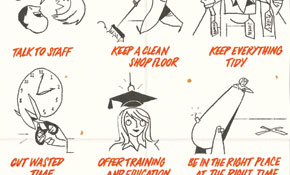
If the solution to getting more out of your machines – more speed, more uptime and of course more margin – is automation, then one answer to unlocking more from your workforce is to use lean manufacturing principles.
Lean consultant Wayne McDougall says that while printing companies tend to be good at hiring from within the industry, they fall down when it comes to the kind of ongoing training that creates an industry-wide skills base. And many fail to develop proactive strategies for their company. “Many printing businesses just keep on doing what they think they’re good at.”
McDougall is principal director of SkilledForce, a consultancy with a team of eight trainers nationally and 25 print industry clients in commercial sheetfed, digital and label printing. The company runs 18-month programmes, and since the GFC, he has noticed an uptick in firms seeking efficiency training, in order to provide extra capacity or to avoid re-work.
The focus of SkilledForce’s training “is end-to-end, on all aspects of the process, from sales, through production to dispatch”, says McDougall.
“We look for ways to reduce wasted motion and unnecessary transport. Our aim is to make the space work for the business, not to force the business to work in its space. We organise self-managed work teams, we measure performance in localised and broader areas.”
Problem zones
Some “problem zones” are common to companies in any industry. McDougall points at poor communication between departments, poor information flow, a lack of standardisation and consistency, as well as a failure to stick to quality assurance (QA) systems. In terms of print-specific problems, pressroom bottlenecks, such as makeready times, are common.
LabelCraft is one industry player who turned to SkilledForce for help. The national label manufacturer, which has 190 staff Australia-wide, was in the market for an onsite government-subsidised training package to help it increase productivity. It decided on employee qualification, which was supported by a grant of $5,100 per employee for daily on-site support over a two-year period. It turned to SkilledForce because of its print industry specialisation, says LabelCraft quality assurance manager Aidan Lyons.
After initial meetings in December 2009 to ensure each staff member qualified for the grant, apprenticeship centre MAS National was brought in to sign up staff to a Certificate 3 or 4 in Competitive Manufacturing. Since May 2010, two consultants from SkilledForce have been on-site each Monday.
Two phases of SkilledForce’s programme were piloted at LabelCraft’s main flexo/screen facility in the Sydney suburb of Leichhardt. Pre-qualifications were conducted at its Villawood sheetfed plant. (It also owns Labelworld in Perth, The Label House in Melbourne, LabelPlus in Queensland, and Phoenix Labels in Griffith, NSW, all of which will eventually undergo the SkilledForce programme).
Clean-ups occurred around print machines and under printers’ benches. Obsolete hardware or consumables were disposed of, then red tags fixed to anything that did not have an operational purpose, with a deadline for allocating it to a functional place or removing it.
Lyons says: “The factory hadn’t been marked out for a number of years. We moved to laying out the shopfloor, painting lines on the floor, allocating where bins should be, allocating a place for incoming and outgoing goods. We introduced shadow boards for signage to identify specific areas.
“If you come in off the street now, you can see where everything ought to be. It looks smarter, which is also good for customer audits and visits. Most importantly, it got everyone involved, which is the key to the project,” he adds.
The second phase, “Mini-Business”, is now underway, capturing performance data, recording loss times, and reviewing internal non-conformance reports.
LabelCraft is recording data and setting KPIs for all departments: sales and administration, pre-press, printing, finishing and despatch. For example, the sales department has been given targets for quotation turnarounds and the time it takes to process work tickets. In the printing department, loss times are recorded then divided into maintenance and operator errors. In finishing, DIFOT (Delivery In Full On Time) scores are analysed, involving errors in invoicing and defects picked up during inspection.
LabelCraft upgraded to the latest version of its Prism MIS and maintains its Gallus flexo presses and HP digital label presses in top nick, as well as its Manrolands and its Bobst diecutter at Villawood. But Lyons is adamant no single piece of hardware or software is a magic bullet for productivity.
Globus Group Australia, a supplier of packaging and equipment for perishable foods, approached Printing Industries Association of Australia about going lean. Globus manufacturing manager Rodney Wong-Pan says that following MAS Australia approval, the company was introduced to SkilledForce, which implemented an 18-24 month programme in Certificate 3 and 4 training. The aim is to improve efficiencies on a Comexi flexo press and an older Globus press, as well as downstream – a laminating, slitting and centre-sealing area, and at a converting site that manufactures plastic bags and small goods casings.
A dedicated facilitator makes fortnightly visits and the factory is shut for four hours to conduct sessions. Wong-Pan says the site is less cluttered. “In the warehouse, we had unbalanced workflows. A lot of demands were immediate, so we are now reporting production to the warehouse twice instead of once daily.”
Globus provides feedback to Printing Industries via six-monthly reports for a case study on production efficiencies. Wong-Pan says that unlike ISO 9001 and types of QA, the programme is “written for the production floor, not the auditors”.
It was management training that brought Sydney-based Lindsay Yates Group (LYG) to SkilledForce’s lean programme. LYG managing director Paul Richardson was looking to commission some training for senior management, when Printing Industries recommended SkilledForce. “It turned out to be bigger than we anticipated, and certainly not just for managers,” says Richardson.
Mixed reactions
The offset and digital house underwent SkilledForce Certificate 3 lean manufacturing and a Certificate 4 training and supervisors programme. Goals were documented and KPIs set. While Richardson is overwhelmingly positive about the impact of the training, not everyone was a fan of the new approach.
“Some supervisors didn’t want to be part of it, didn’t want to be held to KPIs. Some decided to leave, but most went for further training and benefited enormously from it,” he says.
For example, the firm employs 5S principles (see box) in the pressroom and bindery of its Artarmon sheetfed facility. Supervisors and factory personnel affix a red tag to all extraneous items, says Richardson. “Anything that sits in the factory for over two weeks and doesn’t move gets a tag. This could be old machinery, ink rollers idle on the wall, waste paper in a corner, ink on an ink rack, pieces of old packing equipment, broken pallets or overs from a job that need to be resold, cut up for waste or recycled.”
Three-and-a-half years along, the programme has made a significant impact on buoying the bottom line. Richardson feel vindicated in his decision to go ahead with it during the GFC.
Another advantage of a lean programme is that it prepares the firm structurally and culturally for other programmes, including ISO 14001, as well as industry-centric programmes such as Printing Industries’ Sustainable Green Print and GASAA’s Truly Green, which LYG is currently undertaking.
Avoiding bottlenecks
Lean is all about identifying restrictions and eliminating bottlenecks. Another lean consultant, Michael Taylor from Contours Customised Solutions (CCS), uses an anecdote to illustrate the mentality behind lean manufacturing.
An Australian printing business was going head-to-head with a competitor from China. The local printer thought that the shorter lead times it could offer were a significant advantage over its offshore rival, despite the Chinese contender’s better deal on price. But the Chinese print house ended up winning the contract thanks to a brilliant flourish. It installed bindery equipment on the ship and finished the job in transit to Australia.
Rather than seeing the threat, Taylor says printers should see the opportunity in this salutary lesson in innovation.
Taylor, operations manager at Brisbane-based CCS, formed the business four years ago after a management career in pharmaceuticals. CCS is just one consultancy targeting myriad industries across the economy. He noticed a significant rise in the number of printers among the company’s client base over the past 18 months, perhaps a symptom of general angst at the trading conditions. But several had specific aims, chasing a contract or new market segments and wanting to free up saleable capacity.
“In the printing industry, there seem to be lots of great tradespeople, but not many great managers,” says Taylor. “Many owners and managers think they can get by just by doing what they’ve always done. They are great at putting out spot fires but don’t have a structured problem-solving process in place.”
CCS’s programmes take a business through a six-month assessment, but progress is open-ended, and the most effective approach is to revisit every three to six months.
A selected steering group from within the client company translates broad principles into print-specific ones. Taylor advocates not trying to improve everything at once, but cherry picking one or two practices for improvement. The steering group might be charged with reducing makeready from two hours to 30 minutes per job.
Vendors will say that the best way to reduce makeready is a matter of installing bells-and-whistles machinery. This isn’t necessarily the case, says Taylor. “A printer needs to ask themselves what gains they can make on the existing equipment, before spending an additional $1.5 million.”
Practices under the microscope include process and material flows, basic maintenance, work methods and waste reduction. Amazingly, four of the six basic steps of press set-up reduction are likely to be cost-free, he says. It is just a matter of finding a better way of organising the workflow. And don’t forget the front office. In this industry, there is an over-emphasis on production and a neglect of administration, says Taylor, but some 60% of a company’s activity will be in the latter. The ultimate goal is the entire workflow operating in perfect harmony.
Comment below to have your say on this story.
If you have a news story or tip-off, get in touch at editorial@sprinter.com.au.
Sign up to the Sprinter newsletter