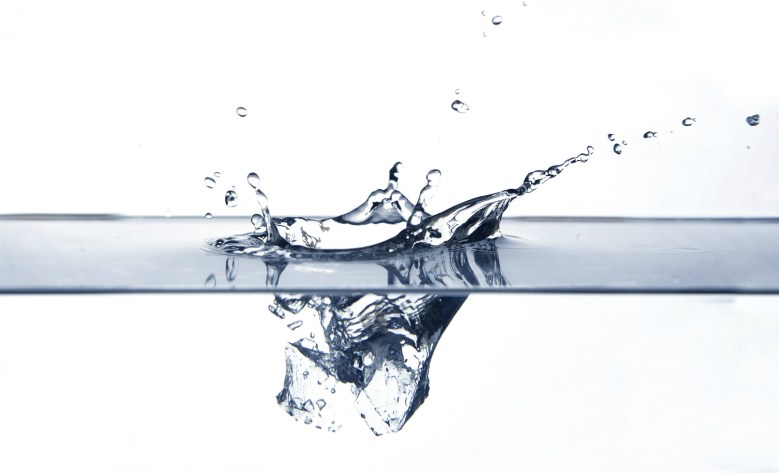
The decline in offset printing volumes across the world has hit demand for printing presses. It has not though had the same impact on demand for printing plates as it has on paper, because every job, no matter how short or long, requires a new set of plates. And with an increasing trend to short runs plate volumes are holding up.
This emphasis on short run puts an onus on the plate, the ink, blanket and fount chemistry to work in concert to reduce waste and enable the press to get running as rapidly as possible. No printer can afford to be producing more than the minimal amount of waste, either in time or materials.
When UK company ESP first started to work on the processes that enabled it to print more than 80 million impressions on a press a year with considerable emphasis on short print runs, it needed an ink which could cope with the rapid accelerations in press speed to 18,000sph without causing ink fly or the ink splitting, and then to zero after a few hundred sheets had been printed. It needed a blanket, fount and plate that would perform just as well. It went through a lot of suppliers and combinations before it was happy.
Not everyone needs this type of performance, priorities may lie elsewhere. For some the emphasis will be on reducing the environmental footprint, using a develop on press plate perhaps, a fount without IPA and inkset that uses vegetable based oils. Whatever the goal, the intention is to discover a trouble-free combination of consumables that suits the press and operating conditions.
It is one of the benefits of working with Heidelberg’s Safira branded consumables. These have been thoroughly tested by the press manufacturer for effectiveness. It also means a single call when something throws the press out of balance as it inevitably will. Within the range there are Eco versions to minimise environmental impact as well as more conventional approaches.
Flint Ink has gone a step further with Vantage, designed as a one stop solution for LED UV printing in partnership with lamp and diode supplier AMS. “The is a turnkey solution, from calculating the ROI to installation and helping a printer market its services afterwards,” says marketing director Peter Baird. Flint takes on everything, from a pre installation assessment, to installation of the LED system and provision of the consumables to a certain amount of training.
The blanket plays a key role in delivering performance. Different coverings are needed for UV inks as they are for rollers. But the aim is still “to provide solutions for end users to make their life easier” according to regional sales director Matthias Horn. Blankets have been refined to match high speed presses, packaging requirements as well as UV. The environment is a key focus says Horn. “We have a produce which helps to reduce the need for washing during a run and to allow printers to move from job to job without always needing to wash up blankets,” he says. “Printers will tend to avoid a blanket wash if they can. This is not designed to eliminate the need for washing, but to meet demands for printers to be more efficient in handling short run jobs.”
Fujifilm has adopted the name Superia (It had been used on a range of 35mm films in the old days) for its consultancy of consumables package. “It is about resource savings and delivering a financial benefit,” says Sean Lane, Fujifilm EMEA product group manager. “We lookout the complete product range in offset, measured five factors: labour, costs, energy, water and the materials. The idea is that a printer will be able to save money by becoming more environmentally friendly.”
There is an app which is an ROI calculator, delivering a comparison of the consumables a printer currently uses against those in the Supra programme. And this assumes the use of manufacturers’ recommended settings for a press and so on.
It shows that one plate can use considerably less water and energy than another for example, showing the savings that can be achieved. “Being smarter in plate production gives measurable savings,” he says. On top prepress software can help with ink optimisation as thinner films will use less water on press, will create better operating conditions and deliver a brighter result.
Fujifilm announced the introduction of a process free plate, Superia XD, as part of the programme. This is a develop on press plate that can cope with UV inks and longer runs than the Pro-T3 plate which has carried the flag for develop on press plates at Fujifilm. The new plate has a refined graining structure which delivers a better ink/water balance, a more resilient surface and changed coating with greater hydrophilic properties for the non image area.
Develop on press technology has leapt forwards in recent years. The sensitivity of coatings combined with the power of lasers has helped make it easier to image the plates and new types of coating provide higher contrast of the latent image.
Agfa’s Azura plate has had most of the process free market to itself. While not a develop-on-press plate, it requires no chemistry to process and only a gum to protect the surface on the way to the press. It has a decent image contrast and with successive generations of plate, has increased run length and moved running this type of plate from the preserve of smaller printers into the mainstream. While it is not recommended for web offset or packaging, almost every other application is possible including VLF. The Azura TE fills the develop on press gap, more as like for like for customers already using develop on press plates than because Agfa feels this is the better option.
But process free is not always the answer. Fujifilm has promoted the idea of low-chem plates and at drupa Agfa showed that it is following up. The Energy Elite Pro can cope with harsher conditions yet no longer needs baking. It also comes with a dedicated processor designed to cascade water through the system so that cleaning water becomes processing solution to minimise consumption.
“It uses only 40 per cent of the volume compared to a standard processor,” says Paul Andriaensen, head of marketing. “And just 30ml of chemistry is needed to process four plates. The waste bath only needs cleaning after 20,000 plates and then it takes just 15 minutes to clean.
“For many printers that means cleaning just once or twice a year,” he says. “We are taking the ideas and experience we have from chemistry free plates to conventional platemaking.
“We believe there is still a need for conventional plates: the Energy Elite Eco will run to 600,000 impressions without baking which makes it a very interesting plate for customers that are still producing long runs.”
Kodak by contrast is convinced that develop on press is the future thanks to the success of Sonora. It has quickly become a mainstream product for Kodak and one of its products for the future, accounting for 16 per cent of the company’s revenues, some US$120m a year, and doubling in the next four years.
The latent image is strong and the image area can be seen clearly before mounting on press. There is no penalty in the platesetter where previously output might be limited. The plate is also far more durable, good for tens of thousands of impressions. And good for large users as well. Kodak has signed a deal which will mean 30,000sq m of Sonora plates a year to one customer.
It has invested heavily to improve facilities at sites in the US and Europe to keep up with rapidly increasing demand. It reckons that 30 per cent of all plates worldwide will be process free by the next drupa.
“Over the next four years, pretty much the whole industry will shift to process free plates says Kodak senior vice president Brad Kruchten. “This saves a huge amount of water and energy. And the plates will be suitable for a growing range of print and packaging applications.” Currently these are served through Electra Max or the Sword negative plates though a Sonora UV plate is coming.
Kruchten says: “It has been launched in Japan and is in beta testing elsewhere. It will move to controlled sales in Q4. We see great opportunity for packaging applications. We believe that by the next drupa, the majority of litho plates will be process free.”
Presstek was ahead of the game with image on press as well as develop on press plates with its own presses. It has long offered a selection of different plates which have failed to make a significant impression. It is optimistic that its Nytro plate, produced at a company it acquired earlier this year, can change this. It is a negative working plate processed in a soapy solution which is flushable according to some local authorities, and is good for 500,000 impressions.
The problem is there is still a premium attached to process free plates. Some printers, while appreciating the environmental benefits, continue to be motivated by price. These are likely to be offered a choice of thermal plates as the original patents begin to expire next year and as improvements in laser diode technology have made it possible to expose presensitised UV plates at acceptable speeds.
Manufacturers of this type of plate have not concerned themselves too much with achieving the consistency needed for direct imaging in the past: it was too slow and while it was attracted attention of those using large amounts of plate, computer to conventional plate has never become mainstream.
The Chinese might change this. Cron has built a plate factory to produce plates for its own platesetters, initially UV sensitive plates and shortly thermal and process free plates. Another Chinese plate is known as the Certus Aqua+. This takes a different approach to improved environmental performance, claiming that in use, the plate needs 25 per cent less water which in turn means ink consumption is reduced by 10 per cent. Currently the plate is undergoing final testing around Europe and the US, apparently to positive feedback.
There will also be gains from improved rub resistance, faster drying and reduced paper stretch.
The difficulty will be in trying to dislodge the big three suppliers, let alone the secondary companies like IBF in Brazil or Ipagsa of Barcelona, which produce very acceptable plates. Printers should look around, they might find there are appealing alternatives available.
Comment below to have your say on this story.
If you have a news story or tip-off, get in touch at editorial@sprinter.com.au.
Sign up to the Sprinter newsletter