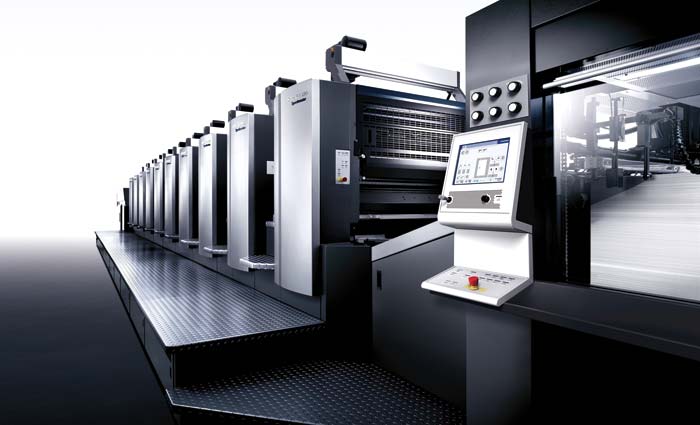
When Heidelberg unleashed the Speedmaster SX series at Drupa 2012 to a fanfare of publicity, it was abundantly clear the press maker had high hopes for the new range. Given the global popularity of the German firm’s machines, the series was expected to sell well. But even Heidelberg’s top brass must have been pleasantly surprised by the sales performance of the range, which is available in three formats: SX 52, SX 74 and SX 102. In November, Heidelberg announced it had shifted more than 1,000 SX units worldwide, exceeding its original target by 25%. Of those 1,000 units, 37 sales were to customers in Australia and New Zealand.(For clarity’s sake, it is worth pointing out they mean 1,000 individual printing units, not whole presses. A four-colour press would comprise four units.)
A Speedmaster SX 52 has already been installed at Apex Print & Design in New Zealand. The first SX 74 presses are expected to be shipped to two Australian customers in Sydney in May. According to Heidelberg, a “well-known South Australian printing company” will install the first SX 102 perfector equipped with the new Autoplate Pro fully autoatic plate changing system, in the early part of 2013. The manufacturer says that 200 of the 1,000-plus units sold to date are for the perfecting version. Heidelberg expects the model to continue to fare well, with more than 30,000 users worldwide of its perfecting technology.
It’s easy to see why the machine has struck a chord. The SX 102 builds on Heidelberg’s perfecting legacy, combining the technology of the XL series with the Speedmaster SM 102 platform, to give print shops “a crucial competitive edge by delivering consistently high print quality on both sides of the sheet at maximum production speeds”, says Heidelberg.
According to Shane Hanlon, head of product management and remarketed equipment at Heidelberg Australia & New Zealand, the SX 102 is predominantly tailored to the requirements of commercial printers. The press, which has a top speed of 14,000 sheets per hour (sph), is suitable for existing Heidelberg Speedmaster users looking to upgrade, he adds.
“Furthermore, users of other manufacturers’ equipment have expressed interest due to the availability of unique features such as flexibility of printing substrates from 0.03-0.6mm in both straight printing mode and perfecting,” explains Hanlon.
One of the unique selling points of the new range is that the machines can be custom built to suit individual user requirements. “You can have a configuration that is highly automated with features such as perfecting, fully automatic job changeover with the Intellistart Software coupled with Prinect Inpress control system and Autoplate Pro fully automatic plate change, which offers unparalleled makeready potentials,” explains Hanlon.
In addition to offering the “highest flexibility”, the machines come with a host of features in standard configuration. These include a new surface technology for the exchangeable jackets of impression and transfer cylinders – PerfectJacket Blue and TransferJacket Blue – which has been installed across the SX range to ensure a far longer service life and extended wash-up intervals.
Speed demon
The SX 102 is available in configurations of two to 10 colours with coating unit and perfecting available as an option, explains Hanlon. “The maximum speed has been increased for perfecting up to eight printing units to 14,000sph. Combining this with the optional Prinect Inpress control system and the fully automatic plate changer Autoplate Pro, users will be able to boost productivity levels by upwards of 30% compared with existing models.”
But don’t just take his word for it. German printer Görres installed an eight-colour Speedmaster SX 102 perfecting press last July and after just a few weeks, efficiency levels had increased by around 20%, says managing director Arnd Spitzlei, He is confident of achieving efficiency levels of 30-35%.
What we particularly like about the SX 102 are technologies such as Prinect Inpress Control,” says Spitzlei. “This enables us to control colour and register on the fly and results in much less waste. The optimised sheet travel and new dynamic sheet brake also make the operator’s work easier and boost productivity.”
Clients like Görres are attracted to the SX’s eco-friendly credentials, says Heidelberg, which calls the series the most environmentally friendly press in its class.
“The Speedmaster SX product range is designed to be as energy-efficient as possible,” says Hanlon. “Features such as the Airstar Central air supply system consume around 30% less energy than available systems from other vendors. Our presses are driven by brushless sinusoidal synchronous motors, which have the highest efficiency of 95% compared with regular DC motors with 90%.
“Combined with Heidelberg’s patented frequency control that allows the feedback of braking energy to the intermediate power circuit, the efficiency is unmatched. These motors benefit from wear-free operation, are also far quieter and produce less electromagnetic interference.”
He adds that Heidelberg is the only supplier to offer an integrated energy meter that can calculate and display the energy needed to print 1,000 sheets [kWh/1,000 sheets]. Hanlon says this
is the “only value that matters”. Energy efficiency is now displayed on the Prinect Wallscreen, underneath press speed.
As you’d expect from Heidelberg, a comprehensive range of support packages is available. Hanlon believes this has become a major factor in buying decisions. “Customers tell us that the first thing that comes to mind when they think of Heidelberg is excellent customer support.”
Going spare
Because the platform for the SX models is the established Speedmaster range with XL technology, upgrades and spare parts are readily available through existing spare part channels. Heidelberg ships spare parts worldwide within 24 hours from its existing world logistics centres based in Germany and regionally in Hong Kong and Atlanta.
This combination of a proven technology mixed with new technology, in addition to the eco-friendly overtures and first-rate service and availability of spares, make a compelling argument
for printers looking to upgrade, so it’s little wonder that sales to date vastly exceeded the manufacturer’s expectation. Hanlon, for one, expects this upward trend to continue.
“The first SX models are already entering into the Asia Pacific market where there is a high demand for long perfecting eight-colour SX 102 configurations.
“In Japan, for example, Heidelberg has installed the first low-energy UV SX 102-8P-LE UV press to meet the specific requirements of energy saving and low waste in the Japanese commercial printing market,” adds Hanlon.
During the economic crash of 2008-09, sales of perfectors fell significantly as printers went bust. But even though there are fewer print shops around today than there were five or so years ago, the presses seem to be back in demand with 70% of the units sold for the Speedmaster SX 102 for perfecting presses. If this trend continues the future of the SX range looks bright.
Specs: Speedmaster SX 102
Max sheet size 720×1,020mm
Min sheet size 340x480mm
Min sheet size (perfecting mode) 400x480mm
Thickness 0.03-0.6mm
Max speed 14,000sph
Contact
Australia: 1300 135 135
NZ: 0800 803 865
au.heidelberg.com
The Alternatives
KBA Rapida 105
Since its launch in the late 1990s, KBA’s machine has proved very popular in the commercial print market thanks largely to its flexibility. The 105 can switch from straight to perfecting mode in under two minutes and thanks to productivity enhancements introduced over the years, the Rapida now boasts a top speed of 15,000sph.
Contact KBA Australasia, 0419 616427, davelewis@kbaaustralasia.com.au
Manroland 700 HiPrint
The Manroland 700 HiPrint can be configured with two to 12 printing units, as short and long perfectors. There’s also an option for inline configurations with coating modules, foil enhancement, and quality control systems. The 700 has a standard sheet size of 1,040x740mm, but can also produce larger special sheet sizes of 1,050x740mm and 1,040x780mm. In straight printing mode it has a top speed of 16,000sph, which drops to 13,000sph in perfecting mode. The press can handle substrate thickness between 0.04 mm to 1mm.
Contact Manroland Australasia, (02) 9645 7900, www.manroland.com.au
Komori Lithrone S40SP
Komori launched a perfecting version of its S40 at Igas in 2003. Capable of running at a top speed of 15,000sph, the S40P can handle stock up to 0.45mm thick and according to the manufacturer
it’s possible to build versions with as many as 13 or 14 units. The perfector uses three double-size cylinders, which Komori claims gives very stable and precise sheet transfer without marking, even when the press is running at full speed.
Contact Ferrostaal, (02) 9338 3900, rayne.simpson@ferrostaal.com
Comment below to have your say on this story.
If you have a news story or tip-off, get in touch at editorial@sprinter.com.au.
Sign up to the Sprinter newsletter