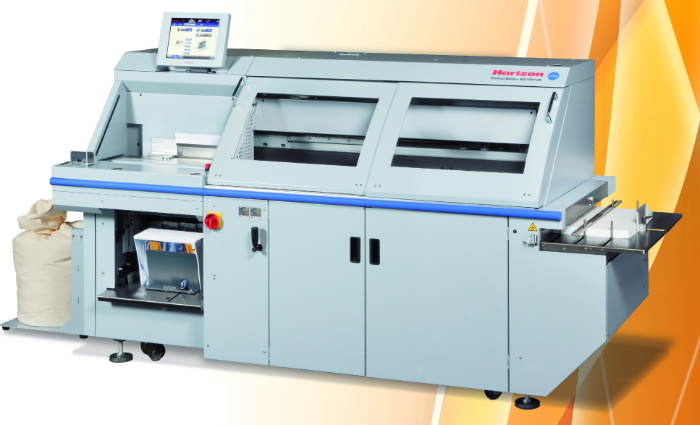
CANON IMAGEPRESS FINISHING
An array of inline finishing solutions is available for Canon imagePress digital colour presses, including hole punching, stapling, folding, stacking and perfect binding.
The most popular option is a Booklet Finisher that can combine stacking, stapling, hole-punching and saddle-stitching in the one device. It provides the flexibility to neatly stack flat sheets for easy offline or near-line finishing along with the ability to produce fully finished saddle-stitched booklets.
Saddle-stitching is the most popular finishing choice for high quality, digitally produced, multi-page documents such as brochures, guides and catalogues. This is due to the low cost of finishing, the ease of production and the quality of the finished product.
The saddle-stitcher available for the imagePress produces professional looking booklets of up to 100 pages, including a cover of up to 300gsm. A saddle press applies even, consistent pressure along the spine of the booklet to reduce bowing, and the staples are flat clinched to ensure they sit flat on the sheet. Three-knife trimming ensures full-bleed booklets are produced ready for distribution.
The inline saddle-stitching solution – with three-knife trimming – saves labour, time and money in the production of booklets. A booklet with more than a few pages runs at the rated speed of the press, and no additional steps are required in the production of full-bleed booklets other than packing and distribution.
The Canon Booklet Finisher with Trimmer module needs no third-party finishing to be added to the digital press in order to produce fully finished, full bleed saddle-stitched booklets. Canon says its inline solutions requires a capital investment around 25 per cent less than an equivalent third-party inline or near-line finishing solution.
Little additional training is required for operators to produce fully finished booklets, and servicing is provided by the same engineer who services the Canon imagePress.
SPECS AT A GLANCE:
Finishing options: hole punching, stapling, folding, stacking and perfect binding
GMP PROTOPIC AUTO QUATRO SLIT LAMINATING MACHINE
The new range of laminating equipment and specialty digital films from Korean manufacturer GMP, distributed through Renz Australia, is assisting printers to add new revenue streams from new and existing customers.
Aimed at the digital on demand market, the Protopic Auto Quatro Slit is an example of the flexibility and new revenue opportunities one machine can offer. This machine automatically feeds and bursts the laminated media and in the one machine can provide four value-adding embellishments to digital prints:
- single and/or double sided lamination/celloglazing;
- single and/or double sided photo matt or texture embossing;
- digital sleeking, producing a range of full sheet or spot effects with metallic foils, gloss or matt coatings;
- patented GMP Slit Book technology which produces an inner hinged book block for lay flat photo books.
- Apart from traditional laminating and celloglazing, the GMP Protopic Auto Quatro is capable of producing photo prints (silver halide replacement), photo books and photo calendars to a booming market sector. The silver halide replacement technology produces photo prints and/or finished printed images that look and feel like traditional silver halide photographic prints. This reduces the cost by 50 per cent compared to traditional silver halide processing and also provides obvious environmental advantages.
- Digital sleeking, which is an easy way to achieve special effects such as spot varnish, metallic foil stamping and holographic effects in-house. The process involves a special image transfer that bonds specifically to HP Indigo inks and other digital toners applied in spot locations or to the full sheet, creating a wide variety of special effects and designs.
- The Slit-Book system can produce the inner book block of a lay flat photo book. The process comprises a pre-bonding and inline guttering device that creates the book hinge prior to lamination. Compared to most existing solutions Slit-Book can produce a lay flat book block at a lower cost with far more choice and flexibility in different finishes.
The fully optioned version of the Protopic Auto Quatro Slit can be financed for as little as $370 per week (subject to finance approval), including delivery and installation. Comprehensive training is also provided with ongoing operator and technical support nationally from Renz Australia.
SPECS AT A GLANCE:
Max laminating speed: —
• slit book lamination: 5m/min
• single glossy lamination: 15m/min
• duplex glossy lamination: 7m/min
• single photo matting: 3m/min
• duplex photo matting: 3m/min
Laminating films: Polynex, Perfex, Nylonex, Micronex, Photonex
Substrate weight: 120-300gsm
HOHNER DIGIFINISHER
Cyber Australia, distributor of the Hohner Digifinisher, says that it is ideally suited to printers who have recently invested in digital print engines to complement an existing litho department.
The Digifinisher is designed to tackle complex finishing jobs that require collation and binding of numerous pieces, with individual items different in size or content.
For example, it would suit printed personal accounts and reports for the financial market, with the need to combine personalised information which has been digitally printed in sequence, variable from person to person depending on the size of their investments and overall portfolio. One book may have 24 pages, the next eight, followed by a 36-pager, and so on. Each customer may have a six-page preface letter followed by a glossy cover. Cyber says The printer must have verification that each and every book, without fail, matches the personalised cover.
Another example is a security printer which has landed a contract to produce school examination papers. In this instance the documents are not printed on flat sheets, but on a continuous reel.
The brief says that each page must be personalised to each student. There are 30 pupils in year one, taking six subjects each. The number of pages for each pupil will vary depending on which subject he or she is taking. There may be 20 pupils in year two, taking five subjects, but their papers will contain more pages due to slightly more complex question papers. Eventually year six will have fewer students, but each one will have considerably more pages in each subject. Such complex finishing problems can be tackled by investing in a Hohner Digifinisher, says Cyber.
This system is based around a Hohner HSB 8000 Saddlestitcher fed by either a flat sheet pile feeder or an optional continuous reel feeder. A number of barcode optical recognition systems are available to provide complete security.
Two-up production and hole punching inline are also options.
SPECS AT A GLANCE:
Speed: 8000 cycles per hour
Max untrimmed spine length: 365mm
Min one-up format size trimmed 95 x 65mm
Min one-up format size front trim only 95 x 65mm
HORIZON BQ-280PUR PERFECT BINDER
Horizon’s BQ-280PUR Perfect Binder is specially designed to handle the requirements of digital print – with digital print friendly processing, quick set-up and changeover for shorter production runs, book-of-one capability, and even inline verification for document integrity.
The BQ-280 also uses environmentally-friendly PUR glue which meets the requirements of lay-flat binding for both offset and digital prints as well as coated stock.
The large colour touchscreen features intuitive icons for easy operation. Just input book block and cover information at the touchscreen for quick and automatic setup, including carriage clamp, milling, glue tank, nipping and cover feeder.
Book thickness is automatically measured by placing the book block into the digital caliper. The caliper slides into position with no manual intervention and thickness data automatically begins set-up. It handles the production of digitally printed books, personalised photo books, smaller sample runs and other ultra short-run work.
It will handle book block sizes of minimum 135 by 105mm up to a maximum of 385 by 320mm, and book thickness of 1mm up to 51mm. Cover weight range for normal paper is 62 to 302gsm, and for coated paper is 105 to 349gsm. Cover pile height is up to a maximum of 70mm. Milling depth is up to a maximum of 4mm. Production speed is up to 500 cycles an hour.
SPECS AT A GLANCE:
Min book block size: 135 x 105mm
Max book block size: 385 x 320mm
Cover weight range: 62-320gsm (uncoated) Cover pile height: 70mm
Max milling depth: 4mm
Production speed: 500 cycles per hour
MGI JV-3DS SYSTEM
The new JETvarnish 3DS is designed and manufactured by MGI and Konica Minolta to help printers expand their services with spot UV and 3D tactile varnishing capabilities, with inkjet productivity and efficiency benefits.
Designed primarily for the digital print market, the JETvarnish 3DS will make the popular 3D tactile varnish finish available to all digital printers printing on widths up to 360mm. The JETvarnish 3DS can turn regular printed jobs into high-margin spot UV jobs, or even higher margin 3D embossed jobs with up to 100 microns of varnish applied to the sheet, which lifts the image from the page and adds a higher level of sheen to colours.
The new varnish formula, combined with Konica Minolta print heads, can create a 3D effect on laminated surfaces or on toner directly. The variable data option adds full personalisation capabilities for maximum one-to-one marketing impact.
Print speeds are up to 4,800 A3 sheets per hour in flat mode (2D) and up to 1,500 A3 sheets per hour in 3D mode.
With single-pass printing, the JETvarnish 3DS is a UV spot varnish device. The digitisation of spot UV finishing allows printers to take a few sheets from each job and spot UV coat it so customers can see the effect their jobs could have, making the 3DS ideal for lucrative short- and medium-run printing.
The combination of MGI’s inkjet technology with Konica Minolta’s drop-on-demand Piezoelectric print heads enables lines as small as 0.5mm or as wide as the sheet.
JETvarnish 3DS HubManager production software allows printers to follow jobs, manage job queues, create job tickets, recall reprints and adjust ARC camera systems in one tool. A function exports detailed production data for internal costs for analysis and reports. The Spot Varnish Editor is designed for editing job files on the fly, so the operator can adjust and modify print jobs on the fly to save time and money. The Product Cost Analyser calculates production costs to one-tenth of a cent, and gives customers precise information on consumable costs per print job before the job has been printed.
The JETvarnish 3DS is equipped with Automated Registration Camera (ARC) technology designed to calibrate (on the fly) coating registration from sheet to sheet. The first camera reads printed marks and automatically corrects for changes in the X and Y position of each sheet. The second camera detects the paper skew and makes adjustments on the fly. The ARC system ensures accurate spot UV coating, even on jobs with inconsistent print registration.
The JETvarnish 3DS is able to spot varnish on toner and offset prints with and without lamination, making print workflows more flexible and easier.
Sales and service are available through Konica Minolta Australia’s direct and dealer network across Australia.
SPECS AT A GLANCE:
Coating thicknesses: Depends on file, inks used, type of surface
Laminated and aqueous coating: 15μm – 100μm for 3D raised effects and tactile finish
On toner and coated paper: 30μm – 100μm for 3D raised effects and a tactile finish
Production speed: Up to 4,800 A4 sheets/hr in flat mode (2D); Up to 1,500 A4 sheets per hour in 3D mode
Registration: Automated registration with MGI ARC system
Overall registration: ± 200μm
Min format: 210 x 300mm
Max format: 364 x 1,020mm
Max printable width: 355mm
MORGANA DIGIFOLD PRO CREASER/FOLDER
Ideal for digital through to large offset printing companies, the Morgana DigiFold’s price includes delivery, training and 12 months’ warranty, both electrical and mechanical.
DigiFold has been Morgana’s flagship product since its introduction in 2001.
In this latest version the speed has been increased by 20% and Morgana has added the touch screen as with all Morgana Pro models. This intuitive screen allows the operator to control all the functions of the machine. Set-up takes seconds and can be as simple as pressing three buttons: stock size, fold type and the GO button.
The alphanumeric memory allows jobs to be named and saved, and with a simple search function allows them to be quickly retrieved. This versatile machine has several uses:
- As an integrated creaser/folder performing both functions in a single pass
- As a “stand alone” creaser when folding is not required
- As a perforator when neither creasing nor folding is needed.
The vastly increased speed now makes the DigFold Pro a viable proposition for litho
printers who suffer the same cracking problems as digital printers. Using Morgana’s patented flying knife technology they can ensure that there will be no scuffing or marking on digital stocks that are caused by using conventional folding methods.
Additionally, Morgana’s DynaCrease mechanism will give the same high quality crease that Morgana/Ferrostaal customers have come to expect, but without stopping the sheet and, therefore significantly improving productivity.
SPECS AT A GLANCE:
Max sheet size: 700 x 385mm (900 x 385mm with optional extension table)
Min sheet size: 210mm x 140mm
Max paper thickness: 0.4mm (approx 400gsm) including laminated material
Min paper thickness: 0.11mm (approx 80gsm)
Max folds per sheet: 2
Max programmed applications: Unlimited alphanumeric
NAGEL DFC
The Nagel DFC offers various possibilities in applications which have until now only been provided by much bigger and more expensive machines. It can be the ideal solution for digital printers with small or medium sized jobs.
The products produced can include unusual boxes and packaging, pharmacy cartons, presentation folders, CD covers, labels and much more.
The DFC processes paper and cardboard up to 450gsm as well as many plastic materials. Die-cutting, perforating, creasing, embossing and kiss cutting can all be performed on the DFC.
The principle of the machine is based on a high quality magnetic cylinder, a conveying cylinder and a flexible die cutting form. The die cutting form is produced according to the customer’s specifications and can be used up to 100,000 times.
The DFC 450 can take a maximum sheet size of 500 x 430mm up to 450gsm. It can run at speeds up to 2,300 sheets per hour, with a set-up time of less than three minutes.
With touchscreen display, the menu navigation and set-up is very simple. There is no need for trade qualified staff to operate this die cutting machine, an advantage over traditional die cutting methods.
The Nagel DFC 450 is distributed in Australia by Papepr Handling Equipment. PHE has Nagel trained staff to install and train print staff on the DFC’s operations. This machine can be purchased from $348.00 per week.
SPECS AT A GLANCE:
Sheet formats (L x W): 160 x 90 – 500 x 430mm
Paper weights: 45 – 450gsm
Max speed: 2,300 sheets/hr
Max height of stack on feeder: 60mm
Gap clearance (when die cutting): 0.8mm
Die cutting accuracy: up to +⁄- 0.2mm
NEOPOST UD-300 ROTARY DIECUTTER
According to Neopost, the UD-300 diecutter is ideal for short run offset or digital printers, although each plate can last up to 250,000 impressions. It offers the equivalent performance and productivity of a Cylinder, but with a much quicker set-up time of two minutes.
The UD-300 has the capability to perform multiple cuts, slit-scores, perforations, window and hole punches in one pass.
Neopost offers complete installation and training, with on-site service also available. Neopost offers up to five-year agreements on this solution.
With simple, easy set-up and one-button stop and start, Neopost claims anyone can use the UD-300 successfully. Adjustments are also easy, with 0.1mm increment adjustments on both length and width.
Neopost also offers in-house finance options.
SPECS AT A GLANCE:
Max speed: 6,000 cycles/hr
Min paper size: 219 x 297mm
Max paper size: 354 x 515mm
Paper weights: 106-400gsm
PLOCKMATIC BM500/350 BOOKLET MAKER
Plockmatic International has introduced the replacement for the BM200e system booklet maker — the upgraded BM500/350 system.
Now available in two configurations of either 50- or 35-sheet capacity, this off-line booklet maker has the same features as the popular in-line version for Fuji Xerox and Ricoh. The Pro50/35 for Fuji Xerox and the PBM500/350 for Ricoh have been well received by production digital print users over the past year, and now digitally printed booklets of up to 50 sheets, can be produced off-line with the same high quality.
The BM500/350 comes in two versions, a base 35-sheet unit and an optional upgrade kit to allow for up to 50 sheets of 80gsm. The standard BM350 is capable of 35 sheets creating a 140 page booklet. An upgrade turns the BM350 into a BM500 to staple and fold up to 50 sheets of 80 gsm, which creates booklets up to 200 pages.
Customers can choose to include the Squarefold module to complete the finishing touch with a square folded edge and printable spine, giving booklets the professional look of a perfect bound book. The Face Trimmer module trims the side opposite to the spine eliminating the “shingle” effect that occurs with thicker booklets.
Together with the trimmer and SquareFold module, quality booklets can be produced either hand fed or connected to the new AF602 digital feeder from Plockmatic. The large capacity bins on the AF602 will accommodate long uninterrupted, unattended runs that will fit well into the digital print workflow.
New features on the BM500/350 include a patented set-positioning mechanism that enables the operator to adjust the staple and/or fold position up and down on the spine from the user interface independently. Fine-tuning can be performed at any time during the run.
New patented folding technology means fold duration is automatically optimised based on stock type and sheet count, achieving the best possible result on every booklet without manual adjustments.
With maintenance-free staple heads, and high-wear parts now in the consumable cartridge itself, service frequency is virtually eliminated.
The SquareFold module has been re-positioned ahead of the Trimmer module for precise face trim on high sheet count books. The 100 (50 sheet folded) sheet face trimmer with variable trim length offers a multi-cut feature enabling additional trimming.
The BM500/350 is sold through Fuji Xerox Supplies and Ferrostaal in Australia and New Zealand.
SPECS AT A GLANCE:
Standard paper sizes: A4, A3, B4, SRA4, SRA3; custom sizes possible
Min paper size: W 206 mm, L275mm
Max paper size: W 320 mm, L457mm
Min paper weight: Uncoated 64gsm; Coated 105gsm
Max paper weight: 300gsm
Set size (stapled folding): 2-50 sheets BM500 (80gsm); 2-35 sheets BM350 (80gsm)
Set size (non stapled folding): 1-2 sheets
Off-line use: Yes
WOHLENBERG 76 GUILLOTINE
The Wohlenberg 76, manufactured in Europe, is the entry-level model from one of the most respected guillotine manufacturers in the world. Building on its reputation for precision manufacturing, it utilises a solid steel one-piece cutting table, a clamp bar control with a precision transport spindle and extra thick walled aluminium side walls.
The Man Machine Interface (MMI) in combination with an ergonomically arranged two-hand cut start, allows for stress free working. Specifically aimed at digital stock, the back gauge speed, acceleration and braking are adjustable, which is particularly advantageous when processing sensitive stock.
Automated safety knife change is accessible from the front, and a new knife changing device (knife lift with setting gauge) offers automatic fine adjustment of the knife.
The table blower is activated only when required during the cutting programme, resulting in energy savings as well as cutting noise and heat.
Offering a cutting width and depth of 76cm, and a height of 11cm, the Wohlenberg 76 is an all-round performer.
SPECS AT A GLANCE:
Cutting width x depth: 760 x 760mm
Cutting height (without false clamp): 110mm
Table height: 870mm
Clamping pressure: 200-2500daN
Backgauge speed: 300mm/sec
Comment below to have your say on this story.
If you have a news story or tip-off, get in touch at editorial@sprinter.com.au.
Sign up to the Sprinter newsletter