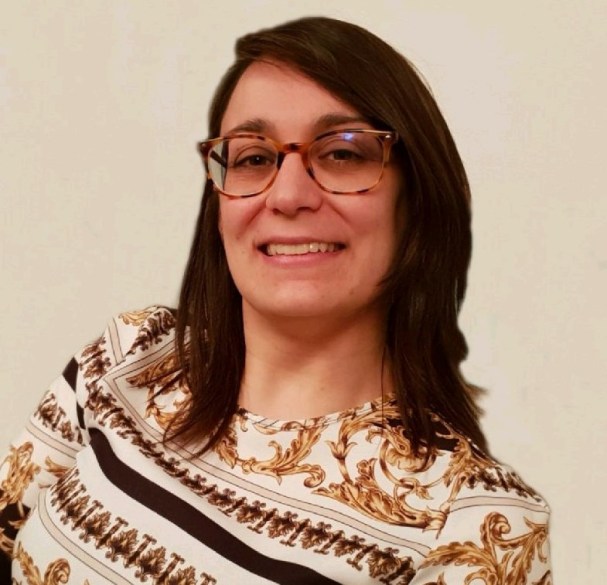
This is an extract about EFI from the Textile Printing Technology Focus which was published in the June 2022 issue of ProPrint. To read the full story click here.
Growth in digital textile printing will continue to grow at an accelerating pace, says Micol Gamba, product marketing manager, EFI Reggiani – EFI’s inkjet textile partnership.
“The regions that traditionally dominate industrial textile production face an increased demand for faster turnaround times and shorter job lots with more design versatility and significant sustainability challenges and increasing labour costs that altogether are driving digital adoption,” she said.
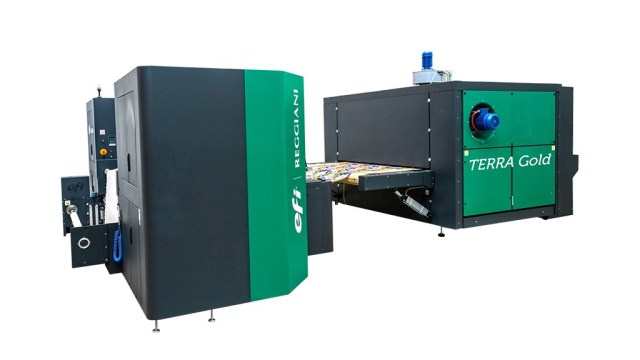
“At the same time, other regions – places that have long had very limited textile manufacturing – are seeing the ways digital enables near and re-shoring. This is a sustainability-driven vision as well and the result is that we will see more digital printing being done, in more places.”
Gamba says industry data reflects what EFI Reggiani and its customers are witnessing in terms of growth. Digital textile printing, as well as the textile and printing industries overall, had a slowdown during the pandemic, but digital textile is expanding again.
“For instance, World Textile Information Network in its 2021 Digital Textile Industry Review projects a CAGR of nine per cent growth from 2019-26, and other sources predict even superior growth rates, like the research group Smithers, which states that digital textile printing will have a 13.9 per cent CAGR from 2021-26,” she said.
We asked Gamba how she thinks fast fashion is revolutionising the fashion industry in terms of shorter cycles and seasons – and what impact this will have for on-demand textile printing in Australia.
“The trends that began with fast fashion retailers are becoming more of a model for the apparel industry at large,” she notes. “In an apparel industry that has traditionally suffered from overproduction of designs because of difficulties in predicting demand, apparel companies are more focused on having more accurate predictions. That is important from a financial standpoint because apparel companies wish to reduce the number of designs that are overproduced and then sold at a discount or never at all. As demand forecasting improves, EFI Reggiani customers have the important responsibility of reducing the time it takes to produce new designs,” Gamba said.
“We are, however, spotting an additional trend – on-demand personalisation. The request for increased personalisation and customisation is increasing in Europe and North America, and we believe this can have a positive impact on Australia as well. In fact, while Australia has relatively easy access to imported apparel and textile goods, on-demand textile printing and the near-shoring movement in textiles may increase in the future, thanks to green and short printing processes like dye-sub and pigment printing.”
Gamba says tradeshows and events represent a significant portion of soft signage demand and while these markets were heavily impacted by COVID, the long-term trend is all about growth.
“Most of the vinyl printed displays you would have seen at a tradeshow in 2012 is printed on fabric today. EFI’s Display Graphics business has been a leader in helping printing companies capture that growth trend,” Gamba said.
She adds EFI’s VUTEk FabriVU printers and other EFI dispersed dye-sublimation printers leverage some of EFI Reggiani’s innovations so customers can confidently and efficiently deliver high quality
soft signage graphics. Décor textile printing, such as upholstery and wall coverings, is a strong and growing opportunity.
Delving into EFI Reggiani’s direct-to-fabric (DTF) range, Gamba says the recently launched EFI Reggiani BLAZE printer is an easy-to-use solution for businesses taking their first steps into industrial digital textile printing.
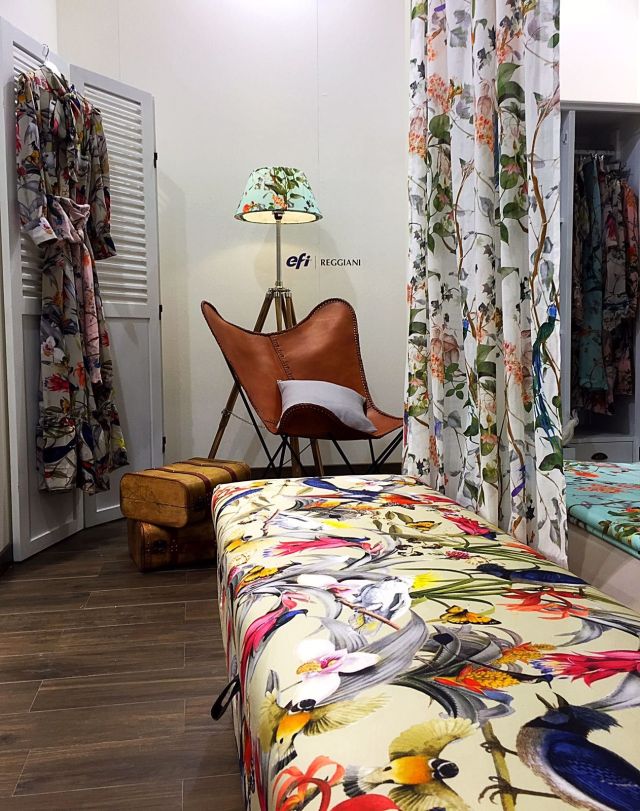
“Some of our newest printers, such as the EFI Reggiani TERRA Silver, leverage our proprietary pigment technology with inline polymerisation. This offering can simplify the production process for anyone new to textile production. Both the TERRA Silver and the BLAZE printers are good industrial entry solutions for manufacturers moving into the textile industry,” she said.
EFI Reggiani’s NEXT press is a digital solution for sublimation printing on paper and non-elastic fabrics which Gamba says will revolutionise fashion, sportswear and home décor markets with its combination of cost effectiveness, speed and quality.
Higher-volume production models include the EFI Reggiani VOGUE, which offers accurate fabric handling and energy-efficient production, and the EFI Reggiani COLORS, a textile printer which utilises up to 12 colours in a row to extend gamut and depth, increase penetration and enhance printing quality and uniformity.
Taking another step up in productivity is the EFI Reggiani POWER – the top seller in the EFI Reggiani range. “With its outstanding performance, extended uptime and low maintenance needs, the POWER is the perfect industrial textile digital printer to increase your productivity and printing capability, without compromising on quality or flexibility,” says Gamba.
She adds the new EFI Reggiani HYPER is the fastest scan digital textile printer in the market, adding its 72 new print heads and EFI Reggiani’s legacy continuous-ink recirculation system make it a champion for uptime and reliability.
Gamba goes on to say the award-winning EFI Reggiani BOLT single-pass solution is said to be the world’s fastest industrial textile printer with speeds up to 90 metres per minute.
“It can not only perform at analogue rotary screen printer speeds, but also enables digital printing quality at an unparalleled speed. The Reggiani BOLT also delivers high uptime thanks to minimum maintenance at start up and during production. The BOLT printer expands the design possibilities offered by single-pass technology.”
In terms of inks, Gamba says the EFI Reggiani TERRA line of water-based pigment inks with binders eliminate the need for steaming or washing on DTF applications, using a greener, more efficient polymerisation process that takes place as the printed textile goes through the printer’s on-board dryer.
“As a result, users can achieve superior printing results while using less time, water and energy,” she says.
For more information, visit EFI.
Comment below to have your say on this story.
If you have a news story or tip-off, get in touch at editorial@sprinter.com.au.
Sign up to the Sprinter newsletter