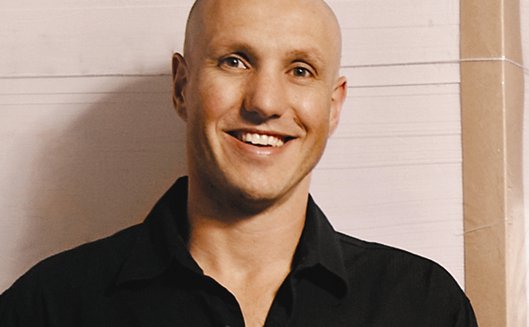
Andrew Cester, managing director of Whirlwind Print has just come back from drupa, and says, “I would not be surprised if everyone who visited drupa is already missing the snitzels, kransky and steins, after such an amazing trade fair this year. I have returned from the fair inspired by so many great print innovations on the horizon. It can be easy to lose sight of how exciting the print business is when you are busy with general operations, so it is great to experience drupa firsthand and see the fair breathe new life into the industry. I am already looking forward to 2020 when they do it all over again.” S
This drupa has also given Cester renewed confidence that the company is doing a lot right at Whirlwind. Rather than focusing on the somewhat isolated nature of operating down under, he is looking to the future needs of the clients. “With our distance from the US and European markets, you can be forgiven for thinking Australian printers may not have the latest and greatest tech. I assure you the machines we have got on the floor are at the leading edge internationally, but above and beyond that it is how we use our tools that put us head and shoulders above the rest in our local market.”
Cester strongly believes that if you did business with it five years ago, you would almost not recognise the Whirlwind of today. It is a leaner, smoother, more agile version of itself.
“Our operations are leaner as we have committed ourselves to an ongoing, bottom-up reorganisation of the business. This process has touched everything from optimising the layout of our factory floor for maximum efficiencies, to how we manage jobs from quote/order, through pre press to print ready, finishing and finally dispatch. Our customers are already seeing the benefit of our streamlined operations with 99 per cent of jobs dispatched accurately and on time.
“Our investment in the software driving our operations has completely smoothed out any bumps associated with being an early adaptor and now we have the benefit of years of development. Every component of our software is tailored to the needs of our customers and Whirlwind operations. Our commitment to deliver the best possible solutions to our customers means that not only do our operations need to be flexible, we are helping our clients become more agile players in the market too.
“The introduction of our web-to-print software w3p allows our clients to tap into the online market, or to meet the needs of their clients who require online print portals.”
Cester’s passion for print and the company is clearly visible. His participation in the group forums discussing market trends and needs of customers as part of the Melbourne Print Group is a reflection of his commitment to, and enthusiasm for the industry.
That passion has been bubbling for 20 years at Whirlwind, in fact it’s the company’s twentieth anniversary this year. “We take great pride in this significant milestone, it is testament of being agile and ever evolving; a necessity in the print landscape now and in the future” Cester says.
The company has come a long way in the past 20 years. In 1996 Whirlwind was formed as a design agency, and as any printer knows, design clients have high expectations. “We were no different and it was our frustration with the quality of print available at the time that drove us to first produce our own print with the purchase of a Heidelberg CD74 5 colour machine. Word got out and within two short years our print work overtook our design work, and we decided to solely focus on trade printing. Fast-forward to 2016 and we have the best technology available, we have clocked over one million jobs, and we are currently powering through over 2000 jobs per week. That really puts the 99 per cent accuracy into perspective – it is no small feat.”
Behind the scenes the Whirlwind team of more than 140 people stretches across Victoria, New South Wales and Queensland. At the forefront is the Account Management team, who directly support their customers every day. “This is a major point of difference, with no other trade printer offering such a comprehensive account management service. Our account managers are backed up by our Estimating, PrePress and Production teams, who ensure the work flows smoothly from quotation, print ready artwork to dispatch.
“Our team is so important when it comes to delivering exceptional customer service, and our success can be attributed to investing in our staff. Happy employees equals happy customers and we see a direct commercial benefit. Fresh fruit daily, filtered water, onsite gym, a new recreation room being installed, training opportunities both onsite (with a company-wide Cert 4 initiative) and offsite activities. Not to mention the coffee machines, or the coffee van that is here every day – we know what is important. A physically and mentally healthy workplace and people creates the optimum platform to deliver world-class service.”
“To understand how to better service our customers, we love it when we are invited to visit, to see where they work and how their business functions. We often reciprocate with tours of our production facility, it is the best way to demonstrate how jobs flow through and it visually highlights what we can deliver: A warehouse full of indented stocks (providing cost efficiencies on even premium stock choices). Our imposition room churning out plates – showcasing our world-class print optimisation, which saves clients time and money. And our lean manufacturing principles at every machine point across the floor, from the HUV 8-colour press to the stitching lines, ensuring our stringent quality control and swift TATs are adhered to.”
The buzz on the floor, the hum of the machines and the methodical approach of staff as they work embodies what Whirlwind is all about. “To maintain our service levels – from our customer connections to our print deliveries, we are always investigating what new opportunities lie ahead. We talk to our customers, analyse job data through our MIS, and attend industry events and trade shows such as drupa (the highlight of 2016 to date). “drupa provided some much needed invigoration to the industry and provided some great insights as to what the future holds for printers in Australia,” says Cester. “We are investigating new machinery from print to finishing, anticipating the needs of the local market and determining where our next point of growth and competiveness should lie.”
Whirlwind is currently measuring the company performance through its biannual customer survey, which will identify any areas where they may better serve their customers. All current customers who have not received a survey are invited to request a link to complete it via whirlwindprint.com/survey. For new customers it is a great time to experience Whirlwind’s service first hand with their 20 year anniversary promotions: to join in visit whirlwindprint.com/20years
The tech: Digital & offset machine specs / finishing capabilities, see below for details.
Offset
A1 10 colour Komori Perfector
A1 Komori 840 HUV Perfector
Digital
HP Indigo
Fuji Xerox iGen150
Finishing
Guillotining
Binding
Folding
Laminating
Creasing
Drilling
Formecutting
Perforating
Padding
Gluing
Gumming
Saddle stitching
Round cornering
Embossing
Shrink wrapping
Collating
Mounting
Numbering
Comment below to have your say on this story.
If you have a news story or tip-off, get in touch at editorial@sprinter.com.au.
Sign up to the Sprinter newsletter