digital presses there is a supported upgrade path. Full certified training is available from the Currie Group training centre located in Melbourne.
KBA VariJet 106
KBA’s Sheetfed Solutions and Xerox announced a partnership at drupa 2016 to develop an industrial digital sheetfed press for the folding carton market. Wide format cartons, for items like cosmetics, food and pharmaceutical products, until now have relied on traditional analogue offset printing.
The two companies launched the concept of the KBA VariJET 106 Powered by Xerox, although they did not demonstrate a machine. It is a hybrid machine which can include any units from a standard Rapida 106 machine such as offset units, cold foil and coating, including double coating units, as well as die cutting. Printers can print offset and digital on the same press, although it can be built as a digital press only. The current speed of 4,500 sheets per hour will increase over the next few months.
KBA will be inviting interested customers to an open house in Germany later this year to show the new machine.
The KBA VariJET 106 Powered by Xerox integrates Xerox Impika inkjet technology into the KBA Rapida 106 press platform. The press, in the final stages of development, will print 4,500 B1 (750 x 1,060mm) sheets per hour. Its modular concept enables the combination of digital inkjet printing with optional inline capabilities such as coating, cold foil application, rotary die-cutting, creasing and perforating.
KBA says digitally printed packaging worldwide will grow at a compound annual growth rate (CAGR) of roughly 16% between 2015 and 2020. Within that, digitally printed folding cartons will see a CAGR of 40%.
The KBA VariJET 106 Powered by Xerox press brings the benefits of digital printing, such as running multiple versions of the same carton as well as customised cartons, opening up new business opportunities for industrial production printers.
“As a leader in packaging printing our customers are confirming that this is exactly the product they need for the market opportunity that exists,” said Ralf Sammeck, CEO of KBA-Sheetfed Solutions.
“By combining digital capabilities like cross media marketing, digital storefronts and automated workflows with those of classic offset printing, our customers will be able to offer new products and opportunities for their customers not seen in the traditional packaging market,” said Robert Stabler, general manager, Graphic Communications Business Group, Xerox.
The KBA VariJET 106 Powered by Xerox will be available in 2017.
Kodak NexPress ZX3900
Kodak showcased this new technology during drupa 2016. The NexPress ZX3900 offers new packaging and retail application opportunities, and now supports thicker paper and thicker synthetic substrates without limiting the range of commercial jobs that can be produced.
The machine ships with System software v16, providing a set of new tools to control image quality and maintain productivity to optimise costs and uptime, including:
· An Ink Estimating Tool, which estimates the CMYK and all specialty inks used in a print job
· Spot Color Recipes, which allows PSPs to create unique colour blends for clients and save them for future orders
· A new production dashboard allows users to monitor the activity, consumables and performance of their NexPress on a handheld device
· Automated Data Export, providing periodic data on press production details for integration with external MIS systems
· NexPert Operator Support, a fully featured operator support and diagnostic system based on HTML5, allowing for fast operator access with no Java-related security or performance restrictions
· Variable speed control allows for the printing speed to be set in the job ticket, optimising quality and press performance.
The NexPress ZX 3900 includes new capabilities such as opaque white dry ink, complementing the already available nine specialty inks for opacity in a single pass for applications such as packaging, signage, labels and invitations. It has more than 20% higher opacity in a single pass compared to multiple passes on competitive presses. The new Opaque White Dry Ink can be installed on most existing NexPresses as an option.
The NexPress Substrate Expansion Kit supports select heavy paperboard stocks of up to 24pts/610 microns and select heavyweight synthetic stocks up to 14mm, available in 2017. Also available in 2017 will be support for sheet lengths up to 1,219mm.
Kodak offers a comprehensive range of services for customers, including Optimised Performance & Uptime Services (OPUS), a portfolio of services that help deliver an optimised production environment to reduce costs associated with downtime, re-work, consumables and waste, and maximise revenue opportunities in the process. There are three categories of OPUS services — Uptime Discovery, Enhanced Preventive Maintenance and Peak Production Support.
Customer education includes NexPress Operator Training, NexPress Gold Training, NexPress Dimensional Clear Training and NexPress Application Specialist Training.
Komori Impremia IS29
Komori used drupa 2016 to launch its Impremia IS29 29-inch sheetfed UV inkjet digital printing system. It uses Komori’s inkjet UV printing system, jointly developed with Konica Minolta.
In addition to driving forward the idea of OffsetOnDemand in offset printing, Komori says that raising efficiency and profits by taking advantage of both offset and digital printing technologies is the key to success for printing companies. Success requires the reliability and print quality of offset presses combined with the variable data printing capabilities and short run convenience of digital printing systems.
To offer these capabilities, Komori is creating DigitalOnDemand solutions. It has developed the Impremia IS29 digital printing system as the key machine in the Komori OnDemand melding of offset and digital.
The Impremia IS29 can print directly on a wide variety of stock in high quality with a maximum sheet size of 585 x 750mm. There is no need for special paper due to UV inkjet technology, and no need for any precoating or certified paper.
It can print sheet thicknesses from 0.06mm to 0.6mm in single-sided printing (0.06-0.45mm for double-sided printing).
It features instant curing and the ability to start finishing immediately due to its use of UV ink. It has the same high front/back register accuracy as offset.
Digital printing in the 29-inch size greatly expands the range of possible work. The system prints large posters, paged items with multiple impositions and packaging that conventional A3 machines cannot handle. Six-up US letter-size impositions are trouble-free.
The machine incorporates a perfecting mechanism, accommodating not only 4-up single-sided but also 8-up double-sided impositions.
The Impremia IS29 also incorporates a direct printing method by means of UV inkjet. Printing that emphasises painting-like contrast can be performed on specially processed papers (such as high relief embossed paper and canvas) that are difficult to handle not only with on-demand printers but even offset presses.
The Impremia IS29 will be available in Australia in early 2017 through Ferrostaal Australia.
Konica Minolta AccurioJet KM-1
The Konica Minolta AccurioJet KM-1 is a sheetfed duplex B2-format digital inkjet press, using UV-cured inks. The company has made toner-based digital colour presses since 2006. The KM-1 is its first sheetfed inkjet press and has been developed as a joint venture with Komori, which will sell it under its own name as the Impremia IS29.
UV-cured inks and cool LED lamps enable the press to handle a wide range of substrates including standard offset stocks or synthetics, with no need for special pre-coatings. It can also handle thicker cartonboard stocks up to 0.6mm as well as heavily textured or embossed papers.
The main target markets are packaging, books and commercial print.
The configuration is broadly similar to other B2 format sheetfed inkjet presses, with offset type feeder, gripper-to-gripper sheet transport and delivery. Konica Minolta makes the print engine (including its own inkjet print heads and controllers), inks and front-end, while Komori provides the substrate feed and transport mechanisms. It takes oversized B2 sheets up to 585x750mm, allowing six-up A4s.
The 600dpi printheads with piezo shear technology are fitted in pairs to give 1,200dpi. There are eight pairs per full-width print bar and one print bar per colour. Initially, the presses will be wide-gamut CMYK, with five and six colour options in future. Inline sensors detect misfires and correct on the fly. The head carriage retracts sideways for maintenance and heads can be replaced by the operator.
The most unusual aspect is the UV-cured ink. This was specially developed for the KM-1 and is heated to reduce viscosity, allowing very thin ink films. The LED curing lamps are compact and cool, though a simple fan extractor and duct is required, largely because of the heated inks.
Production presses will print 3,000 single sided or 1,500 double sided B2 sheets per hour at up to 1,200dpi, with full variable print. This is a little slower than the 3,300sph originally announced. Konica Minolta Business. There are three printing modes, with the same resolution but different ink drop sizes, which helps reduce ink consumption depending on requirements.
Landa W10P Nanographic Printing Press
At drupa 2016, Landa announced the launch of the industry’s highest speed digital press for the high quality publishing market – the Landa W10P Nanographic Printing Press.
The twin-Engine Landa W10P web press for applications such as magazines, journals, catalogues and direct mail magazines and journals, is able to produce over two million digitally printed magazine pages per eight-hour shift.
From a business perspective, Nanography will enable Landa customers to move their mainstream journal and magazine publishing, catalogues and direct mail pages from offset to digital, for a reduced total cost of ownership (TCO) and improved margins. According to Landa, magazine and journal publishers will leverage the technology’s benefits to offer more versatile products and attractive business models.
The metre-wide two-sided Landa web press has twin printing engines, each with 4-8 colours, and prints on virtually any coated or uncoated paper stock ranging in weight from 30gsm to cardstock. As Landa nanographic printing creates zero strikethrough, the press produces magazine-quality printing even on the lightest and cheapest uncoated papers.
Running at 200 metres/minute, the Landa W10P Nanographic Printing Press is up to 24 times faster than any other commercial quality digital press, and requires no setup or makeready. A crossover point with analogue up to 5,000 copies lets users offer affordable digital production while providing fast turnaround and on-demand printing.
Landa will start shipping the Landa W10P Nanographic Printing Press to customers in late 2017.
Ricoh Pro VC60000
The Ricoh Pro VC60000 was showcased to a worldwide audience for the first time at drupa 2016.
It is a modular, full-colour continuous feed engine to help operations compete in challenging commercial printing applications, direct marketing production and book printing.
The Ricoh Pro VC60000 is a continuous feed inkjet printer that enables printers to print up to 150 metres per minute — nearly 100,000 A4 images per hour. It can print at resolutions up to 1,200 x 1,200dpi, and its drop-on-demand print heads intelligently adjust ink use for the job to save on ink costs, while maximising near-offset quality.
The Pro VC60000 inks support high speed printing with high penetration and quick drying combined with high viscosity for less ink bleed and show-through.
It supports a wide selection of paper stocks — coated, uncoated, inkjet treated and offset, from 40gsm to 250gsm — on printable sheet sizes up to 508 x 1,371mm for greater flexibility in the transition of offset and cut-sheet applications.
The Ricoh Pro VC60000 is a flexible, modular design. The base engine includes the entrance unit, four print stations, a dryer unit and exit unit. Two base engines are required to print both sides of the paper in a single pass. An optional undercoat unit can be added to coat one or two sides of the paper to provide high image quality on offset coated stocks.
An optional protector coat can be added to each base engine to improve scratch and scuff resistance on coated paper for direct mail applications. Optional extended air dryers can be added to each base engine for use with harder to dry stocks such as inkjet coated stocks or prints with heavy ink coverage. In addition an external dryer unit can be added at the end of the line.
The modular design of the Pro VC60000 allows for field upgrades based on customer needs.
Ricoh provides extensive operator training, hotline support and 24/7 service, and Ricoh provides its own finance.
Screen Truepress Jet520NX
Screen GP showed a new high-speed 520mm inkjet web at drupa, the Truepress Jet520NX. The new model incorporates many of the image processing and inkjet technologies accumulated by Screen since the launch of the 520 series in 2006.
Targeting the ever increasing demand for diversified, small volume printing capabilities that appeal to the varied attributes of individual consumers, the 520NX increases throughput by at least 20% over the standard 520 model.
The Truepress Jet520NX inherits many of the proven features of the successful high speed 520 series, which have already exceeded 1,000 shipped units worldwide, with 12 in the ANZ region. However, the Jet520NX is equipped with newly developed five-inch print head modules and supports a maximum resolution of 600 x 1,200dpi, plus advanced ink metering control. These features deliver significantly enhanced colour reproduction compared to existing models.
The Jet520NX can be fitted with an extra print head for a fifth colour that could enable the use of MICR ink, invisible UV fluorescent security ink, and other special inks.
Screen GP has specifically designed the Truepress Jet520NX to facilitate smooth replacement of the existing Truepress Jet520 line. It expects the new system to become a key element in printing companies’ ongoing efforts to realise the potential of new printed products and solutions.
Also new at drupa was a new ink system for the high-definition Truepress Jet520HD, released in 2014. The new inks enable the Jet520HD inkjet web press to print directly on to most offset coated papers currently available. The inks are also compatible with printing on a wide range of other paper types, including popular standard coated paper and high-quality inkjet paper, as well as standard plain paper.
Both the new 520HD ink and the 520NX are due for release in early 2017.
A third new inkjet initiative was announced at drupa; not so much a press but an inkjet module that can be retro-fitted to BHS corrugated manufacturing lines so that finished, printed sheets emerge at the end. BHS claims over 50% of the world’s corrugated equipment market and, together with Screen and Inca (a Screen-owned company), plans to introduce the module in 2018. Projected speed is a blistering 300 linear metres per minute.
Xeikon Trillium One
Xeikon’s Trillium One combines the strengths of offset litho in delivering high print quality, ink densities and image coverage on different substrates, with the strengths of digital printing to enable variable data printing at higher volumes with lower costs and easy operation.
The joint development project between Xeikon and Miyakoshi combines the expertise of Miyakoshi in the mechanics of a printing press and Xeikon’s approach to digital imaging, high speed electronics, high resolution LED technology, workflow and toner technology.
Capable of running at 60 metres per minute at 1,200dpi, with a print width of 500mm, Xeikon says the four-colour press delivers cost effectiveness, high quality and speed. It uses Trillium, Xeikon’s liquid toner printing process, which was first presented at drupa 2012.
Initially it is ideally suited to direct marketing materials and catalogues, with more target markets and applications expected to be added over time.
It incorporates Xeikon’s Tonnik, a liquid toner combining all the advantages of dry toner in a liquid format, making it environmentally friendly and economical. Trillium technology resulted in the small toner particle size of less than 2 microns used in the Xeikon-crafted high viscosity liquid toner. The toner contains no evaporating carriers for a more environmentally conscious print production process that also mechanically recycles the majority of the carrier liquid.
Biomaterial derived carrier liquids have been identified, further increasing the sustainability of this new technology. As tested by INGEDE, printed materials are perfectly de-inkable on the Trillium press.
Another benefit is Trillium’s Microgapping process. The initial 5 micron development gap means that toner particles easily transfer from one roller to the other with extreme precision and at a very high speed as the substrate progresses through the imaging process. This improves register and image quality and creates increased density stability.
Trillium One is the culmination of Xeikon’s three pillars of operation in imaging, where the focus is on improving speed combined with print quality, in toners and in workflow.
Shipping of the Trillium One will start from Q2 2017.
Comment below to have your say on this story.
If you have a news story or tip-off, get in touch at editorial@sprinter.com.au.
Sign up to the Sprinter newsletter