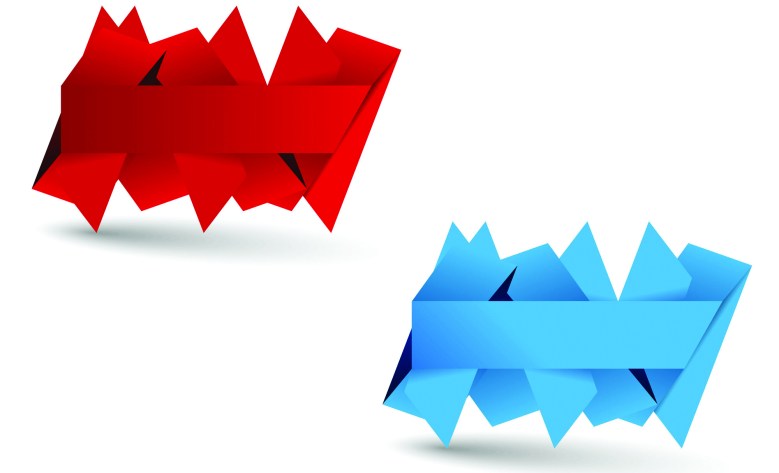
Digital printing is all about turnaround times, ease of use and minimising labour costs. When you are printing a run of 20 the economics are significantly different to printing 20,000. Old school finishing solutions for offset litho work is often not viable for the new breed of digital print shops. But the good news for printers is that the finishing solutions developers have been working hard to come up with innovative solutions.
Chris Pettitt, marketing manager of finishing specialist Neopost, says nowadays digital finishing has become part of general postpress. For instance, Neopost’s Ucos UD-300 rotary cylinder die cutter, while noted for its specialisation with digital print, is also adept at short-run creasing and perforation of offset print.
Likewise Neopost’s DS-200 folder and inserter performs standard mailer insertion and booklet inserts. And Duplo’s upgraded range of DocuCutters, including the DC-646, an upgrade of popular DC-645, are making inroads. Duplo has added to its range of booklet makers with the DBM-600 for landscape booklets, augmenting the DBM-500.
Neopost Australia has also just announced the launch of what it calls the world’s smallest closed tank PUR system, the Duplo PFi2000 PUR perfect binder, and has launched its bigger brother, the Duplo PFi6000 PUR.
Jimmy Nguyen, product manager for graphics at Neopost Australia, says, “They both feature beautiful design, robust quality and economical and automated operations. These machines make an ideal solution for printers who want to grow their businesses; produce high value jobs; increase productivity; reduce cost; and to delight their customers.”
He calls the Duplo PFi2000 PUR a single clamp easy to use perfect binder. He says, “The Patented Orbital PUR System is a startling development in binding technology. This new technology combines precision and accuracy and cost-effective operation.”
Productivity for the Duplo PFi2000 PUR rounds out at a cycling speed of 290 an hour and it offers a start-up time of less than 20 minutes. Nguyen adds that the cleaning time works through at less than five minutes at the end of the day or shift. He says, “This is a great feature to have as it can take between 30-45 minutes to clean an open tank solution.
“The Duplo PFi2000 PUR is designed to open up new markets in Australia, not least because of its low price, small size, ease of use, and high quality. It makes an ideal companion for small to medium size digital printers, copy shops, quick printers, and corporate in-plants and it fits perfectly in our Digital Business Solution range. The Duplo PFi6000 series comprises single clamp fully automatic easy to use perfect binders that produce up to 350 books an hour and have a cycling speed of 600 cycles per hour. They feature complete automation with in-line scoring, and cover feeding as standard.”
The 6000 series features the PFi6000 DUO and PFi6000 PUR. The PFi6000 DUO enables the operator to select between PUR or EVA for side gluing whereas the PFi6000 PUR uses PUR only.
Nguyen says, “The 6000 series can bind anything and everything with ease. Professional binding has never been so easy. The PFi6000 series binders offer the ideal solution for a printer who has litho and digital presses and is producing high to mid volume production runs. The DUO is specially designed for printers who need options. Like its smaller brother, the cleaning time on the PFi6000 Series is less than five minutes at the end of the day or shift.
“Both the new binders work as plug and play machines. Just turn them on and you are ready to go. They have simple, easy to use touch screens, which helps for an easy set up. Non-skilled operators can quickly become quite proficient running these machines.”
Currie Group managing director Bernie Robinson is a firm believer in both inline and offline finishing solutions. For example, you can connect a Horizon SPF-200L booklet maker inline to an HP Indigo 5600 or 7800 and you can add a Horizon HOF-400 high-speed offline feeder. You can take a pre-printed cover and merge it with the book-block.
“My preferred option is offline, because digital presses are made to print, they are not made to finish. But it is horses for courses, and we can provide the best of both worlds,” he says. “Another factor is that while a sheetfed job is being finished, it slows the upstream printing on the same line, so there are no real productivity gains from being all inline.
“For example, with perfect binding, you need to hand-feed the book-block from the digital press into a perfect binder. The Horizon SPF-200L can do 4,500 sets per hour. Digital press speeds cannot match that, so you are better off finishing offline via a robotic feeder,” he says.
In addition, barcode set-up enables unique configurations within a single print run, lessening the need for separate set-ups in a variable job lot.
Robinson says Horizon’s SmartSlitter, a perforator-creaser-cutter specially designed for finishing A3 digital print, uses the same dies as Horizon’s CRF-362, but can do a lot more. It can do a ticket on a tee, with stop-start perforating in the direction of the sheet. It also performs scoring and provides for manual perforating, for four-to-six perfs on an A3 sheet. It will do a tear-off. It can also do business cards and greeting cards, cutting and creasing from an A3 sheet – all with barcoding, including barcoded stop-starts, in code-39 and QR options. “Every second sheet can be different,” says Robinson of the barcoded slitting.
The SmartSlitter was on show at the Visual Impact show in Brisbane in April this year, where it drew a lot of traffic to the Currie Group Mobile Showroom. “We demonstrated it with five different pre-printed items and it sets up five times within a matter of two-to-three minutes. That means five jobs finished within minutes,” he explains.
Meanwhile, the CRF-362 creaser-folder will take pre-printed digital work, crease the spine, with two creases and two perfs on an A3 sheet, top to bottom, and also has two buckle plates. “Again, all the Horizon gear has memories for 200 programmes, with provision to download configurations to a USB stick, and clear the onboard drive for a further 200 programmes.”
And a Horizon SmartStacker is a B2 stacker that integrates with an HP Indigo Digital Press for scoring, perforating and slitting – computerised and able to finish a job on the run, says Robinson. Smart stitching of digital rollform is taken care of with a StitchLiner 6000, connected to a Hunkeler system for sheeting and creation of book blocks.
Heidelberg ANZ post-press product manager Brian Evans says some of the onboard finishing available today is adequate for digital print work. “Three-side trimming, stitching and punching are three processes that work well with online digital print engines. However many other processes often need to be included and for these functions, offline finishing machinery is required.”
Evans believes a range of offset equipment can be used in conjunction with digital printing. “Card cutters, die-cutters, scoring and slitting devises are just a few examples.”
Creasing is a major issue with stock printed digitally, and Heidelberg offers a range of products that can help eliminate this problem. Heidelberg’s Ti52 inline scorer performs what Evans sees as a basic of digital folding. The Ti52 is designed for high speed, accurate folding, he says. Most suppliers can provide scoring inline, but accuracy at speed is a more challenging task and one which Heidelberg has been able to solve, he explains.
Heidelberg also offers its CH56KT folder, which has made a major impression in Europe. Meanwhile, for cutting, there are the Polar 56ECO and NET models, Polar 66ECO and NET, Polar 80ECO and NET, Polar 78ECO and Plus, and Pro models, as well as the Polar Guillo-crease.
Evans says that with digital print’s popularity and most offset printers now also having a designated digital print room, ‘cutters and folding machines can be used for both digital and offset and with the appropriate accessories, most digital work can be processed’.
“Most digital print shops will have their own finishing machinery that stands alongside the digital print engine and is suited for the short run work,” he states. In fact, he points out that printing often starts with post-press, that is, cutting of sheets prior to printing.
According to Nathan Broughton, national product manager at Ferrostaal Australia’s digital and offset finishing division, vendors today offer a range of finishing solutions inline with the print engine, some of which come in at low investment costs, and can add value to the end product without the need for additional processes.
He says one such machine is Morgana Digifold Pro, which can crease to remove any paper or toner cracking and fold in one process. This multi-step process achieves the same level of quality as traditional offset procedures.
“This is an attractive concept, however when the printer investigates further, they find that the total solution is not always as flexible as they need. Many of the inline finishing units can slow the printing process considerably and there is usually a need to trim the products before finishing as a folded brochure or making a booklet. Additional click charges can also apply if the product requires multiple processes and then is required to be re-fed through the print engine to finish the products,” he says.
Broughton believes that in some cases traditional offset finishing equipment can be useful to finish the end product but, in most cases, printers would do well to consider the difference of using finishing equipment that has been specifically designed to produce digitally printed products.
“One point in particular to note is the amount of sheets required to make ready when using offset finishing equipment, which can require up to 50 sheets to set up, whereas a machine doing the same job from the digital finishing specialist such as Morgana generally only require one or two sheets to set. Time to set up the machines is also something to consider, as most digital finishing equipment is set up in a matter of seconds, which obviously improve the all-important turnaround time to deliver the job,” he says.
“Today’s digital print finishing equipment is designed to take away the need for highly skilled operators and make the process of print finishing very simple and user friendly. This can immediately improve the bottom line by cross-skilling staff without the need for specialist operators to output high quality products. The equipment is usually very versatile,” notes Broughton, “and often one machine can handle a range processes that can add value to the end-product.”
Graph-Pak’s Thermotype range from the US has attracted interest, says managing director Tom Ralph, particularly its NSF foil presses, which provide die cutting, hot foil stamping, foil fusing, creasing, dimensional embossing, single-level embossing, numbering, hologram placements, perforating and crash printing – all in a single device.
To show ROI and keep margins low, a bindery needs to offer rapid makeready, low wastage, and flexible kit, argues Ralph. Robustness and operability at low skill levels are also advantages in the digital bindery, he finds.
For digital printers there is no doubt that finishing solutions developers are on their page, and they now have a wide choice of options to complement their digital presses.
Comment below to have your say on this story.
If you have a news story or tip-off, get in touch at editorial@sprinter.com.au.
Sign up to the Sprinter newsletter