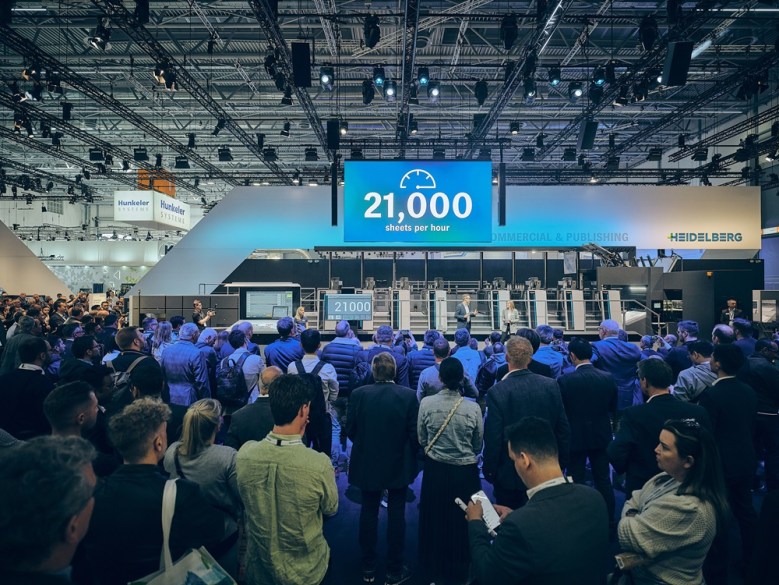
drupa 2024, held in Düsseldorf from May 28 to June 7 this year, marked its first on-site event in eight years since 2016.
The 11-day event attracted exhibitors from 1,643 companies across 52 countries and saw a turnout of 170,000 visitors.
The Heidelberg booth in Hall 1 was a hub of activity, with many visitors attending daily presentations focused on commercial, packaging, and label printing.
Heidelberg’s focus at drupa was on four key messages based on market megatrends and promoting solutions through innovation, including:
- Competitiveness: Productivity increased by up to 20 per cent, significantly reducing print shop costs.
- Skills shortage: Reduced staffing needs in print production, through autonomous printing and cluster production.
- Sustainability: New technologies that save energy and reduce raw material consumption.
- Digitalisation: Integration of the
entire production process within the printing industry.
The printing industry faces four significant challenges: increased cost pressures, a shortage of skilled workers, and rising demands for sustainability and digitalisation. To address these megatrends, Heidelberg unveiled numerous innovations at drupa under the theme ‘Unfold Your Potential’ — focusing on optimising businesses to maximise potential using the latest technologies and services. Innovations such as the new generation Speedmaster XL 106 enable Heidelberg to support customers with a holistic concept that achieves up to 20 per cent higher productivity compared to previous solutions.
How can the printing businesses enhance production efficiency?
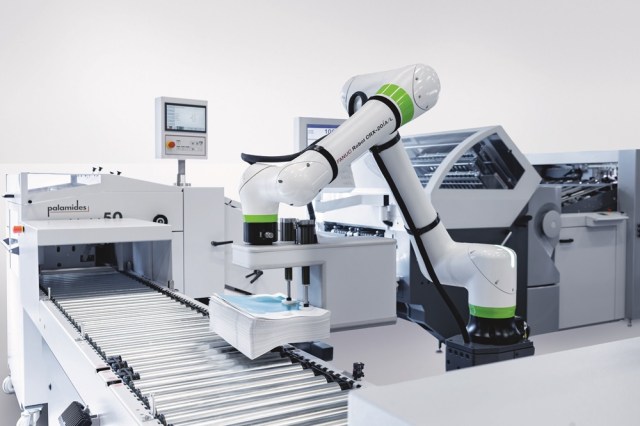
With rising cost pressures, print shops need to invest in productivity, efficiency, and new business areas to stay competitive. Heidelberg understands the value drivers of its customers in the commercial and packaging printing industries and develops optimal products to adapt to market changes.
For example, innovations like the new generation Speedmaster XL 106, with a printing speed of up to 21,000 sheets per hour, AI-assisted systems, and enhanced push to stop functionality, make industrial offset printing more competitive.
Heidelberg also displayed new innovations for the packaging printing industry at drupa, such as the Boardmaster, setting new productivity standards with up to 90 per cent machine utilisation and a top printing speed of 600 metres per minute. Compared to previous generations, this machine concept dramatically reduces the total cost of ownership for industrial packaging production.
With rising cost pressures, print shops need to invest in productivity, efficiency, and new business areas to stay competitive. Heidelberg understands the value drivers of its customers in the commercial and packaging printing industries and develops optimal products to adapt to market changes.
How do print shops address skills shortage?
The printing industry is increasingly facing a severe shortage of labour and skilled workers. In response, Heidelberg offers automated product and process solutions and provides training for print shop staff. In commercial printing, fully automated plate to unit plate logistics on the Speedmaster XL 106 and the new robotics solutions for postpress operations are two examples of this.
The new-generation Speedmaster XL 106 also supports cluster production, whereby a single operator controls an entire machine park. Heidelberg plans to enable autonomous printing for standardised packaging applications and will continue to support complex printing jobs with navigated user guidance.
How can the printing industry produce sustainably and economically?
Sustainability is a global megatrend and a significant challenge for the industry. Modern print shops aim for sustainability by reducing energy and resource consumption. Print products are also changing, though moving away from plastic and toward more paper.
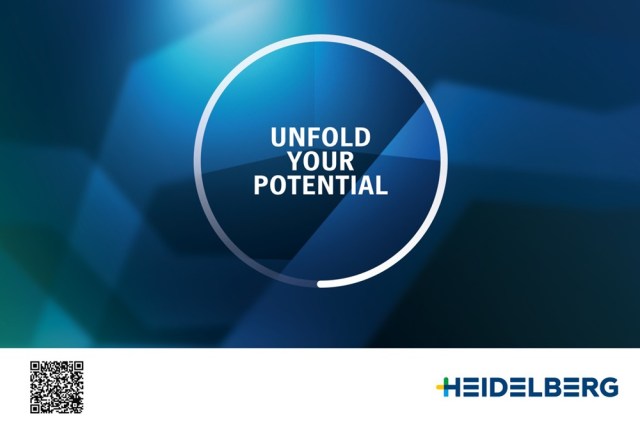
Heidelberg offers sustainable print solutions that help save energy and raw materials. Comparing the 1990 Speedmaster with the current version shows up to a 40 per cent reduction in energy consumption per 1,000 sheets.
At drupa, Heidelberg announced the latest generation presses could produce up to 21,000 sheets per hour, further reducing per-sheet energy consumption. Moreover, the use of artificial intelligence and new auxiliary systems reduces paper waste, saving even more resources.
How does digitalisation benefit the printing industry?
Digitalisation in the printing industry enables the integration of the entire production process, from receiving digital customer orders to preparing print data, planning and executing print jobs, delivering printed products for postpress, shipping, and billing. At drupa, Heidelberg showcased end-to-end autonomous printing for commercial and packaging customers. The introduction of a new customer portal elevates digitalization to the next level, enhancing press management, including capacity management, maintenance, and servicing.
The printing industry is increasingly facing a severe shortage of labour and skilled workers. In response, Heidelberg offers automated product and process solutions and provides training for print shop staff.
New Speedmaster XL Unveiled
Eighty per cent of print shops consider maintaining competitiveness their greatest challenge, while 70 per cent are concerned about labour market issues. Addressing increased cost pressures and labour shortages, the demonstration of the Speedmaster XL 106 at drupa emphasised reducing manual tasks from 20,000 to just 400 per day.
In commercial printing, the elimination of 98 per cent of manual interventions from production data to finished brochures in the value chain is achieved compared to non-push to stop production. In packaging printing, the numerous innovations in the Speedmaster XL 106 enhance overall productivity by up to 20 per cent, while simultaneously reducing labour, paper waste, and energy consumption. This results in lower costs per print sheet, becoming a critical competitive factor for print shops.
In partnership with POLAR and MK Masterwork, Heidelberg addresses the most pressing challenges facing industrial printers, including cost pressure, skills shortages, sustainability, and digitalisation.
Productivity – innovations in postpress achieve 1:1 performance ratio
Additionally, the new highly automated Peak Performance generation of the Stahlfolder TH 82-P folding machine restores a 1:1 performance ratio between pressroom and postpress operation. This means that the new Stahlfolder TH 82-P can handle the full output of the new generation Speedmaster XL 106 at the postpress stage. The new Stahlfolder TH 82-P generation offers approximately a 15 per cent net output increase without increasing the machine speed. Moreover, the new collaborative robot system, StackStar C, reduces staff burden by automatically stacking products in the postpress section.
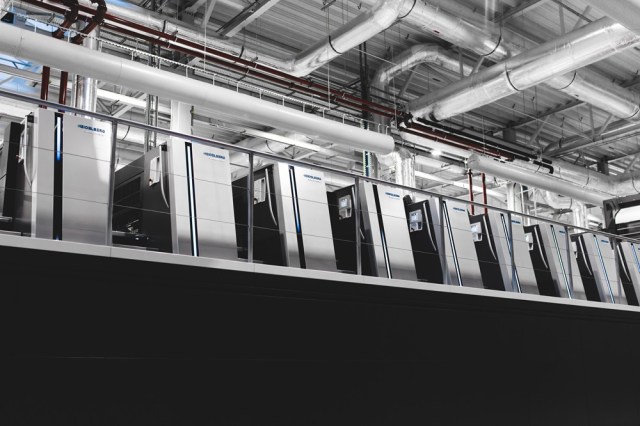
The StackStar C is mobile and can be easily moved between different machines. Operating collaboratively, it features an innovative safety concept that eliminates the need for safety fences, allowing staff and the robot system to work together safely. Additionally, quality control processes can be conducted during production without stopping the robot. By linking two StackStar C units, production capacity can be doubled, with various stacking patterns and pallet sizes intuitively selectable from the control terminal.
“Enhanced automation and process efficiency enable our commercial printing customers to increase productivity while reducing resource usage. This way, we help them further enhance their competitiveness for the future,” said Dr. Frank Schaum, who is in charge of the print segment at Heidelberg.
Digitalisation – fully automated job processing and avoiding waste
Heidelberg also offers digitalisation solutions that elevate automation to a new level using the Prinect workflow system. For instance, Prinect provides additional data to many assistance systems and operates using artificial intelligence. Many new and enhanced digitalisation features, such as Intellistart 3, reduce operations at the Press Center by about 70 per cent, while the improved Color Assistant Pro system achieves fully automatic ink presetting, preventing operational errors.
This reduces makeready times by up to four minutes and cuts paper waste by 100–150 sheets per job. Combined with the inline Prinect Inpress Control measurement system and automated delivery logistics, inline waste is eliminated. This provides waste-free stacks for post-press operations, enhancing overall process efficiency.
Heidelberg displayed new innovations for the packaging printing industry at drupa, such as the Boardmaster, setting new productivity standards with up to 90 per cent machine utilisation and a top printing speed of 600 metres per minute.
The need to reduce operator workload whilst achieving higher output with fewer staff, and lower costs is required. This is achieved with advanced automation technology, digital workflow integration, and intelligent operator assistance systems. As maximising existing potential becomes increasingly important, digital integration and automation make production more economical than ever. Heidelberg recognised these needs at drupa with innovation and technology to suit the industry moving forward.
This was first published in the October edition of ProPrint magazine. Read the original article here.
Comment below to have your say on this story.
If you have a news story or tip-off, get in touch at editorial@sprinter.com.au.
Sign up to the Sprinter newsletter