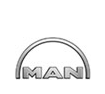
It’s the endless search for an advantage, a step forward, a gain in performance that drives athletes and artists. It also drives printers in their own marathon of boosting efficiencies to find higher productivity and so, hopefully, profitability.
High-volume production print centres long ago found that investment in wider web widths brought higher productivity, although the greater widths also brought their own inherent technical problems. But there has been a trend in the last couple of decades of going wider to boost production numbers. It has been a largely successful migration, especially in Europe and to an extent, in Australia.
And so there’s been a swell in the variation in web widths, each of which provides distinct advantages in both product format and print volume. MAN Roland has now developed what it considers to be the ideal press for A4 page production – a LITHOMAN with a web width of 2,250mm, or a signature of 80 A4 pages.
Germany goes first
In November 2007, German print company J Fink started production on the first MAN Roland LITHOMAN press with a web width of 2,250mm, for 80 DIN A4 pages per cylinder revolution.
This was, according to Eugen Gansser, managing director of J Fink, a mammoth project from the very beginning. It all started at Ipex 2006 in Birmingham in discussions between MAN Roland and the production manager of J Fink about how web widths in high volume commercial web offset printing would develop. The two companies had enjoyed a very positive long-term relationship for many years and it was agreed that they should embark on another joint project to boost production efficiency. MAN Roland developed and built a LITHOMAN in a new performance class in just 13 months – – a web width of 2,250mm, a cylinder circumference of 1,240mm, and a maximum output of 3.2 million four-colour DIN A4 pages per hour.
Herr Gansser stated at the official opening of the new press line at J Fink, “Thanks to German engineering artistry from Augsburg it has been possible for web widths to be increased from 0.965 metres to 2.25 metres over the past 32 years. Fink has invested some 40 million euros in the last two years, and this is an expression of confidence and a sense of responsibility towards the company’s staff … globalisation and fragmentation demand catalogues and other products that can be optimally produced on an 80-page press.”
More than two metres
“Productivity lies in web width,” MAN Roland delegate to MAN Ferrostaal in Australia, Dietmar Zutt, told ProPrint. “Before this press printers could find 2,000mm and 2,060mm web widths, but they weren’t a pure 80-page A4 press. For a true 80-page A4 press you really need a 2,250mm web.
“In competition with other printers you can differentiate with either value added printing – you can produce certain products differently from your competitors – or you can produce work more efficiently than others. For example, to look at these efficiencies, if you move from a 48-page press to a 64-page press you increase the productivity by 50 per cent, but you increase the investment by just 15 per cent or so, so that’s possibly a profitable alternative.
“The market itself – customers in the publishing market – are also seeking to differentiate themselves in different formats, and in Europe, more so than here, that can be achieved with different kinds of presses. The cylinder circumference defines the height of your product. With the variation in the web width you vary the width of your products. You differentiate yourself with format.”
The market says yes
Alongside the sheer volume of print that a 2,250mm web width can deliver, there is also a corollary benefit in versatility in the style of printed products that can be achieved.
“From a market point of view, these presses are very flexible,” said Dietmar Zutt. “Because of their high productivity and output they are suitable for, on the one hand, long runs. High volume can mean long runs, but it can also mean short runs, where the pagination is high, like magazines and thick product catalogues.
“You can effectively run these presses for 30,000 or 40,000 run jobs – just very short runs – although if you only have short runs like that and you have to fill that press I would say it might not be ideal. It has a wide range where you can go down to smaller runs if the pagination is right – say, a product of 240 pages in a 30,000 run – so basically you would run three times through in three hours, or say four to five hours with makereadies. But if you did the 30,000 on a 16-page press, you would have to run 15 times through, which would take much longer.
“So this new press size is much more productive and the economies of scale show these presses are highly profitable, but you have to be able to fill it. You have to have the volume.”
The 2,250mm web has attracted positive attention from European printers, and has already become a genuine success for MAN Roland.
“There are about six of these presses sold already, in Europe – Germany and Austria,” said Dietmar. “Not in America – America is slow in this respect – you find a lot of single-width presses in America for low pagination, high run length work.
“I think the success of these presses in Europe has proved that even though there are areas around the press where logistical changes are necessary, the economy of scale is worth it. These presses are even seeing work from what was originally the gravure market.
“The number of presses sold is tremendous. That goes for all larger web presses in the last couple of years. A main driver is raising revenue and cutting costs. This 80-page press has an output of three to four other presses in theory, so if you have the right products to fit on it you could shut down three other presses, and find savings in labour as well. If you put work on the new press it might clear production capacity of, say, 50 per cent on other presses so you have greater opportunities as a business.”
More than just width
The MAN Roland LITHOMAN 80-page press features numerous new developments. For the first time moveable operation panels have been integrated into each unit, and a new device simplifies roller handling. Exchanging inking and dampening unit rollers has been made much simpler.
Plate changing has been speeded up with the addition of Power Plate Loading (PPL), allowing automaitc infeeding and clamping of the new plate and release and ejection of the old plate with the web in place. One operator can change the plates on all four double printing units in about ten minutes. The blanket cylinder has been equipped with spindle clamping systems for the front and rear edges so that there is uniform tension on the blanket at all times.
The printing units feature standard film inking and integrated hydromix dampening units. The inking unit has four ink form rollers, two of which oscillate to avoid ghosting. Inking units, folder superstructure and folder units feature automatic presetting options.
The 80-page LITHOMAN features two identical folder units which provide flexible product combinations.
It’s not just the press
Obviously, making the transition into a “two-metre web family” press reverberates right through the plant, in plate production facilities, reel handling, postpress logistics – not to mention the impact on the sales force and planning stages.
“It has to be looked at from a complete point of view,” Dietmar Zutt points out. “For a 64-page press operator, it’s not just the press change, with the increased productvity of the press, when you move to this size web, particularly if you are not already in this size.
“These companies are high industrial production areas so you have a lot of automation in plants, for handling reels and so on. Customers with a 16-page press, for example, will often have manual reel handling – – a guy can roll those webs through the factory, but larger than that you need automated systems, for safety as well as productivity reasons.
“You find in Europe that many printers move directly from a 16-page press to the family of two-metre wide web presses, although not necessarily a width of 2,250mm. It is a big move but a lot of companies are managing it and doing well.
“Production people are always looking for standardisation – that’s natural – while the marketing people are always looking to differentiate themselves, and price is not the only criterion. It needs open communication between them.
“This technology now assists printers to achieve differentiation, and also productivity. It is essential that sales and production in a company are aware of the opportunities that the presses are offering, and then to come up with differentiation possibilities. Problems can be minimised if you do things together early enough in the production cycle. Input from the production department in the sales process can help to reduce problems and create new opportunities.
“A key driver of any print business is always how do you raise revenue and cut costs, and here is an example of productivity and flexibility in an ideal combination of that, and it is the trend to larger web widths. Productivy lies in web width, but you have to look at your product mix, run lengths and paginations, to see if a press like this really fits.
“Not moving ahead is usually a step backwards. On the one hand, we [MAN Roland] are showing that we are moving forward, but on the other hand, we are considering our responsibilities to the press user, and we are not just doing this because big is beautiful.
“The business model must work before we can make this recommendation to move to this web width. From an 80-page press to a 96-page press might be a 20 per cent increase in productivity, but it’s not clear yet that the increase in investment is under 20 per cent, so there may be question marks on that. Of course, we can also assist in consultancy in investment planning for production systems including prepress, press and bindery.”
The local market
Australia’s web capacity is notoriously high, but there is room for new investment here, according to Dietmar Zutt. Capacity alone is not the only consideration.
“There is a lot of web capacity here in Australia, but there is also quite a lot of older gear here which, in terms of flexibility, makeready times, power consumption and productivity, is not state of the art. They are behind what is currently available in web presses,” he declared.
“Australia was always a strong market for longer runs, or shorter runs with high pagination. Australia was always a leading market for high-volume presses. I think there is definitely a market here for these high volume presses because you have a lot of high volume products here, and high pagination products.
“I think Australian printers would find production output versus investment is just the best in this size.”
Comment below to have your say on this story.
If you have a news story or tip-off, get in touch at editorial@sprinter.com.au.
Sign up to the Sprinter newsletter