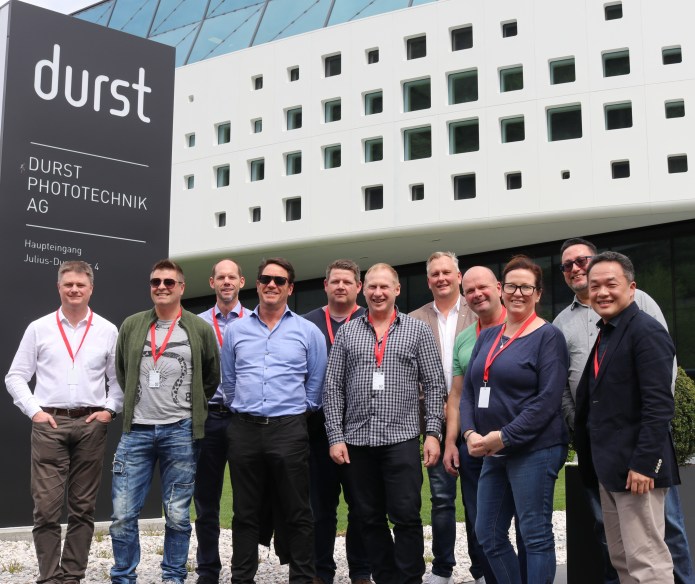
The first impression you get after walking into the new Durst factory in Brixen, South Tyrol, is that this is a company that gets the details right. The tour features locally bottled spring water, chocolates from Loacker, an Italian-wafer company which also manufactures in the region, along with cured meats and cheeses sourced from a local deli.
It is all part of the Durst story, a manufacturing business set against the backdrop of the Alps, producing only top-tier equipment, with an unabashed focus on quality.
Matt Ashman, sales manager Australia and New Zealand, Durst, took the group of 14 through the site, including stops in the historic old town, where the attendees admired the architecture and history of the dual German/Italian city.
The Durst building itself is immense – 850 multi-coloured luminous windows cover the exterior. On the inside, a custom-cut staircase above the building’s reception, which features its own barista, takes you to the higher floors, where you can see the local childrens’ attempts to capture the building on a blackboard with chalk.
The first stop on the tour is an introduction to the company’s origins. Durst began production in Brixen in 1934, with its specialty being photographic devices and cameras. Making its name with a camera patent, the company has always operated in the high-end imaging space.
Perfecting production
To have complete control of its production line, Durst manufactures all of its metal parts and aluminium for the printers in-house from aircraft-grade materials.
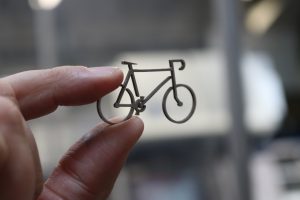
The fully-automated Robotic Bender takes steel sheets up to 10mm thick from the magazine, places them, and then cuts them with a plasma laser, with what Ashman calls, “supreme accuracy”. The parts come off finished and ready, and are delivered through a conveyor system, with the leftover steel recycled.
Durst does not produce steel parts for any other companies at its printer manufacturing site, with its machines there dedicated to producing its own devices.
It has used its expertise to start up a separate company, also based in the region of South Tyrol, which manufacturers aluminium parts for major companies around the world and a duplicate factory in Lienz, Austria.
Those who are on the tour and have bought the equipment, speak highly of it.
Cactus Imaging is one such company, and purchased two Durst Rho 512R roll-to-roll printers in 2017.
Nigel Spicer, general manager operations, Cactus Imaging, explains,“They are expensive machines, but you do not get the problems with them, they do not break down. We use ours for billboards, front-lit and back-lit fabrics, block out fabrics. We also print a lot of posters and self-adhesives. The only material we do not print on it is mesh, we have other machines for that.”
Alastair Wilson, director, Colourtech, recently purchased a Durst Rho P10 160, and says, “We have had it for two months now, a majority of the work we put on it is foam PVC for the exhibition industry, but we also produce acrylic ACM panels, self-adhesive vinyl, banner vinyl, and it is a great machine. The most reliable machine we had was the old one, and that is why we have went with Durst.
“I am their biggest fan, I rave about Durst, in all honesty they are the best machines I have ever run. I tell people it is like buying a Weber, you buy one, become a start raving fan, and then almost sell for them. That is what Durst are for printing.”
Work/life balance
The factory is open four and a half days a week, closing at midday on Fridays. Staff in the assembly line have milestones they need to reach, giving them the freedom to set their own hours.
This means they can come and go as they wish, whether it means heading home to pick up kids from childcare, or running errands.
The factory is also open to 7pm, with the baseline hours for most staff 7:00am-7:00pm, with a 34hr week.
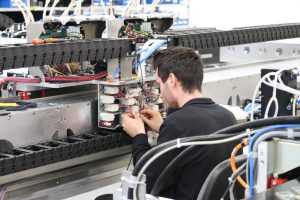
At the end of each year, staff are reviewed, given bonuses aligned to company performance, with individuals putting in extra hours also rewarded.
Ashman says, “The people locally can manage their lives, and get their work done. They love it, as they have complete flexibility to run their lives.”
Once a year, Durst has an open house with the local community, and tries to inspire younger generations to go into engineering, to learn how to create modern technology.
They are getting more and more successful, with other businesses in the region now taking part.
Final acceptance test
Each machine is made by two people, an electronics expert, and mechanical expert, seeing the build the whole way through.
Customers are invited out to the factory for a final inspection of every machine to ensure it meets their expectations before signing off on the deal.
They see their exact machine, with a repeated demo, next to the duo that built it, using the customer’s files and substrates.
Ashman, says “A criticism of many printer manufacturers is that they may have a great demo centre, but the machines are so finely tuned, that they print everything perfectly.”
Adding to this, most demo centres can select files that have been meticulously curated, with a combination of substrates which have went through meticulously testing beforehand.
It is a far-cry from the reality of a print site where you might be expected to get a perfect result in less than two days, with a substrate the customer selects, and an image they provide.
The benefit is that your machine will be up to your exact needs when you purchase it, says Ashman, explaining, “With Durst, if the customer is unhappy with any results of the demo, it is in the perfect place to put it right before they purchase it.”
The prints from the Factory Acceptance Test go into the Durst archives, and can be referenced years later, to confirm whether the machine is still producing the same results.
Spicer visited the Durst site before the purchase of Cactus Imaging’s dual 512R machines, with the company wanting to move into fabric and originally considering a dye-sublimation machine.
He explains, “When we saw the 512R, which prints on fabric, and complemented our existing business, it allowed us to stay within our niche, while putting a foot in the fabric market. It is brilliant for what we need to do, and offers versatility.”
Comment below to have your say on this story.
If you have a news story or tip-off, get in touch at editorial@sprinter.com.au.
Sign up to the Sprinter newsletter