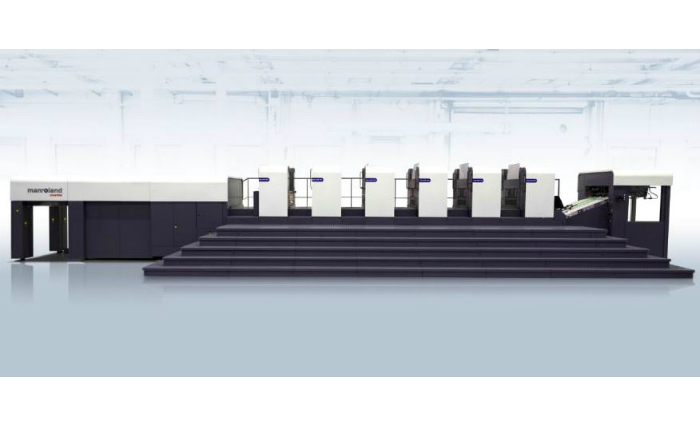
German press giant manroland has launched its first brand-new printing press in four years with a new version of the Roland 700 that the company says combines the best of all its presses.
The new press, branded Evolution, was unveiled at manroland’s German production centre, and while technical specifications are not yet available, it will supersede both the four-year old Roland 700 HS and 700 Direct Drive machines and produce what manrioland claims is ‘hitherto unseen’ quality.
The company says the Evolution press has taken all the best features of the Roland 700 HS and DD models and made one machine in an all-new design built from the ground up.
The new Roland 700 Evolution represents a milestone in the manroland journey, it is the first new press since the company was battered in the aftermath of the GFC and separated into separate sheetfed and webfed operations.
[Related: More offset news]
Features manroland will discuss include nine new technological developments aimed at improving efficiency, productivity, operation and quality, while saving on production costs.
“From the DD comes the multitasking features of operations done in parallel and from the HS comes the feeder, delivery and dampening system,” the company says.
“It also has a new operating console and a simple interactive operating system with a mobile app using QR codes so you can see your press and production when you’re on the move.”
The manroland sheetfed head of research and development Stefan Finger says advance orders have been flooding in with ‘several’ customers signing up during the trial stage.
“We observed the challenges faced by the market, we listened to our customers and we learnt from the daily experiences of our own printers in our Print Technology Centre,” he says.
“Our preliminary demonstration and trials of the new press to the first customers were encouraging and we knew we were on the right track.
“The number of customers registering for the launch event has exceeded our expectations; the demand was such that we have now included an additional day with some more dates in the new year.”
A new central console replaces buttons with touchscreen panels, giving graphic information for better flexibility and comfort for the operator.
The new feeder pile transport aims for productivity and improved sheet travel from the feeder to delivery with fewer interruptions, less start-up waste and less walking distance to the feeder.
Manroland has solidly fixed the suction head to reduce vibration and wear while ensuring safer sheet separation and higher average printer speeds.
[Related: More machine launches]
The press also has completely redesigned cylinder-roller bearings, with separate bearings for radial and axial rotation for longer life and better print quality.
New dampening units bring greater solidity and lessen vibrations during passing of the plate cylinder channel, meaning fewer stripes as well.
Software for practice-oriented roller washing cycles reduces downtime and makes for a more precise dosage of the dampening solution across the entire width, reducing the possibility of skewing the dampening dosage roller.
A three-phase AC motor makes for lower energy consumption with higher power output. Manroland says the machine has no need for wearing parts, carbon brushes or additional costs for part, helping it to further cut down on unproductive time, strengthen the market position of printers and raise its green credentials.
The Evolution also features a new chambered doctor blade system, which the company says will exceed expectations in the gloss effects it can produce.
The system, with additional profile, aims to provide higher solidity over the width of the doctor blade, and a more even varnish application.
Manroland says that not only does it feature better absorption of vibrations from the Anilox roller and doctor blade caused by passing the coating form cylinder, it also results in fewer stripes, especially in combination with pigmented varnish.
New suction belt sheet brake technology offers higher printing speeds, with improved sheet alignment and tail edge stabilisation. This gives a more even pile contour and reduces the risk of misaligned sheets in the delivery pile.
Comment below to have your say on this story.
If you have a news story or tip-off, get in touch at editorial@sprinter.com.au.
Sign up to the Sprinter newsletter