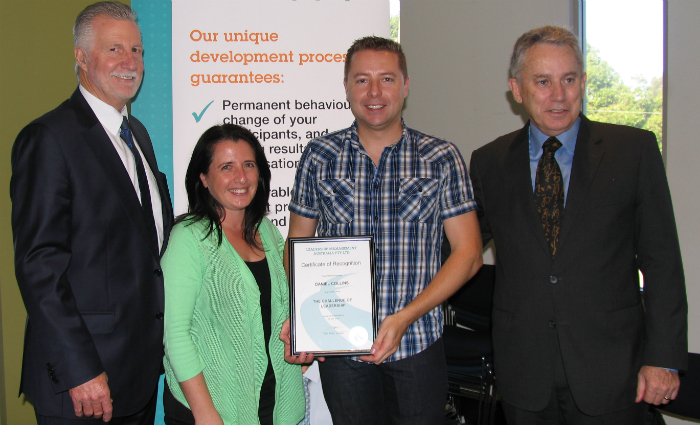
Sydney wide-format firm Look Print has added ‘enormous value’ to its bottom line by putting two of its managers through a leadership course that gave them the skills and confidence to get the most out of their teams.
Traffic workflow manager Daniel Collins and fabrication manager Jason Clancy underwent a Leadership Management Australia (LMA) course, graduating last Friday, paid for by Look Print, to improve the skills of its core management staff.
Collins removed 70 per cent of labour from setting up colour tests by using a colour comrade programme, and reduced waste, mistakes and inefficiencies in prepress operations by up-skilling staff.
He says all prepress staff were cross-trained to use all the equipment so the team had the flexibility to pitch in on any part of the process when needed.
“We tend to play to peoples’ strengths in this industry which is usually fine, but sometimes you end up waiting for someone because that is the only person who can operate equipment or knows a process,” he says.
“If everyone can do it, you won’t have any downtime,” he says.
[Related: More training news]
Collins says up-skilling the prepress staff cut interruptions for spot white file setups for 90 per cent; prepress pro-cut setup by 80 per cent; and significantly reduced reworks and reprints.
He says the course has helped him get better at time management, problem solving, delegating tasks and listening; he is able to trust his staff more and he is better at handling issues among them.
Senior managers now have more time to focus on strategic issues while he handles the day-to-day. Staff members now have more confidence and operate much better as a team to the point where things ran smoothly while Collins was on a four-week holiday.
Look Print chief executive David Leach says his company believes in investing in its staff and found the LMA course worthwhile.
“We believe everyone should leave Look Print better than how they came in. It’s better to train your staff and hope they stay than not to train them and hope they leave,” he says.
“I encourage all staff to come to me if they find a course they think would help them and if we see value to the company we at least subsidise it for them.”
Leach says every primary manager at Look Print has been through the LMA course and it is recommended for managers once they reach an appropriate level of seniority.
“Daniel and Jason are part of our core team and the projects they led have added enormous value to the company’s bottom line,” he says.
[Realted: More Look Print news]
Clancy managed to save the company an annual six-figure sum by mapping out the best delivery options.
“The goal was to maintain a 2.5 per cent or lower average freight income by May 2014. There were a few ways to achieve this,” he says.
“We established relationships with courier companies with better rates. We developed new ways of packing that not only lowered weights, but actually turned out cheaper.
We now consolidate freight headed for the same destination, and we’ve reduced the use of express couriers, late pickups and overnight deliveries.
“In the last couple of weeks we have hit our target, and the trend is going steadily where we want it to be. Return on investment is significant. We’re talking six figures per annum. It’s massive.”
Clancy says he’s keen to continue driving improvements in his department; with changes in the pipeline to redesign the fabrication area for better workflow and putting more accurate timings of how long each prepress, print and fabrication process takes into the scheduling system.
“The most pleasing aspect of the course was driving towards a major shift in cultural attitudes and focusing on new continuous improvement plans, and this course has given me the tools and the drive to be an active member of this change. I’m looking forward to keeping this momentum going.
Clancy’s mentor on the course, Look Print workflow and efficiency leader Darren Nellies, says he has seen big changes in Clancy over the 12 months of the course.
“He’s more receptive to new ideas now, and he is also relying on his team more than he was before. Before the course he was very much a hands-on person – if it had to be fixed, Jason was fixing it,” he says.
“The difference now is: it has to be fixed, how do we plan to fix it, and who do we get to fix it, and how do we maintain that. Before, it was – it’s here, how do I deal with it. His whole attitude has changed.”
Comment below to have your say on this story.
If you have a news story or tip-off, get in touch at editorial@sprinter.com.au.
Sign up to the Sprinter newsletter