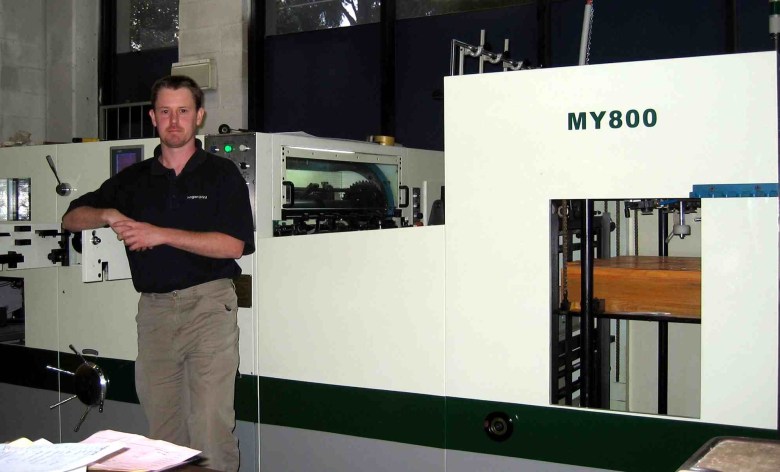
When you’re on a good thing, stick to it, goes the saying. When it was time for Hogan Print in Sydney to update its diecutting requirements, it turned to Graffica, the supplier from which it has sourced other production equipment.
Based at Artarmon, Hogan Print is a 30-year-old family business run by brothers Mark and Andrew Hogan with their cousins Peter and Tim Hogan. The company, which has been operating for three generations, was founded by Mark and Andrew’s grandfather, who soon ushered their father and uncle into the business.
Today the company utilises about 12 staff in a commercial printing operation that specialises in folders, brochures, and general commercial work. Because all its work is done on the premises, Hogan Print can offer its customers low costs and rapid delivery times, says co-owner Mark Hogan (pictured).
To keep its workflow inhouse, the company has made a considerable investment in technology, with a Heidelberg computer-to-plate system, and a new five-colour Speedmaster 74, which was added this year to augment the existing offset line-up, a two-colour Speedmaster 52 and a single-colour GTO.
Hogan’s has also beefed up its bindery, with an MBO and a G&K folder, a Sheridan stitcher and a Tauler laminator. Meanwhile, a Toppy pile turner from Graffica, which Hogan Print bought three years ago, has made the nearline workflow far more productive.
But what was missing from the equation was some state-of-the-art diecutting equipment, says Mark Hogan. “We were using a Heidelberg Cylinder but it wasn’t able to keep up and was creating a bottleneck in our production flow. We had all brand new technology and we were using a 1950s-era diecutter — it just didn’t add up.
“We were using it to score jobs such as presentation folders, top-cutting stickers, basically the full range of diecutting. But the sheer amount of work backing up was becoming a problem, as the Cylinder runs 1,500 to 2,000 an hour, and on any given day we could have around 40 hours of diecutting in there, waiting to be done, so we needed something faster.”
Hogan and his team searched comprehensively for a more up-to-date solution and took a close look at some of the top European brands of automatic diecutting equipment, but their search led them back to Graffica.
“It came down to size and cost,” he says, explaining the process that led to the company investing in a Yuyin MY800 diecutter-creaser supplied by Graffica. “It’s really fantastic value for money.”
Since taking delivery of the MY800 in February this year, Hogan says the machine has made a significant impact on production. “It alleviated what was a bottleneck because it is constantly running, and doing so without drama. It’s easy to set up, and it runs efficiently on any kind of board. We’ve used heavy board that’s been celloglazed or 200gsm material — it all goes through.”
The MY800’s straight feed-through path offers smooth operating conditions that enable it to be used at high speeds without crashes, he says, unlike the older S-shaped feeds well known in the industry.
“It’s an oval-shaped ‘chain’ configuration that stops and starts as the material moves through. It will move through, say, 20 per cent of its cycle, stop, the platen comes up, diecuts, then it moves on and drops the sheet. It’s a very straight, smooth path, whereas before, you’d be putting so many nicks into a forme to keep the sheet from falling apart. Now you rarely nick a forme.”
So far, Hogan’s has not drawn in new diecutting business, just made shorter work of the existing loads coming through. “Space is at a premium here. The equivalent of the MY800 would have to be another two Cylinders, so we can get that kind of speed with a much smaller footprint. You’re getting three times what you can load into a Cylinder. You can just get that much more into the Yuyin’s feeder and delivery.”
The work that Hogan’s is processing through the MY800 includes diecutting folders. As we speak, Mark Hogan is diecutting a batch of sample folders, to be followed by a scoring operation on a 150gsm gatefold with a solid black, which needs to be scored to prevent cracking. After that, the MY800 will be top-cutting a batch of stickers. “That’s just this morning’s work,” he says.
Graffica’s managing director, Neil Southerington, says the MY800, manufactured by Yuyin Company in China, enables an almost nickless job without lumps and furry perimeters. In addition, pallet loading and continuous feeder and delivery maximise sheet numbers.
He also cites operator-ease — Cylinder operators will quickly pick up the operation of the MY800, he says. “It’s an all-round value proposition.”
Comment below to have your say on this story.
If you have a news story or tip-off, get in touch at editorial@sprinter.com.au.
Sign up to the Sprinter newsletter