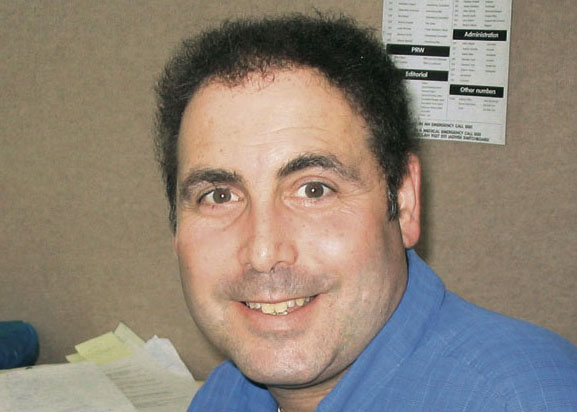
When WorkSafe Victoria launched a series of TV commercials last year, viewers sat up and took notice because it wasn’t the usual “lecture” from public organisations. The ads were not even based in workplaces, but in family homes, and focused on Australians reuniting after a day spent earning a dollar. The tagline of each of these mini-plots, involving concerned loved ones or near-misses at the plant, was “The most important reason for workplace safety is not at work at all”.
When we read news reports of workplace tragedies, we have a momentary empathy for those involved, but then we turn the page, while families are burdened, sometimes by a lifetime of anguish, and often financial hardship.
Earlier this year, Melbourne’s Herald-Sun reported on the death of an 18-year-old man entangled in a printing machine at a local carton plant. He had suffered severe injuries after an accident with a box printer at Advanced Cartons in Thomastown. He was taken to Royal Melbourne Hospital, where he later died.
WorkSafe Victoria’s CEO, John Merritt, told the newspaper that every employer should be meeting with their staff about known or predictable safety issues, then develop and implement a safety improvement plan.
Without reflecting on the particulars of the Advanced Cartons case, it is interesting to go back to 2007, when Merritt was emphatic about unguarded machinery, in an article posted on WorkSafe’s website.
“There are no excuses for unguarded machines. These are problems that can often be resolved on site for little or no cost, but ensuring it happens has enormous benefits. WorkSafe inspectors deal with businesses operating unguarded machinery every day. Sometimes it’s in response to a person being injured, other times it is a risk factor.
“Unless action is taken to eliminate the risk before someone is hurt, we will apply the law. Apart from a person being hurt, the ability to get or maintain contracts can be affected, staff turnover can rise and the business’s reputation can be undermined. It will always be much better for everyone involved to assess and eliminate their workplace’s hazards early than to do it after the event.”
In fact, WorkSafe Victoria, like its counterparts in other states, sets out an employer’s obligations regarding work safety (SEE PANEL).
Tough NSW laws
Tough legislation places the onus squarely on employers. In New South Wales, employers can even be sentenced to prison if found liable in certain cases.
In 2005, when the New South Wales legislation was introduced, it was condemned by Printing Industries, which lodged a submission to the New South Wales government calling for the immediate review of “the onerous requirements” of the Occupational Health and Safety Act on employers.
Lobbying by the PIAA’s New South Wales division resulted in the New South Wales Government modulating the legislation to allow a defence where there was reasonable excuse for the conduct causing the accident and to allow appeals to the Court of Criminal Appeal.
AMWU concern about national laws
Steve Walsh, national secretary of the printing division of the Australian Manufacturing Workers Union (AMWU), tells ProPrint that his union is keen to see print businesses adopt safety audits of their workplace, and he identifies five key issues health/safety reps supported by the AMWU joining on-site committees, a pro-active approach to hazard management, workforce participation and consultation, training in the workplace, and managerial commitment to health/safety.
“You can’t preach health and safety on the shop floor if managers aren’t committed to it,” says Walsh. “The research shows that where there is involvement of delegates and OH&S reps, and these five steps take place, there is a much better record, and that’s well documented.”
Walsh sees “marginal improvement” in recent years but asserts that the printing industry in Australia “does not treat health and safety with the same sort of importance that other industries do, and that’s an issue the industry needs to tackle. There are good examples of [health/safety management] in individual workplaces, but I’m talking about the industry in general”.
He is concerned that the economic downturn will deter employers from doing all they can do ensure a healthy and safe work environment. “Our experience over the past six months is that there is a huge emphasis on how we can cut costs and, as a general rule, those things which get cut first are those which don’t seem to improve the bottom line. Yet if employers analyse the costs of health and safety, not only of having workers injured, but other factors, it’s a different story.”
Comment below to have your say on this story.
If you have a news story or tip-off, get in touch at editorial@sprinter.com.au.
Sign up to the Sprinter newsletter