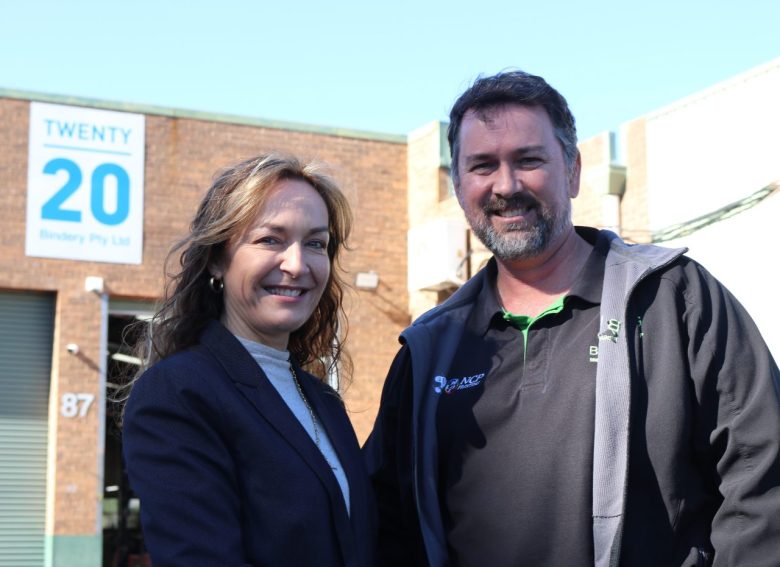
This article was first published in a Sustainable Printing and Packaging technology feature in the February 2021 issue of ProPrint. To read the magazine, please click here.
Bright Print Group – a dynamic family-owned NSW print business – has blazed a trail when it comes to sustainability.
Co-directors John Bright and Debbie Burgess say the sustainability goals of Bright Print Group (BPG) are not just limited to machinery and consumables but are also reflected in the attitudes of tradespeople and staff who consciously maintain these habits.
“Since 2008, BPG has held the internationally recognised accreditation ISO14001:2015 Environmental Management System. Initially this accreditation created the need for an overall shift in company thinking but as time passed, environmentally conscious methods and questions have become part of the everyday conversation,” Burgess told ProPrint.
Bright and Burgess apply numerous environmental safeguards within their company.
In 2019, BPG installed an Agfa Arkana Processor which limits production waste due to its use of cleaner and fewer chemicals than the previous model. It also eliminates the need for rinse water.
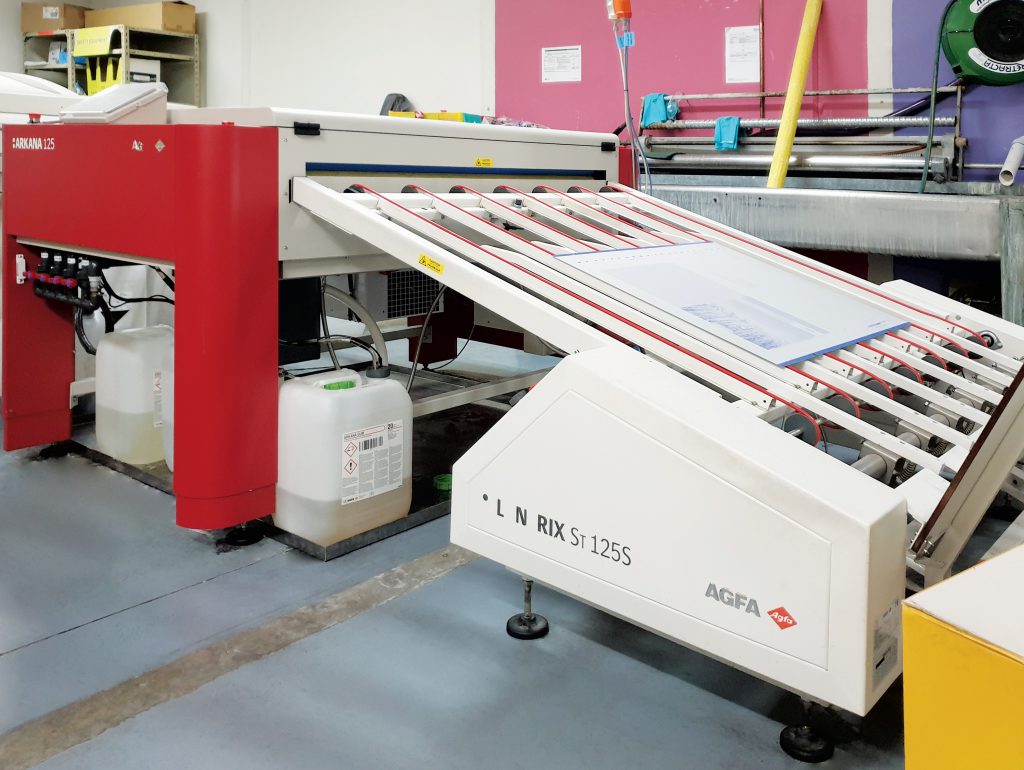
Then in 2020, BPG installed a PlateRite 8600 NII Z + SA-L8900 Auto Loader from Screen GP.
This device has improved operational efficiency, as well as having power saving and standby modes, greatly reducing energy consumption compared to previous models.
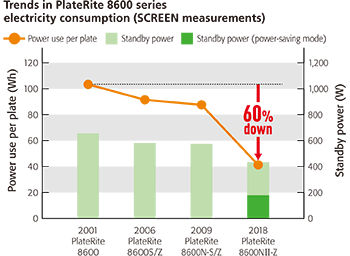
In the wide-format area, BPG’s two primary presses (producing 75 per cent of all work in this area) are LED, eliminating the need for mercury disposal and ozone gas extraction. This also results in significantly reduced energy consumption.
In 2018, BPG asked air compression specialist, Kaeser, to perform an analysis for an improved compressed air system due to the introduction of the wide-format department.
Kaeser analysed the power consumption and energy efficiency of the existing system and presented new scenarios, demonstrating energy efficient comparisons.
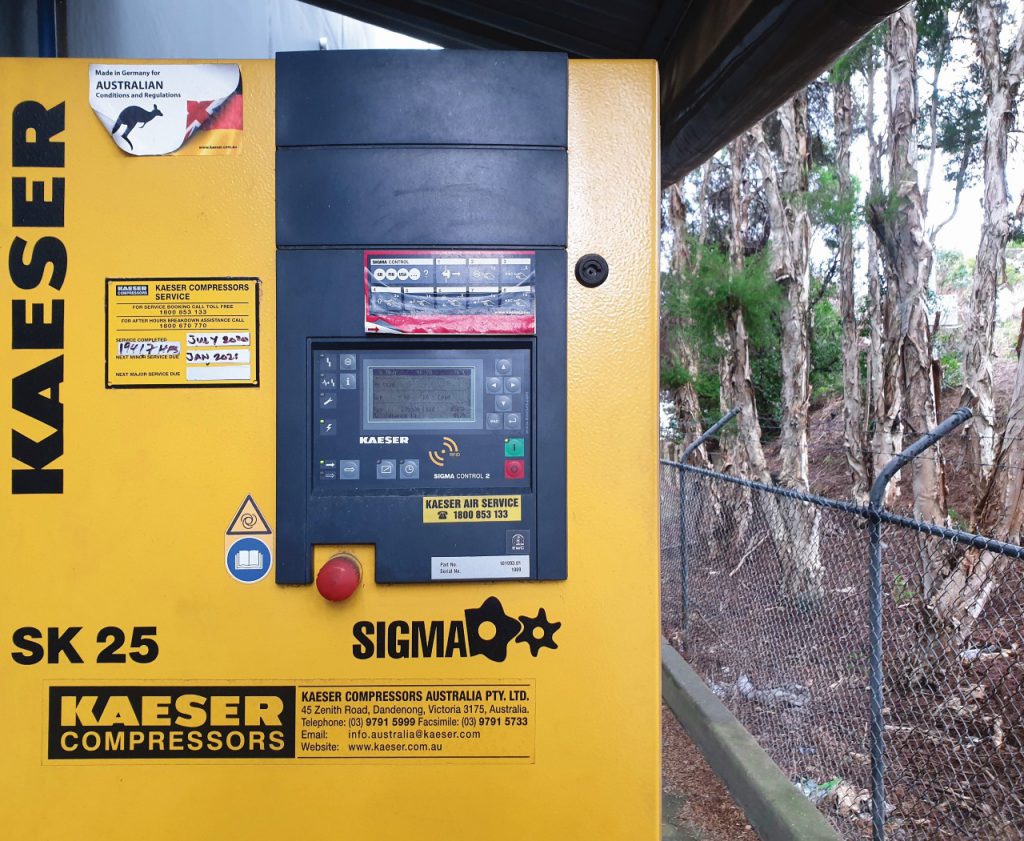
“This enabled us to choose the option which best fit the current circumstances and provided a viable solution for the next five-to-ten years. The existing Kaeser Aircentre 15 was kept, and in conjunction, a new Kaeser Aircentre 25 was installed,” Burgess says.
“The Aircentre itself is an all-in-one compressed air system with a rotary screw compressor-block, and energy saving Sigma Profile rotors. Designed for maximum energy efficiency, this profile can achieve power savings of up to 15 per cent compared to conventional screw compressor-block rotor profiles.”
Solar panels
In the electricity space, solar panels are installed at both the BPG and NCP Printing facilities. The company has been able to reduce consumption from the grid by an average of 33 per cent daily.
Sensor lights are installed in amenities and lights are switched off in common areas when not in use.
In 2008, BPG installed a water recirculation unit on its CtP processor which at that time saved a staggering 92 per cent of water use, says Bright.
“With technological improvement and progressively more environmentally efficient methods, we now have a CtP processor that needs no rinse water,” Bright said.
“For the little water that is used throughout the factory, we have a Sydney Water-authorised onsite sub-ground pit designed to filter water, should there be any contaminants present. Our primary use of water now is via staff amenities.”
Recycling
Looking at recycling, BPG has several streams throughout the company.
Office printers, a proofer and digital press ink cartridges are recycled with Planet Ark. Staff are also encouraged to bring cartridges from home for recycling. Soft plastics such as pallet wrapping are compacted onsite in the Elephant’s Foot for collection by recycling contractors.
The company also uses recycled plastic within its despatch department and asks its suppliers to minimise plastic packaging wherever possible.
All paper waste generated by jobs or general miscellaneous paper waste is shredded by BPG’s onsite industrial paper shredder and collected for recycling.
In partnership with recycler Corex, production waste from wide-format jobs using polypropylene and corflute is collected regularly for recycling.
Burgess explains that all lithographic inks are soy-based, and spray powder is fully digestible.
“UV LED inks used for our Jeti and Anapurna wide-format presses conform to the stringent Greenguard certification,” Burgess says.
BPG also does not generate any toxic emissions.
“All our chemicals are environmentally friendly and low volatility – most chemicals are water miscible,” Burgess says.
“The few chemicals still used for machinery maintenance, such as oil, are stored and collected by licensed waste contractors.”
Burgess says NCP, the company’s purpose-built printing facility in Mayfield West, utilises building materials that were determined on acoustic and thermal qualities, insulation, cross-ventilation and also features a sophisticated air extraction system that utilises temperature-controlled energy efficient automation.
“It all helps to maintain a constant temperature within our factory area, without the need for air conditioning and the associated high energy use. Induction lighting, new compressors and better digital technology assist with minimising our carbon footprint,” Burgess said.
If you enjoyed this story, you may also like this recent Star Business profile on Bright Print Group, please click here to read it.
Comment below to have your say on this story.
If you have a news story or tip-off, get in touch at editorial@sprinter.com.au.
Sign up to the Sprinter newsletter