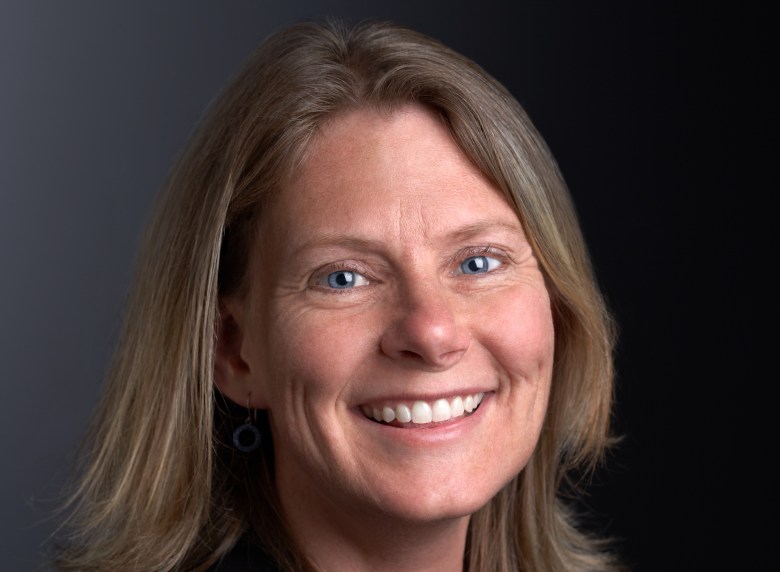
This article was first published in the November 2020 issue of AP – By Kodak plates and CTP product marketing manager Pam Morgan
With a good prepress solution, a printer can offer quality, consistent print to customers in a timely manner at a competitive price. Workflow software is critical for saving time and reducing mistakes in prepress. The best workflow software solutions can automate manual tasks, increase productivity, improve colour and print quality, and drive out costs.
Platesetters are important for ensuring that plates are imaged accurately and get to press quickly with minimal labor and cost. Newer platesetters offer a wide choice of automation and imaging speed options, so printers can find a solution that matches the needs of their business. Plates have a big impact in the pressroom, which is where any downtime and waste can be extremely costly to a printer.
Kodak has a number of solutions that aims to produce results for prepress processes. Kodak is the only supplier worldwide to develop and manufacture an integrated solution comprised of a platesetter, plates and workflow software, backed up by responsive, expert service. Printers can be sure of getting a one-stop CTP solution built from precisely matched components that work reliably for a very long time.
Our CTP portfolio includes a uniquely diverse range of models as well as various automation and speed options, so that printers of any size and specializing in any area are guaranteed to find a Kodak solution tailored to their needs that can be upgraded to reflect future increased productivity and efficiency.
Kodak Prinergy On Demand Workflow brings the power of Prinergy Workflow to the cloud. It helps printers reduce their IT costs, improve productivity, protect their data and workflow against cyberattacks and natural disasters. It also helps printers analyse data to eliminate waste and grow their business.
Kodak Sonora Xtra Process Free Plates are the latest generation of process free plates, offering greater image contrast, faster imaging speeds, and more robustness. Now nearly every printer is able to reduce costs and waste and be more sustainable by removing plate processing.
The Kodak Magnus Q800 Platesetter is now the world’s fastest eight-page CTP device with the new T-speed option, which offers imaging speeds of up to 80 plates per hour. The platesetter is available with an updated Multi-Pallet Loader (MPL) that can keep up with the 80 pph speed and has a capacity of up to 3,200 plates.
All of these solutions enable printers to streamline their platemaking operations, cut labor costs and ensure a consistent, uninterrupted output of high quality press-ready plates.
Printers can take advantage of a great opportunity to improve their business by moving their workflow to the cloud with Prinergy On Demand. With this combination of cloud computing and managed services, printers can eliminate the cost of buying, maintaining, and administering workflow servers, and their system is protected against the growing danger of cybercrime, which can be catastrophic.
Another opportunity is for printers to switch from traditional, wet processed plates to process free plates, where the cost savings are significant.
Printers who are still running older prepress systems should consider investing in CTP devices with more automation, faster imaging speeds, up-to-date hardware and software compatibility to lower operating costs.
The ROI for a new CTP system can be significant because often printers are able to replace two aging devices with one new device and still produce more plates in a shorter amount of time because of faster imaging speeds and increased automation. New prepress equipment keeps the presses running because there is less downtime to service the equipment or replace parts. In addition, updated workflow hardware and software protects businesses from hackers and malware.
In the future, prepress will become faster and more efficient with more automated and fewer manual touchpoints for files, equipment, and plates. With the elimination of plate processing, some printers using Sonora Plates have been able to move their platesetters onto the pressroom floor to be closer to the press, and with Prinergy On Demand, workflow operators are now able to work remotely from their homes or other sites.
Therefore, in the future as prepress becomes more automated and remote, there may not be a dedicated “prepress space” at all.
Comment below to have your say on this story.
If you have a news story or tip-off, get in touch at editorial@sprinter.com.au.
Sign up to the Sprinter newsletter