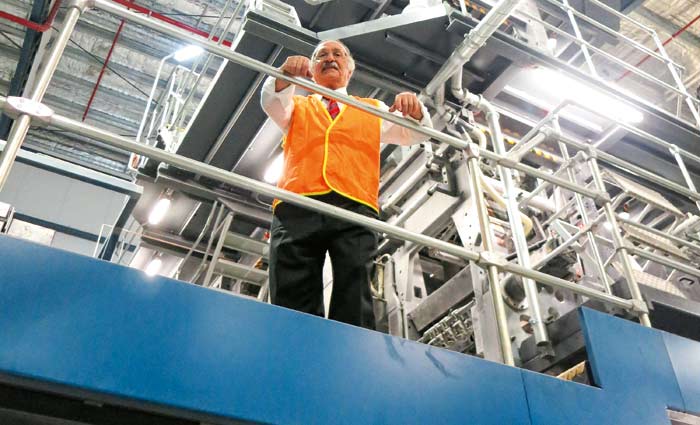
It takes quite a while to get around Hannanprint’s Warwick Farm supersite. That’s not only because of the building’s aircraft-hangar footprint, although that’s part of it. The other reason for the slow progress is the tour guide, Tony Dedda. The outgoing managing director of the IPMG-owned business just keeps stopping. People have told ProPrint in the past that Dedda prides himself on knowing everyone’s name. Taking a tour of Warwick Farm with him, it’s clearly not lip service. Dedda is shaking hands, shouting out ‘g’day’, asking after people’s children. One worker, who was offered extended leave after a family member fell ill, tells ProPrint, unprompted, “Not every boss is like Tony. It’s nice.”
[Photos: Go behind the scenes]
Over recent weeks, Dedda has also been playing tour guide for an increasing number of customers. Warwick Farm is a showpiece; it’s easy to understand why he would want to show it off.
While there are no customers visiting the plant when ProPrint tours, they are there in spirit. Dedda’s office is bare – like the rest of the plant, it lacks that lived-in feel found at even the tidiest print shop – so it’d be hard to miss the single piece of A4 paper pinned to the empty noticeboard in an otherwise sparsely decorated room. The note reads, “There is only one boss, the customer. He can fire everyone in the company from the directors down simply by spending his money elsewhere.”
For Dedda, this philosophy starts at the top and permeates the business. “The whole company is customer focused. Not just me; it’s the guy in the bindery, the guy in the pressroom. We understand the customer is the business. It is not a motherhood-type statement. We live it.”
Back to the tour, which continues at a stop-start pace. The gregarious MD is not the only reason that a journey around the newly opened plant takes quite some time. Warwick Farm is all about size. It represents the most significant build in this industry since Fairfax established Tullamarine 10 years ago and the biggest heatset project since PMP set up its Moorebank supersite in the mid-90s.
Warwick Farm, a former Kimberly Clark plant, occupies 12.8 hectares. Everywhere you go, there are huge numbers to ponder, staggering volumes, impressive run lengths, machinery values with plenty of zeros. Rainwater tanks hold a combined three million litres; the paper store can fit 22,000 tonnes. Some 20 tonnes of ink per colour is on hand. The newest press is running at 180,000 sheets per hour.
Dedda says that if all four web presses were running full speed at their optimum web width, the plant could churn out eight million pages per hour.
If those numbers aren’t impressive enough, then double them. Because plenty of the integral equipment is counted in multiples of two. When Hannanprint relocated from long-time home in Alexan-dria to this new site in western Sydney, it needed to double-up on essential kit, to ensure continuity for its customers.
“We need two sets in case one breaks down. When you buy a new piece of equipment, you try to align it to the old one,” says Dedda.
“Redundancy is built into the plant. The new Lithoman is exactly the same web width as the other two; we could’ve bought something wider, but then if you have to move work to another press, you would have an issue. Staying with one width also makes warehouse management the same.”
Seeing double
This case of double vision doesn’t only apply to duplicate machinery: the flagship press also has a split personality. The heart of Warwick Farm is a 96pp Manroland Lithoman in a twin web configuration. When ordered, it was the only press of its kind anywhere in the world.
Reaching 45,000 cylinder revolutions per hour, the machine’s productivity has been boosted further thanks to optional bells and whistles.
According to Manroland, automation includes: automatic plate loading; the AutoJobChange control package with QuickStart pre-inking function; inline control systems for cut-off register; ink density control; and colour register.
While twin webs are not as popular as wider presses, Dedda is an advocate of the configuration. “Some people are frightened by having one web on top of the other, but we have mastered it. They give you enormous output; it is technology that we are very familiar with.”
Everywhere you look in Warwick Farm there is technology. Shiny new machines sit alongside older models relocated from Alexandria. In the centre of the plant, printing technology actually fuses with the building itself. The masterstroke in the factory’s design is the control room for its fleet of four Manroland presses. The offices have been built directly over the press lines. Freshly printed catalogues clipped to the Ferag lines zip down and around the press control desks like laundry spinning on the world’s most high-tech Hills Hoist.
It is in stark contrast to the congested layout at the old site. “Alexandria grew over many years, so you stuck things where they fitted. Here you had the ability to develop a flow; you have paper, presses and finishing and stitching and dispatch.
“We have the people who live this in the control room, the mezzanine over the pressroom. They can feel the presses. They are part of it. That is important,” he says.
On the ground level, press operators man the control desks. Some of them have been at Hannanprint their entire careers. Guys like Tony Moore, who has been with Hannanprint for three decades, or a fellow pilot at a Manroland press console, Terry Fripp, who has “only” worked for the company for 18 years.
Dedda says designing the layout of the presses and control centre was “one of the most exciting things in the planning stage”. A lot of thought went into creating the perfect workflow. For instance, the engineering department is located a stone’s throws from the printers’ workstations. “If a press goes down, the engineers are right there. Normally engineers are stuck at the back of the factory.”
On the floor directly above, production planners strategise the hundreds of jobs that will fill the press capacity over the months ahead. Pressroom manager Simon oversees the method in the madness. He seems young for such a major position, but he has also has been with Hannanprint for his whole career.
“Simon was an apprentice at Dubbo and when we closed that plant, he completed his apprenticeship, moved to number two printer, then number one. He is pressroom manager – he’s a young guy that cares and he does a fantastic job.”
Dedda remembers similar anecdotes about employees in every department. He praises another Hannanprint lifer, a lady on the night shift who has spent 30 years with the company. “She works one of the drum stitchers; she is an excellent worker. She lives and breathes Hannanprint.”
Long service does not go unrecognised. There are staff awards for workers who have committed 10 years, 15 years and 20 years to the company. These gatherings, usually morning teas, occur in batches of four each time, to account for people working across any of the four shifts. The smiles on people’s faces as ProPrint tours the plant seem like the looks of a genuinely happy workforce. “People don’t leave Hannanprint,” says Dedda.
There are plenty of staff dotted around the plant, but nowhere near as many as might be expected from a facility of this size. Automation black magic has replaced many manual roles.
The company went through significant redundancies in the lead-up to the opening of Warwick Farm: according to IPMG chief executive Stephen Anstice, when he spoke to ProPrint in August 2011, there were plans to cut 140 jobs to bring the headcount down from 420 to 280.
March of progress
Call it the march of progress. The presses running at Warwick Farm have been optioned with the latest and greatest automation technology.
It is not just the new, $20 million Manroland Lithoman, but the other three presses – two 48pp Lithomans and a 32pp Rotoman – that have benefitted from Manroland’s latest and greatest on-press intelligence.
Dedda explains that Hannanprint took the opportunity to retrofit the older models with InlineDensity Control systems, as well as giving them a general tune-up.
“We installed the two Lithomans when I joined Hannanprint about 12 years. They are good presses; they’ve been well maintained. With the relocation, we had a chance to refresh those parts that aren’t usually visible. We upgraded the software and the colour management. They are performing almost as good as when they were new,” he says.
But for all these techno smarts, Dedda still sees a place for the human touch in even the most highly automated processes.
“[Technology] will allow you to have fewer printers. It allows you to have printers who can run bigger presses. Rather than three printers, you can have two printers, but that is not really the trans-form-ation. The printer is learning better ways of getting to colour. That technology drives performance – through the printer. You still need these guys. It is like a car with a GPS and cruise control. You still need a driver, but you get there quicker.”
It is not only about what’s on-press but what comes before it. Dedda says Hannanprint’s pre-press department is “without doubt one of the best in the southern hemisphere”. The first thing to strike a visitor when they step inside the cavernous pre-press department is not its size but the number of people working in it. That number is exactly zero.
The Kodak Magnus platesetters hum silently, automatically exposing the enormous plates that will be carted back to the Lithomans. Soon, even this manual task of carrying plates will be replaced by automation. Hannanprint is putting in a “plate superhighway” – a conveyor mechanism to move plates from pre-press all the way to the press hall.
Even the storage cupboards are automated. Dedda points out a silo that reaches up as high as the roof. Spare parts are stored on rack after rack, each shelf’s position catalogued electronically. An engineer can simply call up the required part in this VLM (vertical lift module) system and the mechanism kicks into action, bringing the correct shelf down to a collection point.
Hannanprint’s technological evolution continues into the ether. The group is in the process of switching to the Technique MIS system. There’s an interesting back story to the investment. Hannanprint was one of the many companies affected by EFI’s acquisition of Prism. The print group had been a major user of the Prism Win and QTMS systems; at the time of the EFI acquisition, Dedda admitted to ProPrint of some shock over the change of ownership and how it could impact systems in which the group had invested many thousands of dollars.
Hannanprint made the decision to move to UK-owned Technique . The system is clearly a favourite among big groups: other users include Hannanprint’s largest competitor in catalogues, Franklin Web. Rounding out the heatset web players to use Technique are AIW Printing and PMP.
The decision by Hannanprint to switch to Technique was, it seems, a major reason why EFI acquired the British MIS developer. At EFI’s Connect conference in Las Vegas at the start of 2013, chief executive Guy Gecht said: “We lost a big deal to Technique in Australia. We hated that we had lost and so we bought them.”
Empowering people
The implementation of Technique is one of many projects Dedda has overseen. Just as he takes close interest in his workforce, he also keeps a check on all the departments in the group, from operations to sales. But he “doesn’t micro-manage”, he says.
“I build the managers to do their job. I believe that my major role is to help the people who report to me do a better job. I manage by accountability. The operations manager runs operations, the sales manager runs sales. But I get involved in sales, client visits, client quotes, major quotes and tenders. Today, we have been looking at two tenders and payback on capital for certain projects. People come to me for ideas,” he says.
Dedda is not a printer. He came from a finance background when he originally joined the group.
“I am ‘an accountant gone wrong’, according to Michael Hannan. I started with the group as chief accountant, then moved to general manger of finance. I kept telling Stephen Anstice they should ‘do this and do that’ so he made me general manager 13 years ago.
“It has been a very exciting, challenging employment history for me. I love the group. It has a family aspect about it. You are talking to people who know what they are doing. When you meet with Michael Hannan, he knows what he is doing.”
When ProPrint visited Dedda weeks ago, he wouldn’t comment on the group’s plans for future leadership. He would just say: “That’s a secret. There is a succession plan.”
However, since then, IPMG’s succession plan has been made clear. Dedda is retiring on 1 October. Hannanprint’s chief financial officer, Adrian O’Connor, will take the top job. The changing of the guard is echoed across the wider group, where IPMG chief executive Stephen Anstice is also stepping down, to be replaced by Kevin Slaven on 1 July.
Plans change
This shows, as much as anything, the presence of strategy at the business. The focus on planning is eminently clear when looking at the progress of the Warwick Farm project. The plan has been fluid, changing in line with the market. The initial idea of building the country’s only gravure supersite had to change as page volumes fell amid the GFC. Instead, IPMG opted for heatset web offset, a technology it was familiar with, from Manroland, a supplier it knew very well.
But the relocation was beset by a number of other obstacles over the many months of execution. The first challenge was planned for: the necessary period during which Hannanprint operated out of two sites.
“There was a fair amount of logistics,” says Dedda. “You are printing here and stitching at Alexandria. The hardest part of the transition was when it was 50-50, when we were doing 50% of the work here and 50% there. That was when everyone was so stretched. We had the same number of staff to manage two plants.”
Tensions must’ve been riding high. “That was the part that needed good stewardship and a good understanding; not going off and blasting everyone but understanding the issues and resolving them. That is the major part of project management: look at the problems and the solutions. Get people involved, explain it. There is a light at the end of the tunnel.”
Another obstacle came like a bolt out of the blue. Few could have missed that fact that IPMG made one of the largest equipment investments in its history just months before Manroland filed for insolvency. When the press maker collapsed in November 2011, it brought shutters down on production in Germany. Somewhere in a workshop in Augsberg sat the pieces that would become Hannan-print’s press. It took almost two months before a new owner for Manroland was announced, manufacturing corporation Possehl Group.
There’s no doubt the mishap cost Hannanprint a lot of money and sleepless nights. It was a contingency that few could have planned for; Dedda admits it was the biggest disruption of the entire the project.
“The major hurdle was the Manroland insolvency. That could have put Warwick Farm on the shelf because it was a Manroland [press]. That probably would be the major hurdle that was out of our control but it was mitigated fairly well, with us working together with the receivers to achieve an outcome that wasn’t the best, but it was an acceptable outcome.”
The other mishap truly was an act of God. “We had 24 days of consecutive rain,” says Dedda. “We were building a swimming pool instead of a pressroom.”
The answer was to shift the focus away from waterlogged parts of the site and target those things that could be done despite the inclement weather. So even with the rain wreaking havoc with plans on the ground and the Manroland insolvency dragging energy away, Dedda and co never lost sight of the goals. They found ways to push forward. “The project was exciting so there was never a hurdle that become insurmountable. You overcame the hurdles.”
With a clear sense of pride, Dedda says that the project was “spot on to the week”. That’s right: this multimillion-dollar exercise, which involved a cast of hundreds and faced plenty of unforeseen twists and turns, was only off the mark by a matter of days. When ProPrint visits, Dedda says Warwick Farm is 99% done, bar a few licks of paint.
He looks around the buzzing pressroom with pride. “When I look back, I would do it again.”
Factfile
Staff 300 approx
Size 38,000m2
Established 2013
Owners Hannan family
Presses
• One 96pp twin-web Manroland Lithoman
• Two 48pp Manroland Lithomans
• One 32pp Manroland Rotoman
Markets magazines, catalogues, newspaper inserts
Comment below to have your say on this story.
If you have a news story or tip-off, get in touch at editorial@sprinter.com.au.
Sign up to the Sprinter newsletter