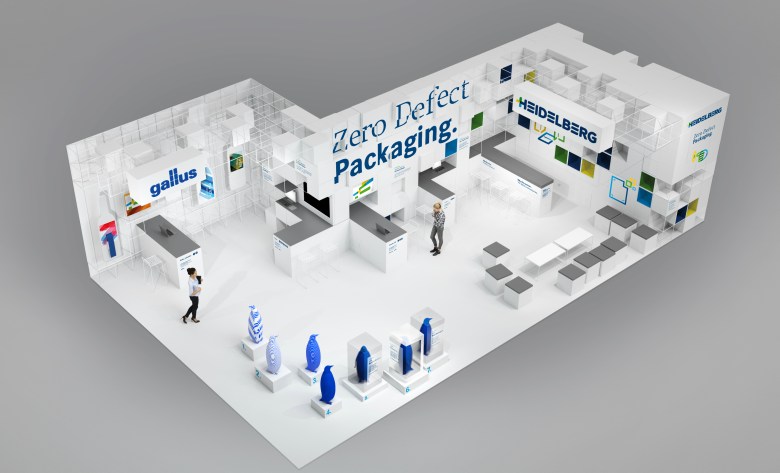
Heidelberg and its Swiss subsidiary Gallus have combined to create what they call zero-defect packaging, which they say is made possible through digitisation, automation, and communication between machines.
Heidelberg and Gallus will display this networked production environment at Interpack, under the motto “Smart Print Shop – Zero Defect Packaging”.
The company says that digitisation of all key process steps in production offers a way of greatly reducing the risk of defects, even eliminating it altogether. As the packaging segment of the print industry grows, both companies are underlining the strategic significance of packaging and label printing for their economic future.
Stephan Plenz, management board member for Equipment at Heidelberg, says, “The appearance of packaging at the point of sales has a direct influence on the purchase decision and the brand experience of consumers. Depending on the market segment, poorly produced packaging – even just variations in colour – can result in loss of image as well as a high liability risk. The Heidelberg promise of “Zero Defect Packaging” fulfills the requirements of brand companies for flawless packaging from an aesthetic, legal, functional, and marketing point of view.
“Heidelberg is the leading provider in the industry that can guarantee digitized and industrial packaging production with a defect-free, standardized end result. Our intention is to continue to expand our offering in this growth market.”
Heidelberg says this is made possible by its Prinect Packaging workflow, which enables automation of the workflows – from order acceptance, through structural design, prepress, and press through to postpress – and facilitates intelligent communication between the areas in order to prevent defects.
Prinect integrates Heidelberg’s offset and digital printing systems into one continuous workflow, and offers functions for quality assurance and documentation as well as standardisation and production of repeat jobs.
According to the company, the result is a fully automated and industrialized printing process where manual interventions are reduced to a minimum.
Comment below to have your say on this story.
If you have a news story or tip-off, get in touch at editorial@sprinter.com.au.
Sign up to the Sprinter newsletter