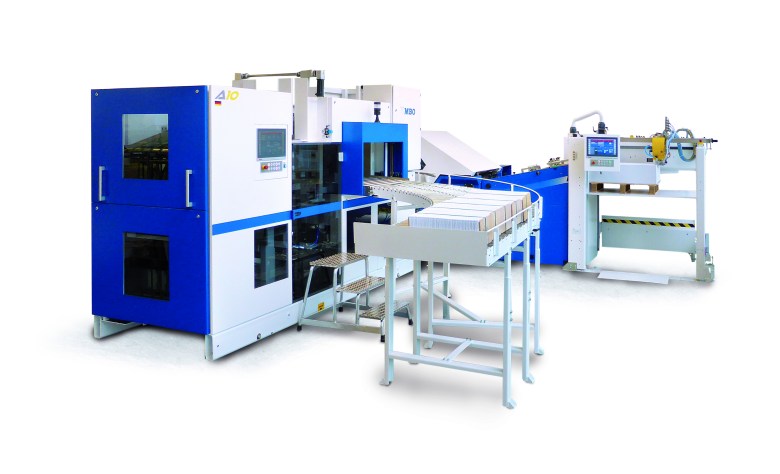
All the drupa exhibitions I have visited – and there are far too many to count – have had a major theme or trend. This year’s show, could well be remembered as the smart show. As was explained by many of the exhibitors, we live in an ever changing world which is becoming increasingly complicated. This is going to provide many opportunities for the printing industry, but it also means that everything is going to have to become more connected and automated, and hence digitised since there will be no option but to produce shorter runs of a greater variety of products at an ever faster rate and higher quality.
This move into what is being called Industry 4.0, or in the case of drupa, Print 4.0, and as far as the bindery is concerned Finishing 4.0, has fortunately come at a time when the cost of motors and sensors have dropped, while computer cloud has become more prevalent and accepted. This not only enables more connectivity and more complex processes to be handled automatically but also more data to be gathered, stored and analysed resulting in more efficient job processing and communication, with both customers and suppliers.
As was obvious at this drupa this trend is affecting all areas of the production process from input to delivery of the finished product, as well as maintenance and servicing. However, where it will have one of the greatest impacts is in the finishing department since the process still tends to be labour intensive, making it time consuming and often a bottleneck. Nor does it help that, despite offering an excellent way of moving out of the commodity zone and adding value, finishing is undervalued and overlooked. It not only comes last in the production process but also when planning the job and when investing in new equipment.
That having been said, there are areas of finishing which have been automated. Bookletmaking was the first to make the move and manufacturers such as Watkiss Automation, Duplo International and Horizon are still leading the way, especially in terms of offering multi-finishing lines. One example is the new Watkiss PowerSquare 160 bookletmaker, a smaller, lower cost version of the 224, which can staple, fold, form and trim in one pass to produce squared backed books in-line – it has JDF/JMF compatibility – near line or off line. It will be available in fourth quarter 2016.
Nor is multi-finishing just being applied to bookletmaking. For example, at drupa, Duplo launched the DiCut 300 on-demand diecutter which performs multiple cuts, slits, scores, perforations and window punches at up to 3,000 cph and includes an x and y automated registration system. Also new from the company is the iSaddle Pro Duetto digital saddle stitcher and the DC-646i JDF multi-finisher which links to HP’s PrintOS open workflow via Duplo’s E-Tandem technology.
Horizon has been demonstrating integrated finishing for a number of drupas. This time round, it included a new book block feeding device for its Smart binding system enabling cut sheets to be fed from its SmartStacker into the binder, plus a new folding technology which enables changing the fold pattern on the fly, all of which are capable of being JDF linked.
In fact, a welcoming trend to be seen at drupa is the willingness of manufacturers to integrate their finishing equipment with those of others. For instance, at drupa, a sheet-feeder from CP Bourg was feeding a Watkiss PowerSquare bookletmaker and a Challenge three-knife trimmer was being fed from the new Bourg sheet Preparation Module, while Hunkeler not only had its finishing equipment linked to digital presses on the stands of HP, Canon, Ricoh, Xerox and Screen, but it was also being demonstrated on the stands of other finishing equipment manufacturers such as Horizon, Muller Martini, Pitney Bowes, Bowe Systec and Meccanotecnica.
The move towards more integration is also leading to more open systems, another good news trend to be seen at drupa since proprietary systems have no place in a networked society where everything needs to be freely linked. Companies which have realised this include Kolbus which has opened up its control systems by putting its XML syntax language on the Internet for free download. This enables it to be used by third party developers as well as its customers for designing their own workflows within which they and their customers can communicate directly with Kolbus systems.
Then, there is HP’s new OneBook, which is described as an end-to-end workflow for producing customised books of any run length. Involving both its PageWide web and Indigo sheet-fed digital presses, it can be used with HP’s SmartStream server-based or PrintOS cloud-based platforms, as well as HP partner workflows. It can also be used to integrate equipment from Horizon, Hunkeler, Kolbus, Manroland Web Systems, Muller Martini, Tecnau and VITS International.
Digital driving force
There is no doubt that digital printing is a driving force in post-press equipment development. One of the most active areas is in the production of digitally printed books where there has been a rise in the number of suppliers of complete, automated systems such as was announced at drupa by Fujifilm. Developed in partnership with EPAC Technology, its robotised book production system covers everything from digital printing through to finishing and order sorting for delivery to book stores or end users, all without human intervention and a claimed zero up-time.
Another company to enter the market is Manroland Web Systems which has high hopes for its FormerLine business, as well as for its FoldLine system for finishing newspapers. Based on web offset press folding technology, these are controlled and managed by software also developed in-house for pre-setting, processing and job management. So far, the presses involved have come from Kodak and HP, and the number of systems ordered/installed globally is 20, the latest order coming from Guam where the FoldLine demonstrated a drupa will be used to finish the 20,000 circulation digitally printed Pacific Daily News newspaper which is published by Gannett.
Then there is Muller Martini which at drupa demonstrated how its equipment can produce a variety of publications including books from a mixture of digitally and offset printed sections with on the fly format and pagination changes in runs down one. The publications can then be sorted into the ideal sequence for delivery.
As Muller Martini CEO Bruno Muller explained, the company believes that short-run printed products with variable pagination, content and formats can only be produced economically in fully integrated workflows. In other words, Finishing 4.0.
As well as its Sigmaline digital book production system with its on the fly changing capabilities and higher speed, Muller also showed the new Primera MC saddle stitcher which uses Motion Control technology to reduce job processing times; a digital version of the Allegro adhesive binder capable of varying book block thickness and dynamic job change; and the InfiniTrim three knife trimmer which enables format and thickness changes for each book.
In fact, in total, the company linked nine finishing systems including inserters, binders, book sewing machines and saddle stitchers. These were all controlled by its Connex data and process management system which can also interface to Heidelberg’s Prinect, HP’s SmartStream Production Centre and Enfocus’ Switch workflows. In addition, Muller has expanded Connex to enable it to collect data and feed it to servers to improve equipment diagnosis, maintenance and servicing, especially now that remote access is available. In addition, it introduced MPower, a customer portal for resolving technical issues.
Similar digital book production capabilities were being demonstrated by Kolbus at Drupa with its KM 200 Bookjet system and what the company described as 3D format as well as page variation, all without stopping for make-ready. This was achieved using the KM 200 adhesive binder linked to the HD-HD 143 three-knife trimmer which can trim books of different thickness, height and width on a book by book basis at up to 1,000 cph and without stopping for format adjustments.
Upping productivity
In fact, encouragingly, drupa demonstrated that automation and hence productivity of finishing equipment overall is on the increase. For example, Ferag had two main demonstrations on its Drupa stand. One involved the personalisation of advertising leaflets and brochures with bundles sorted according to delivery route sequence at up to 30,000 cph.
“Nowadays, advertising really cannot be personal enough”, explains Ferag’s CEO, Jurg Mockli. “In future, advertising and direct mail products will be targeted more and more directly at individuals and their needs.” He added, “A personalised process needs to run without any errors whatsoever.”
To achieve this the Ferag line consisted of an Easysert inserter, an inkjet addressing unit, a UTR conveyor and a new loop which Ferag claims guarantees 100 per cent accuracy in the collecting process. It was driven by the Navigator planning and control software which processes the distribution data and automatically controls the personalised inserting, while the optional Optimizer software can calculate the best way to operate the line.
The Navigator software was also used to control the new One2Out system for pre-collating up 41 advertising brochures and inserts at up to 40,000 cph: to save costs, one of the brochures is folded into a jacket and the remaining products are automatically inserted into this jacket to form one marketing package. Again, the line had a loop which enabled it to be run as two parallel lines with up to 21 hoppers each, both operated by the same personnel.
Increasing productivity is also the name of the game when it comes to folding machines. Good examples of this could be seen on MBO’s stand where it was demonstrating amongst its 12 different finishing lines how three types of new stackers – the A10 log stacker, the A700 automated stacker and the A7 digital signature stacker – can increase output. For instance, the company has paired the A10 with the new K10 folder to form the LeMans signature processing system which can fold signatures at over 20,000 sph automatically. Alternatively, the A10 can be paired with the new web-fed K8-RS Digi-folder to form the Monza signature processing system making it a one man operation.
Another interesting idea could be seen on the Stahl stand in the form of the latest generation of Stahl folders, the TH/KH 82-P series. Aimed at industrialised commercial printers and bookbinders, they can produce up to 16,000 16-page A4 sections an hour due to the use of the PFX shingled sheet-feeder and a sheet guide which permits shingled folding through the machine. In other words, 50 per cent more sheets can be processed in the same time without increasing the 150 m/min speed at which they are transported, thus reducing the number of folders required to handle the work coming off the new fast sheet-fed presses.
In fact, as is pointed out by Mark Hogan, head of sales for post-press at Heidelberg, it should be the bindery which determines the volume.
He says, “There is no point in putting massive capacity in the pressroom if it creates a huge bottleneck in the bindery. If you cannot invoice, what’s the point?”
Hogan believes that overall finishing equipment will never be as automated as presses where eventually everything will be activated by pressing a single button. However, as could be seen at drupa, significant strides have already been taken enabling post-press equipment to become that much smarter.
Comment below to have your say on this story.
If you have a news story or tip-off, get in touch at editorial@sprinter.com.au.
Sign up to the Sprinter newsletter