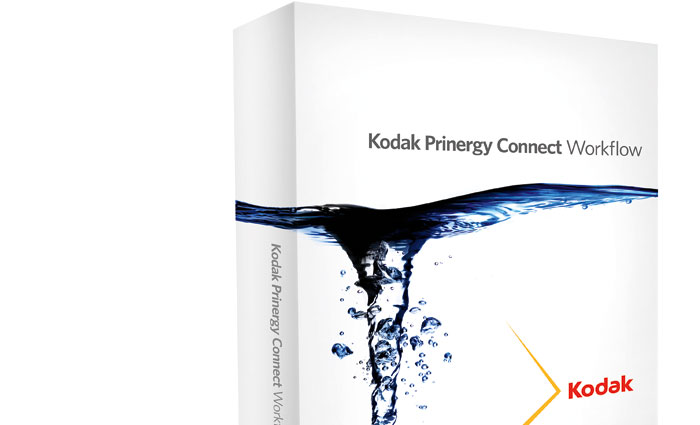
"The customer is always right”. It’s the age-old business adage that’s increasingly finding favour in these straitened times as customers look beyond the sheer quality of a product and take into account issues such as price and service.
The adage is driving Kodak through its ‘voice of customer’ (VOC) programme. In a nutshell, this programme seeks to gauge what clients are looking for. For the graphic arts industry, the VOC takes the form of a yearly seminar called the Graphic User Association, which is attended by printing companies from around the globe, including Australia.
The seminar gives attendees unprecedented access to Kodak product developers. Printers get to share their ideas about existing products and express their desires for future product launches; Kodak gets invaluable customer interaction and feedback.
Michael Smedley, business services and solutions group manager at Kodak Australasia, says: “Kodak relies on the VOC. Often the input of the Graphic User Association appears in future releases of Kodak’s software products.”
This was the case with the latest version of Kodak’s popular Prinergy workflow system. Although a new version was touted as far back as 2009, with many industry experts expecting a launch in 2010, the workflow was only given it global launch at Drupa 2012.
Causing a stir
It caused quite a stir. Kodak claims that Prinergy 6 goes even further than previous incarnations by bringing together a number of previously independent Kodak workflow products into one package.
“There’s a fundamental change in the way that we are selling Prinergy and its functions,” explains Smedley. “When workflow started, it was predominantly a RIP for a platesetter, but now we’re very much looking at Prinergy as a business process where it automates and connects to a management information system (MIS).”
This change of tack has been warmly welcomed by the select group of printers who have had the opportunity to play with the new workflow. Following a user group meeting earlier this year, Kodak filmed the response of printers in attendance to the new product. Phrases like “game changer”, “a big step forward” and “a dramatic leap in capabilities” were thrown around like confetti. Aspects that came in for high praise included the “very simple new user interface”, greater levels of flexibility and the fact that it “ties everything together in a web portal”.
The product’s warm reception is largely down to one word: automation. “Printers are becoming more automated, with a growing focus on digital print, integration with other systems and device management. Prinergy will be the hub of the production environment and the release of Prinergy 6 makes this vision a reality.”
At the heart of Prinergy 6 is an option called ‘rules-based automation’ (RBA). Smedley claims this can create business rules to “such a powerful level almost every process at many print companies can now be automated, Many rivals do not have this level of power.”
For Smedley, RBA is the main unique selling point of Prinergy 6.
“Often we show customers the rules-based automation ‘engine’ and discuss how much cost we can take out of a customer’s business by driving automation with Prinergy 6 and some of its options like Preps, Colorflow, InSite PrePress Portal [on screen proofing], web-to-print solutions like OPS and the Kodak ICW [digital asset management], plus many, many others.”
There are as many as 20 basic options within Prinergy 6, such as Preps and InSite. Within these options, there are “hundreds of sub-options”, says Smedley. He adds that the UpFront job planning tool has disappeared from general sale and been merged into Prinergy as standard.
This combination of different features is sure to go down well with Kodak’s strong Australian client base. Printers are increasingly waking up to the benefits offered by greater levels of automation. “Kodak is working with a high percentage of the biggest printing companies in Australia, and one of their primary focuses is automation,” says Smedley.
“Many people learn the hard way that the ‘devil is in the detail’ with end-to-end automation. Kodak has proven overseas and now in Australia that our software works and our team of experts can build these workflows for our customers. With the Kodak software many of our customers are even building this automation themselves.”
Although Prinergy 5 was a big step into hybrid production with digital and offset working as one harmonious workflow, version 6 “builds on that strength supporting more digital engines and robust VDP support”. The product is targeted at all print and media production companies, with a big focus on the packaging space thanks to the addition of new tools and options for Kodak’s packaging customers.
“In the past, Prinergy’s key strength was in commercial print. Today it’s the workflow of choice for digital as well as packaging and wide-format. Many print companies now have many different combinations of equipment, so Kodak is targeting this workflow at each vertical separately, but more importantly, showing customers that you can have one workflow drive all equipment in the same automated way,” says Smedley.
Beating rivals
Prinergy 6 features a number of other enhancements that Smedley believes elevate it above rival products. Colour management software is built into the heart of the workflow, meaning there’s no requirement to manage colour via a third-party system. It’s also JDF compliant and can connect to MIS and other compliant applications – Kodak offers custom development and can alter core applications to either JDF or non-JDF software.
Prinergy can be bought as a virtualised piece of software run from a cloud or it can be run off a server. If choosing the latter, the printer will need some “pretty powerful computing power, but Kodak is happy to help customers figure out the best option”, says Smedley.
It might sound too good to be true, but there is a minor catch. Those printers who have been waiting for version 6 for years are going to have to be patient, because it’s not going to be available until the first quarter of next year – and that’s just an approximate date.
When it does hit the market, Smedley is confident that sales will be strong among Prinergy users new and old due to the feedback the company received at Drupa, which was “very positive” with printers wanting more information about the new version.
“At Drupa, the workflow stand had the most visits of any area and many people voted the Kodak stand to be among the most visited. Therefore the feedback from the market is that Kodak ‘got it right’ with Prinergy 6,” claims Smedley. “The market is telling us that the focus on automation and connecting systems reflects the challenges the market has.”
As the price of Prinergy varies depending on the options taken, it’s difficult to say how it’s going to stack up with the offerings of rival manufacturers. Service contracts also vary, with Kodak providing full-service contracts to customers that covers upgrades, breakdowns and issue resolution in addition to preventative maintenance.
Smedley refuses to divulge what sort of sales targets have been set for the product in its first year of sale in Australia, but given Kodak’s existing presence in this country, the company could afford to be bullish, with Kodak’s workflows touching “more than 50% of all printed pages in Australia – in fact the market share in Australia is more dominant than many other countries throughout the world,” he claims.
With Prinergy 6’s ability to automate the production process by connecting all of the different parts and in doing so seemingly reduce costs, errors and time, it goes to prove that listening to what your customer says is a sensible and ultimately profitable approach to doing business in the modern world.
SPECIFICATIONS
Contact: Kodak Australia, (03) 8417 8000, www.graphics.kodak.com/AU/en
THE ALTERNATIVES
FujiFILM XMF 5
The release of Kodak’s all-singing, all-dancing new product at Drupa coincided with new incarnations of its three biggest rivals. At the show, Fujifilm unveiled the latest edition of its XMF workflow, with the focus on ease of use and offering the software to as many members of staff as possible. It adds an HTML5 web interface to XMF Remote version 9 that supports Android tablets. Online job submission and approval workflow were also added to Remote, with XMF benefiting from enhancements to the 3D proofing module, speed bumps to job rendering times and further integration with MIS systems. The company also revealed a new cloud-based colour management system – XMF ColorPath – that Fujifilm claims boosts efficiencies and reduces colour errors.
Contact: Fujifilm Australia, (02) 9466 2600, www.fujifilm.com.au
Agfa Apogee 8
Agfa also chose the halls of the Messe Düsseldorf to showcase the latest version of its workflow management suite, Apogee, which was demonstrated driving systems live at the show. The manufacturer claims Apogee 8 now offers greater connectivity and drives an ever-expanding range of digital presses. The new version supports 64-bit systems and offers optimised imposition for large-volume web printing systems. Another Apogee option unveiled at Drupa was a cloud-based web-to-print platform, Apogee StoreFront. Agfa says the tool makes it easier to set up online stores for printed and non-printed products.
Contact: Agfa Oceania, 1300 363 396, www.agfa.com
Heidelberg Prinect
The German company hatched a few new additions to its Prinect product range at Drupa, including a new MIS called Prinect Business Manager, to replace Prinect Prinance. Perhaps the most important addition is Prinect Digital Print Manager, which was born out of its recently forged digital relationship with Ricoh. According to the manufacturer, integrating Digital Print Manager into the Prinect print shop workflow creates a “seamless hybrid workflow between offset and digital printing that is unique in the industry”. Users have access to all of the functions of the Prinect workflow, such as job planning and standardised colour management, with the added benefit being that printers can manage and calculate both their offset and digital print jobs from a single workflow.
Contact: Heidelberg Australia & New Zealand, 1300 135 135, www.au.heidelberg.com
Comment below to have your say on this story.
If you have a news story or tip-off, get in touch at editorial@sprinter.com.au.
Sign up to the Sprinter newsletter