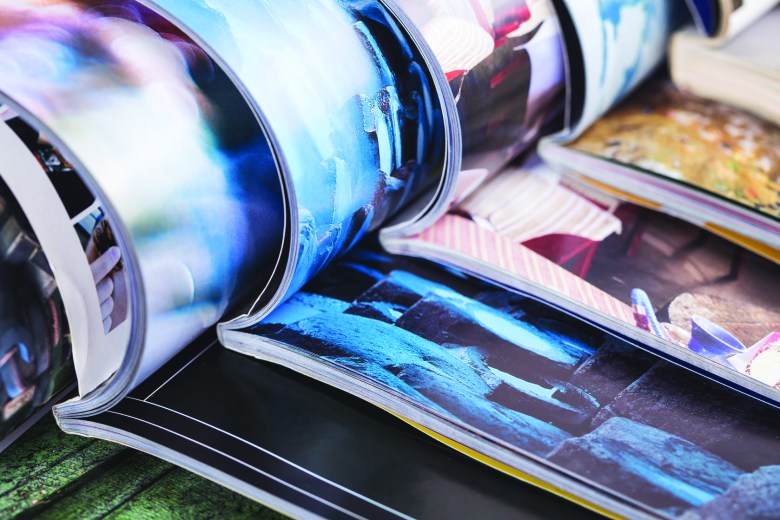
Short run printing ability is worth nothing if sheets remain on the floor waiting to be turned into books, magazines or brochures. Fortunately equipment has been developed to work with litho or digital sheets, which is rapid to set up and which links once separate processes into an automated flow to reduce manual steps, cost and waste.
The old stories where a trade house, asked to finish 50 digitally printed books, called the printer to say that the binding line was set up and he was now waiting for the job to arrive is in the past. Today the printer has to finish these sorts of jobs in house: the client wants the job tomorrow and there is no time (or margin) to load sheets for a few dozen books into a van to ship across town.
Single clamp perfect binders are typical of finish on demand machines. PUR adhesives overcome the difficulties of binding digitally printed sheets, uncooperative papers and images running into the spine. Supplied by Currie Group the Horizon BQ270 is typical of the equipment that is suited to this on demand production. There are many small lightweight perfect binders, including the BQ160 from Horizon, designed for occasional binding, but where better performance is a requirement, something like a BQ270 hits the spot. It has touch screen controls to set the dimensions of the book before the automation kicks in and sets clamp widths, the milling wheels and glue rollers.
It can be linked to a JDF workflow, but in reality the costs of doing so are not justified by the level of productivity anticipated. It is a different matter for the highly successful BQ470, the four clamp binder that can adjust on the fly for books of different spine thickness without missing a beat.
Books will normally drop to a delivery chute for offline trimming. But it is possible to fit a conveyor and to take the books to a three knife trimmer. With the manually operated HT-30 a single operator can run both binder and trimmer. But for a fully automated system, the HT-1000 is a fully automated trimmer capable of ‘book of one’ production.
It has taken a company from outside the traditional binding suppliers to come up with the automated approach that allows operators that are not fully steeped in bookbinding experience to produce high quality perfect bound books. Muller Martini and Kolbus have been playing catch up.
Kolbus has remained true to its high volume background, but with technology that can link the KM200 binder with the ability to cope with different thicknesses and length of book, adjusting to score covers to match the book block. Muller Martini meanwhile has developed Vareo as a three clamp binder designed to cope with a sequence of book of one or on demand production batches, as a standalone machine or linked to a SigmaLine to take a web of paper, fold trim and gather signatures in a fully automated production line for books.
This is a far cry from developments aimed at commercial printers where small batch production is necessary. Here simplicity of operation is essential. There are differences in how glue is applied in single clamp binders, assuming that PUR is used. Open tank systems need to be kept clean and may result in waste of expensive consumable, nozzle systems may become clogged or victim to the aggressive nature of PUR. A new generation of advanced hot melt glues, led by Planatol’s Planamelt, provide a bind strength that is close to PUR and ease of use that matches a conventional hot melt. It is catching on quickly.
Muller Martini also has a stake in saddle stitching, able to feed from a reel of digitally printed pages as well as handling standard folded signatures, combining this to produce hybrid catalogues using the Presto II Digital. The feeding sequence is delivered from the company’s Connex production system that can communicate with all Muller Martini stitcher and binders and on to a production management system, perhaps Heidelberg’s Prinect, and to an MIS. Its conventional stitching and binding lines have all benefited from servo motor automation to both cope with short runs and to identify where a problem occurs to minimise down time caused by old-fashioned misfeeds.
In a configuration shown at drupa, the Presto combined a preprinted litho signature with a reel printed on the Xerox Trivor inkjet press with personalised covers printed on an iGen.
The IBIS SmartBinder also copes with digital products, switching automatically between different styles and formats of product, even when mixed on the same reel of paper. It can work in offline mode when linked to a folder, an MBO is a popular choice.
This is an example of a combination product that is going to become standard. Sections from a folder, instead of heading to a stacker, are delivered to a conveying system and dropped over a saddle for stitching, or perhaps as in the Digitaline from Smyth, for sewing and gathering as book block for hardcover binding.
Again Horizon has been successful with its StitchLiner 5500 machine, taking flat sheets, accumulating these with a separate cover, folding stitching and trimming in sequence. The advantage is that there is no separate folding stage, cutting the process steps and thus the amount of handling needed.
Throughput speed is a steady 5,000 products an hour, but as the sweet spot for this style of machine is around 2,000 copies, speed is not the most important factor. Automated set up, touch screen adjustment and the ability to cope with variable product sizes, triggered by matrix codes to match body section and cover, or by trigger marks where personalisation is not needed, characterise this style of product.
These are also heavier machines than those that have moved up from inplant requirements. Here equipment has always been designed to be easy to operate, limited in format and speed, and with the emphasis on combined functionality in one machine. Morgana possibly set the pace for digital print when adding a creasing unit ahead of a folder to eliminate problems associated with cracking on digitally printed papers. Others have followed and this has become a standard set up for simple folders in digital print businesses.
Morgana has added a collating tower and stitching heads to create the Documaster, a best seller for the business. Fast set up is enabled via a touch screen panel on the Pro version of the machine, using icons to guide a semi-skilled operator through the set up steps required. For any machine targeting the digital end of the market, simplicity is essential. A common interface style across a manufacturer also helps cut the amount of training required.
Morgana is part of the same group as Plockmatic which provides finishing equipment that operates inline with the print engine, from Canon, Konica Minolta or Fuji-Xerox for example. The quality of product possible from inline production is improving, just as the quality of print from these print engines is also improving. However, inline suits business models where the product is essentially the same day in day out. In a jobbing environment, working with a sheet and having the ability to take that to a folder, collator or for lamination and guillotining, offline will be preferred for the flexibility. But it will require more people and at least some skills.
Inline does not mean second best, but does mean fewer people will be needed. The Watkiss PowerSquare can deliver a square backed stitched product from an inline print engine. This will also work as an offline unit. The popularity of the finish has led to imitators and to Watkiss developing a smaller PowerSquare unit which was shown as a prototype at drupa.
Lighter machines are moving up market with Duplo as the best example of this. Its early machines were suited to lightweight production only with product quality perhaps a secondary consideration. That is no longer the case. The booklet makers that the company made its name with are now capable of working with a wider range of papers, feeding from a stack of digitally printed sheets, or from litho sheets in collating towers.
It has tried to match the increase in use of digital print engines with more production focused machinery, the iSaddle being the best example to date. The folding unit is stronger than on the booklet makers and a Hohner stitching head ensures a professional finish. This will also deliver A4 landscape products, one of the hottest applications for digital printing.
Duplo has also led the way with its multi finishers: able to slit, perforate, score and fold in a single unit. A pile of sheets at one end becomes several stacks of business cards at the other, or a number of folded greetings cards, menu cards or other examples of the sorts of product that are increasing ordered online.
Horizon has now emulated the Duplo DC machines with the new SmartSlitter. This draws on experience it has with the SmartStacker, developed to handle the B2 format sheets from the HP Indigo 10000 and 12000 series digital presses. The SmartSlitter is positioned inline to the B2 Indigo, in turn fed directly from the server that receives orders from the website. The first time that an operator touches the product is when stacks of leaflets emerge from the big grey box. An identification code is applied and the pile shrink wrapped ready for shipment.
It is finishing controlled by prepress or by the production network and a harbinger of the direction that all finishing is heading. Robots are operating around guillotines to do the heavy lifting and presenting the stack under the blade ready for the first cut. The cutting sequence is downloaded from the production network.
Folders likewise are adopting automated makeready, reducing the skills needed to operate them and also the numbers of overs needed for a set up. This accelerates the speed that jobs can move through a finishing department, matching trends with presses using UV to cut the time needed at that stage of production.
For many years finishing has been regarded as the Ugly Sister department in a print business. It is more like Cinderella, now being transformed by the technology dedicated to automation and eliminating the waste of materials and time that finishing no longer need be associated with.
Comment below to have your say on this story.
If you have a news story or tip-off, get in touch at editorial@sprinter.com.au.
Sign up to the Sprinter newsletter