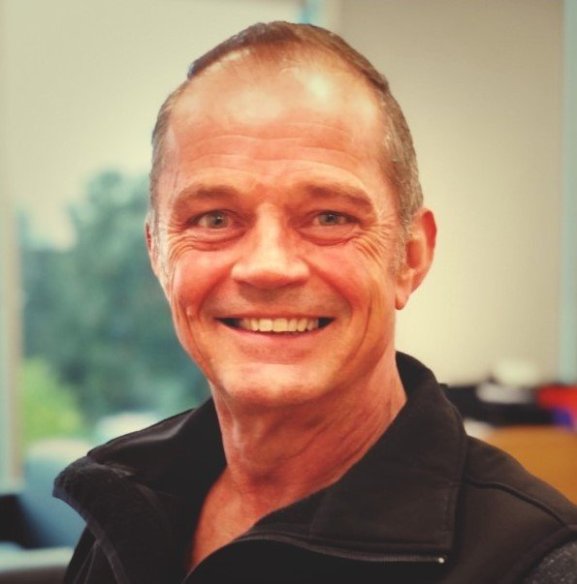
This article is part of a broader digital printing and finishing Technology Focus which appeared in ProPrint October issue. For the full story, click here.
Australian finishing technology developer, Trimatt Systems, is now offering the Trimatt ValidForm Certification System, which streamlines the postpress process for digital printing in the areas of on-press barcoding, folding, stitching and binding, collating, polywrapping, insertion and sorting.
Trimatt owner and CEO Matt Johnson says ValidForm reads and collects unique data from printed media and performs real-time monitoring of the printed job, while checking for missing records, duplicates, mismatches and poor quality.
Features include a single, fully synchronised controller, Windows-based software that offers ease of set-up, job saving templates and the ability to run from data files.
It has the capability to run two programmable outputs, an onboard real-time error log, the ability to read TrueType fonts, and 1D and 2D barcodes (QR codes). It also features remote accessibility. Johnson says ValidForm is available in various configurations from a single read head up to eight read heads.
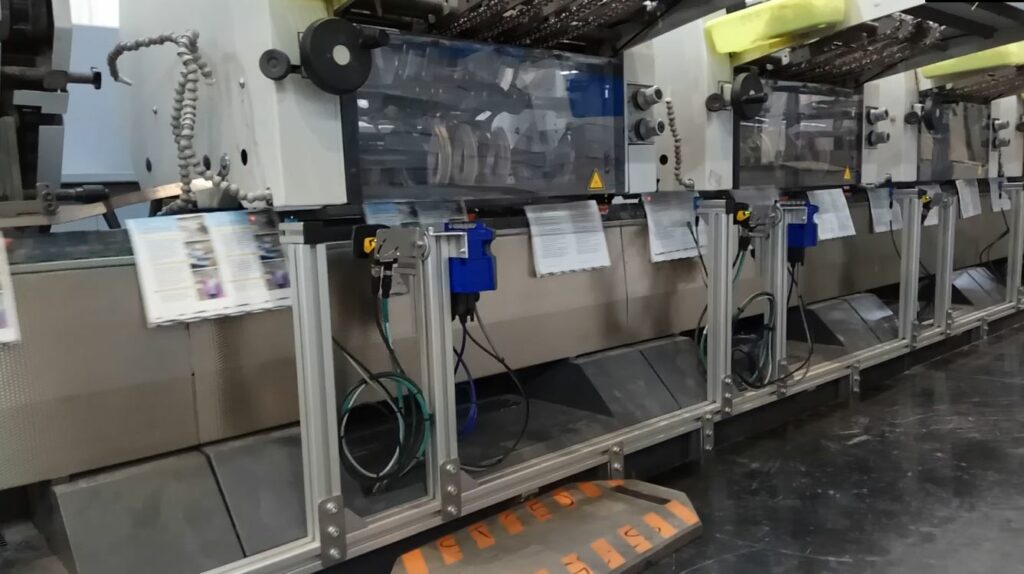
Moreover, the support of experienced and knowledgeable staff at Trimatt add peace of mind, says Johnson.
“Trimatt Systems developed ValidForm as a software suite that uses digital cameras to inspect each printed section for accuracy,” he explains.
“As the section is fed by the binder, our cameras take a picture and analyse it. This solution ensures print finishing meets 100 per cent accuracy. ValidForm is our own developed software and we now have over 100 installations around the country.
“The system is configurable to meet the varying requirements of our clients. We have solutions for capturing OCR or barcode information also. It all delivers an intelligent solution for matching personalised media.”
Johnson says Trimatt’s solutions are locally designed and supported and use leading modern technology.
“Unique requirements can be handled by our inhouse engineers,” he says, adding the data capture solution can be integrated into practically any process in the production environment, including established analogue workflows.
More broadly, Johnson observes that consulting and listening to clients is the key to understanding their problems and opportunities.
“Trimatt outlines the hardware and software required to deliver desired outcomes,” he said.
“By reducing risk and waste and offering 100 per cent quality assurances with full production reporting to users, investing in systems automation with Trimatt Systems gives printers and finishers a tool to capture new clients.”
Comment below to have your say on this story.
If you have a news story or tip-off, get in touch at editorial@sprinter.com.au.
Sign up to the Sprinter newsletter