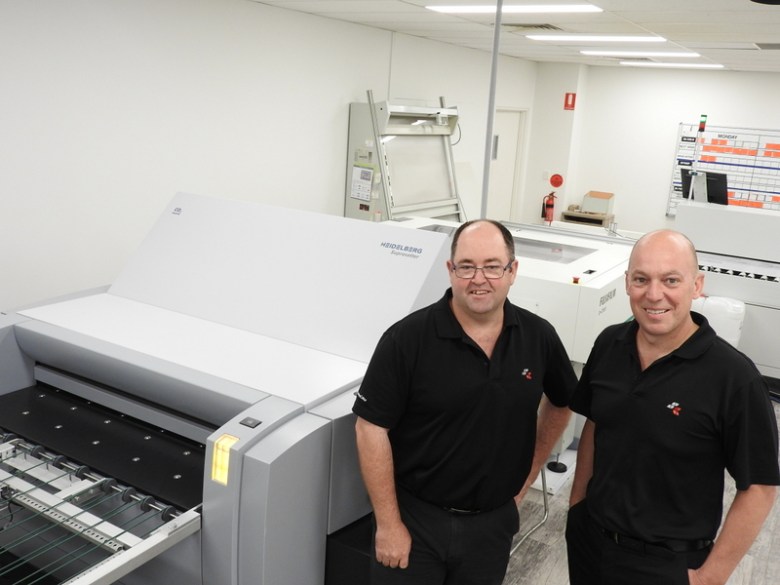
Melbourne’s Southern Colour has achieved a fully-automated platemaking process, using a combination of Fujifilm, Heidelberg, and Nela tech.
The plate room is operated by one employee, a multi-tasker who receives an alert that the 660-plate skid is running low and another skid needs to be positioned for acclimatisation, before the empty skid is removed and the already-acclimatised one is positioned.
Southern Colour says at 42 plates per hour through the Suprasetter and Superia ZAC processor, there is more than enough on a single skid to service a 12-hour shift.
The company, one part of Southern Impact Holdings, says its offset litho plate production can rise to 8,000 sqm or more per month in peak times. Southern Impact Holdings owns Southern Colour, Impact Digital, Intelligent Media and new label printer Onpack.
Southern Colour's Heidelberg XL106-10 colour and XL 106-6 colour with coater operate 24 hours four days a week, with 12-hour shifts for two days. Southern Colour says a constant uninterrupted plate supply is called for to keep up with the Autoplate changing, on-the-fly register control and piped-in Technotrans/ToyoInk automatic ink delivery used on the presses. The Prinect workflow is JDF-driven, integrated with Heidelberg’s Business Manager.
Job ID information is Data Matrix (QR) coded and tracked throughout the entire production workflow.
Allan Gardiner, prepress manager, Southern Colour says the decision to fully automate plate production dates back to the drupa 2016 exhibition, with the new XL 106s having been ordered by Rod Dawson, managing director, Southern Colour at drupa 2012.
“We happened to see an Auto Pallet Loading device made by German company Graphoteam, on the Heidelberg stand. It was automatically lifting plates from a skid, removing interleaves and feeding them into a Suprasetter CtP device which in turn transported the exposed, punched plates into a Fujifilm lo-chem processor and onwards to Nela bending. What impressed us was the complete absence of human intervention, apart from removing empty pallet skids of plate and placing a fresh one ready for uninterrupted supply. All this was at a rate of 42 B1 plates per hour.”
Richard Timson, managing director, Heidelberg ANZ, says “It is a purpose-built plate production system unlike any other. There are only a handful of similar installations in the world, in places like Switzerland and Austria.”
The Suprasetter 106 is certified CO² neutral and the Fujifilm Superia system delivers savings in five key areas – water, energy, emissions, labour and chemistry. This is achieved with a ZAC lo-chem processor for the Superia LH-PJE positive working plates. The ZAC system intelligently uses a fraction of the chemistry and water of the previous Agfa-based system by accurately sensing developer bath conductivity and pH and injecting only the exact amount of replenisher, rather than a fixed dose every so often.
Gardiner says, “We prefer to see a latent image on the plate and the positive Fujifilm plates provide this for quick recognition. We’ve noticed a reduction in plate processor maintenance and down-time for cleaning and chemistry changes.
“The Fujifilm ZAC system runs a lot cleaner and therefore requires only routine service calls about every three months. This in turn increases productivity and uptime of the entire system.”
He also notes a reduction in plate scratching due to less human intervention. The Graphoteam APL automates slip sheet removal and plates are suction-fed to the Suprasetter.
Colour is managed throughout production to both ISO 12647-2 standard and extended-gamut custom profiles for specific clients. One such client is the Dulux Group, which awarded Southern Colour the Supplier of the Year trophy for 2017.
Southern Colour says colour management in the workflow is RGB up to the point of in-rip CMYK conversion, via the Prepare Sequence inside Prinect. Colour bars are automatically assigned for the job profile and press, while Prinect’s Calibration Manager also greatly reduces the need for human intervention for measuring and calibrating devices.
Gardiner says, “Our press operators receive plates on a trolley that are in the correct colour sequence, for the correct press and for the next job shown on their production screen and ready to be queued in the Autoplate loader.
“If, on a long-run, a plate wears out the printer can easily order a replacement on-screen. The system then knows what plate/s are needed, sends the data to the plate line and within minutes the replacement plate is stacked and ready for loading. If this happens at 2am on a night shift, it’s no problem as there is no need for people to be present in the plateroom.
“Throughout the whole process, the job I.D. is there and constantly updated, such as adding the press operator’s name and time taken on press. This greatly helps with MIS.”
Every job produced at Southern Colour has a mock-up, printed using a Ricoh Pro C5100S SRA3 digital printer and EFI front-end, which was also supplied by Heidelberg. The job file is de-constructed in the software for 2-up digital production and printed in order so customers can see a content proof of their 16, 32 or higher page magazine, catalogue or manual for checking.
Comment below to have your say on this story.
If you have a news story or tip-off, get in touch at editorial@sprinter.com.au.
Sign up to the Sprinter newsletter